Wilfley Table
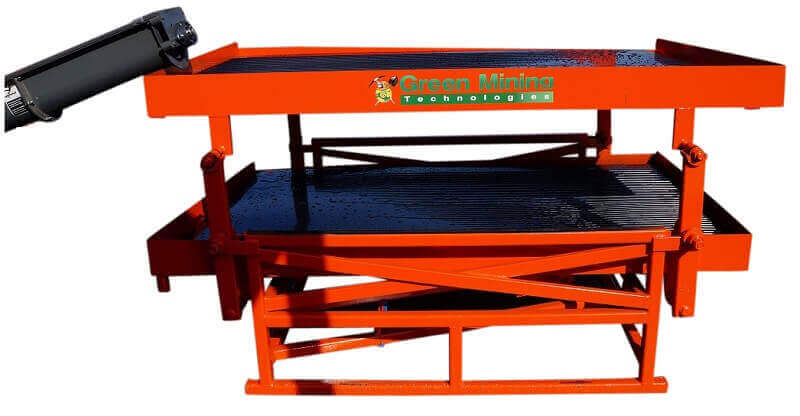
The Wilfley table is a truly remarkable gold concentrating tableĀ first built on a preliminary scale in May, 1895. The first full-sized table was built by Mr. A. R. Wilfley, and was used in his own mill in Kokomo Colo., in May, 1896. The first table sold for installation was placed in the Puzzle mill, Breckenridge, […]
Sulfide Oxide Lead Zinc Transitional Ore Treatment Processing Method
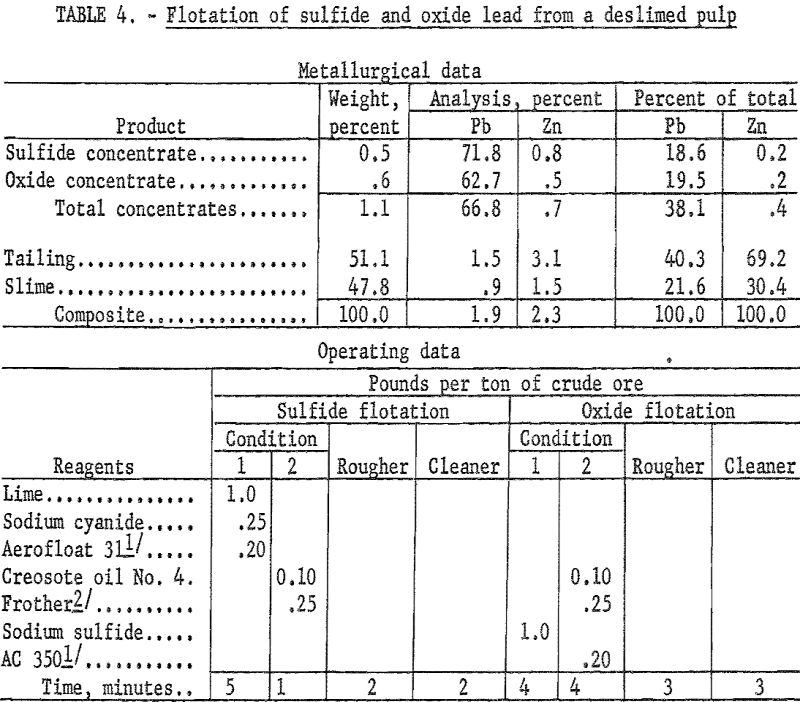
The mineral dressing research here reported is part of a continuing program by the Bureau of Mines to develop new or improved concentration processes for oxidized or partly oxidized lead and zinc ores. A sample of low-grade sulfide-oxide, lead-zinc ore from Jasper County., Mo., containing galena, cerussite, pyromorphite, hemimorphite, smithsonite, and sphalerite was concentrated by […]
Black Sand Minerals in Gold Placer Deposit
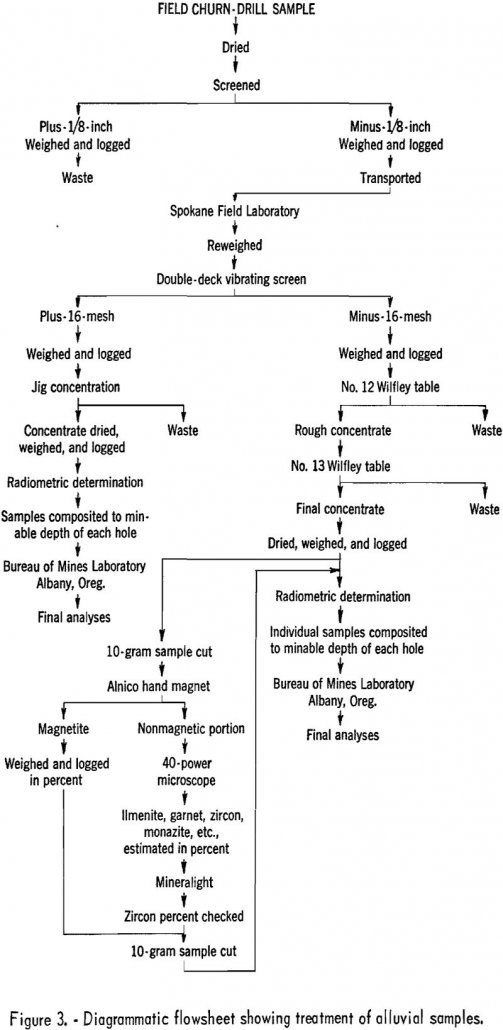
This report describes work done as part of a Bureau of Mines program to appraise the titanium-mineral resources of Idaho. The work included both field reconnaissance and a spot churn-drilling program. Much general information was available, as a result of earlier work done under the Western Radioactive Minerals Exploration Program conducted between 1950 and 1954 […]
Heavy Liquid Testing Procedure
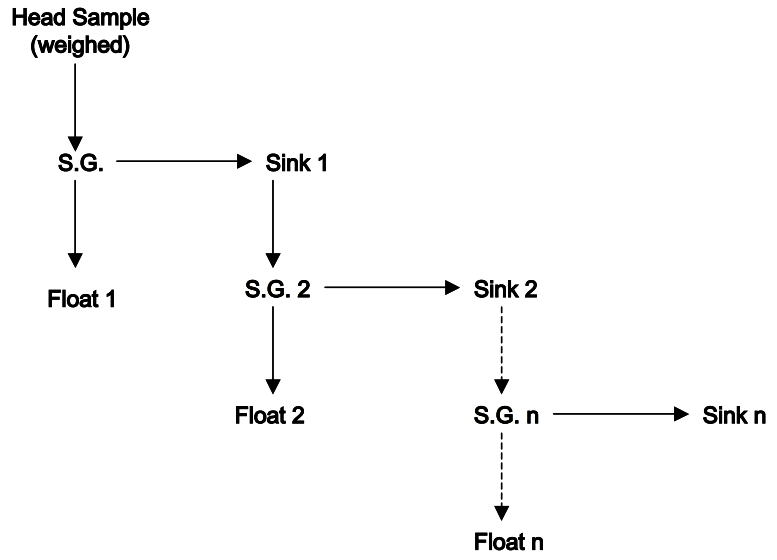
The general procedure is as follows. The sample is placed in the liquid of lowest specific gravity and is split into two fractions. The float fraction is set aside to be weighed and assayed. The sinks fraction is washed in a suitable solvent, dried and placed in the liquid of a higher specific gravity. This […]
Heavy Liquid Separation
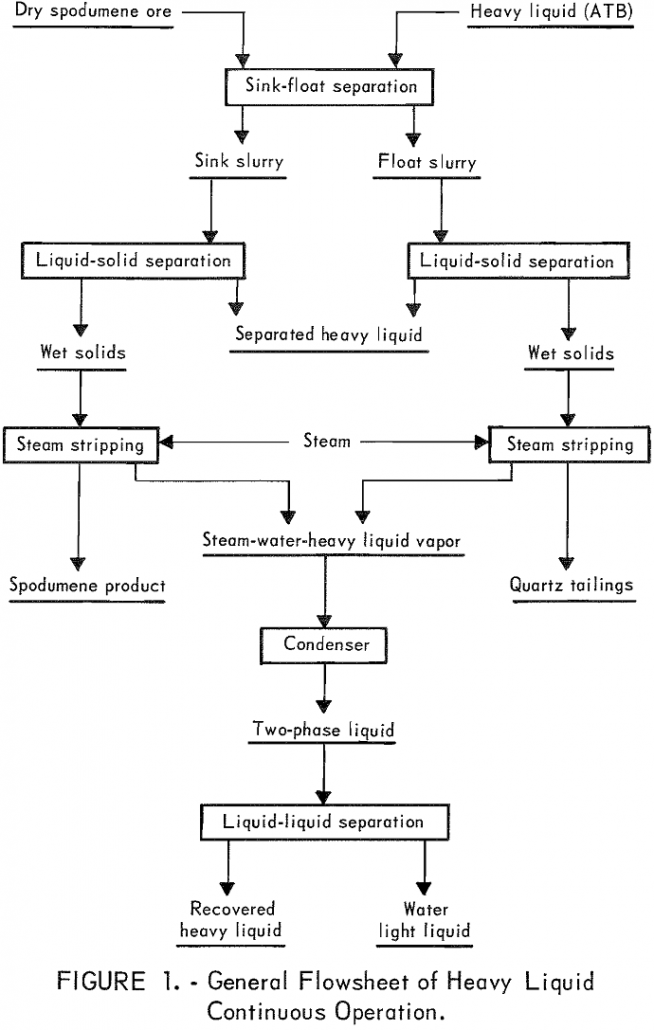
We are continuously engaged in research activities to develop or improve methods of utilizing our mineral resources. One such method, heavy liquid separation (HLS), has long been a recognized laboratory technique to separate minerals but only in recent years has this method been considered as a continuous process. The best prospects appear to be the […]
Heavy Liquid Cyclone Separation
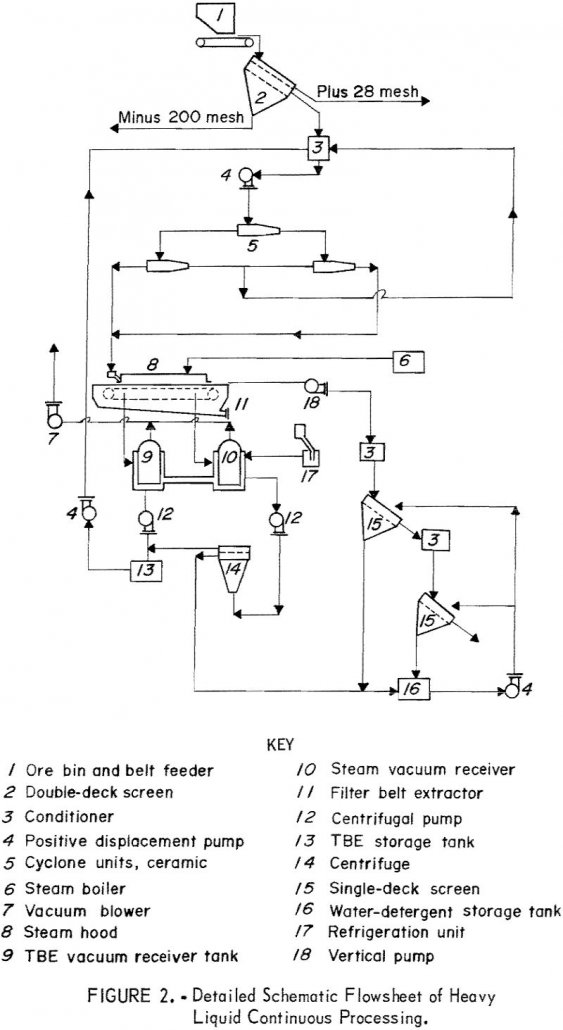
Kyanite ore deposits occur in the Southeastern United States. The ore reserves in this area are estimated at about 100 million tons having an average grade range from 10 to 30 percent kyanite. The Graves Mountain kyanite-quartz rock ore deposit consists of a prominent ridge about 1 mile long and 300 to 400 feet high. […]
How to Remove Bismuth from Lead
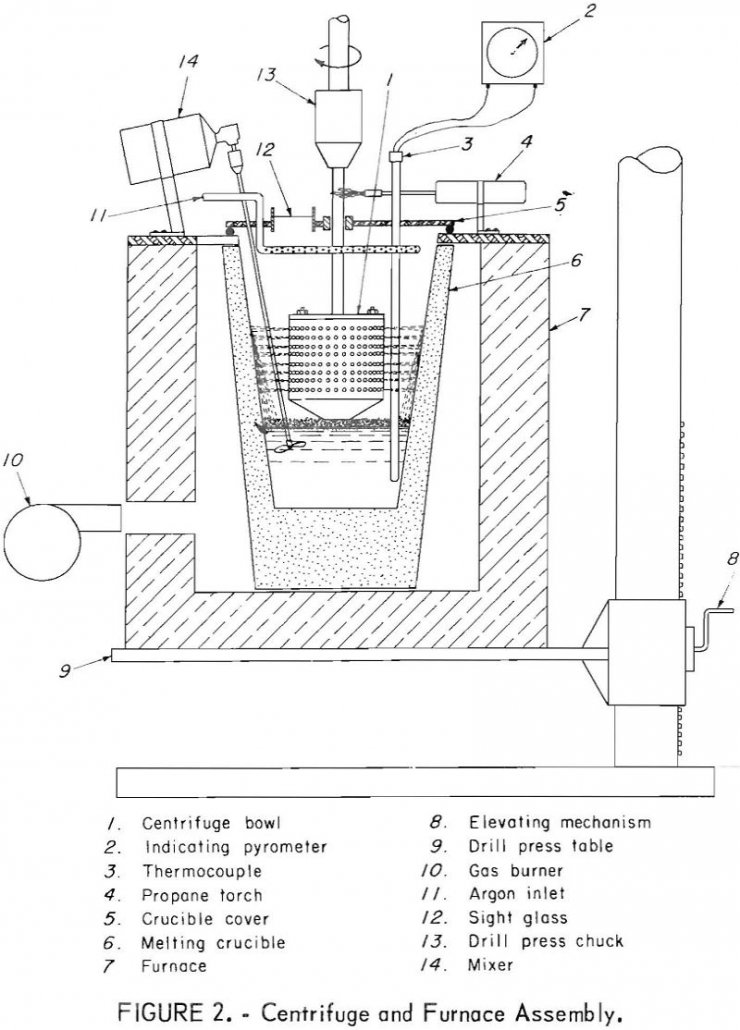
The Betts electrolytic process was for many years the only method available for debismuthizing lead Kroll suggested the use of calcium to form a high-melting-point Ca-Bi intermetallic compound that could be separated from molten lead. This process, however, was not used industrially. About a decade later, Betterton developed a commercially feasible process using a combination […]
How to Remove Pyrite from Coal
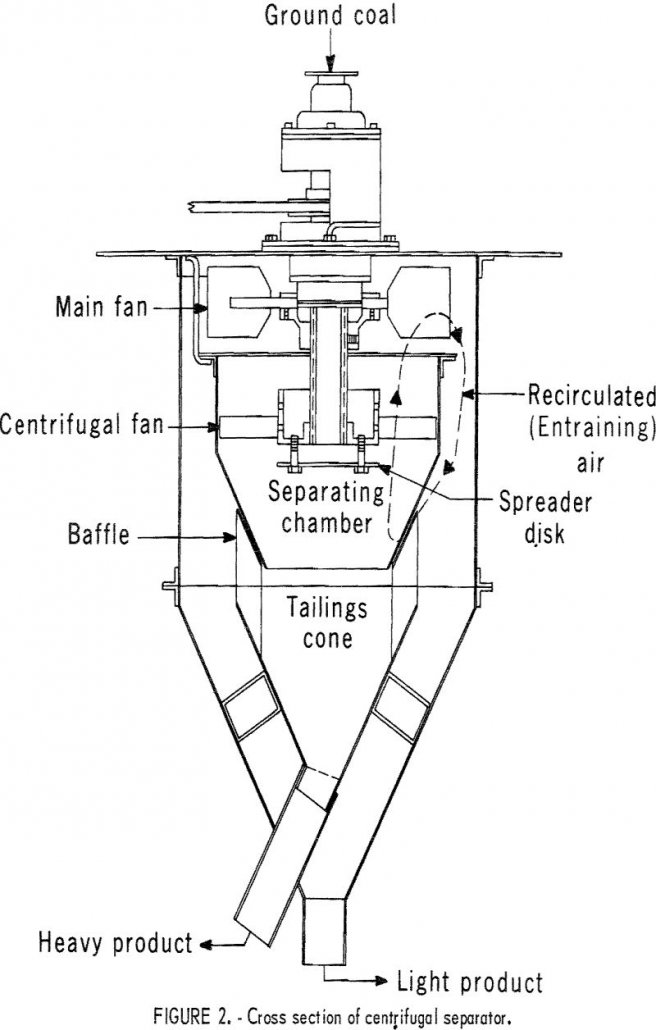
In recent years, coal research has been directed toward environmental problems of the electric power generation industry. A major problem of coal-burning power-plants is reducing the air pollutants in stack gases. In most of these plants, the chief pollutant is SO2, which results from the combustion of sulfur compounds present in the coal. Stack-gas cleaning […]
Bowl Concentrators
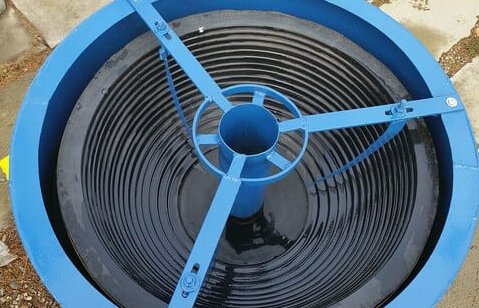
Bowl concentrators have been used only to a limited extent in small placer operations. The two most popular designs were the Ainlay and Knudsen bowls. There is little difference in design and operation between the two, except for riffle design and minor variations in bowl size and shape. They were used primarily as cleaners, but […]
Mineral Jig Concentrator
The Duplex Mineral Jig Machine belongs to gravity concentrating device that separates material based on differing densities of the material. The Jig is widely used in concentration of heavy minerals such as tin, gold, tungsten, manganese and barite. The 911MGTK-XCT Laboratory Mineral Jig Machine is an ideal instrument for research of beneficiation of ferrous metal […]