Industrial Water Treatment Systems & Process Flow Diagram
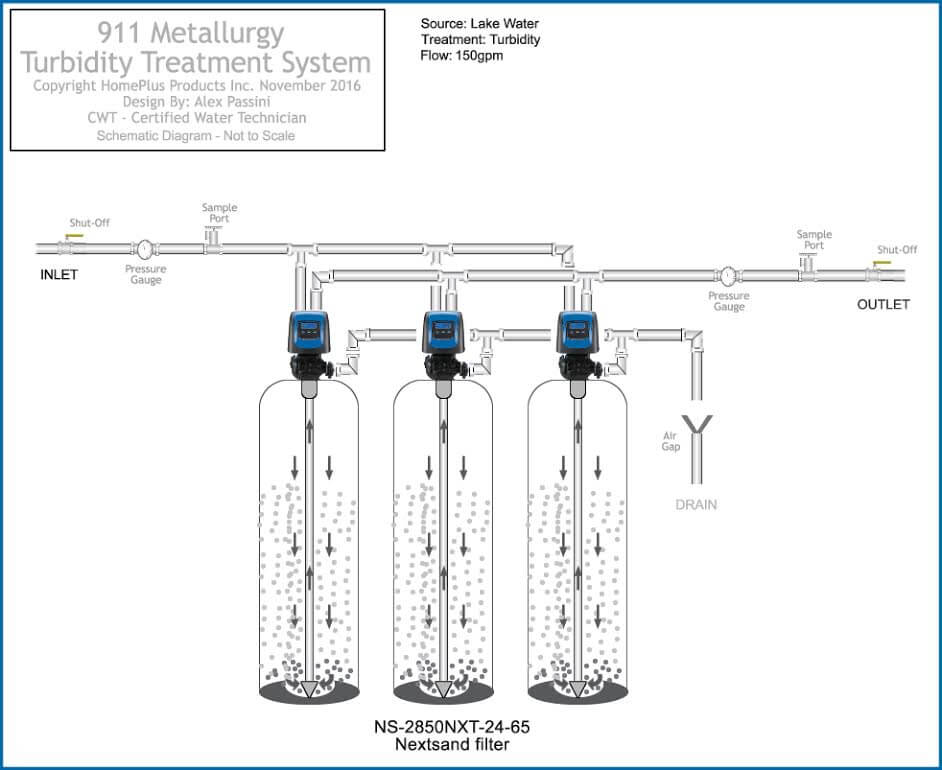
These are existing Industrial Water Treatment Systems, they can be sized from 10 gpm to 250 gpm. With arsenic and uranium, contamination concentrations are important. At 25 ppb As I can run a system at 40 gpm, however at 120 ppb As I need to reduce it down to 10 gpm with the same system to increase […]
Treatment of Mixed Sulfide Oxide Ores of Copper
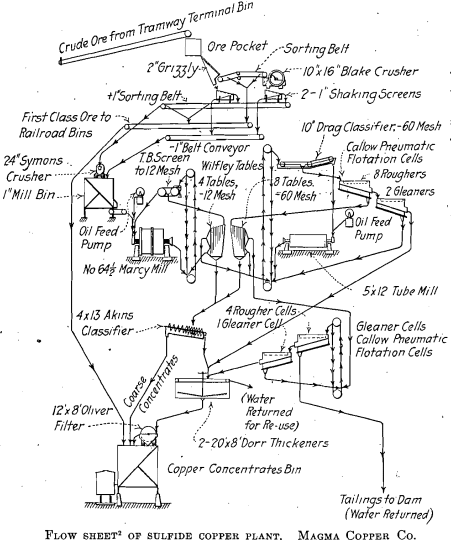
Many of our largest copper deposits contain both sulfide and oxidized copper minerals. The large porphyry mines, with a total copper content of from 1.3 to 2.0 per cent., send to their mills ore with an oxide content of from 0.2 to 0.4 per cent. While the recoveries of the sulfide minerals are considered satisfactory, […]
Gold Ore Roasting Plant
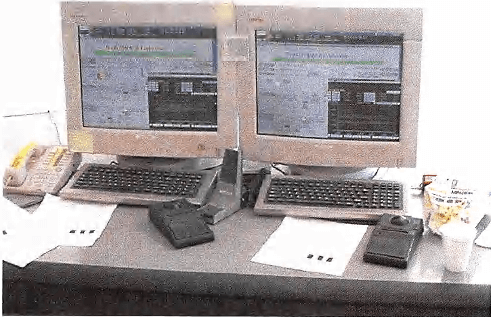
To achieve optimum gold recovery from the certain sulfide ore body, the ore must be finely ground to achieve proper oxidation and mineral separation. The ore is separated into stockpiles after it has been mined. These stockpiles are based on gold content, sulfide content, and carbonate content. The ore is blended prior to being fed […]
Chemical Smelting
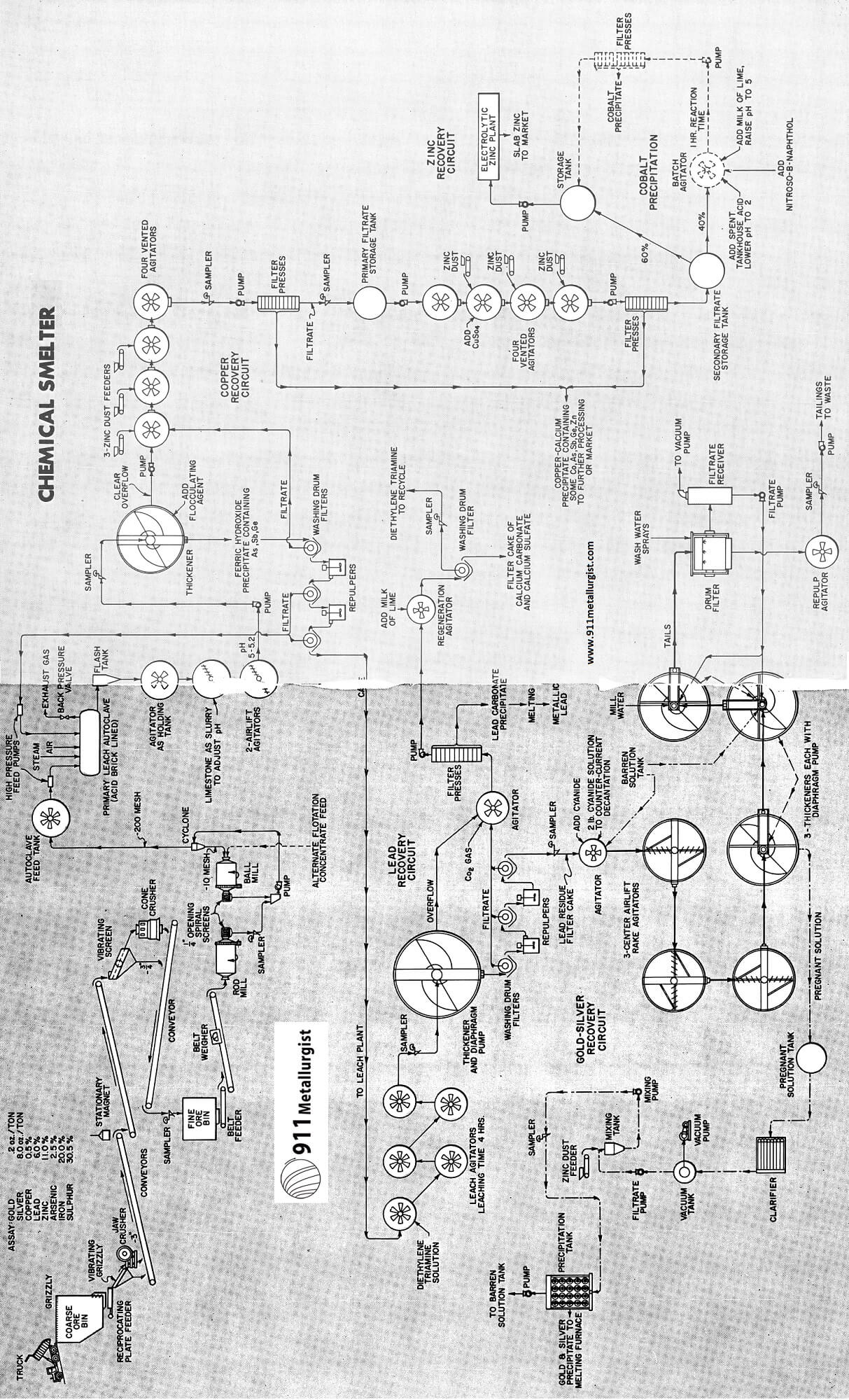
Some of us who have been acquainted with the present methods of production of metals, and who have had an opportunity to witness the impact of some of the newer chemical techniques on metallurgy, have become convinced that it is possible to consider seriously the treatment of sulfide minerals by strictly chemical methods as distinct […]
Electrolytic Refining
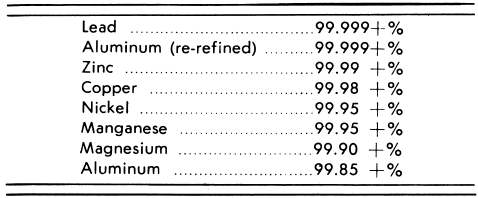
The list of pure non-ferrous metals so widely used in modern industry includes many that are produced by electrolytic means, such as copper, zinc, nickel, aluminum, magnesium, lead, sodium, cadmium, calcium and many others. In the case of some metals, ordinary fire or chemical methods of production are important, but in others, 100 per cent of […]
Leaching Mercury Sulfide
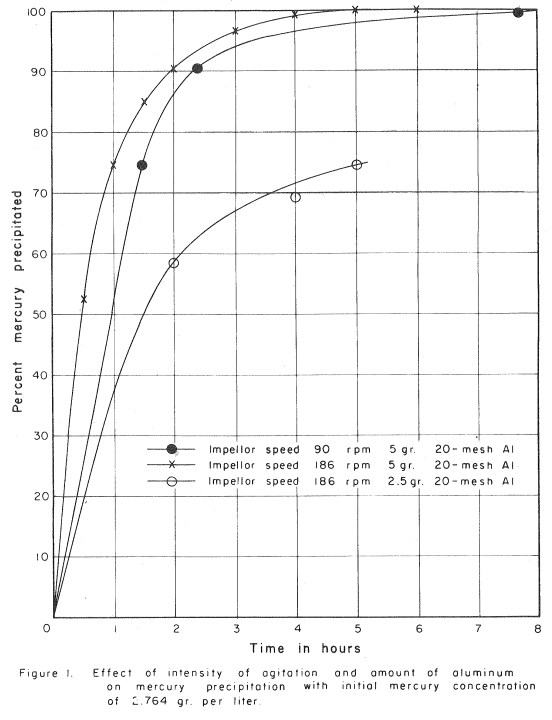
Hydrometallurgical methods have received increased attention for the treatment of many ores in recent years. Whereas, direct furnacing has been regarded as the standard process for mercury (cinnabar) ores, hydrometallurgical methods offer an alternate consideration. The chemistry of this process is not new, but with the impetus to hydrometallurgical methods, it is only logical that […]
LPF Process Metallurgical Testing

EXECUTIVE SUMMARY A Metallurgical Laboratory had completed preliminary economic studies on various processing options applicable to the Minerals Project in South America, containing oxide, transition and sulfide ore reserves. These included heap leaching with SX-EW; use of Roast-Leach-EW of sulfide concentrates to produce CuSO4 crystals; and potential application of the Leach-Precipitation-Flotation (LPF) option to treat […]
Recycling Sand from Foundry Casting Molds
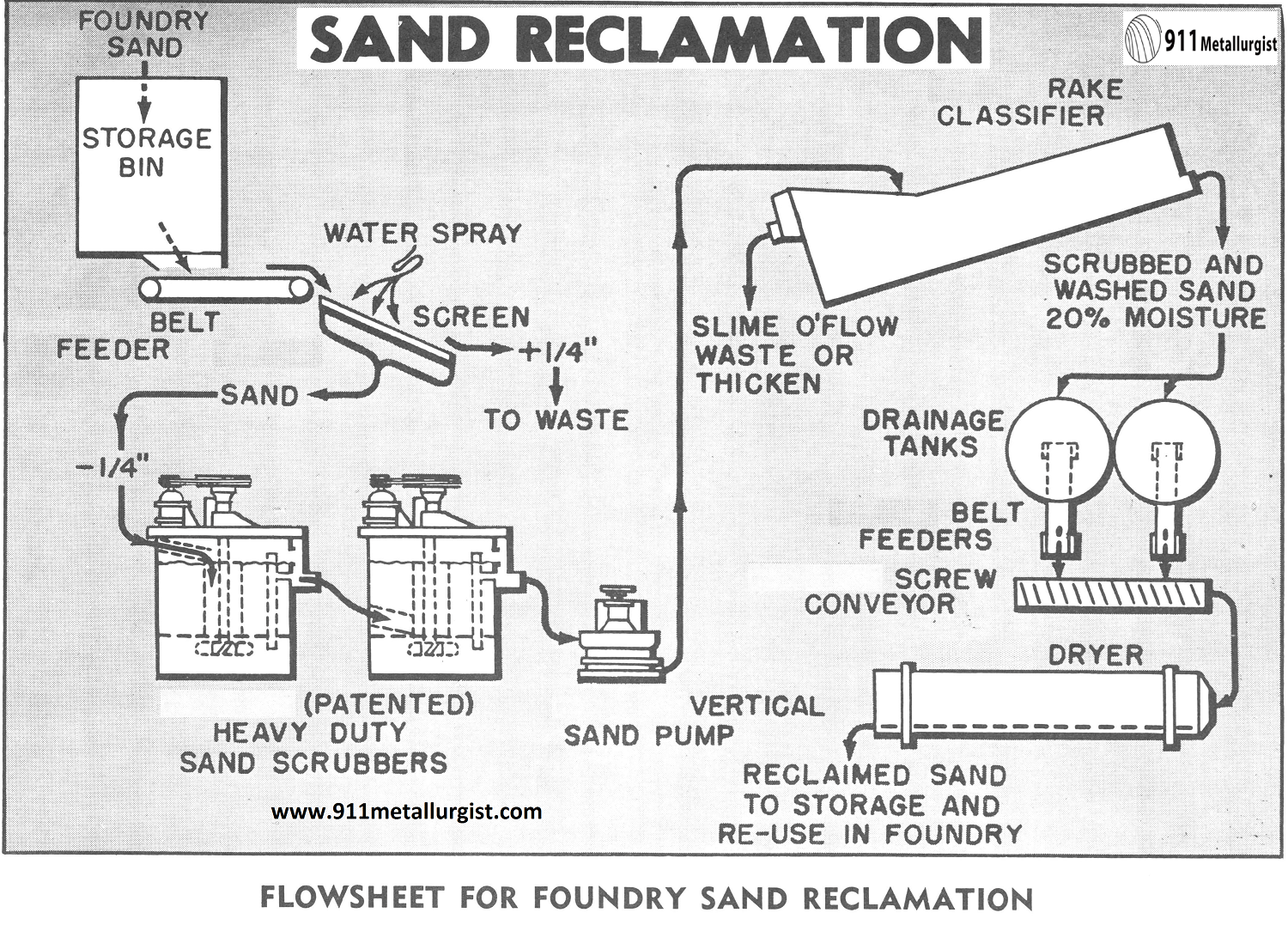
The flowsheet shown in this study is particularly adapted to the requirements of the average foundry to reclaim foundry sand for re-use. Any foundry whose new sand delivered costs is too high should seriously consider reclamation with the flowsheet as illustrated. This reclaimed sand is usually equal to, or better than the original sand. Foundry […]
Mining Business Plan
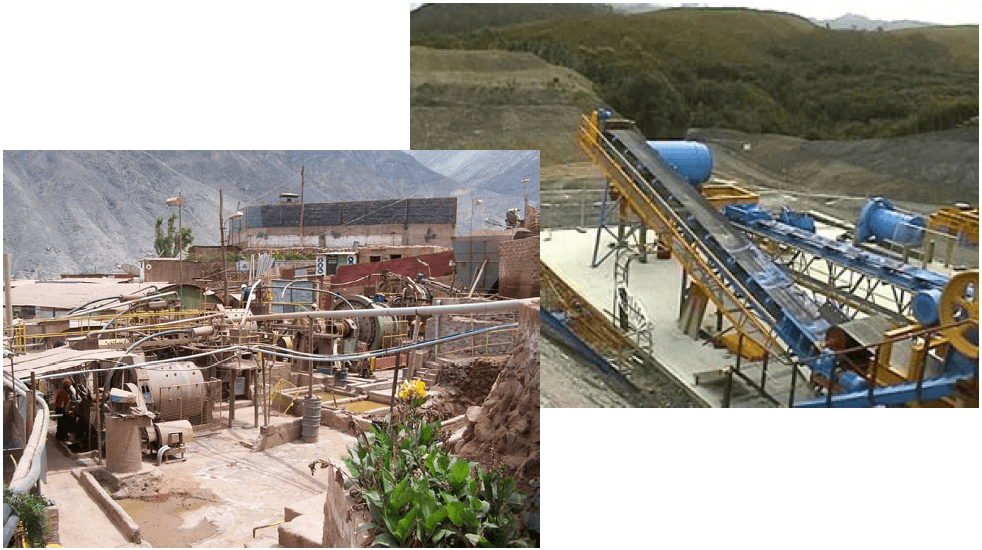
The following document outlines a mining business proposal to design and construct a free standing toll plant facility, known in this document as Peru Toll Treatment (PTT), in southern Peru to accommodate the needs of a growing quantity of small scale miners who produce up to 14 percent of the country’s annual gold production. The […]
Metallurgical Testwork for Process Development
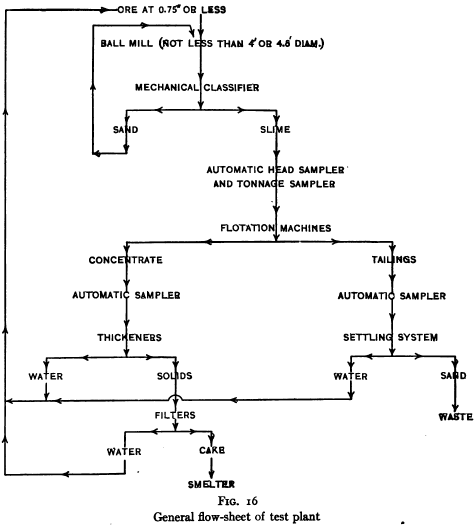
Mineralogy & Microscopy Amenability of an ore to flotation is best tested for by a microscopic examination of the ore followed by a few laboratory flotation tests. As stated in Chapter I, most ores containing minerals of metallic, resinous or adamantine luster associated with minerals of earthy, vitreous, or pearly luster, can be divided by froth flotation […]