Asbestos Mining Methods and Costs
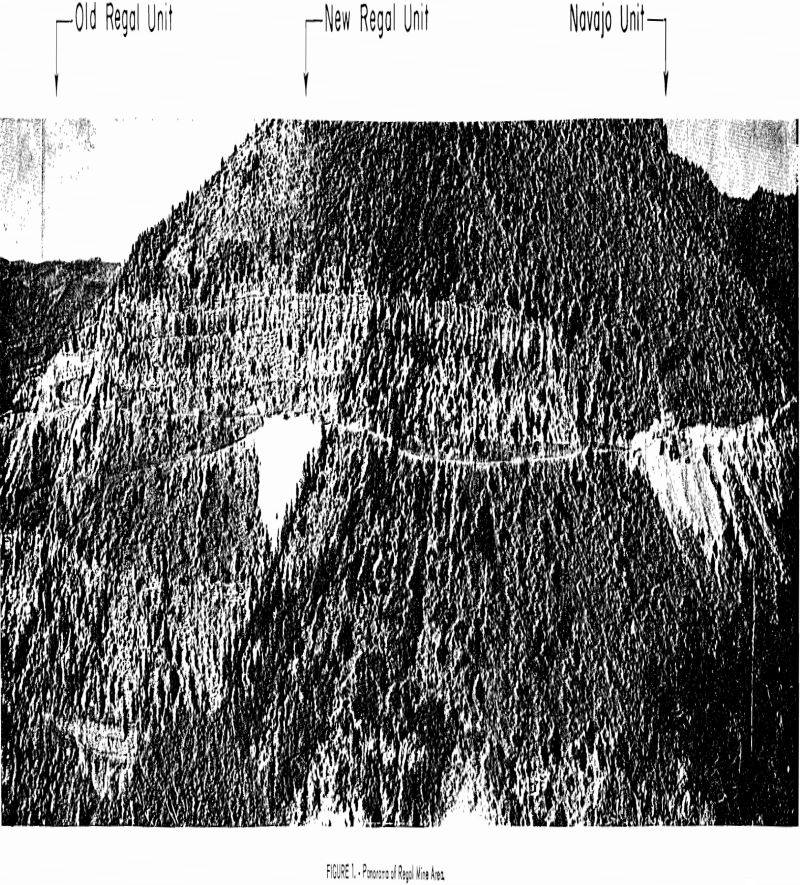
This is one of a series of reports prepared by the Federal Bureau of Mines on mining methods, performance, and costs at individual mines in the United States. The primary purpose of these papers is to promote development and conservation of our mineral resources by disseminating technological information on methods, practices, and results that may […]
Uranium Mining
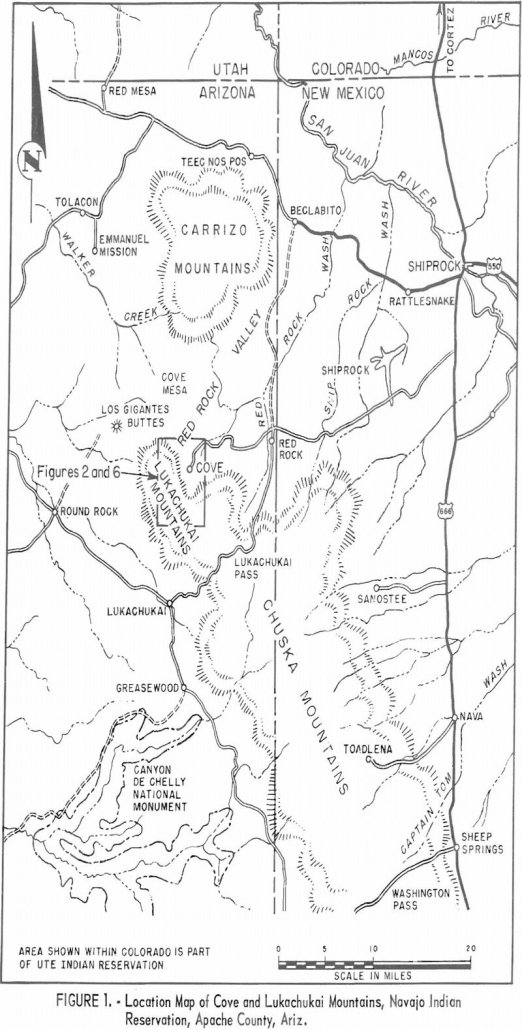
This report is one of a series published by the Federal Bureau of Mines to describe methods and costs of mining uranium on the Colorado Plateau. The Navajo Uranium Division of Kerr-McGee Oil Industries, Inc., mines uranium from several deposits of carnotite-type ores, which lie buried in the Lukachukai Mountains on the Navajo Indian Reservation, […]
How to Design an Underground Mine Opening in Rock
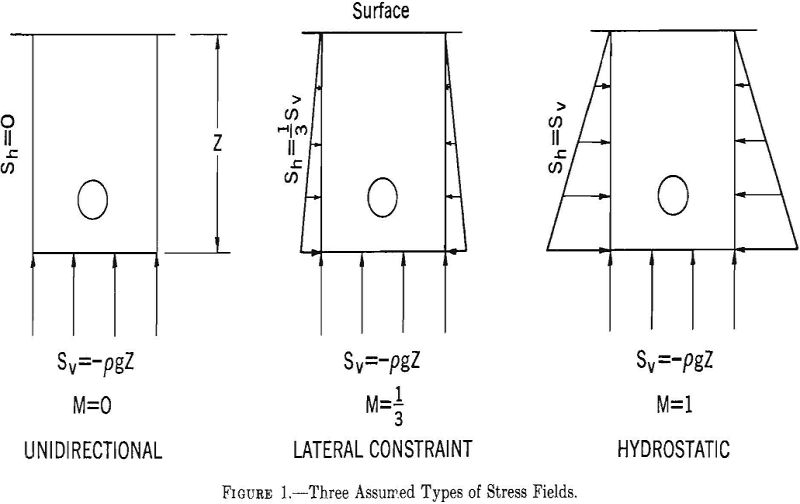
The design and stability of underground openings are problems of paramount importance in mining. Insuring the safety of employees, protecting equipment, mining in a prescribed and efficient manner, and (in mineral mining) achieving an optimum recovery from the deposit depend upon the ability of engineers to design and excavate underground openings that will remain open […]
Testing Method Mine Anchorage Roof Bolts

Two methods of testing anchorages of headed expansion-type mine roof bolts were investigated by the Federal Bureau of Mines to determine whether they are acceptable for general use. In both methods a load was applied to a tightened bolt with a hydraulic jack. A total of 80 tests, 40 using each method, was conducted in […]
Mining Consultants List
Mining consultants play a major role in the feasibility, planning, design and construction, operation and improvement of both small and large mines. Consultants are experienced design engineers, mine designers, operating specialists or maintenance engineers who operate independently of operating mines. They are available to work on: mineral exploration projects, where start-up companies have not yet recruited […]
Brown Iron Ore Mining
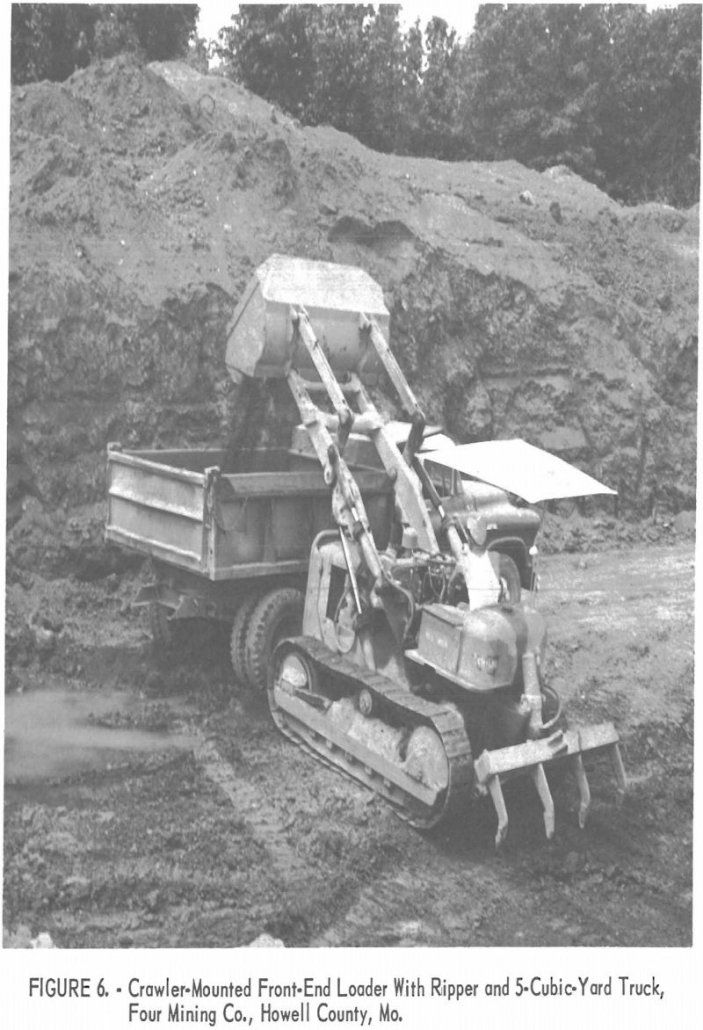
Most brown-iron deposits of southern Missouri occur in residual materials resting on Jefferson City dolomite, Roubidoux sandstone, or Gasconade dolomite, all of the Ordovician system (see table 1). The residual materials, which consist mainly of clay, chert, and iron oxides, are products of weathering of sedimentary rocks younger than the Jefferson City dolomite. Deposits of […]
High Speed Camera in Rock Blasting
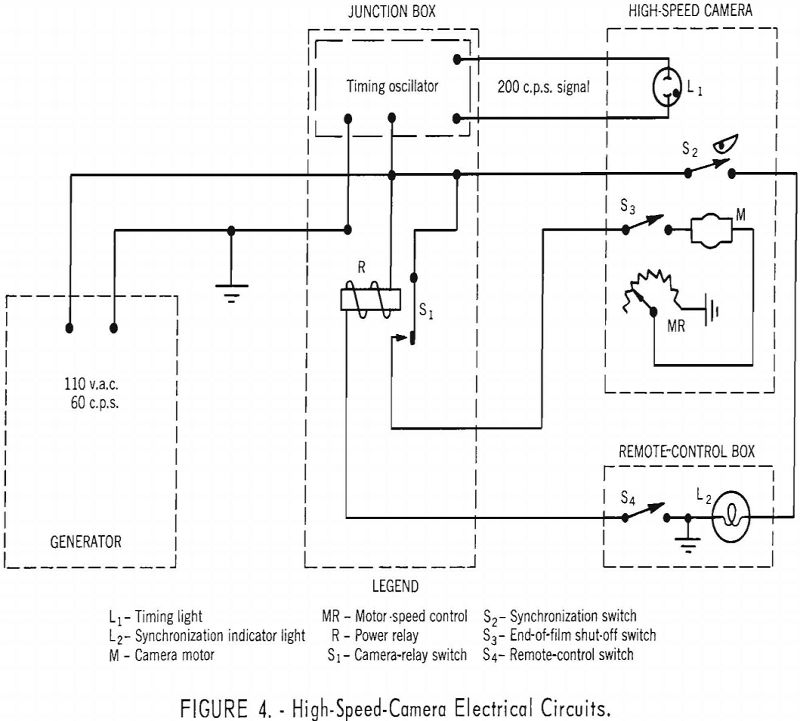
The breaking of rock by explosives occurs so rapidly that the details of the phenomenon cannot be observed by the unaided eye. High- (frame-) speed motion pictures offer a means of slowing down the blasting action so that the various phases of the process can be observed and studied. During the last 10 years, both […]
Tungsten Mining Method & Cost
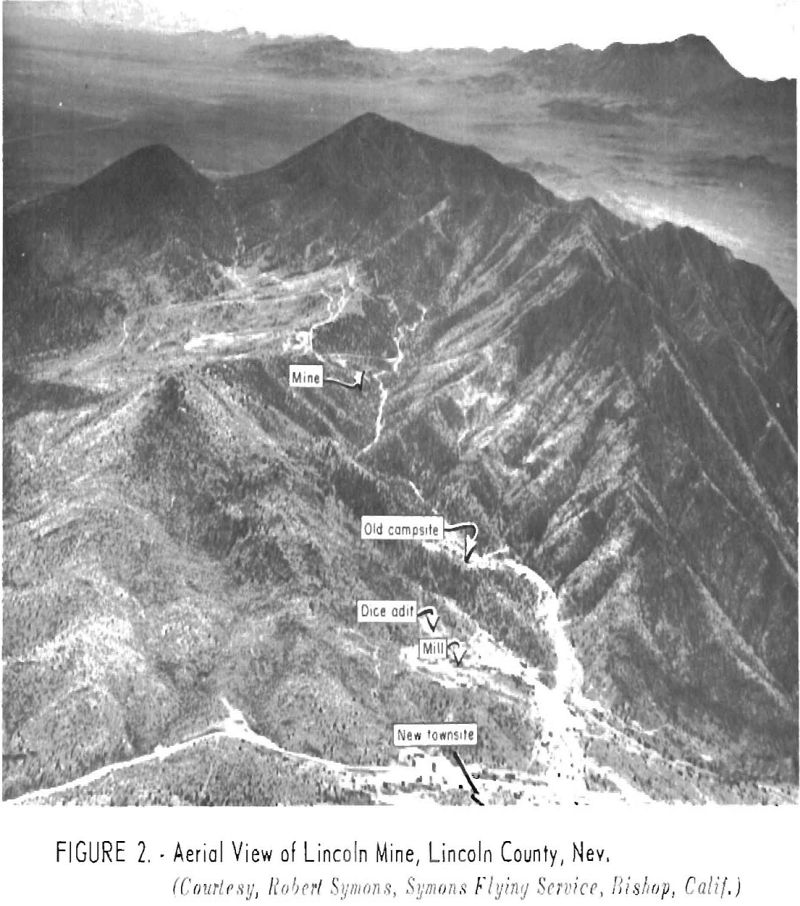
The principal ore deposits occur in the bands and isolated pods of tactite adjacent to the granite on the west side of the south stock. The tactite bodies exposed around the north stock are narrow and discontinuous, although one series of lenses on the northeast side has a total length of 400 feet and averages […]
Gypsum Mining Method & Cost
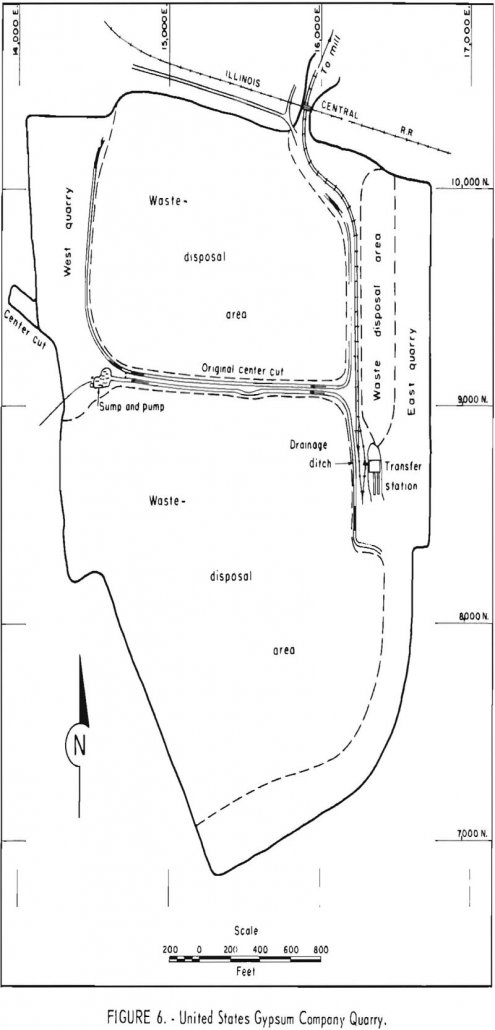
Gypsum and its products are economical materials in their respective fields. Lime and hydraulic cement plasters compete to a limited extent with gypsum in the plaster field. Lime is used today in construction, chiefly as an ingredient in the finish coat over gypsum-plaster base coats. Gypsum plaster is mixed with water and aggregates, such as […]
Mine Shaft Sinking
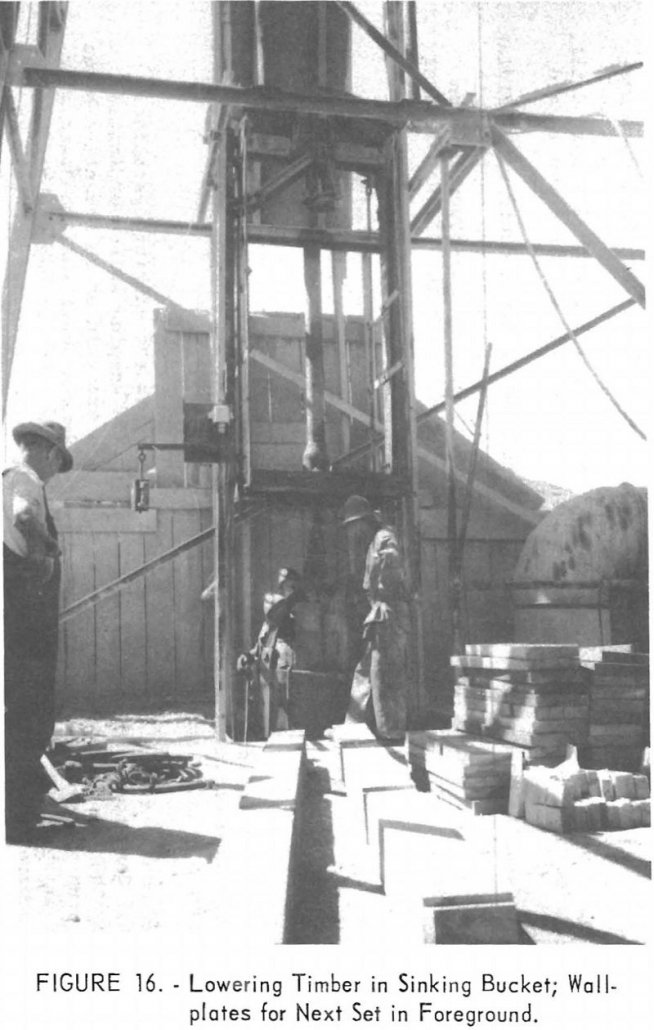
This paper is one of a series prepared by the Bureau of Mines on shaft sinking methods and costs in various districts throughout the United States. The Burgin shaft was sunk as part of the exploratory program of the East Tintic project of Bear Creek Mining Co. The Tintic district is in Utah and Juab […]