Use of Bleaching Clays in Water Purification
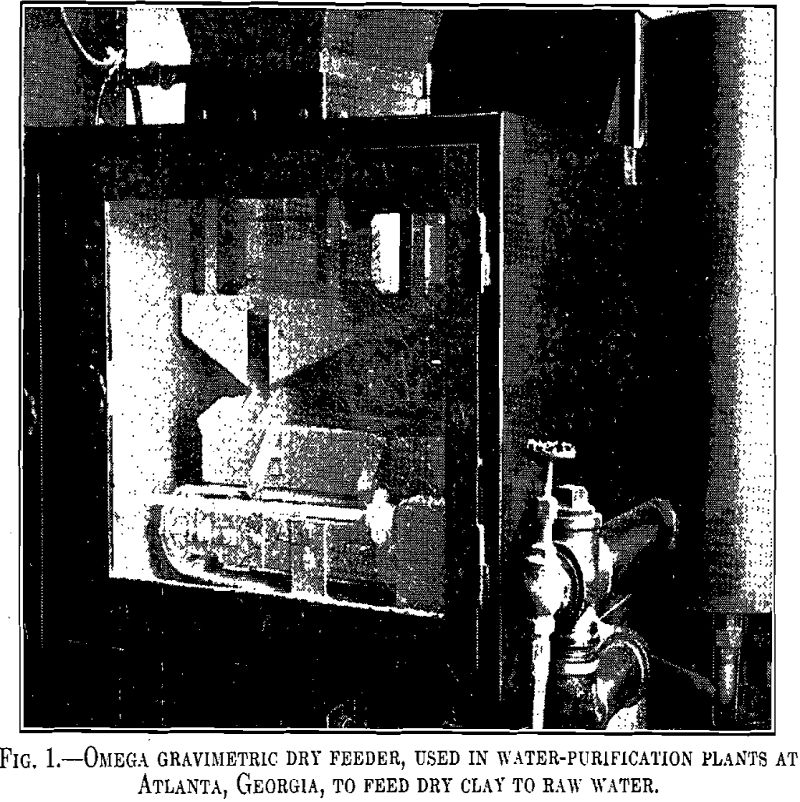
Bleaching clays have been used extensively in the oil-refining industries for a number of years. Their use in water purification is relatively recent and less extensive. They are frequently classified as (1) those naturally active and (2) those active after artificial activation with acid. Fuller’s earths fall within the general group of bleaching clays and […]
Hydraulic Backfill Characteristics with Flocculants
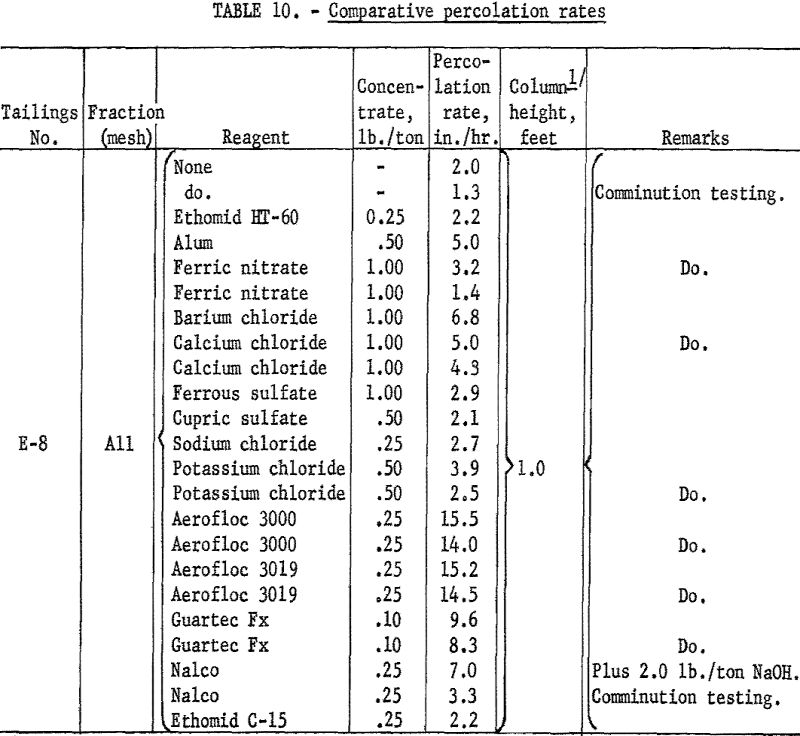
Two practical methods for controlling the physical properties of mill tailings for underground stope backfill may be used. The first is classification to remove objectionably fine size fractions, and is commonly employed. The second method, flocculation, has had very limited application. It is the subject of this investigation. This report covers preliminary laboratory studies of […]
Ferrous Iron Oxidation by Activated Carbon
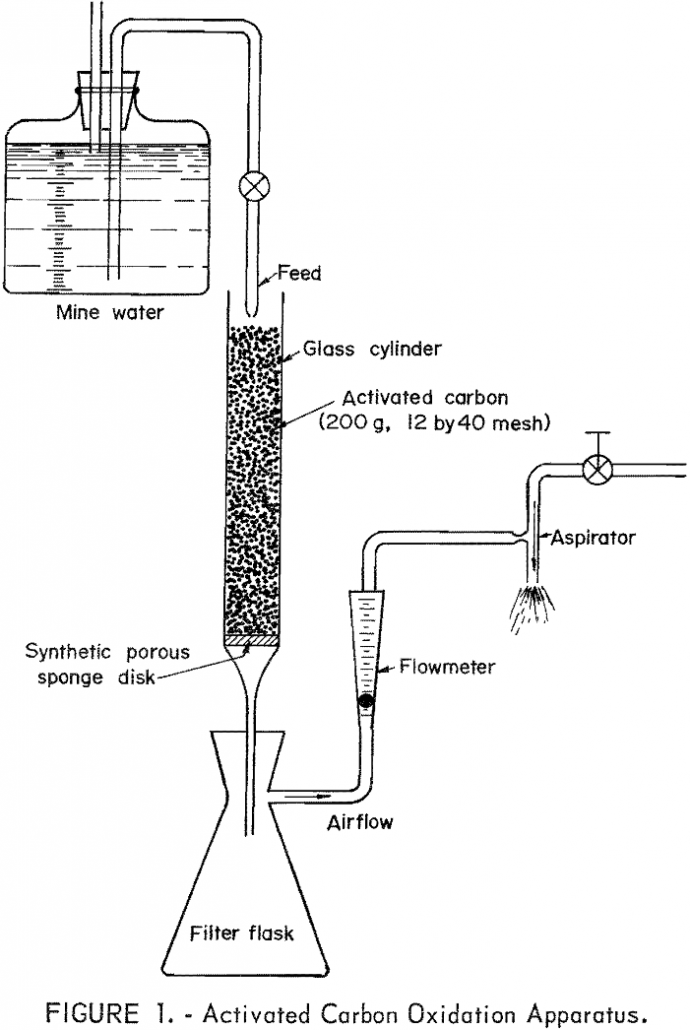
The exploratory tests conducted with activated carbon and a ferruginous acid mine water indicate that ferrous iron oxidation takes place catalytically at an extremely rapid rate. The brevity of this study did not allow defining the reaction kinetics, or resolving the various factors affecting the activated carbon-air-acid mine water system. The favorable preliminary results warrant […]
How to Stabilize Uranium Tailings
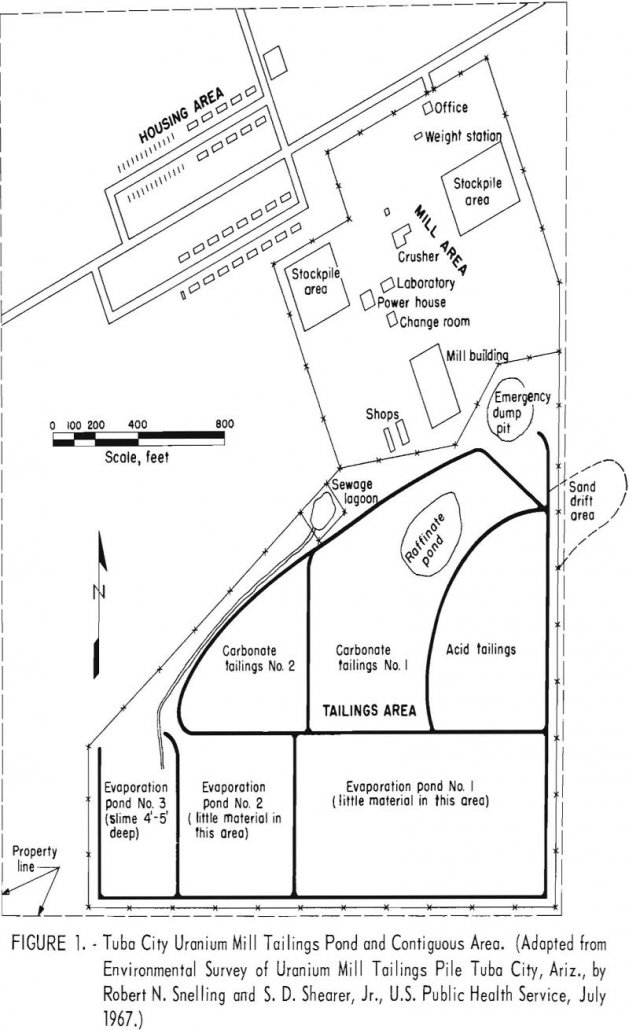
An environmental radiological survey was conducted on the El Paso Natural Gas Co. uranium tailings pile at Tuba City, Ariz., in May 1967, by the South-western Radiological Health Laboratory of the Public Health Service, U.S. Department of Health, Education, and Welfare (HEW). As the abstract of the reports of the survey summarizes the pertinent facts […]
Recycling and Disposal of Solid Mining Wastes
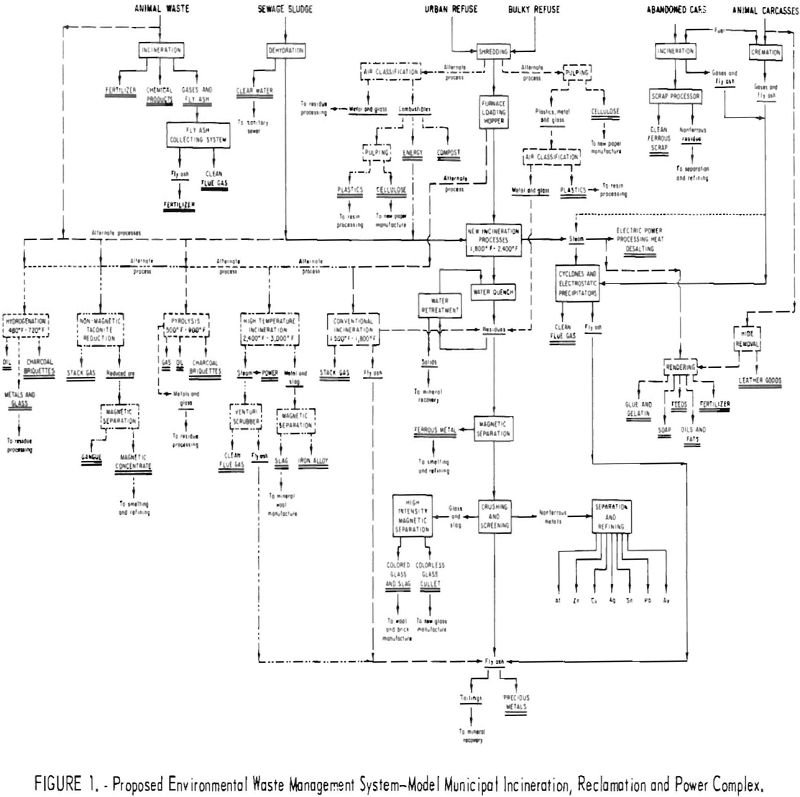
The Interior Department’s Bureau of Mines has always considered the waste products and scrap generated by the mineral and metals industries and the consuming public as potential resources, The Bureau has been active in reclaiming values from byproducts of mineral, metal, and energy processes for over 50 years. This statement is supported by the continuity […]
Recover Uranium from Water by Countercurrent Ion Exchange
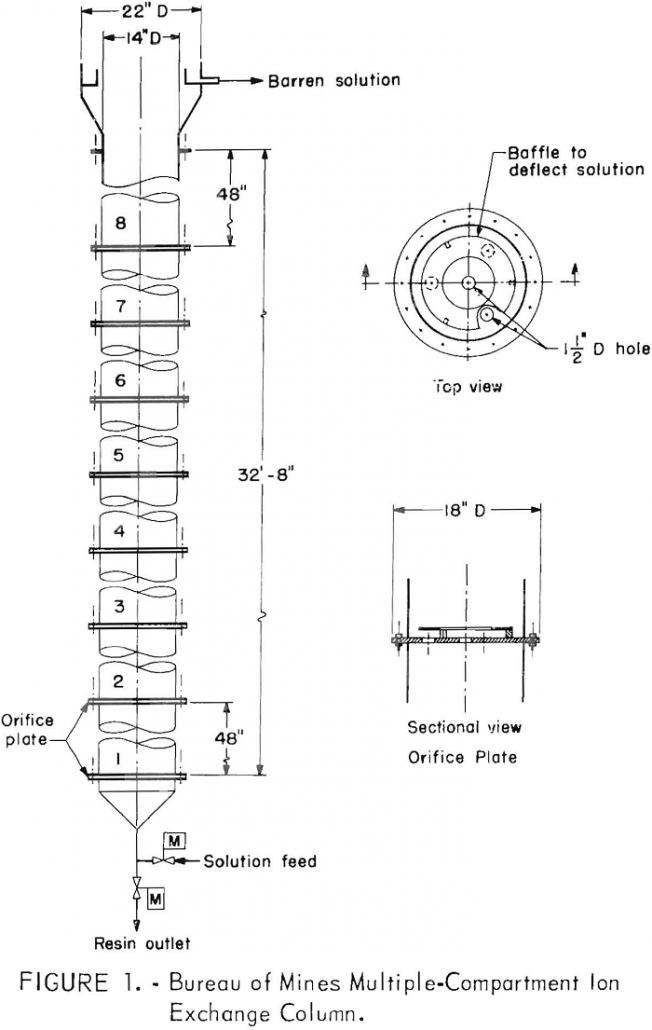
Ion exchange techniques have been used to recover uranium from waters pumped from uranium mines in the Ambrosia Lake district of New Mexico since about 1963. More recently., the natural flow of mine water and the recovery of uranium have been augmented by routinely spraying abandoned areas of the mine with barren solution from the […]
Tailings Pond Seepage
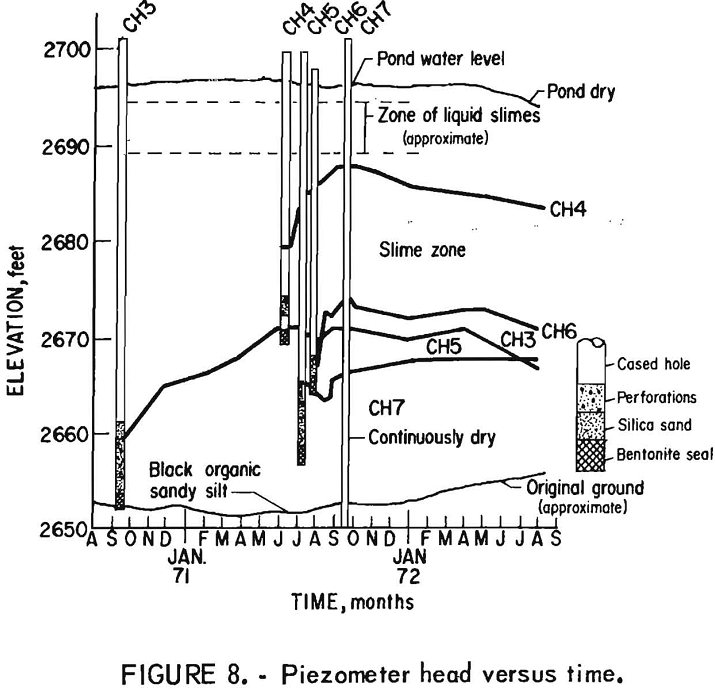
This report is a sequel to earlier Bureau of Mines investigations which indicated the need for a seepage environmental research investigation relative to the slime zone of a typical tailings pond. In the previous studies, slope stability and location of phreati.c surface were of prime concern; consequently, only the outer portion of the pond embankment […]
Mine Water Chemistry – Is Process Water Hurting my Results
Mines are recycling more water than ever before. This is a logical response to water stresses (see our article on Water Balances). However, there is a risk associated with the good stewardship of water. Deleterious elements and compounds can concentrate in recycled mine water as it is recycled again and again, and these deleterious elements […]
Mill Tailings Dam Stability
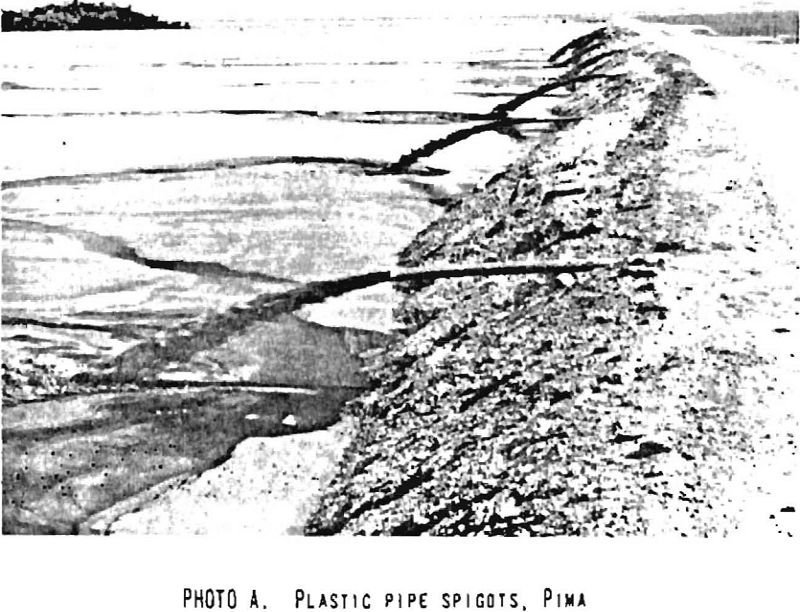
The reconnaissance-level investigations were carried out to gather supplemental data to the in-depth studies of Kennecott’ s Magna and Phelps Dodge’s Morenci tailings deposits and Kennecott’s Chino leaching dump. The data were obtained by personnel of W. A. Wahler and Associates to determine to what extent the disposal systems and techniques used at the three […]
How to Recover Barite from Waste Pond Materials
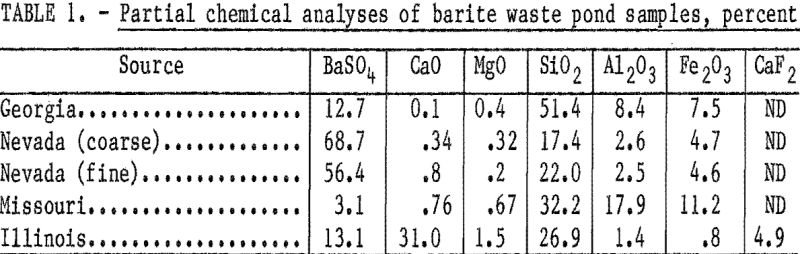
A major goal of the Bureau of Mines is resource conservation, which includes (1) maximizing mineral recovery from domestic resources and (2) recovering mineral values currently lost in scrap and waste materials. To help meet this goal, the Bureau of Mines has been investigating the recovery of various potentially valuable minerals from mineral- processing wastes. […]