Fluorspar Beneficiation Process Plant

The Fluorspar Beneficiation Problem Acid grade fluorspar which is in great demand by the chemical and aluminum industries, must contain at least 97.5% CaF2 with not more than 1.5% SiO2 and 0.5% Fe2O3. Often the Silica is limited to 1.2% with penalties starting at 1.0% SiO2. These limitations on grade and impurities require extremely close […]
Plug N Play Plants
Monometallic Flotation Plant Gravity Recovery & Au/Ag Leaching with CCD Merrill Crowe Plant & Refinery Gravity Recovery & Au/Ag Leaching – CIL Stripping & Refinery
Diamond Processing Plant & Equipment
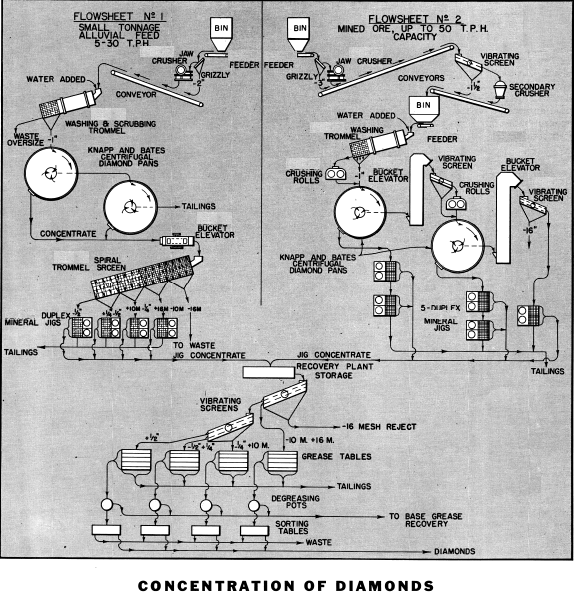
World demand and production of diamonds both for gem and industrial purposes has increased nearly five-fold during the past 25 years. Improved mining and recovery methods together with the discovery and development of new fields has enabled mining operations to fill the growing demands. Producing areas in South Africa, South West Africa, The Congo Republic, […]
Batch Cyanidation Leaching of Flotation Concentrate
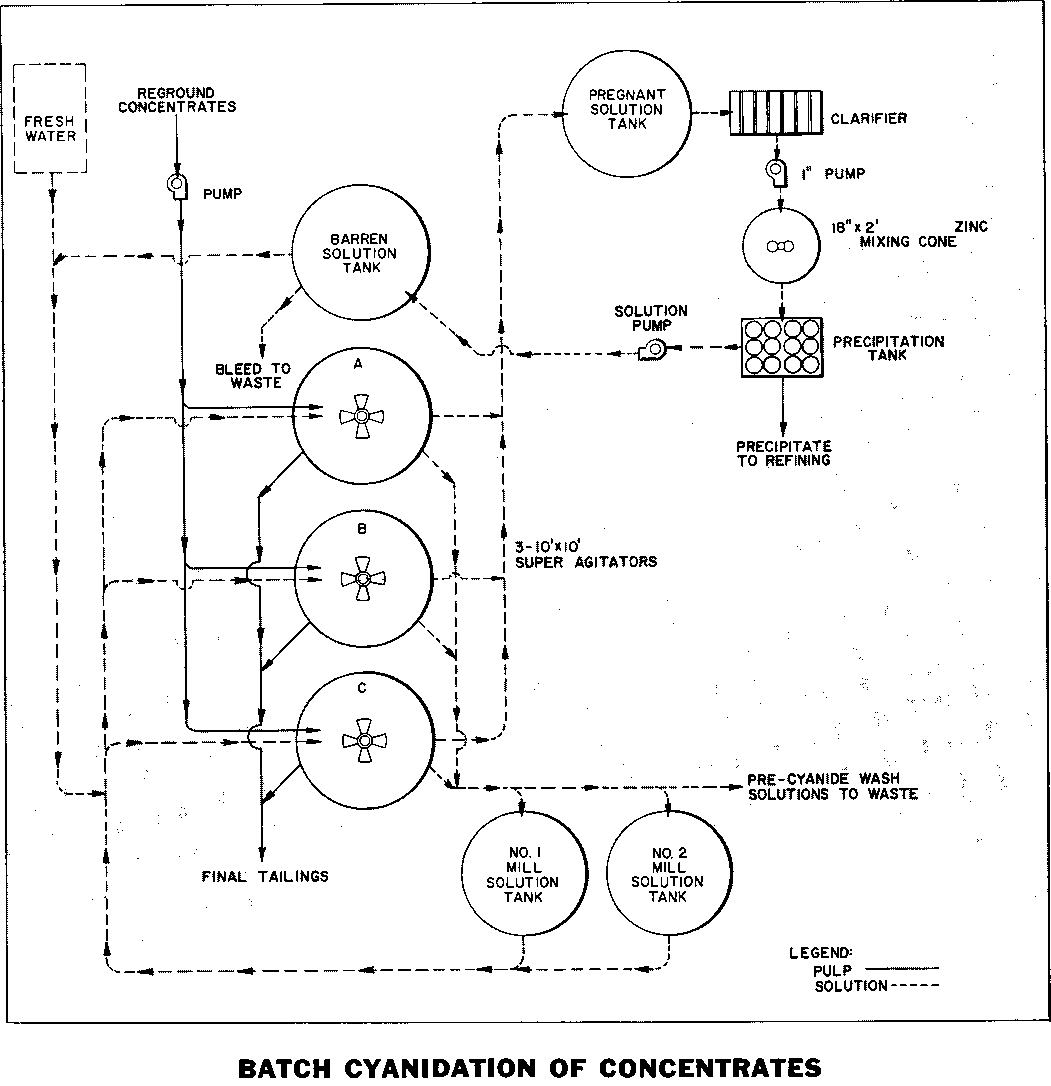
The production of gold bullion from gravity or flotation concentrates is often an important economic consideration for an isolated gold mining operation. It is assumed in this case that the coarse free gold has been recovered by the Mineral Jig in the grinding circuit and that the jig concentrate has been amalgamated. This treatment produces […]
Placer Deposit Processing
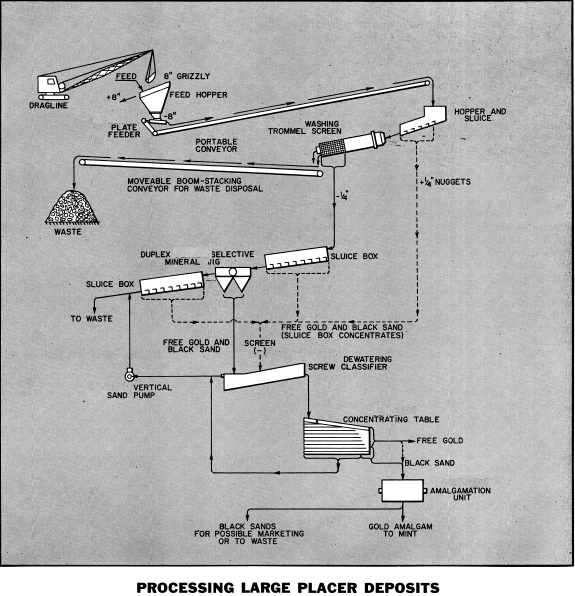
The handling of large quantities of gold-bearing gravels is of utmost importance for most successful placer operations. In addition to providing efficient washing and recovery methods, the placer plant should be constructed as a compact unit that can be readily moved. This is an important consideration because the washing and recovery plant should be close […]
Uranium Solvent Extraction Process
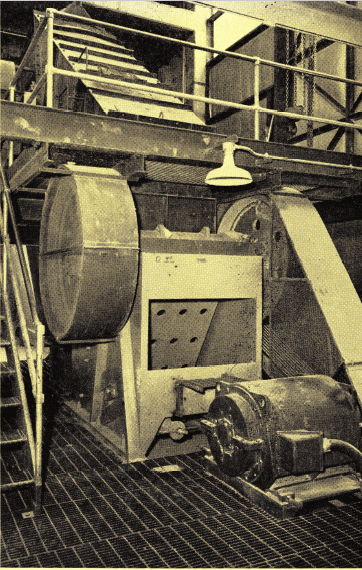
Uranium Geology The ore occurs as uraninite adhering to the outside of sand grains in the Wind River formation which rest unconformably upon Cretaceous shales. The ores are relatively low in clay content and generally regarded as exceptionally clean ores from the standpoint of objectionable impurities. The arkosic sands in which the ore occurs are […]
Acid Leaching – Copper Ore Treatment Method
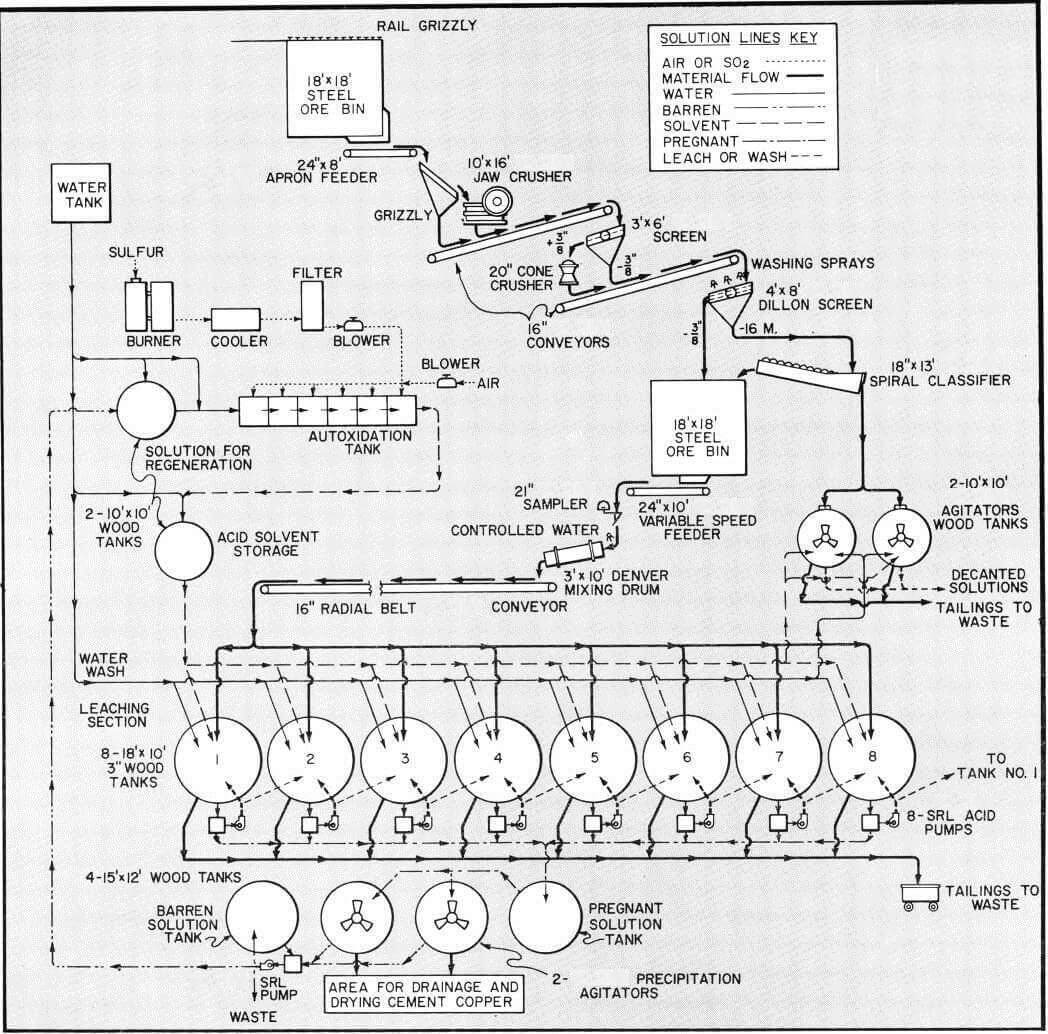
The treatment of copper ores, both oxides and sulfides by means of flotation, hydrometallurgy or other processes has been well established for many years. Flotation has been applied generally to the treatment of sulfide ores, both in small and large scale operations. Hydrometallurgical methods alone or in combination with flotation have mainly been applied to […]
URANIUM METALLURGY
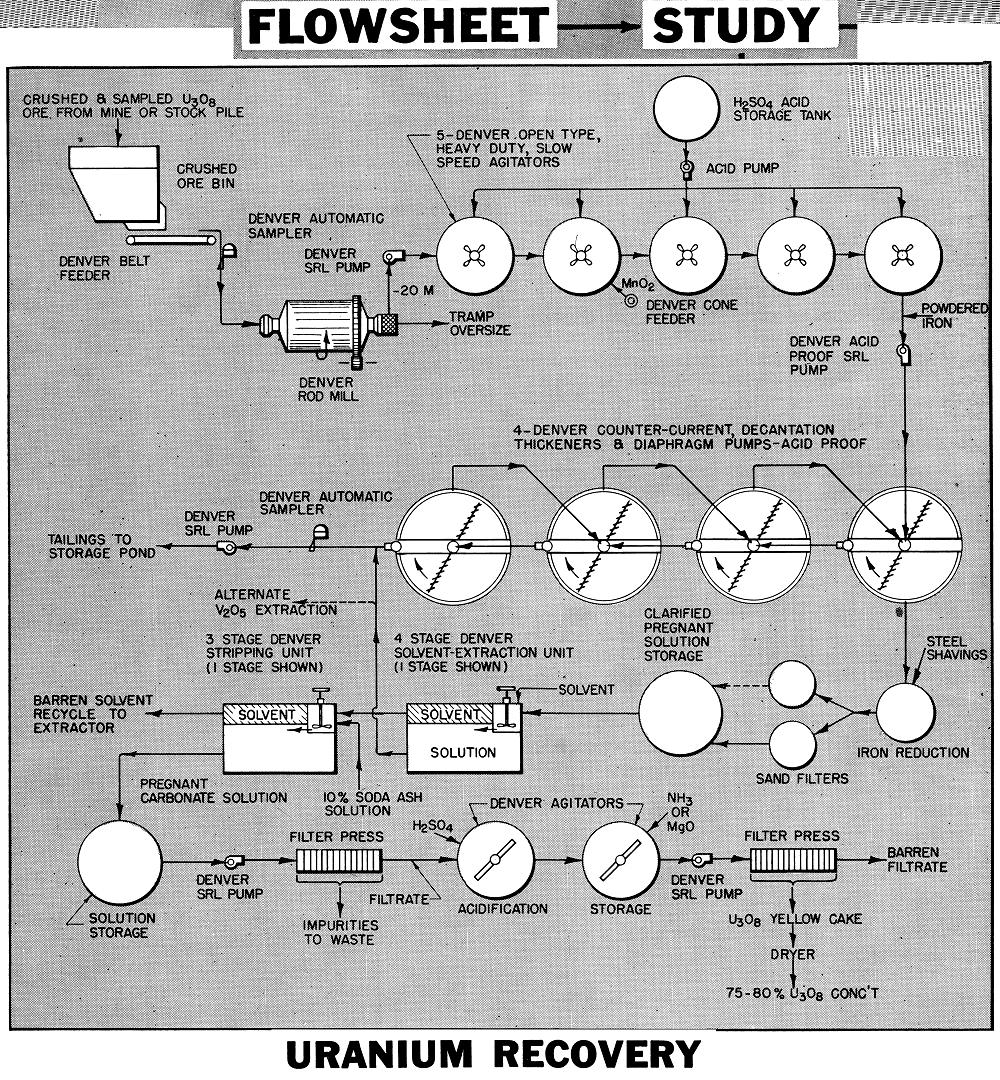
In the metallurgical treatment of uranium ores large tonnages must be handled. Many ores are low grade so it becomes necessary to employ systems which can be operated on a continuous basis at low cost. A vast amount of research has gone into the development of suitable processes. One is solvent extraction, which has proven extremely […]
Uranium Extraction Process
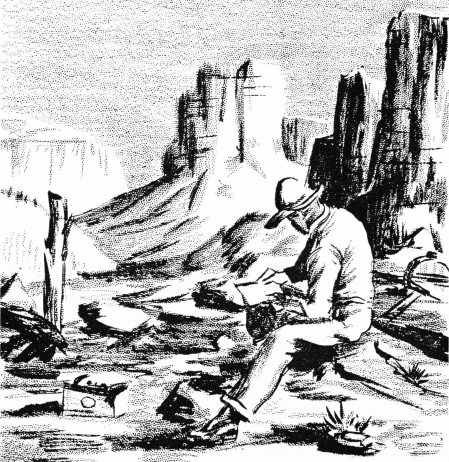
The plant was originally designed to treat uranium ores with low lime-high vanadium content from the Lukachukai Mountains. The process utilized is known as the “Acid Cure” and had been developed for the most part by the AEC to increase recovery of vanadium values. Briefly, it involved “pugging” the ore with 10% water and 400-500 […]
Mercury Ore Processing Plant (Mining)
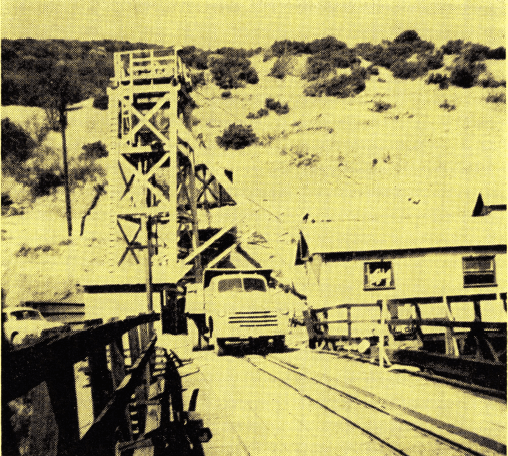
The Abbott mercury mine and mill are situated at an elevation of 2,000 feet in Lake County, California, approximately 24 miles west of Williams on State Highway 20 towards Clear Lake. Williams, which is served by the Southern Pacific railroad, is a local supply point as well as Colusa, located 10 miles east of Williams […]