SAG Mill Reline
https://www.youtube.com/watch?v=9JEko22980I
SAG Mill Liner Design
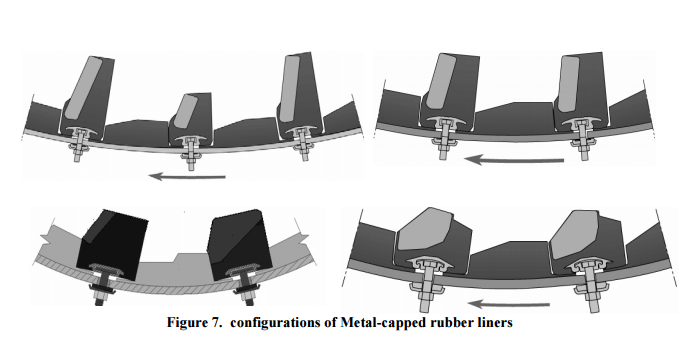
To a more significant degree than in other comminution devices, SAG Mill Liner Design and Configuration can have a substantial effect mill performance. In general terms, lifter spacing and angle, grate open area and aperture size, and pulp lifter design and capacity must be considered. Each of these topics has had a considerable amount of research, […]
SAG Mill Grinding Circuit Design
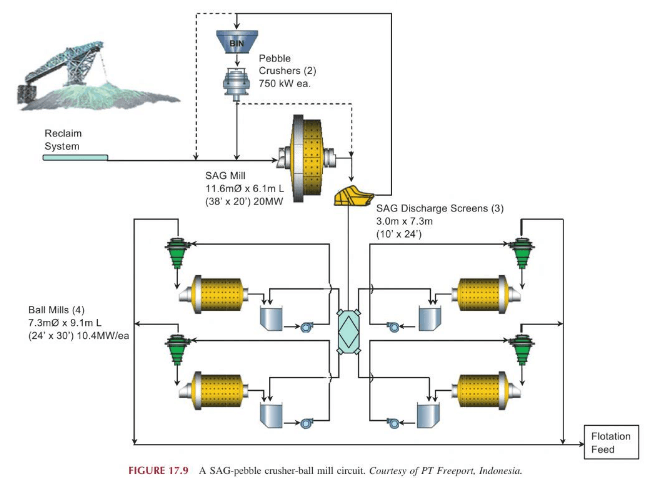
AG and SAG mills are now the primary unit operation for the majority of large grinding circuits, and form the basis for a variety of circuit configurations. SAG circuits are common in the industry based on: High single-line capacities (leading to capital efficiency) The ability to mill a broad range of ore types in various […]
Stockpile Segregation
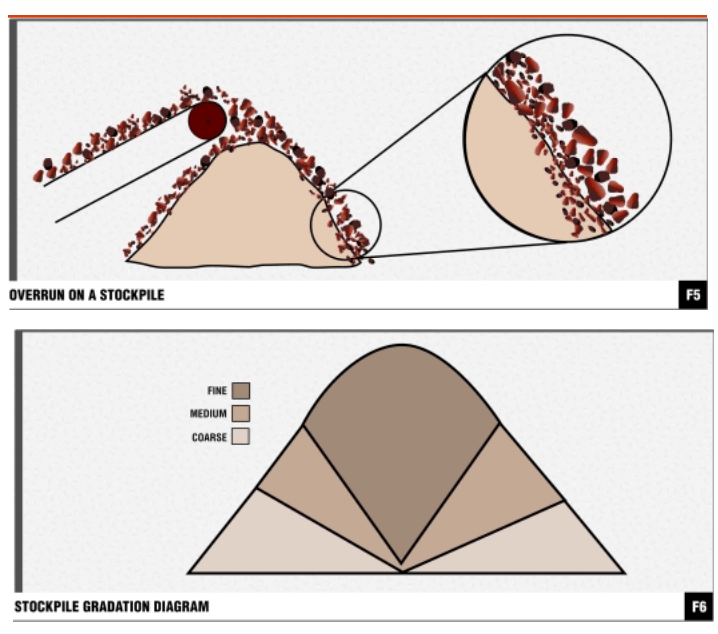
The video below graphically explains the common problem of Coarse Ore Stockpile Segregation. This topic relates to SAG Mill tonnage and the bad habit of putting bulldozers “dozers” on ore stockpiles. Stockpile-Segregation”>
Radial SAG Grate & Pulp Lifter Design
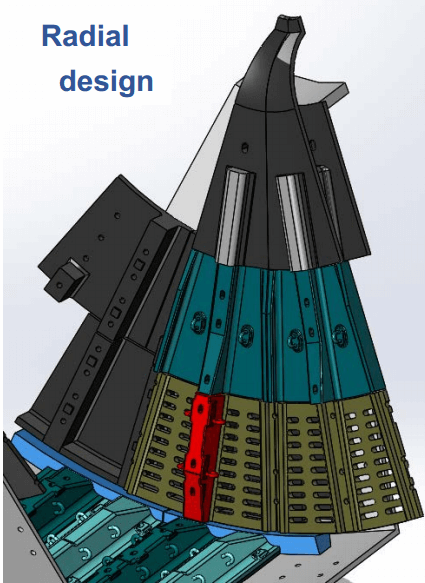
THE BARRATT METHOD
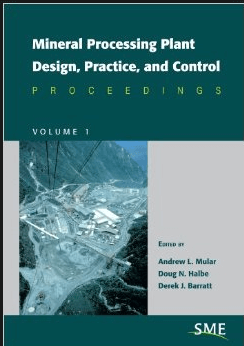
Plants designed using The Barratt Method as published in the Book Mineral Processing Plant Design, Practice, and Control Proceedings, include: Alumbrera Batu Hijau Cadia (one consultant among others) Candelaria Clarabelle (Inco) Collahuasi (line 1 & 2) Dreifontein El Teniente SAG 1 Ernest Henry Esperanza Fimiston Freeport 95K expansion Lisheen Numerous benchmarking exercises to operating grinding […]
Drop Weight tests using JKMRC Rotary Breakage Tester
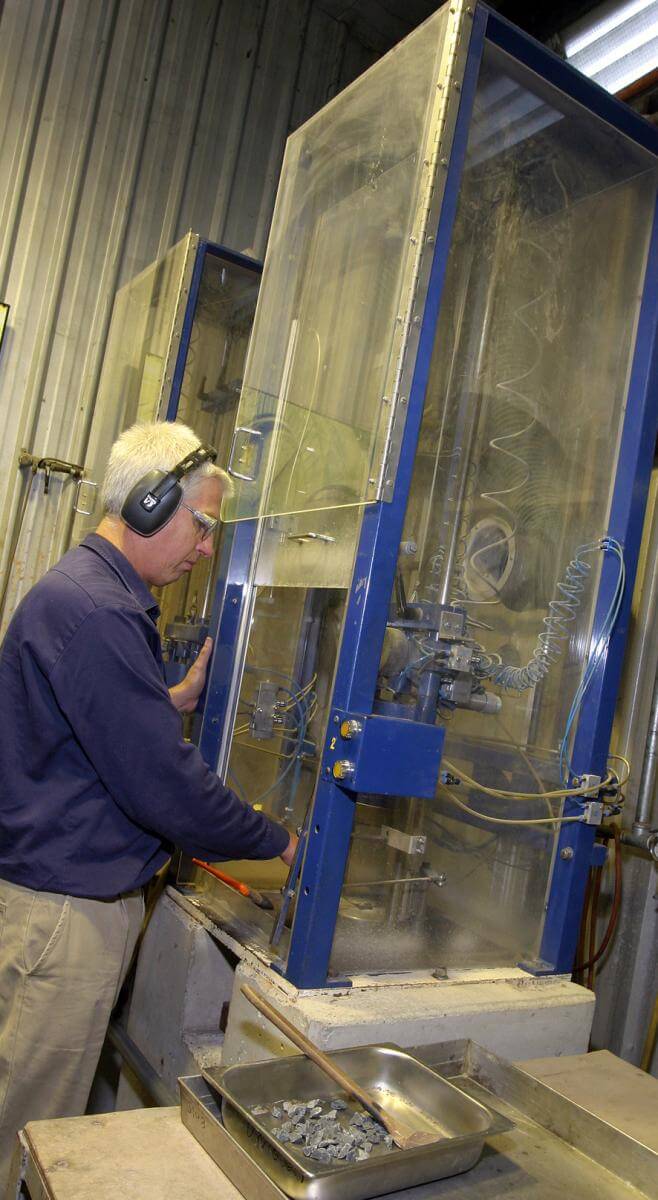
The Drop Weight tests (DWT) by JK is now replaced by the JKMRC Rotary Breakage Tester. It is faster as confirmed by Tony and now used by many since its intro https://www.min-eng.com In an AG/SAG mill there are two main mechanisms of breakage, namely impact (high energy) and abrasion (low energy). The industry accepted JK impact breakage parameters, […]
What Ore Testing is Required For Mill Selection
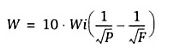
Beginners might ask what grinding test data is required in order to properly size a grinding mill. After the grind requirements are established, testing for the selection of comminution circuits and mill size can be initiated and can include the following: Primary Autogenous Media Competency Primary Autogenous and Semi-Autogenous Pilot Plant Secondary Autogenous (Pebble) Testing […]
SAG Mill Feed Chute Design| Long Life | Wear Resistant

This design of SAG mill feed chute lasted 9 months seeing 90,000 TPD. It is 600 brinell chrome steel. With the big liners on the bottom of the chute you need to get a Chevron cast into the top to push the feed out to the sides for the first little while and then as […]
SAG Mill Operating Load : SAG Mill Volumes
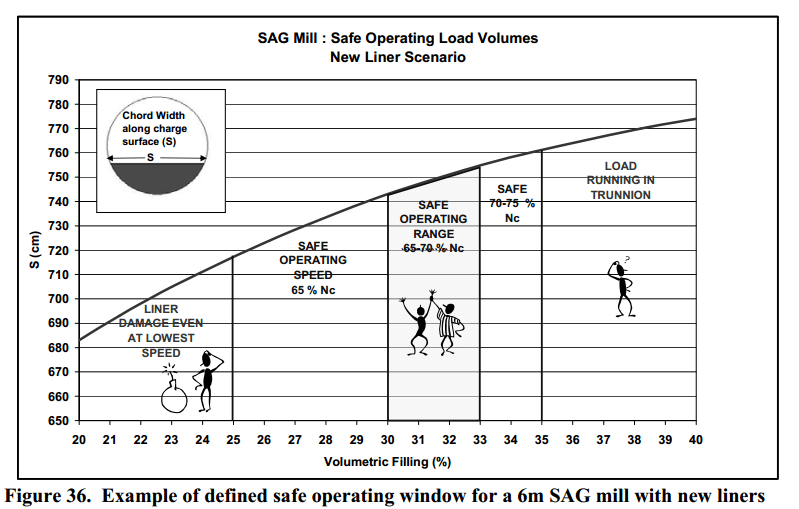
How much rock and balls must you hold in your SAG mill for it to best operate?