Testing Method Mine Anchorage Roof Bolts

Two methods of testing anchorages of headed expansion-type mine roof bolts were investigated by the Federal Bureau of Mines to determine whether they are acceptable for general use. In both methods a load was applied to a tightened bolt with a hydraulic jack. A total of 80 tests, 40 using each method, was conducted in […]
Brown Iron Ore Mining
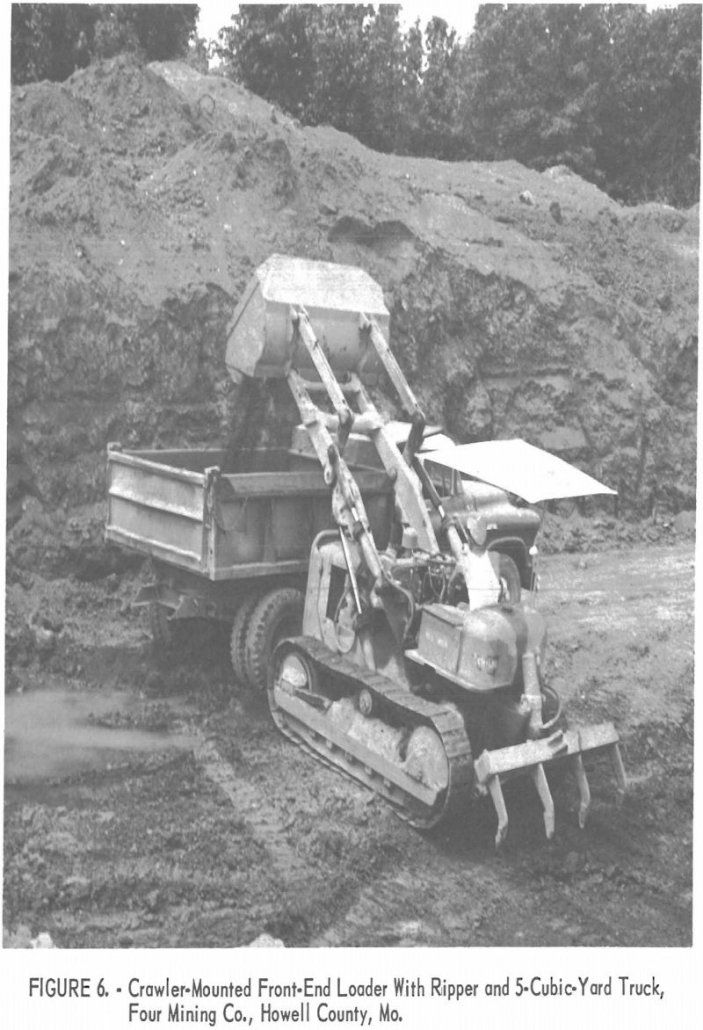
Most brown-iron deposits of southern Missouri occur in residual materials resting on Jefferson City dolomite, Roubidoux sandstone, or Gasconade dolomite, all of the Ordovician system (see table 1). The residual materials, which consist mainly of clay, chert, and iron oxides, are products of weathering of sedimentary rocks younger than the Jefferson City dolomite. Deposits of […]
Tungsten Mining Method & Cost
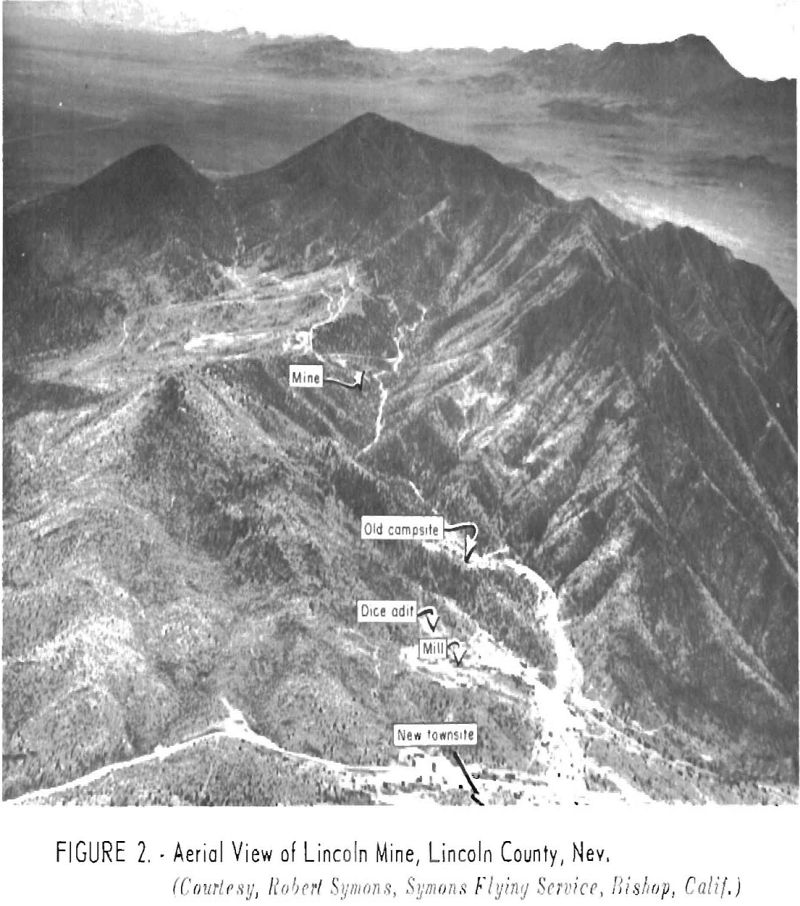
The principal ore deposits occur in the bands and isolated pods of tactite adjacent to the granite on the west side of the south stock. The tactite bodies exposed around the north stock are narrow and discontinuous, although one series of lenses on the northeast side has a total length of 400 feet and averages […]
Gypsum Mining Method & Cost
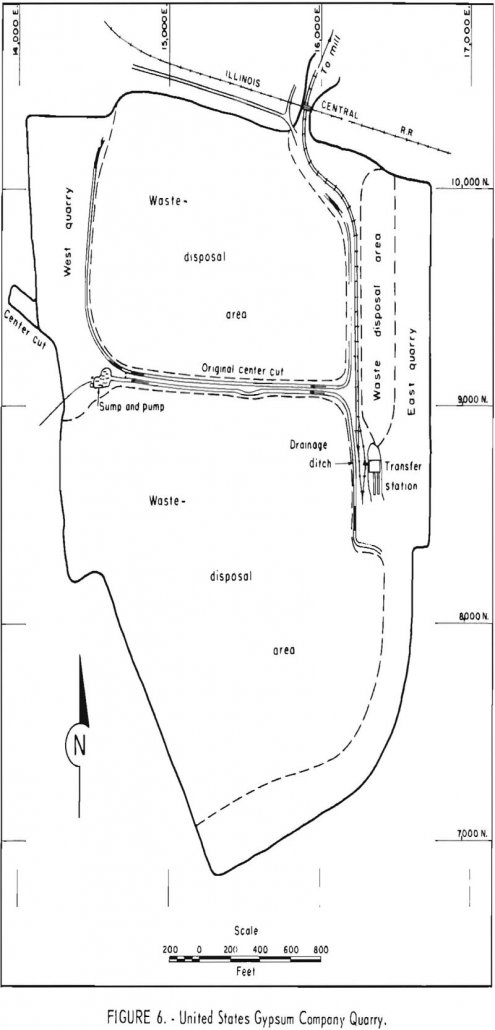
Gypsum and its products are economical materials in their respective fields. Lime and hydraulic cement plasters compete to a limited extent with gypsum in the plaster field. Lime is used today in construction, chiefly as an ingredient in the finish coat over gypsum-plaster base coats. Gypsum plaster is mixed with water and aggregates, such as […]
How to Identify the Surface Texture of Rock
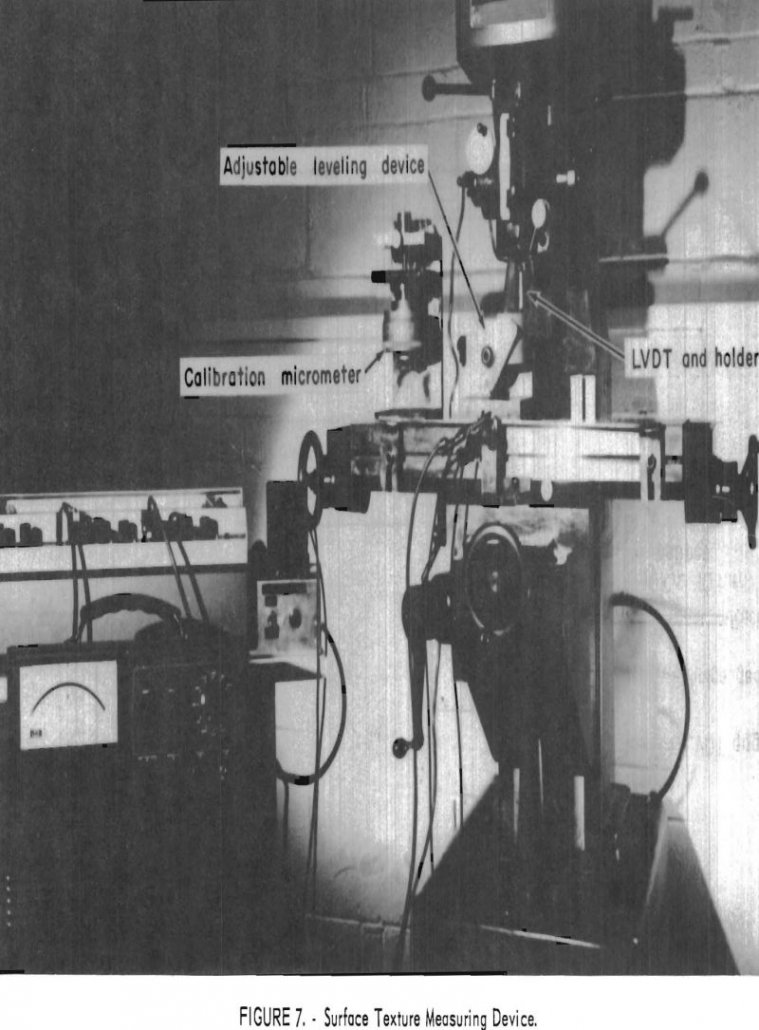
Model studies, using rock, require carefully prepared specimens. Most preparation procedures use some form of grinding or polishing as the last of several steps. During these steps, particularly the final one, the surface formed acquires a configuration defined as texture. Texture is a composite term identifying the physical features called flaws, lay, waviness, and roughness. […]
Drillability – Percussion Drilling
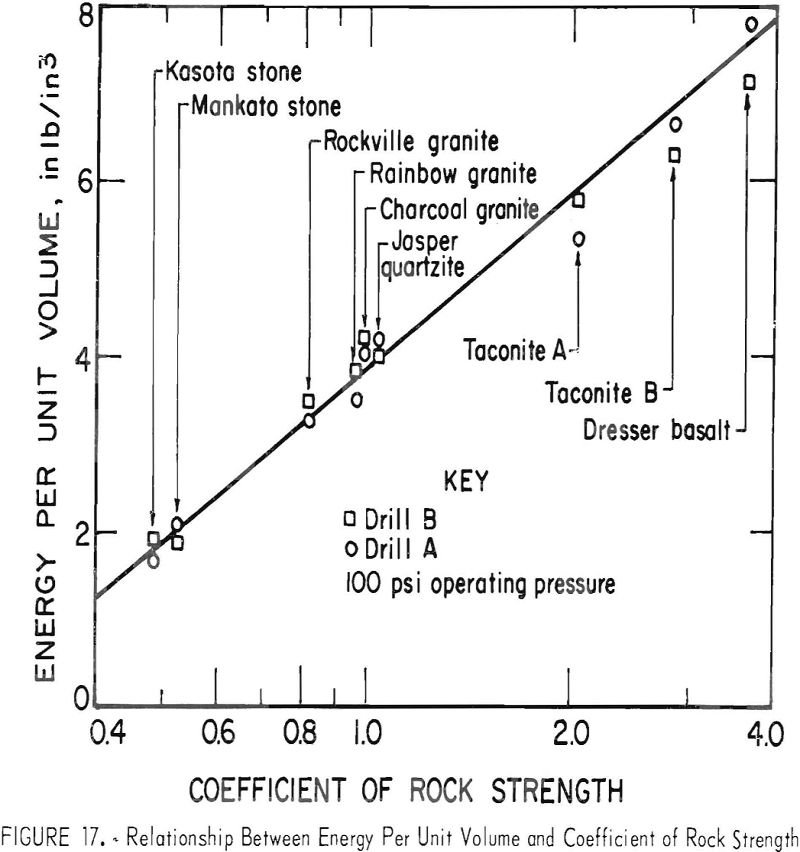
Penetration rate is increased by an increase in applied thrust up to an optimum point after which penetration decreases until the drill eventually stalls. Higher operating pressures result in increased penetration rates with the only apparent limitations being the design characteristics of the drill and bit and the ability to remove the cuttings produced. Rock […]
Rock Testing Procedure
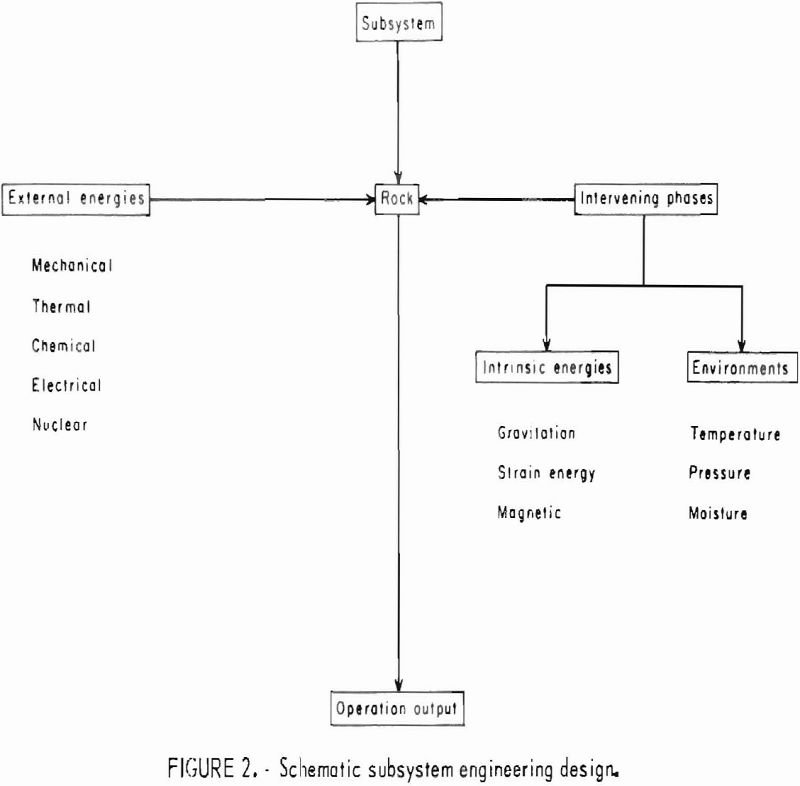
Design engineers involved with mine or tunnel construction require knowledge of rock behavior in order to assure economic excavation of rock and stability of underground openings. For many applications, the behavior of a rock is determined from an engineering approach involving rather empirical experiments. A greater emphasis is now being placed on the use of […]
Mine Stoppings
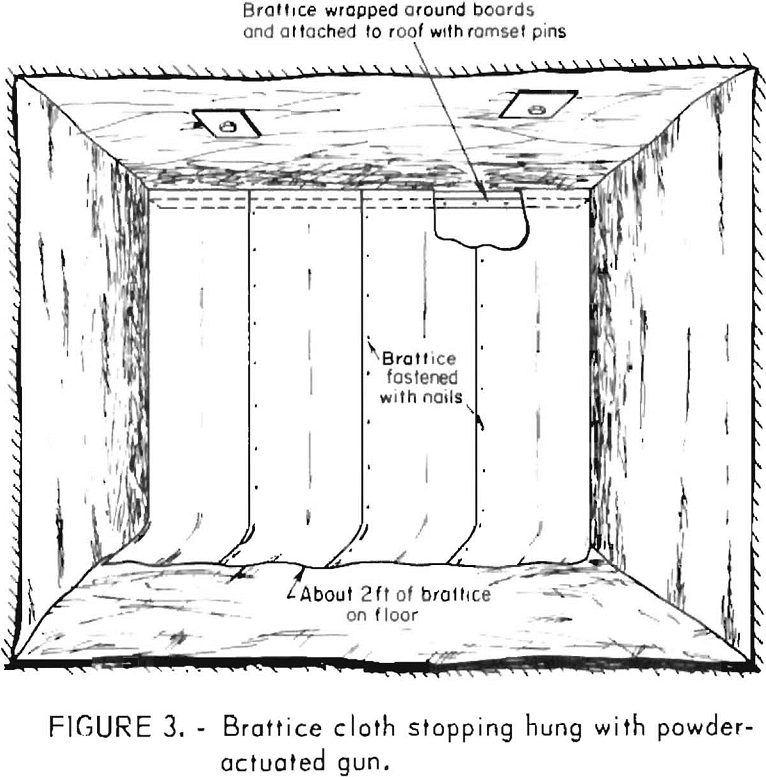
Most of the mines with large openings in the United States today are salt and limestone mines. Some potash and trona mines also have moderately large openings. Moreover, it is expected that in the near future numerous underground oil shale mines will be developed in the oil shale regions of Colorado, Utah, and Wyoming. These […]
How to Determine the Strength of a Mine Roof
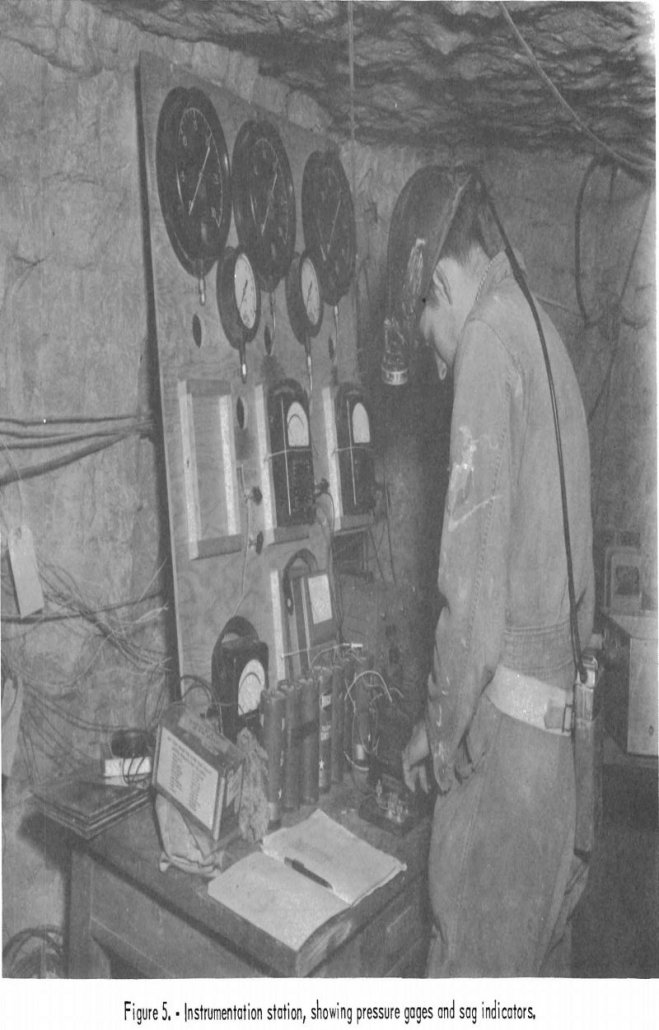
In an earlier phase of the investigation, an experimental room was progressively mined to an areal dimension of 50 by 100 feet. As the dimensions of the room were increased, the roof separated into horizontal layers that were loaded only by their own weight. The maximum stress and the elastic behavior of the lowest roof […]
Longwall Mining Method and Design
Studies estimate that 156 billion tons of coal, representing 68 pct of the minable reserves in the United States, is subject to multiple-seam mining. Historically, room-and-pillar mining has dominated coal production, and this mining method has been the focus of most multiple-seam research. Advances in Longwall Mining Method have made this system more economically attractive […]