Largest Mines in the World
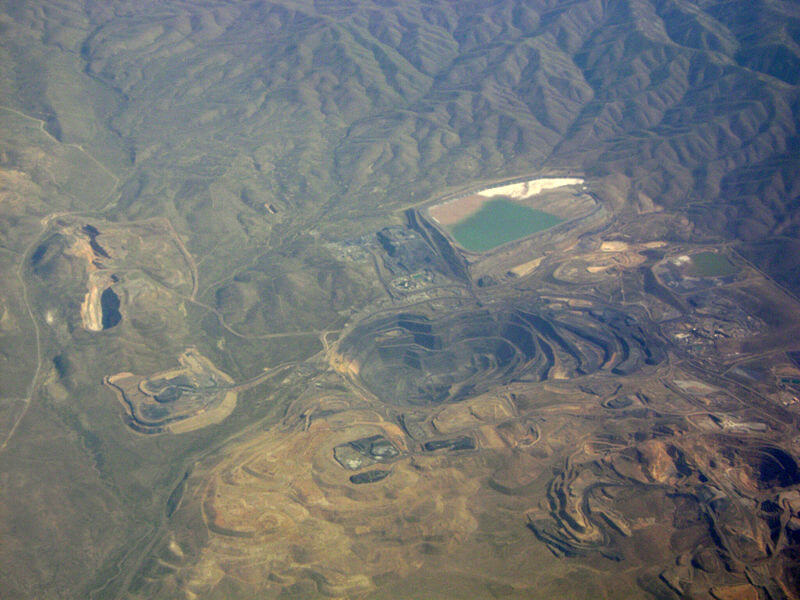
Here is my list of the Top 15 largest and biggest mines in the world: They are economically big and physically large, taking a lot of time and power to excavate using special mining equipment. But in their core, there’s what big mining companies are looking for: the precious ore. Join us as we […]
Mining Consultants List
Mining consultants play a major role in the feasibility, planning, design and construction, operation and improvement of both small and large mines. Consultants are experienced design engineers, mine designers, operating specialists or maintenance engineers who operate independently of operating mines. They are available to work on: mineral exploration projects, where start-up companies have not yet recruited […]
Heavy Liquid Testing Procedure
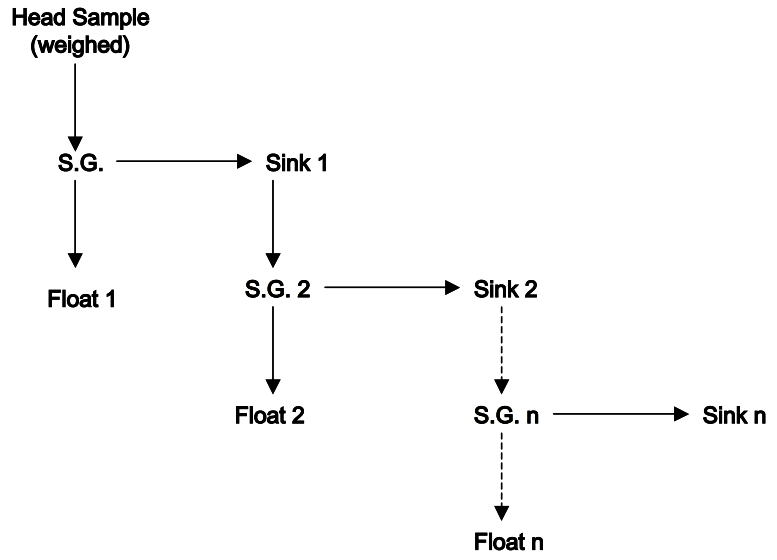
The general procedure is as follows. The sample is placed in the liquid of lowest specific gravity and is split into two fractions. The float fraction is set aside to be weighed and assayed. The sinks fraction is washed in a suitable solvent, dried and placed in the liquid of a higher specific gravity. This […]
Froth Flotation Process
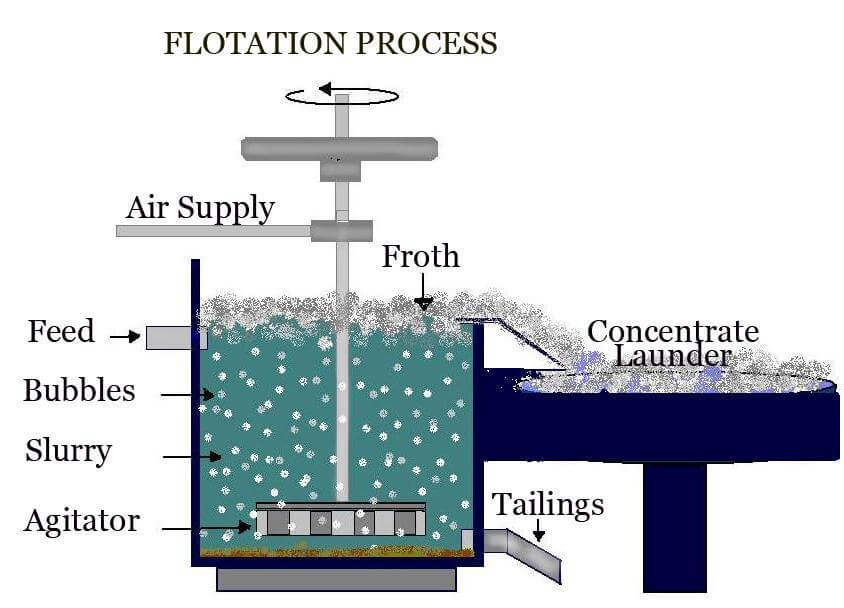
The Froth Flotation Process is about taking advantage of the natural hydrophobicity of liberated (well ground) minerals/metals and making/playing on making them hydrophobic (water-repel) individually to carefully separate them from one another and the slurry they are in. For this purpose we use chemicals/reagents: Frothers (MIBC) is what allows the formation of air bubbles. Think […]
Precious Metals – World’s Top 10
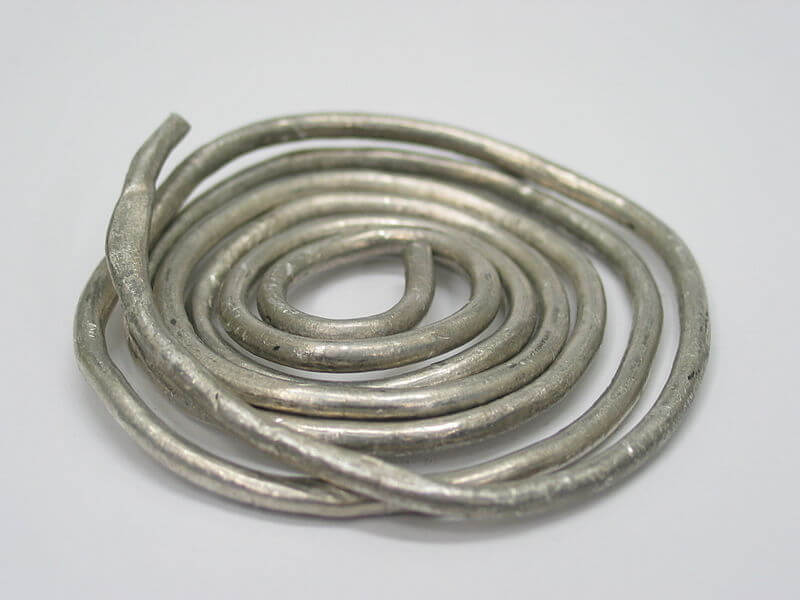
Ever wondered why people keep their gold pieces in safes? And why your family silverware is always so well protected? Well, that’s obviously because gold and silver are two precious metals. That you already know… But what about other metals? There are other substances equally precious, even more, precious than gold, that you must get to […]
Portable XRF Analyzer & Price List
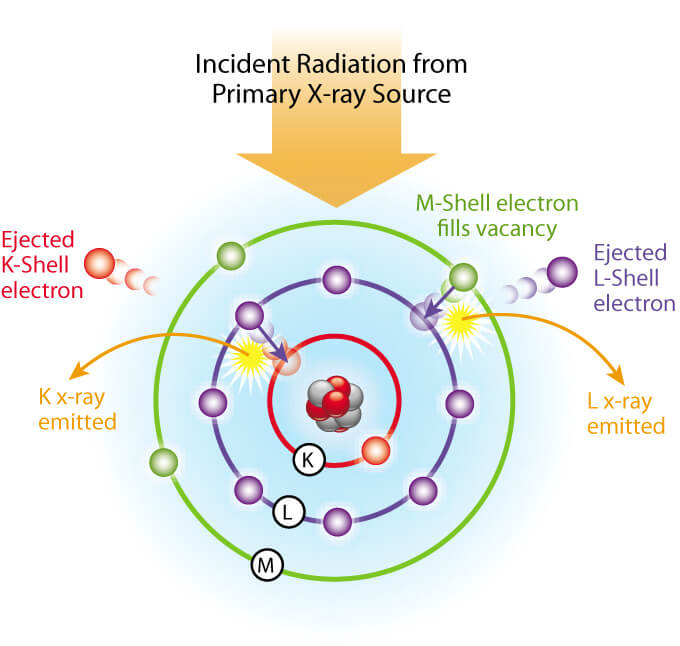
See many used XRF Analyzer Models and their prices. Here I list the price of a Portable XRF Analyzer (AKA handheld XRF spectrometer) depends on functionality and Brand. Used models can save you as much as 70% over new ones. REVIEW XRF TECHNICAL SPECIFICATIONS BY BRAND: Olympus/Bruker/Niton/Oxford/Spectro Visit our XRF Discussion Forum Olympus offers a variety of […]
Where to Find Gold
So tonight’s topic of interest is kind of near and dear to me, I’m going to start with the first slide; Rocks and Gold Clues. What rocks tell you about where to find gold, there are clues that they give and those are very important if you’re going to find gold and that’s what we’re […]
Spent Alumina Regeneration
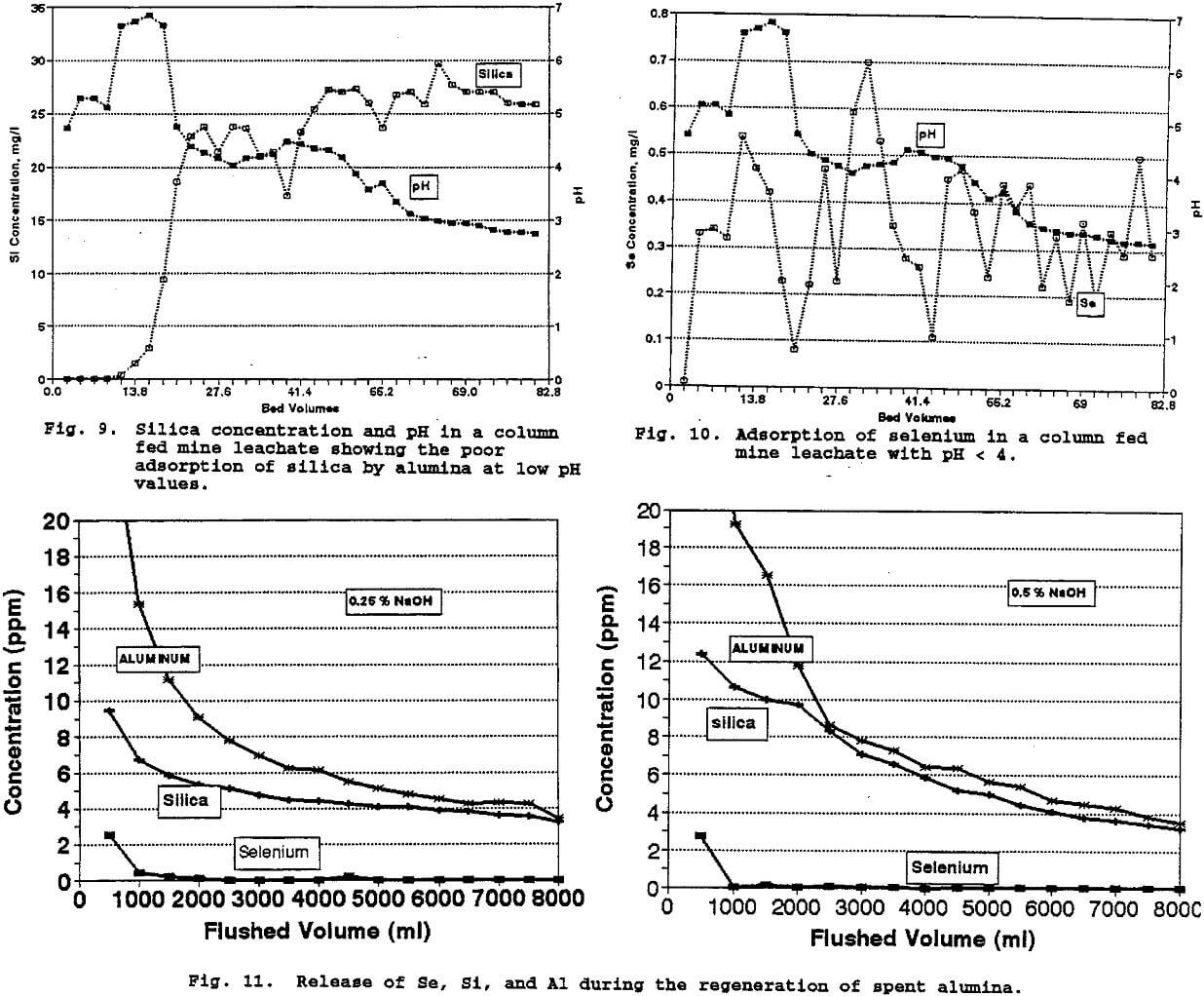
Regeneration of the spent alumina was accomplished by using 0.25% NaOH and 0.5% NaOH. Figure 11 shows the release of selenium, silica, and aluminum when regenerating the adsorption columns that had received the mine leachate. In this case, the regeneration was performed in an upflow mode using 30% bed expansion. As expected, the losses of […]
Dry Grinding Equipment & Plant
Laws of Gravity Gold
Ten Laws of Gravity Gold Recovery DO DON’T Try to Evaluate the Economic Impact of Gravity Recovery Get a Statistically Significant Sample of the Ore to Evaluate Gravity Response on a Size-by-Size basis Design the Gold Recovery Circuit with a Good Understanding of Gold’s Behaviour in Grinding Circuits When GRG Recovery Is Not Indicated, Look […]