Cement Grinding

The principle of Grate Discharge grinding is nearly universally adapted in the cement grinding industry. Grate Discharge Ball Mills are the rule rather than the exception. Rod Mills for raw and finish grinding begin to enter the picture. Larger and larger diameter mills become common. Lengths tend to shorten. Cement grinding using Grate Discharge principles developed in […]
Comminution Theory & Process Equipment
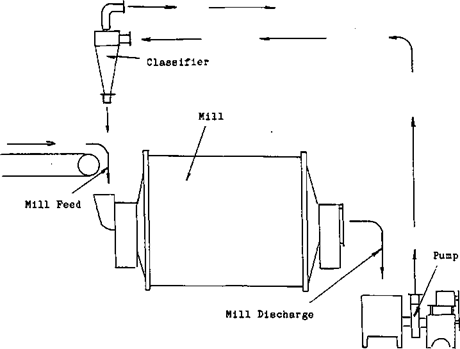
This page is devoted to the subject “From the Comminution Theory to Practice by selection of the correct Process Equipment” by taking you step by step through some of the variables encountered in the specific part of Comminution called grinding and how each of these affect your operations. Should it be possible to reduce all of these variables to […]
Grinding Balls & Rods

The subject of grinding media (grinding balls & grinding rods) is still controversial. The following information is general and based upon facts gathered from many operations. General statements can be made and are worthy of consideration when selecting grinding media. For the best results it has been found that the smallest diameter ball or rod […]
Industrial Ball Mills
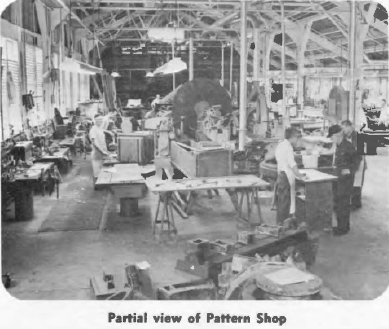
A symbol of dependable quality ore milling machinery manufacturing, industrial and mining equipment, ball mills and rod mills as well as supplies created for your specific needs. During this period thousands of operators have experienced continuous economical and unequalled service through their use. As an industrial ball mill manufacturer and supplier, we have continuously accumulated knowledge on grinding […]
Rod Mill & Ball Mill Manufacturer & Supplier of Grinding Mills

All Ball Mill Manufacturers understand the object of the grinding process is a mechanical reduction in size of crushable material. Grinding can be undertaken in many ways. The most common way for high capacity industrial purposes is to use a tumbling charge of grinding media in a rotating cylinder or drum. The fragmentation of the […]
Rod Mills: Efficient Grinding Solutions for Mining
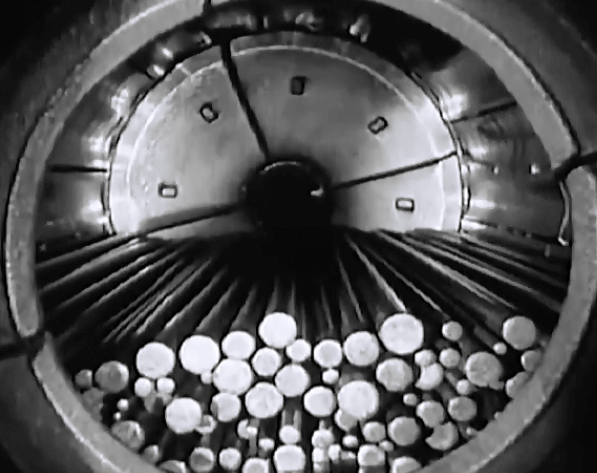
The Steel Head Rod Mill (sometimes call a bar mill) gives the ore dressing engineer a very wide choice in grinding design. He can easily secure a standard Steel Head Rod Mill suited to his particular problem. The successful operation of any grinding unit is largely dependent on the method of removing the ground pulp. The Steel […]
Small Ball Mills

A PULP level sufficiently high to interpose a bed of pulp, partly to cushion the impact of the balls, permits a maximum crushing effect with a minimum wear of steel. The pulp level of these Small Ball Mills can be varied from discharging at the periphery to discharging at a point about halfway between the trunnion and […]
Ball Mill & Rod Mill Design
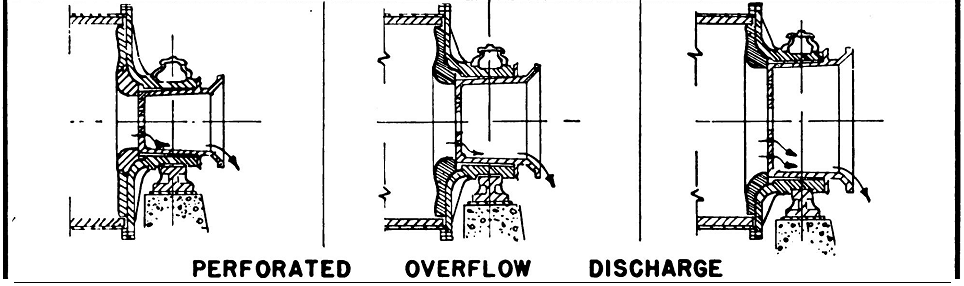
In all ore dressing and milling processes, including flotation, cyanidation, gravity concentration, and amalgamation, it is necessary to crush and grind, often with rob mill & ball mills, the ore in order to liberate the minerals. In the chemical and process industries, grinding is an important step in preparing raw materials for subsequent treatment. In present day […]
Bond Rod Mill Work Index Equipment & Apparatus Review
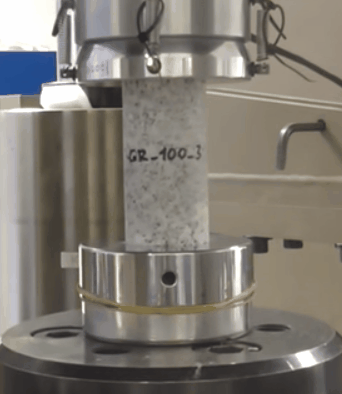
Commentary on the apparatus of the Bond rod mill Work Index by Alex Doll December, 2015 alex.doll@sagmilling.com The Bond “Third Theory” of comminution was originally divided into three size classes reflecting the varieties of comminution equipment common during the time period when Bond (and his collaborators) were gathering the information to calibrate comminution models. The […]
Rod and Ball Mill Discharge Housing

Most Marcy Rod/Ball Mills are provided with a discharge housing mechanism mounted independently of the mill. This unit consists of the housing proper, plug door, plug shaft, arm and various hinge pins and pivot and lock pins. The door mechanism is extra heavy throughout and is subject to adjustment as regard location. Place the housing […]