How to Remove Molybdenum Process Plant Water
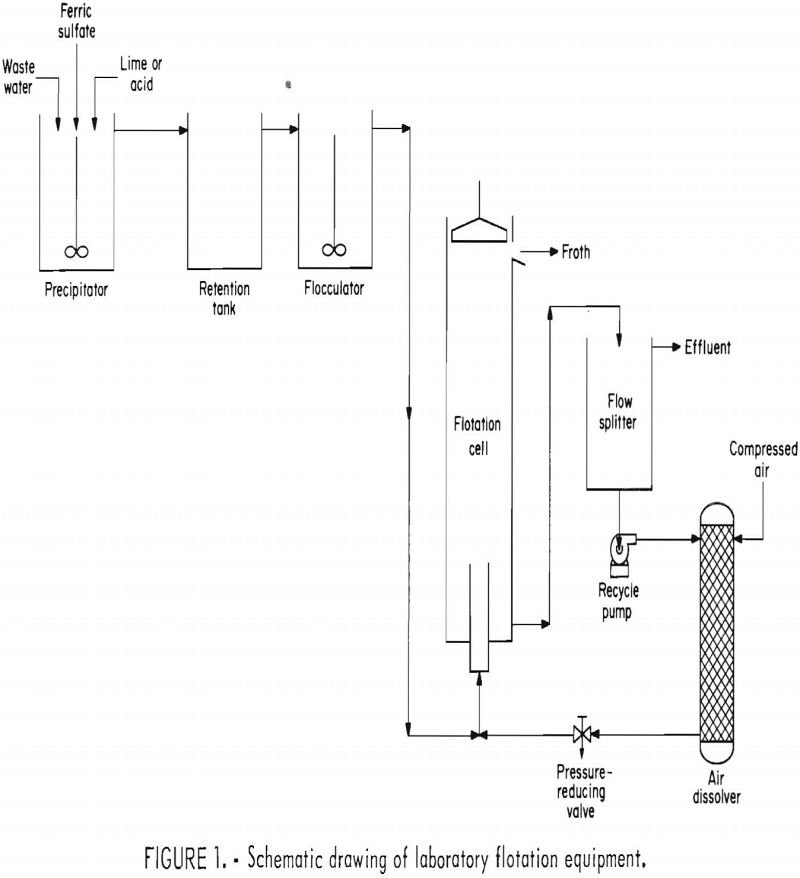
The minerals industry uses large volumes of water in many of its operations. Because of the rapidly decreasing availability of water in many areas and the need to control pollution, efficient and economical processes for purifying mineral waste waters are urgently needed. As part of a continuing program to devise technology for abating pollution caused […]
Acid Mine Drainage Treatment & Sludge Disposal
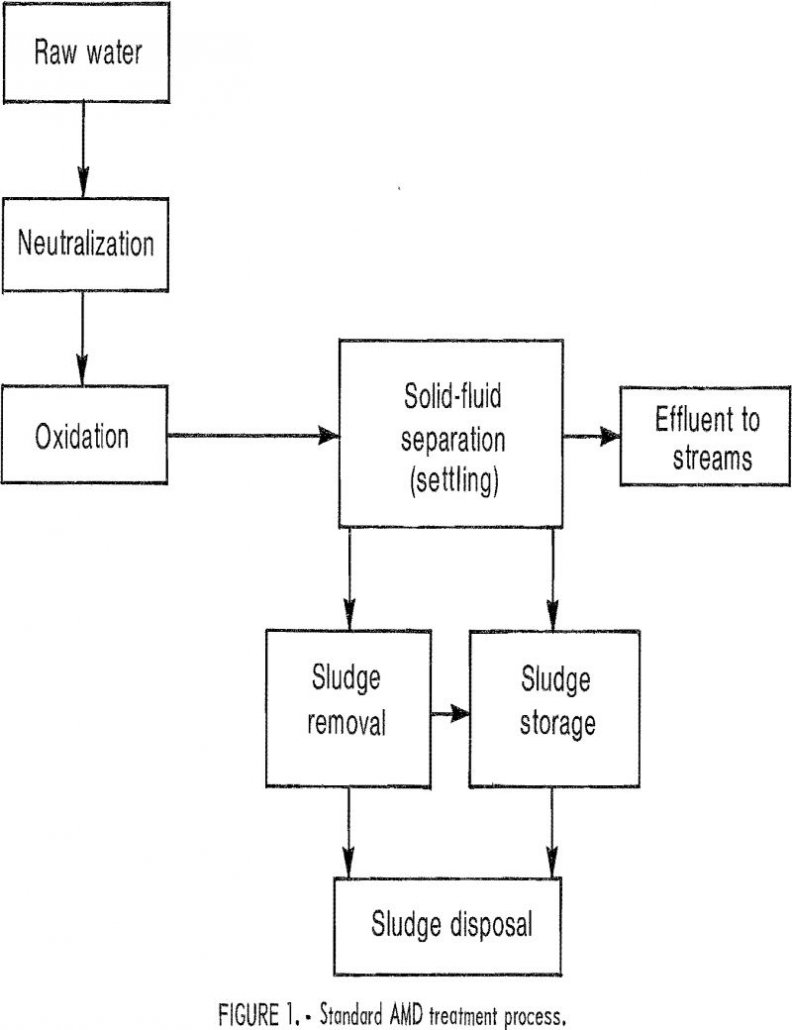
The technology of acid mine drainage (AMD) treatment has improved since the mid-sixties, and water pollution from active coal mining operations has been reduced considerably. Present treatment processes are designed to raise the pH of the effluent to within the range of 6.0 to 9.0 and reduce the total iron concentrations to less than 7 […]
Flotation of Rare Earths from Bastnasite Ore
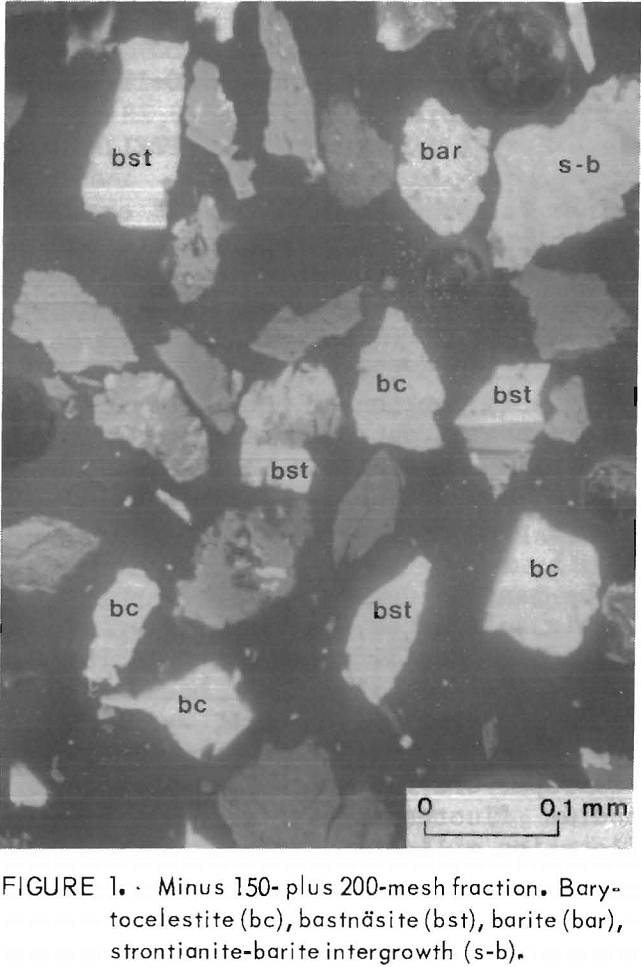
A large bastnasite deposit was discovered at Mountain Pass, Calif. Subsequent development of the deposit made the United States the world’s largest source of rare-earth minerals. Since then, bastnasite, a fluocarbonate of the cerium-group metals, REFCO3, has replaced monazite as the principal source of rare earths; in 1978 it accounted for more than half of […]
How to Identify Scrap Metals
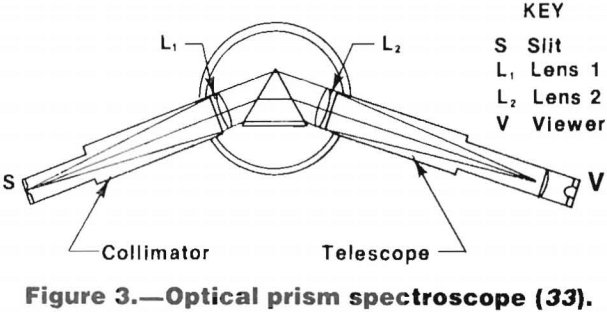
Large quantities of scrap metals are discarded each year by industry and householders; recycling of these materials results in conservation of dwindling domestic resources and helps ease U.S. dependence on imports. Substantial energy savings are also achieved by increased use of recycled material. In order for these scrap metals to be returned to those operations […]
Sand Bed Dewatering
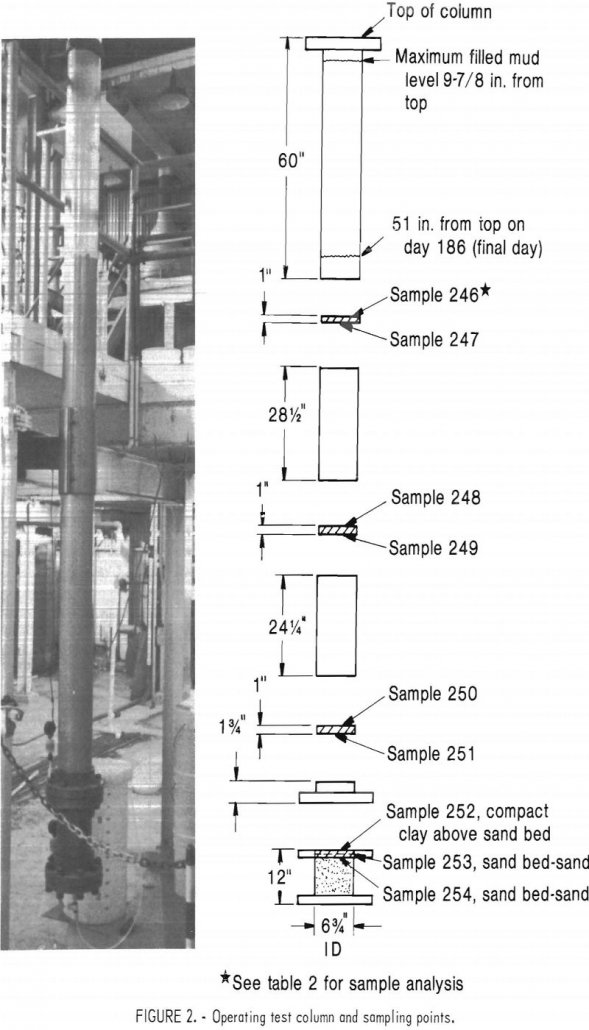
In 1979, as part of its minerals environmental technology research, the Bureau of Mines began a study of mine waste tailings disposal. Part of the investigation focused on evaluating the effectiveness of the sand bed dewatering technique on alumina miniplant tailings. Alumina wastes result from the hydrochloric acid extraction of alumina from nonbauxitic ores. These […]
Mineral Wool Furnace Refractories
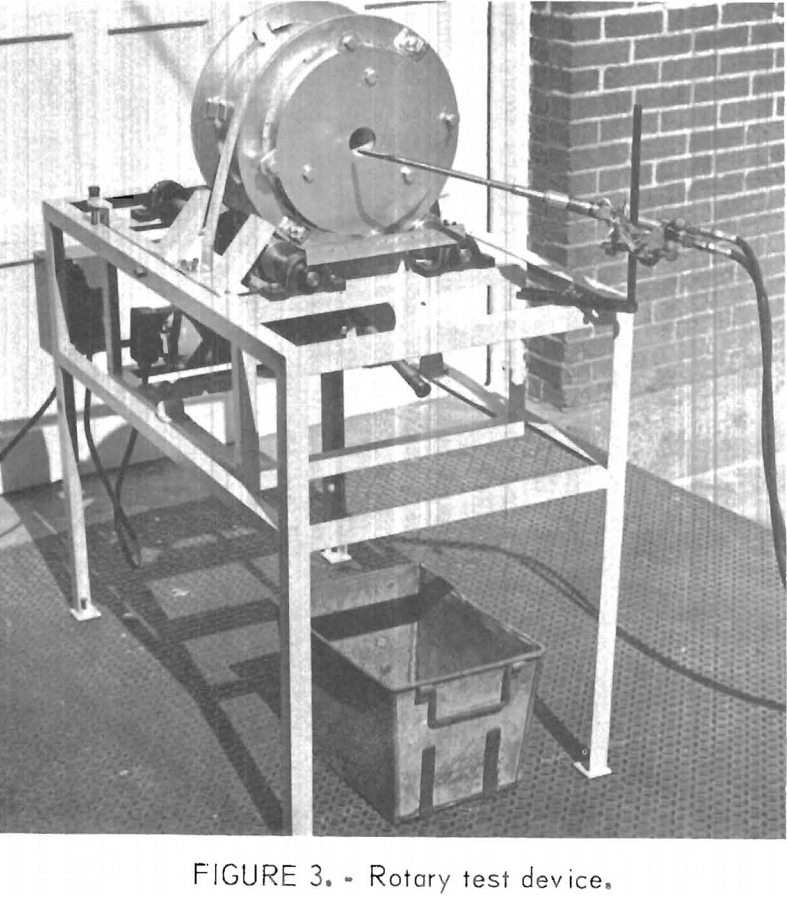
A slag formulation conforming to that used by a commercial mineral wool producer was used throughout testing. The composition of the test slag was as follows, in weight-percent: 9 copper-smelter slag, 41 lead-smelter slag, and 50 iron blast-furnace slag. Each component slag was crushed through 20 mesh, and a weighed amount of each was blended […]
Porphyry Copper Blasting
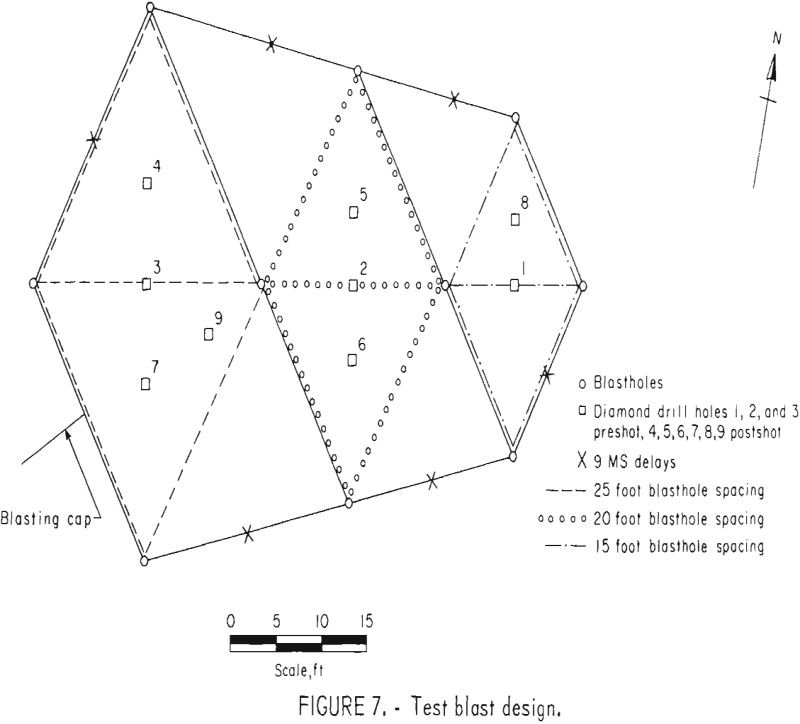
Some are developing fragmentation technology for in situ extraction systems. An in situ extraction system is attractive because it can be applied to deposits that are presently too low grade to be mined by conventional methods, thereby increasing domestic reserves. In situ extraction also reduces exposure of workers to health and safety hazards, minimizes detrimental […]
Nickel Electrowinning
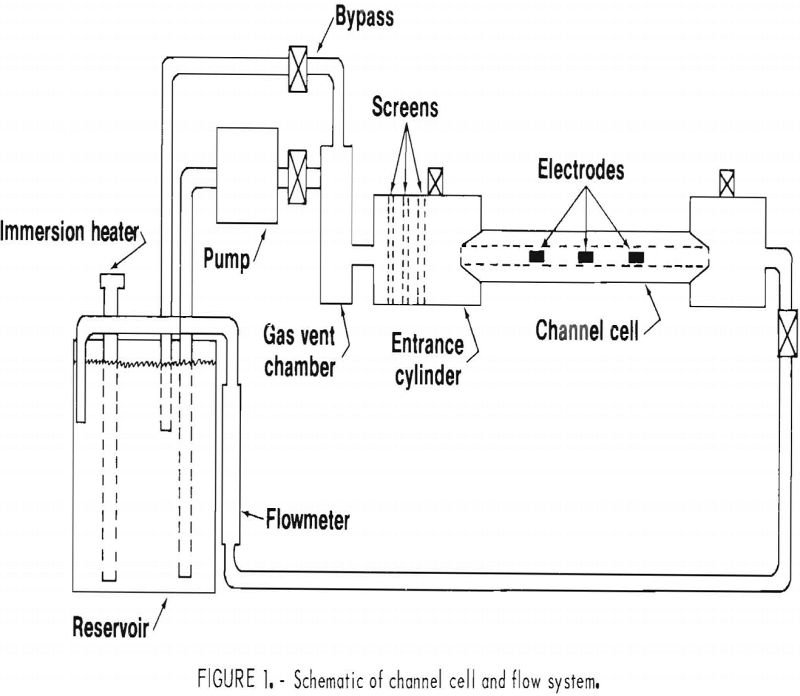
Increasing the relative motion of the electrolyte with respect to the electrode surface has long been recognized as a means by which the mass transport of ions to the electrode can be increased to allow operation at higher current densities. Basic theories and early experiments were discussed by Nernst, Brunner, Lin, Denton, Gaskill, and Putnam, […]
Chalcopyrite Nitrogen Roast & Leaching Electrowinning
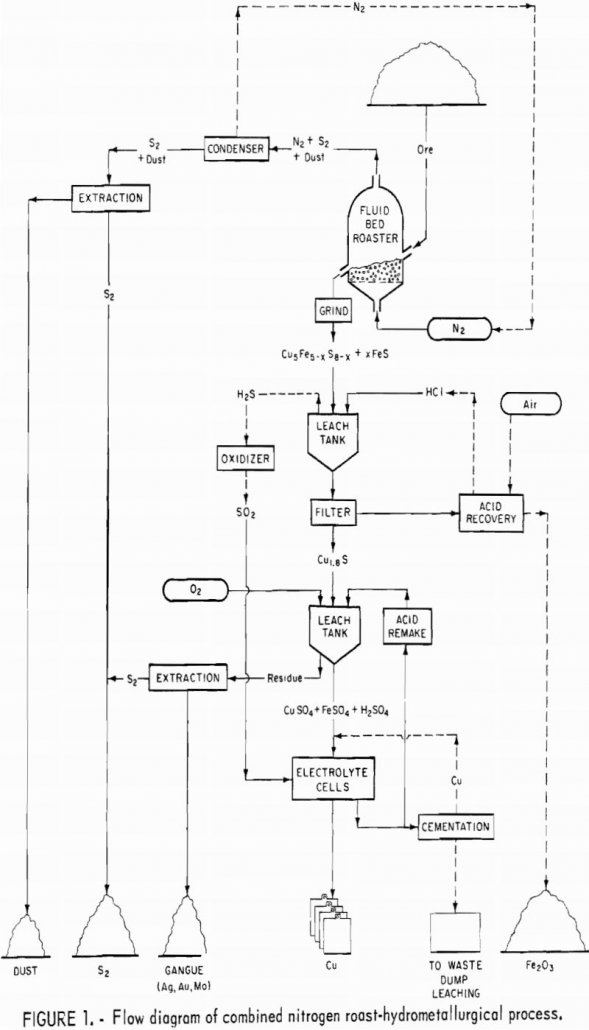
Present copper extraction technology is based principally on pyrometallurgical processing of sulfide concentrates in which high-temperature air-roasting and air-smelting generates large quantities of sulfur dioxide. Because of very stringent environmental standards and increasing cost of energy, there has been a renewed interest in hydrometallurgical processes for recovering copper from sulfide flotation concentrates. Potential advantages of […]
How to Recover Mercury from Cinnabar by Electro-oxidation
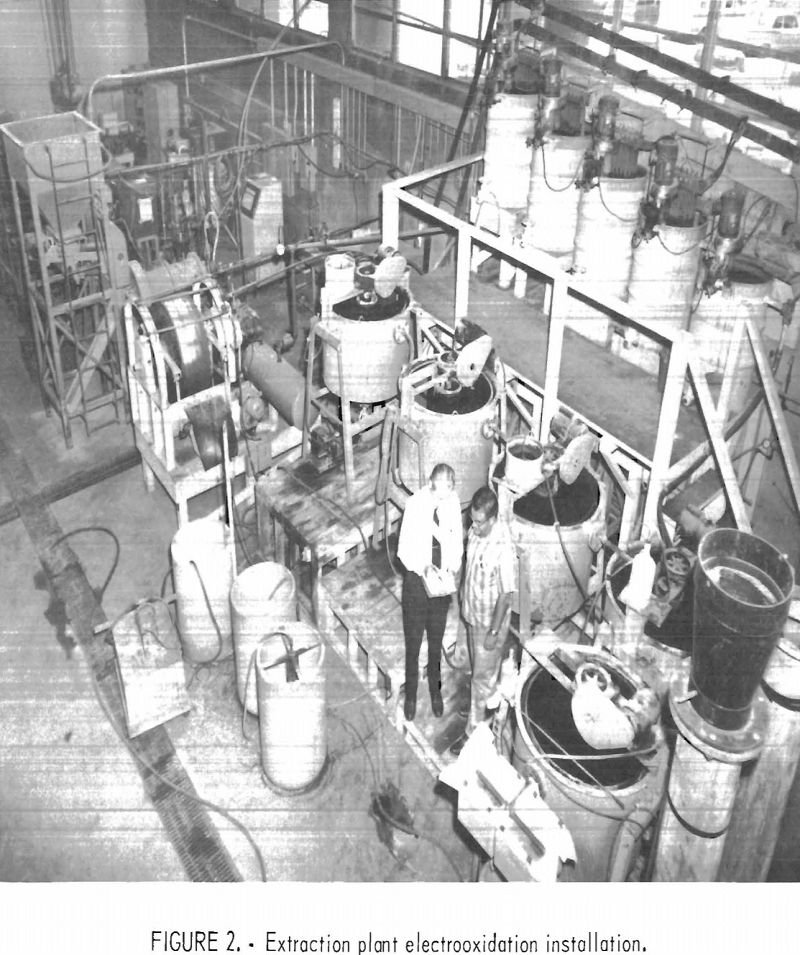
Mercury is customarily recovered from its ores by roasting sulfide minerals and condensing the vapors to obtain the metal. The process is efficient from the standpoint of mercury removal from the calcine; however, vapor and particulate losses in the condensing system, as well as the loss owing to recombination of the mercury with sulfur, can […]