Fine Screening using Sieve Bend
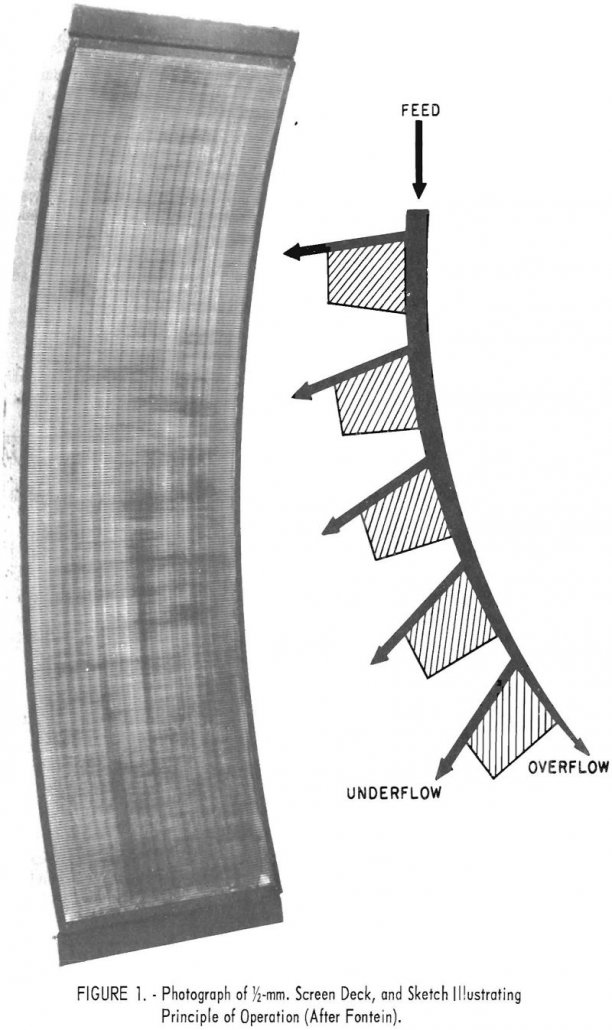
The cleaning of fine coal, particularly for metallurgical use, is receiving greater attention. An increase in the proportion of fine coal in the run-of-mine product has been created by changes in mining practice, and a concurrent deterioration in the quality of the fines has occurred because of more widespread full-seam mining. These two factors, augmented […]
Heavy Liquid Cyclone Separation
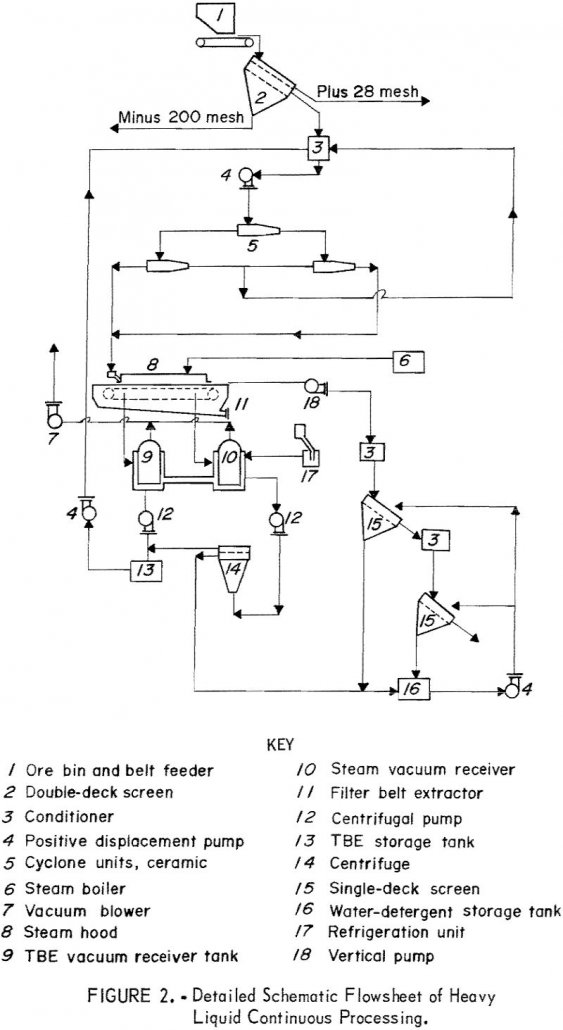
Kyanite ore deposits occur in the Southeastern United States. The ore reserves in this area are estimated at about 100 million tons having an average grade range from 10 to 30 percent kyanite. The Graves Mountain kyanite-quartz rock ore deposit consists of a prominent ridge about 1 mile long and 300 to 400 feet high. […]
Rapid Particle Hydrosizing Size Analysis
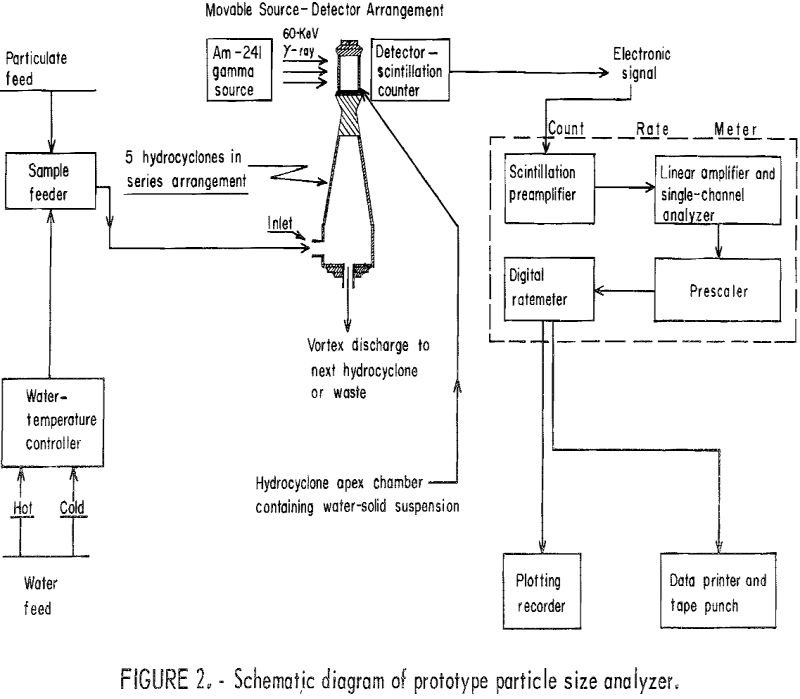
The knowledge of particle size distributions is a critical factor in the monitoring, control and optimization of many processes. This is particularly true of the mineral beneficiation industry, where comminution, the reduction of particle size, accounts for a major source of the processing costs. As an example, it is not uncommon in current taconite operations […]
Effects of Velocity and Orientation on HydroCyclone
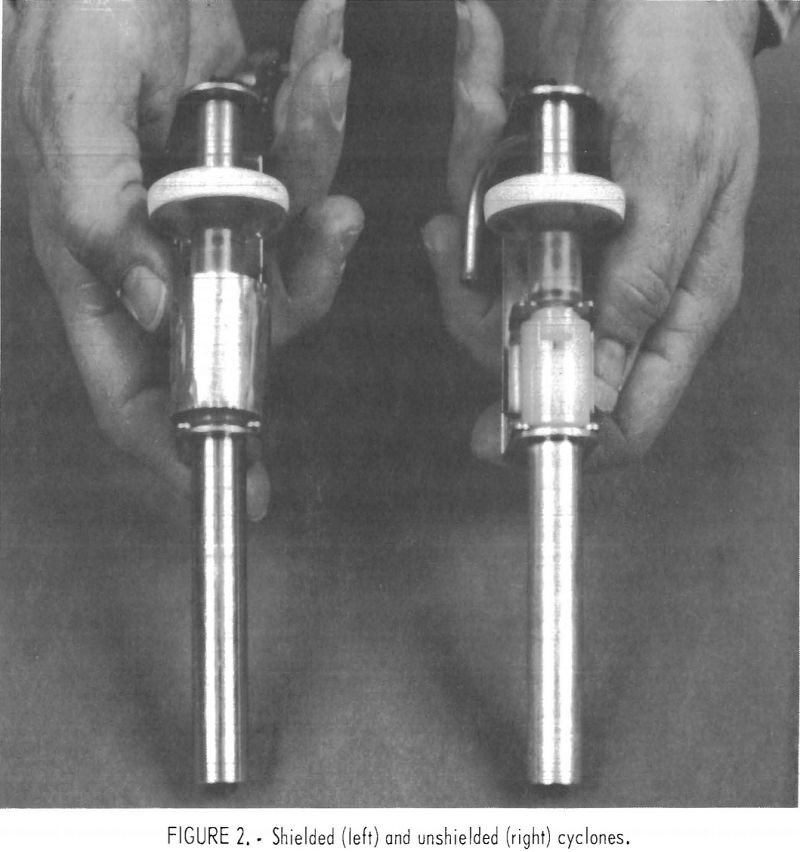
The 10-mm Dorr-Oliver cyclone is used for dust compliance sampling, which includes both stationary and personal sampling. The cyclone classifies “respirable” size particles, which are particles that reach the alveolar regions of the lungs, usually considered to have aerodynamic diameters (AED) of 10 µm or less. Although there are believed to be no instruments that […]
Centrifugal Forces Applies to Gravitational Classifiers
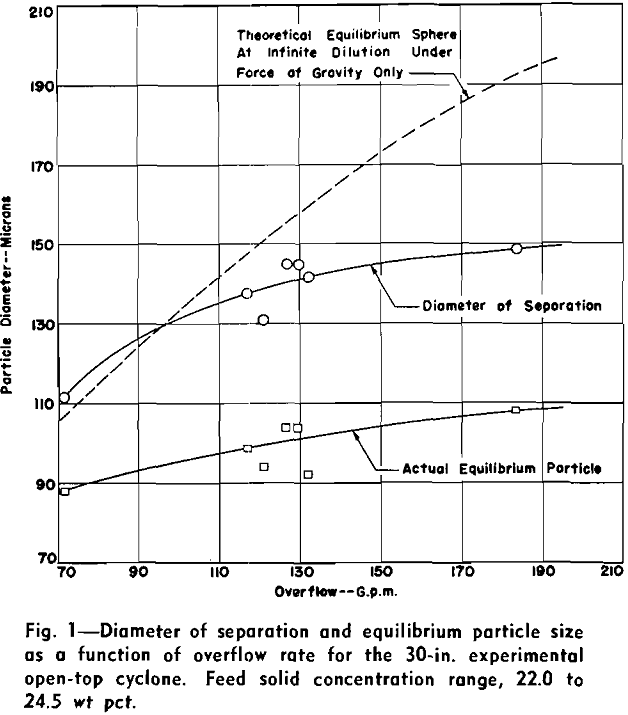
For many years gravitational classification has been employed as a basic tool in beneficiation of minerals and coal. While improvements have been made to increase efficiency and fields of application, the basic flow pattern has remained relatively unchanged in most gravitational classifiers. Feed slurry is introduced into a settling pool wherein the coarser solids settle […]
Photoelectric Sorting of Optical Fluorspar

The crystal laboratory, Dept. of Physics, Massachusetts Institute of Technology, was confronted with the problem of obtaining a supply of optical grade calcium fluoride (CaF2) for use in growing synthetic CaF2 crystals. A search of the known fluorspar deposits did not indicate that any quantity of optical spar could be obtained. Even the best material […]
DorrClone
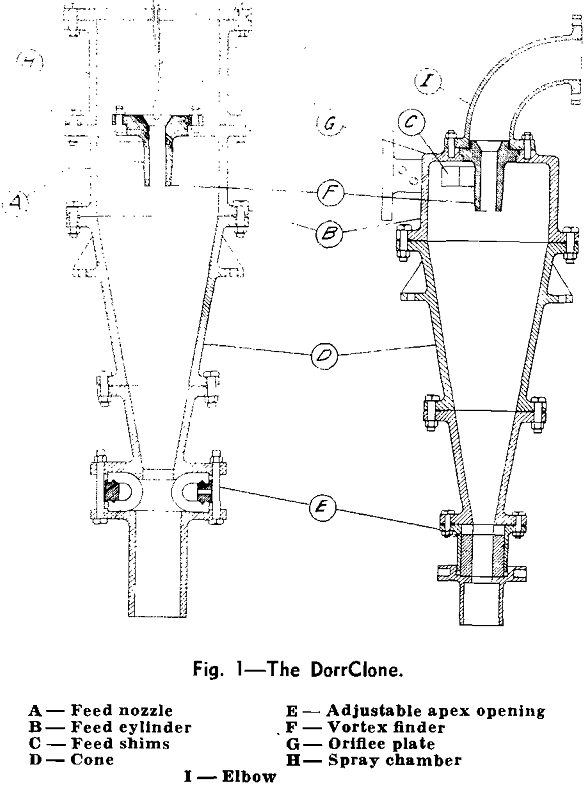
This paper presents in a general manner some of the applications of the DorrClone (Dutch States Mines cyclone) in the metallurgical and heavy chemical fields. Technical or mathematical analyses of the design factors and of the mechanism whereby the cyclone effects its separation have been capably treated in a series of previous papers. Engineering and […]
Method of Preparing Sized Micron Fractions
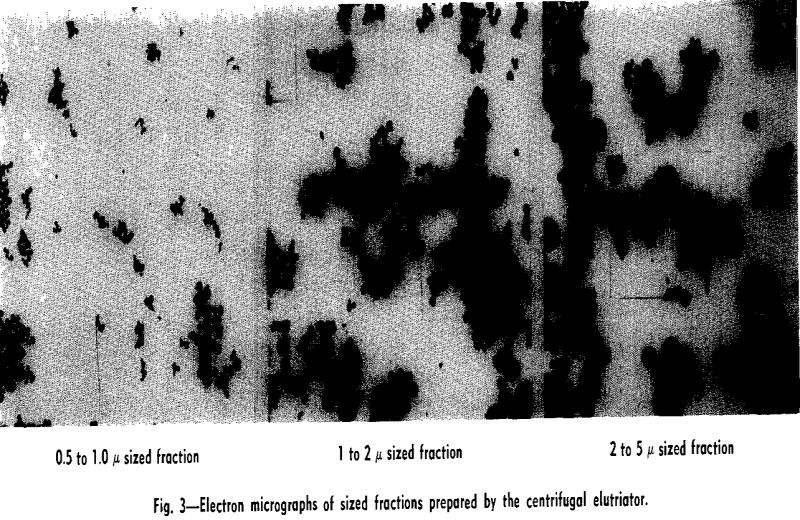
Study of light adsorption, reaction rates, electrophoresis, particle packing, and corrosion is hindered by lack of a suitable method of preparing small amounts of closely sized materials in the micron and submicron range. Most fractionation methods depend on some form of particle movement through a viscous media in which velocity of a particle, relative to […]
High Efficiency Desliming Cyclone
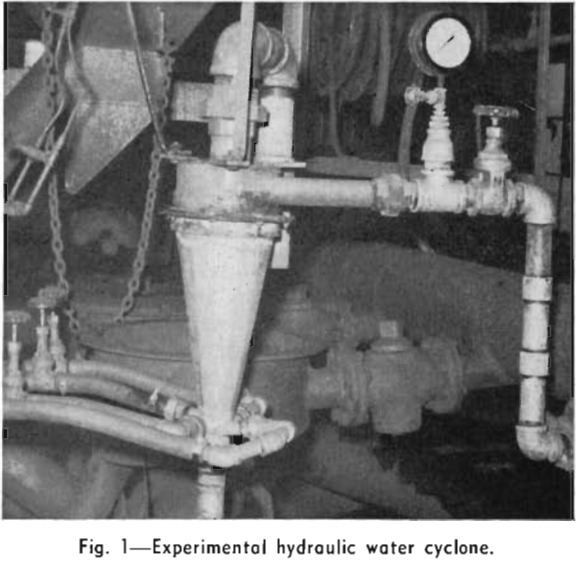
Ordinarily slimes have been classified as ranging from 75 microns, or 200 mesh, down to colloidal dimensions of less than one micron. At the same time there is general agreement that the most troublesome slimes are primarily clays, silts and extreme fines, so that the actual top size may be placed at approximately 30 to […]
How to Select the Correct Classifier
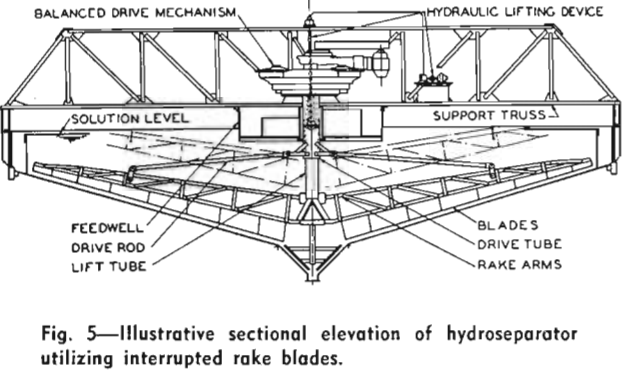
Separating a mixture of particle sizes of material suspended in a liquid medium is by no means an exact science. Selecting machines for individual classifying operations is even more difficult. The plant operator’s own background is of course invaluable, and considerable help may be obtained from technical articles, talks with sales engineers, and handbooks on […]