Photoelectric Charging & Electrostatic Separation
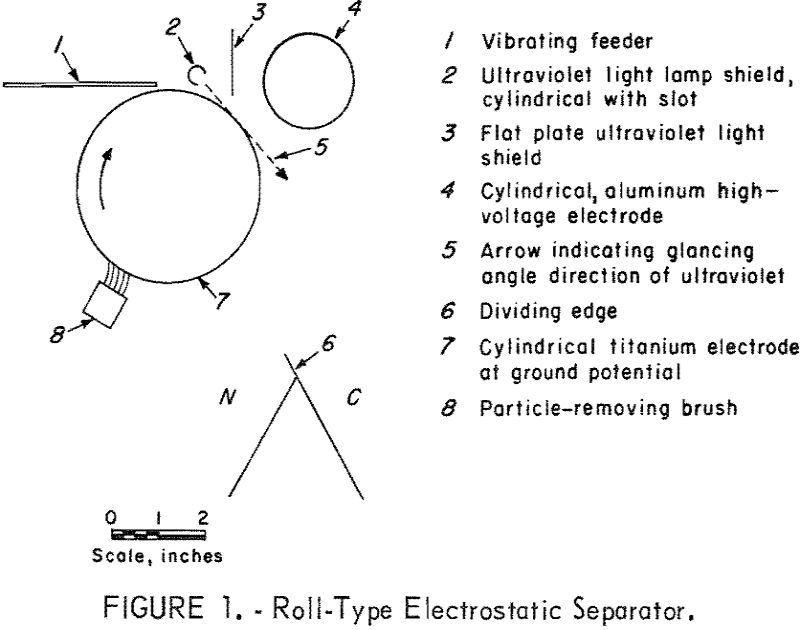
Electrostatic separation is used when froth flotation fails, such as with oxidized ores, or where there are similarities in response with magnetic and gravitational methods, or when the use of water is to be avoided. Theoretically, for fine-size particles the electric field has an advantage over the magnetic field in that the viscosity-limited particle velocity […]
Squeeze Cementing
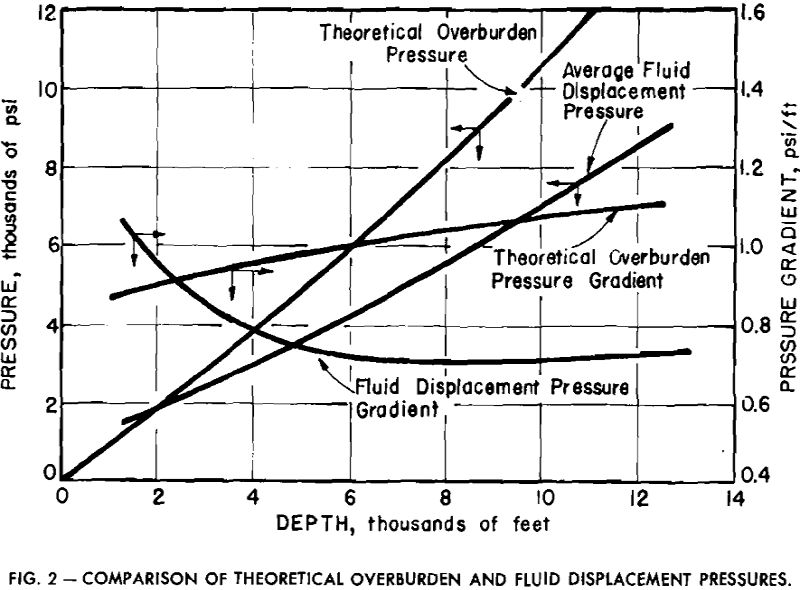
Laboratory and field testing of various squeeze cementing techniques and materials revealed that many improvements could be made in squeeze cementing operations. The use of a slow-pumping squeeze cementing procedure permitted the control of the quantity of cement displaced into a formation and aided in obtaining a high final squeeze pressure. Field testing indicated the […]
Convertol Process
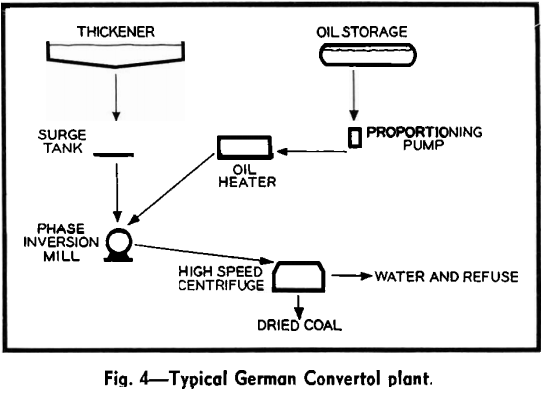
In the last several years the coal industry has intensified its effort to solve the growing problem of cleaning and recovering fine mesh coals. On one hand there has been increasing civic pressure for cleaner streams, and on the other hand there has been increasing production of fine mesh coal, resulting directly from adoption of […]
How to Dry Coal
Moisture in coal must be considered as an impurity, just the same as ash, from the standpoint of utilization of the coal. Being incombustible, it reduces directly the heating value of the coal, and in addition absorbs heat for its evaporation. Its presence means useless expenditures in handling and transportation. In coke plants, extra moisture […]
Lightweight Aggregates
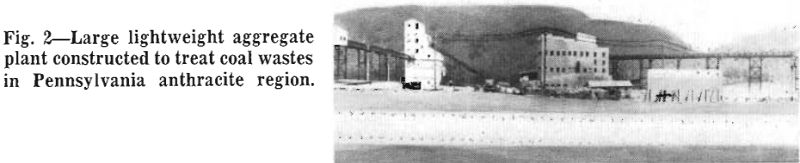
Lightweight aggregates have been in use for many years in the United States but are now receiving more and more attention by manufacturers and users of concrete shapes. These shapes comprise building blocks, special forms, such as door sills, lintels, floor slabs, and beams. Lightweight aggregate also is adapted for monolithic construction. The increased building […]
Small Coal Burning Boiler Plant
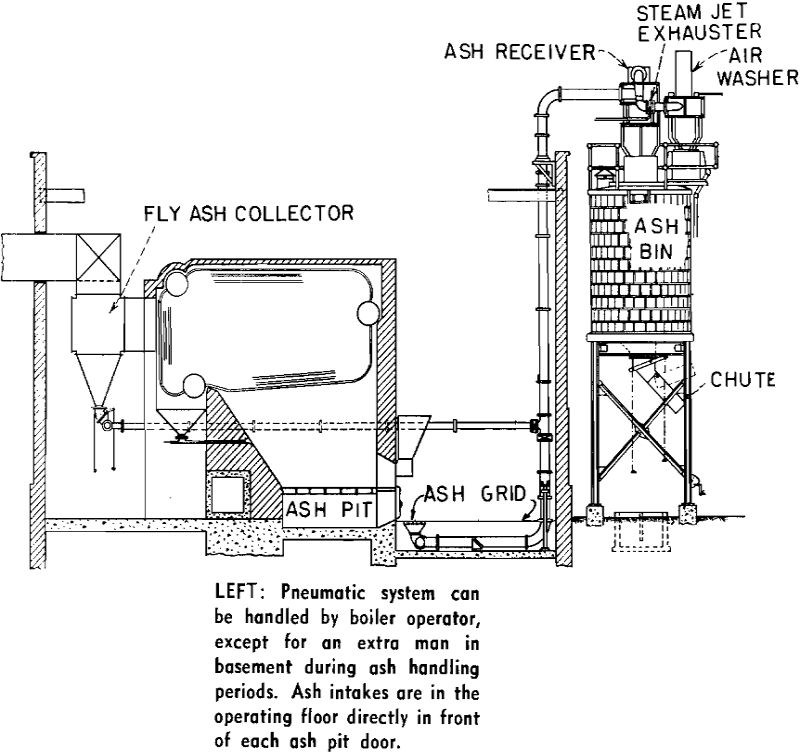
How much can the mine operator afford to spend on his coal burning boiler plant? The usual answer is as little as possible and still get the job done. Thus, attention must be focused on the spot where excessive costs are most likely to arise —the materials handling end of the job. Silo System for […]
How to Produce Graded Glass Sand by Grinding and Classification
The problem of producing a uniform, medium-fine sand for glass-furnace feed has been of interest to the glass-container industry for many years. In the present investigation of the problem, conducted by the Bureau of Mines in cooperation with the Owens-Illinois Glass Co., Alton, Ill., a satisfactory method of producing such sand was developed. The investigation […]
Crushed Limestone Aggregates for Concrete
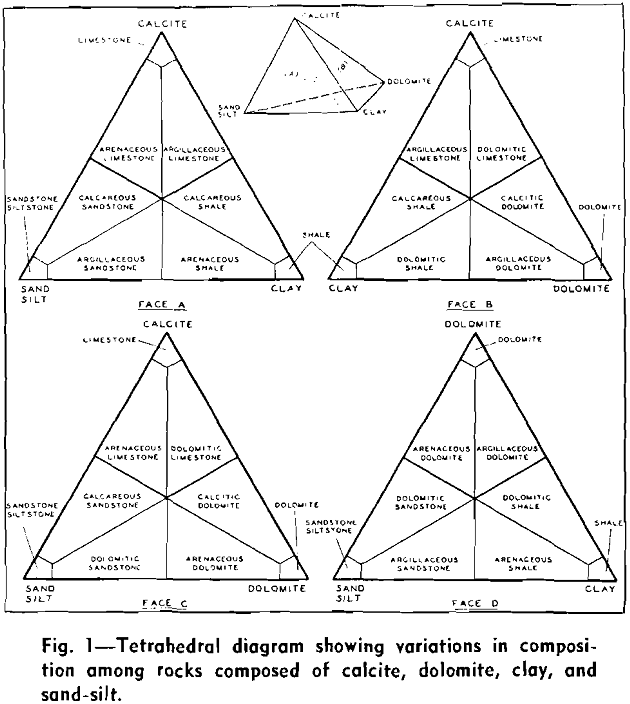
The problems encountered in efforts to explain the behavior of limestones, dolomites, and related rocks as concrete aggregate lie on the frontiers between the ignorance of the geologists and the ignorance of the engineers. The mineral composition and textures of the rocks have not been adequately explored and described, and the effects of mineral composition […]
Dry Process Cement Plants
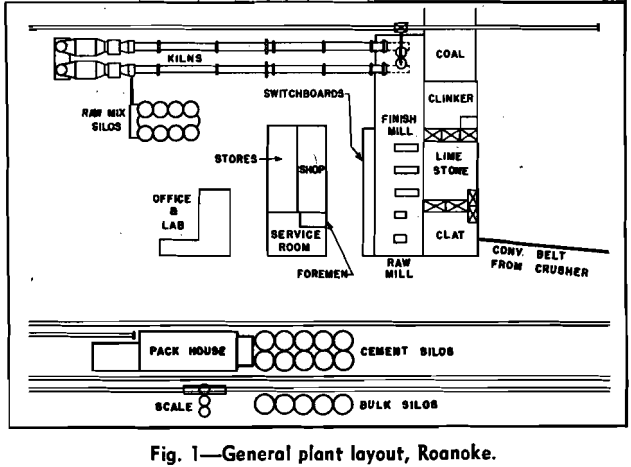
The heavy postwar demand for Portland Cement has created shortages that are gradually being overcome by increases in plant capacity. In the postwar period, the Lone Star Cement Corp. has expanded several of its existing 15 plants and has built 2 new plants, now in operation, with a third new plant under construction in Brazil, […]
Coal Cleaning Equipment
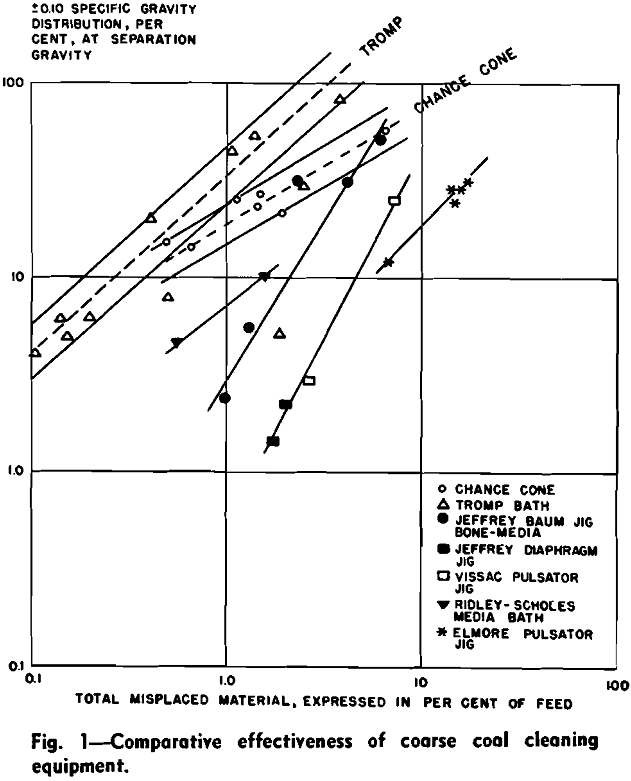
The relative performance of coal washing equipment, or the effectiveness with which any type or make of equipment removes impurities from coal, has been most difficult to evaluate in the past. The most widely used yardstick is the Frazer and Yancey efficiency formula developed in 1922, but Yancey in a later article states that “washers […]