Acid Leaching Copper Flotation Concentrate
As an alternative to Acid Leaching, Copper Chalcopyrite (CuFeS2) concentrates are processed traditionally by smelting, which results in sulfur dioxide (SO2) emissions. The development of a hydrometallurgical process for recovery of metals from concentrates of Cu ores offers industry a low-cost, low-pollution alternative to the traditional pyrometallurgical practices. The hydrometallurgical leaching of chalcopyrite with acid […]
Large Melting Furnace – City Waste
The most widely applied method for the disposal of waste materials, including sludges, dusts, scales, leachable slags from smelting or melting operations, and residues from the combustion of organic materials including municipal wastes, is to inter the materials in an appropriate landfill. Small quantities of some wastes are encapsulated within Portland cement or sulfur, and […]
Recover Neodymium from Permanent Scrap Magnet
Develop hydrometallurgical or pyrometallurgical recycling methods to recover valuable rare-earth compounds from various forms of NdFeB magnet scrap. The U.S. Bureau of Mines (USBM) has developed technology to treat and recycle a variety of wastes containing valuable and strategic metals. As part of this effort, the USBM developed a process to separate neodymium and other […]
How to Make Graphite Flakes from Steel Waste
Develop a technology for producing high-quality flake graphite from the steelmaking waste known as kish. Approach: Treat the waste kish as an ore and apply mineral processing techniques of physical beneficiation and chemical purification to produce a range of graphite products competitive with the natural mineral. Graphite is a naturally occurring form of carbon with a […]
Primary & Secondary AG Autogenous Grinding
Primary autogenous mill feed is either primary crusher discharge or run of mine ore, containing material on each size of the screen analysis below the largest piece in the feed. It is subject to the large variations in size analysis normally found in primary crusher products or run of mine ore. There can also be […]
How to Measure Grinding Efficiency
The first two Grinding Efficiency Measurement examples are given to show how to calculate Wio and Wioc for single stage ball mills. Figure 1. The first example is a comparison of two parallel mills from a daily operating report. Mill size 5.03m x 6.1m (16.5′ x 20′ with a ID of 16′). This example shows […]
Cone Crusher
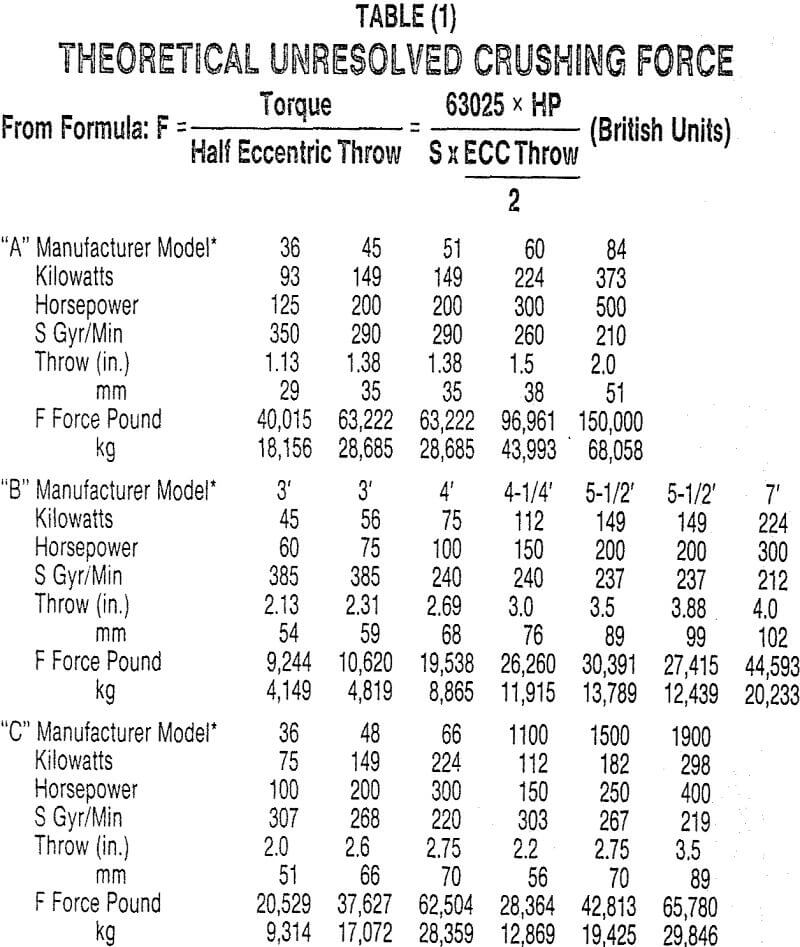
From the discussion so far it is obvious that two energy factors determine a crusher’s productivity: (1) Total power drawn affects the quantity produced of any given size or range of sizes. (2) The energy applied, previously defined as the crusher’s Power Rate (kilowatt-hours per ton of feed) will determine the size reduction. This has […]
SAG Mill Components
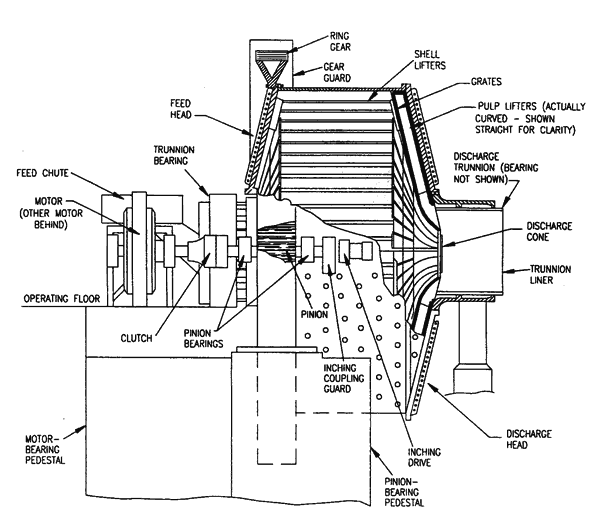
Once the basic operating conditions have been defined for the mill designer then, and only then, can he begin taking into account shell and head stresses and trunnion bearing sizes required to carry the load and to give the required openings for feeding and discharging the mills. Mill heads are key structural components of any […]
Crushing Simulation
In the context of this paper a simulation model for a size reduction device is an equation or equation set which allows the calculation of the product size distribution from the device for a specified size distribution of feed. The model might be expressed as a simple algebraic expression, as a matrix equation, or as […]
Laboratory Balling & Pelletizing Method
Early laboratory balling and pelletizing tests resulted in balls or pellets superior in quality as compared to production pellets, no matter what the variable being tested. In order to indicate more closely what a material would do for balling and pelletizing in a plant we felt it was necessary to approach the plant conditions. When […]