Smelting Taconite in Blast Furnace
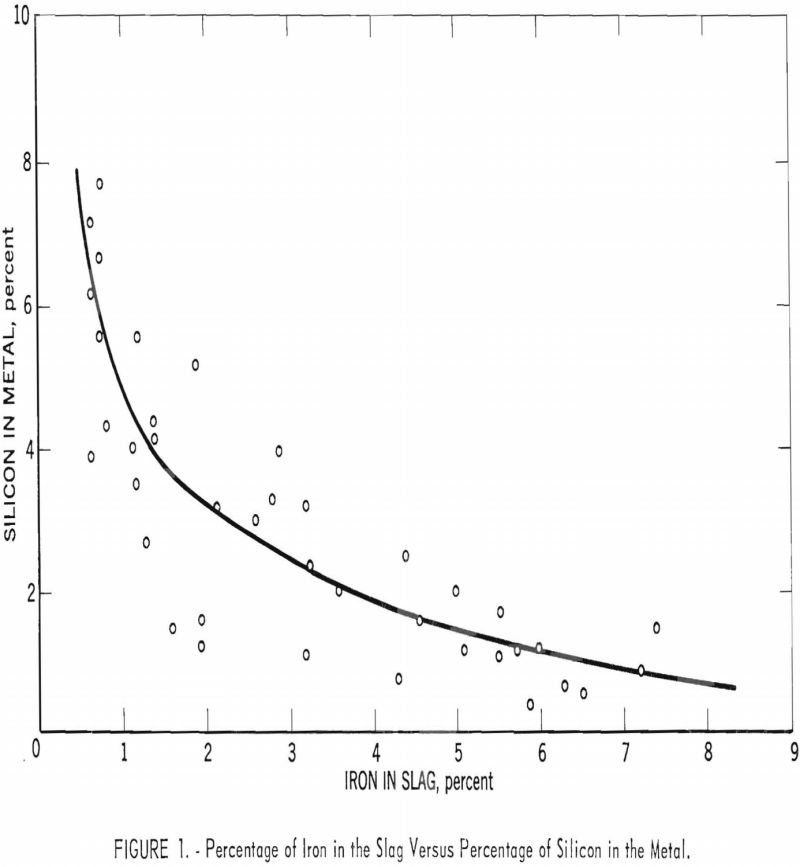
Crude Minnesota taconite was charged in the Bureau of Mines experimental blast furnace so that smelting characteristics of such highly siliceous raw materials could be studied and smelting costs compared with those of a standard Mesabi ore. The Bureau recognized that the highly siliceous nature of the crude ore and its relatively low metallic content […]
How to Recover Thermal Energy from Molten Salts
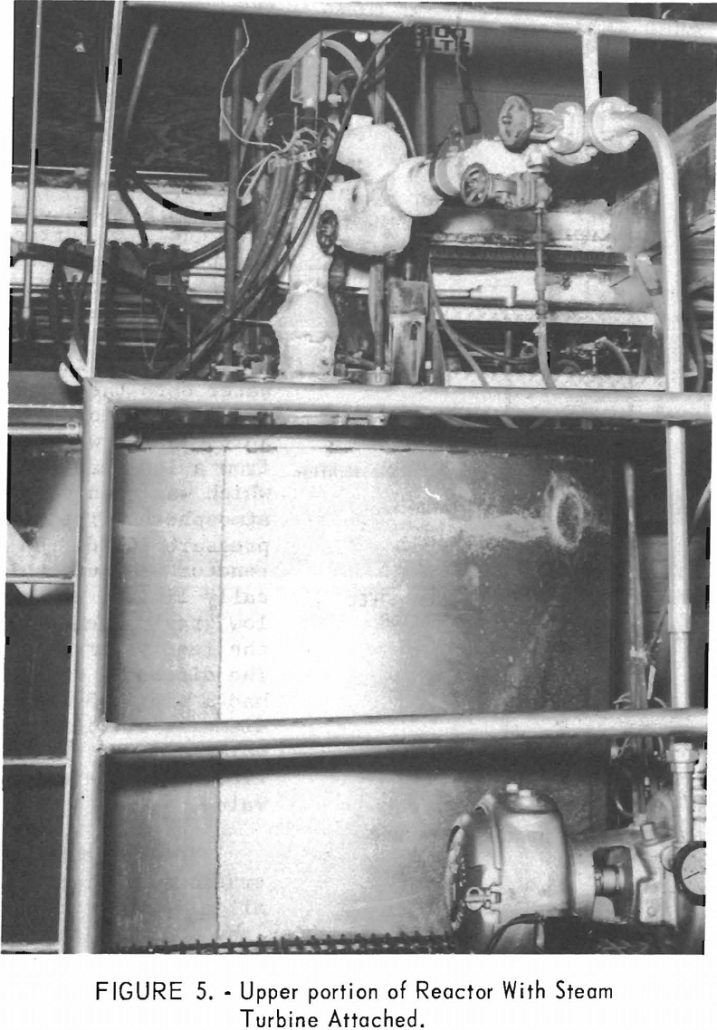
One objective of Project Gnome is to study the feasibility of a phase of the Plowshare program recovering thermal energy from an underground nuclear explosion. The test will be conducted in an underground salt deposit. It is anticipated that some of the energy thus released will be stored as thermal energy in molten salt. This […]
Extract Aluminum from Aluminum Silicon Alloys
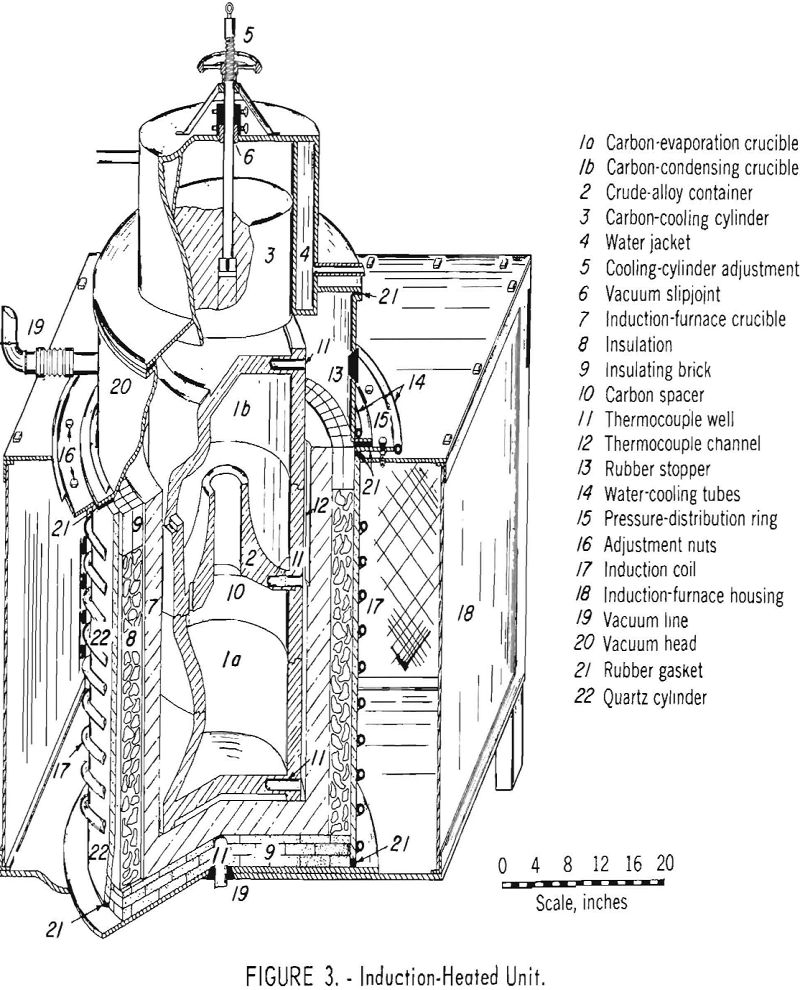
The following conclusions are drawn from the results of these investigations: The reflux leaching method is an effective means for extracting aluminum from crude Al-Si alloy. Aluminum obtained by this method will contain from 1 to 6 percent silicon, 0.04 to 0.8 percent iron, and 0.01 to 0.9 percent titanium. With only minor changes in […]
Casting Titanium Zirconium and Hafnium
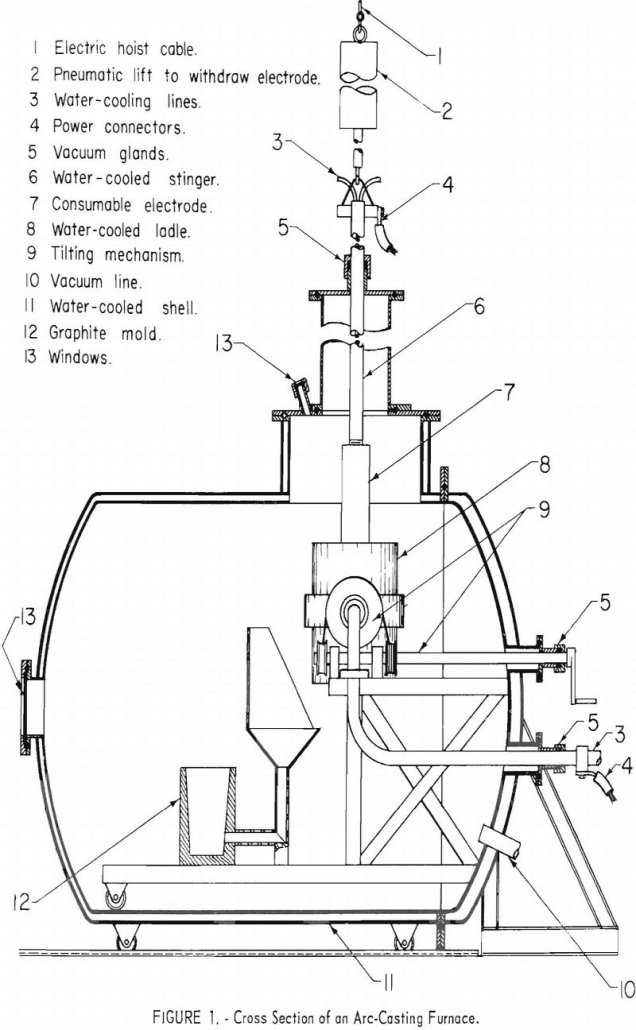
The work covered in this report is a continuation of an earlier feasibility study by the Federal Bureau of Mines and points out improvements in the skull-melting method for casting reactive metals such as titanium, zirconium, and hafnium. Machined graphite molds with laminated sections can be reused many times. Large tube sections can be produced […]
Limonite Siderite Iron Ore Beneficiation
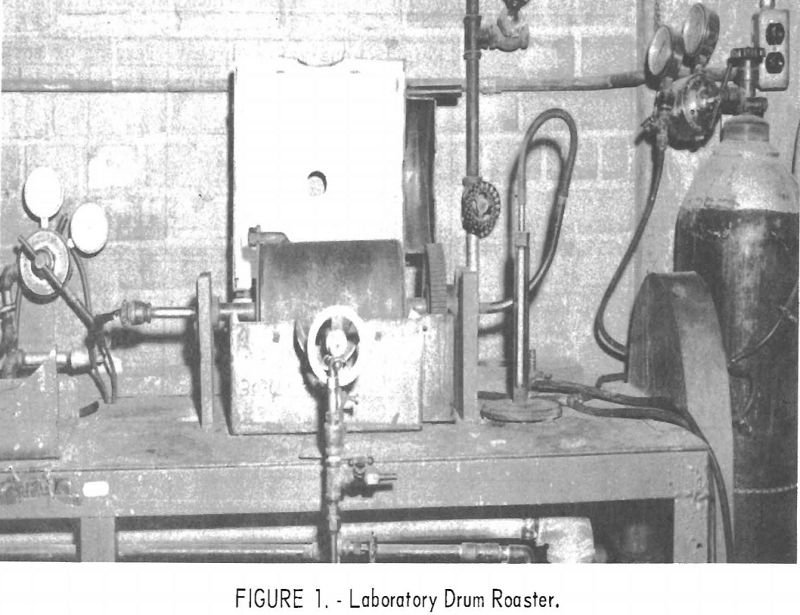
A laboratory mineral-dressing investigation was conducted by the Federal Bureau of Mines on four limonitic and four sideritic iron ores from the North Basin of the east Texas iron-ore district. The samples, composited from drill cores, were considered representative of the iron-ore reserves of the area. The objectives of this research were twofold: (1) To […]
What is the Best Coal for Coke Making
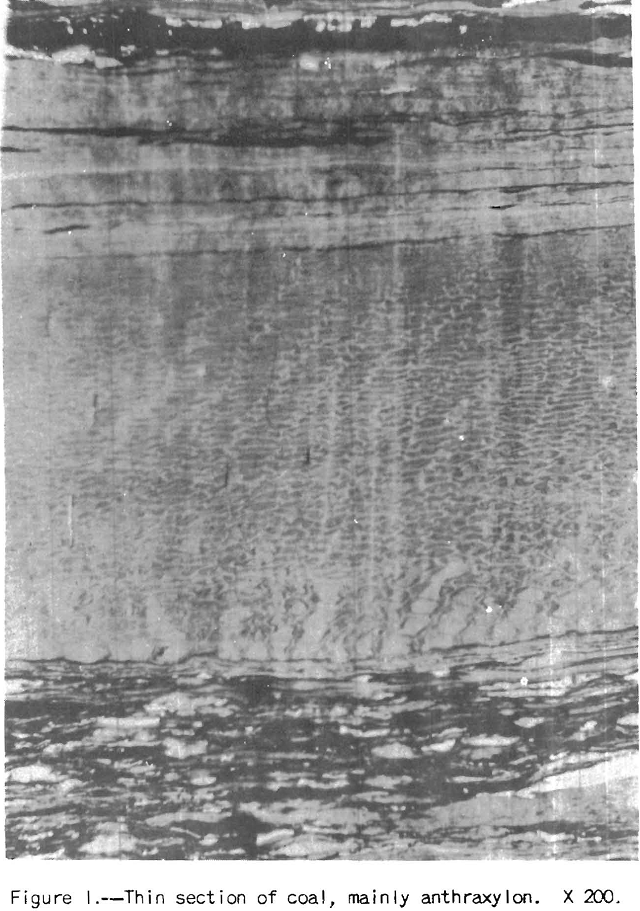
Selection of a suitable coal or coals for the manufacture of coke of desired quality with due consideration of the purpose for which the coke is intended requires careful thought, and often it will pay to go to considerable expense in testing such coals as may be available. In general it will always be possible […]
How to Recover Mercury from Cinnabar Stibnite Ore
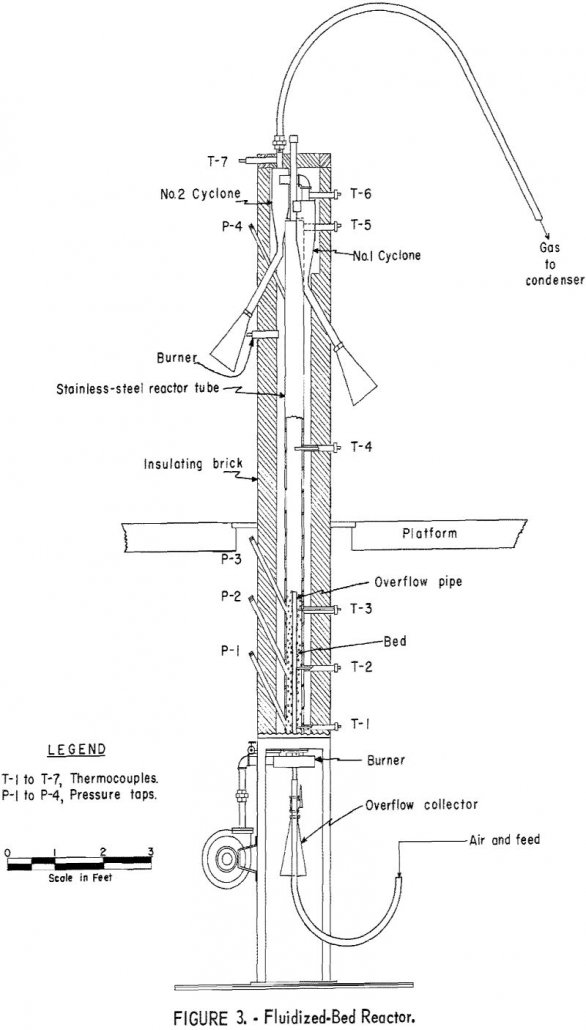
Generalized conclusions cannot be drawn from the laboratory studies about the economic feasibility of extracting mercury by a combined flotation and fluidized-bed roasting process. The 94 percent mercury recovery indicated in the laboratory compares favorably with the 90 to 95 percent recoveries usually reported by mercury-plant operators. Grinding the entire ore to liberation size, plus […]
Columbium Alloys
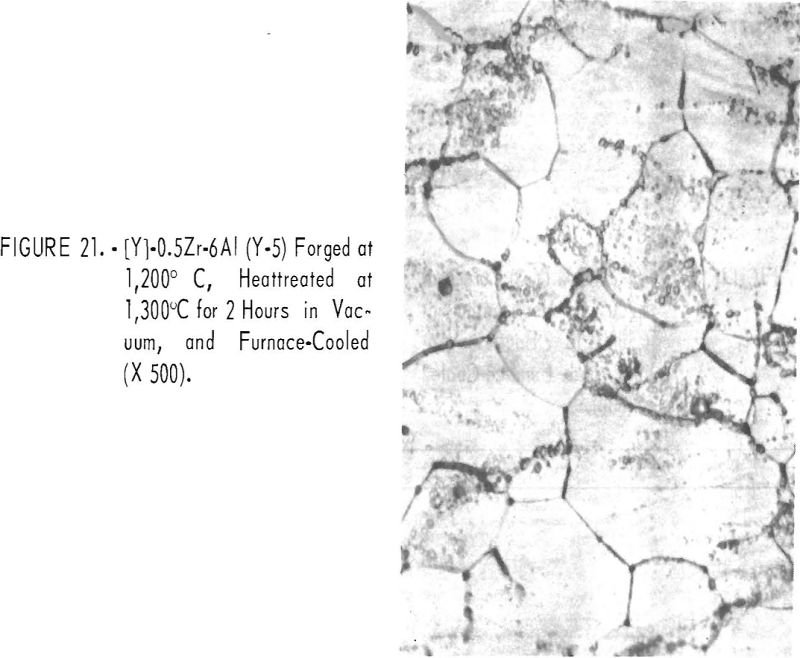
As a continuing endeavor, the Bureau of Mines is developing columbium and tantalum alloys for high-temperature applications. This investigation was undertaken to improve the high-temperature properties displayed by the more common columbium alloys that are commercially available. In a previous investigation beneficial improvements were realized by alloying columbium with elements such as hafnium, tungsten, titanium, […]
Chlorination Of Ferrochromium
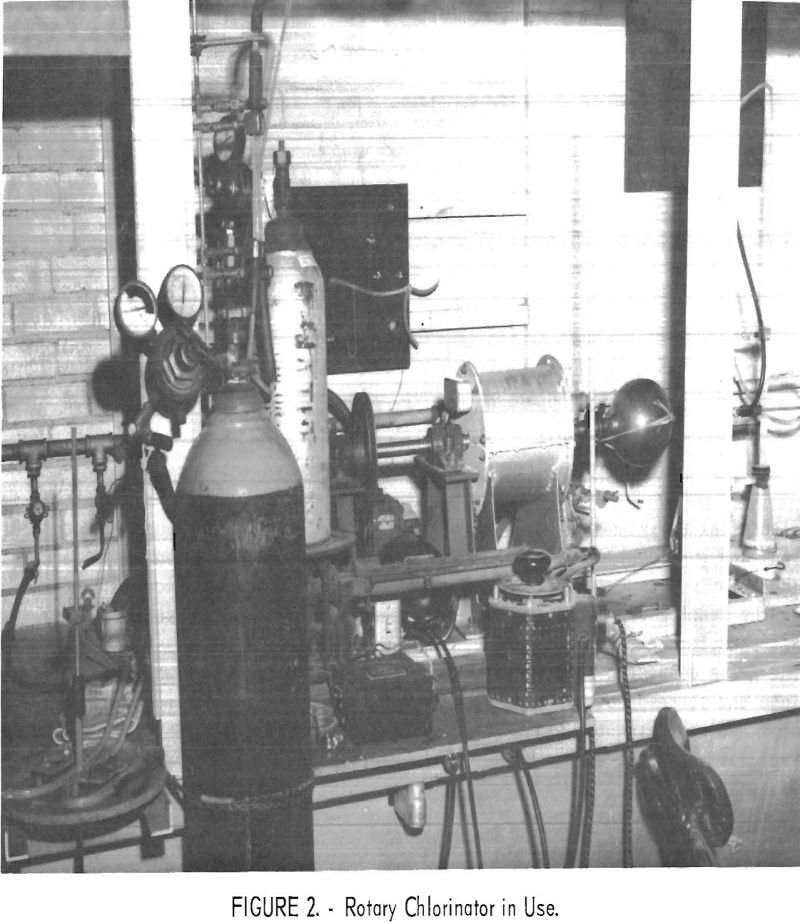
Low-temperature chlorination of three types of ferrochromium at 340° to 525° C chlorinated an average of 89 percent of the chromium and 95 percent of the iron contents of the feed materials. From 81.9 to 91.6 percent of the iron was removed by sublimation as FeCl3. The reactor product was a free flowing material which […]
How to Use Heat to Separate Copper from Steel Scrap
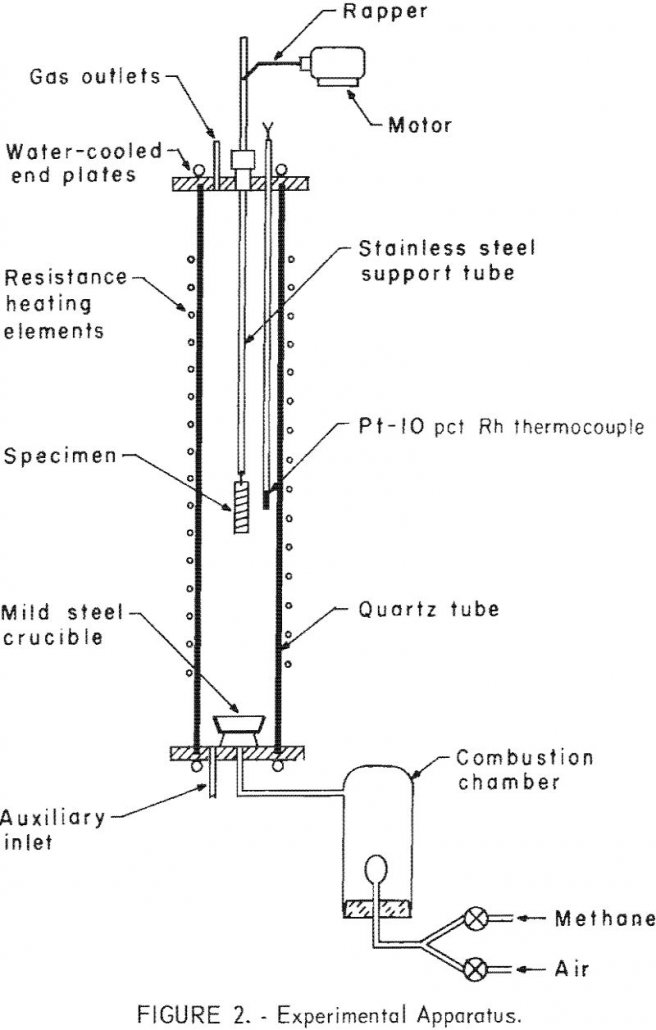
We initiated a program was concerned with the utilization and disposal of steel scrap, as the pollution and unsightliness caused by the accumulation of steel scrap in junkyards. Maybe we could use heat to Separate Copper from Steel Scrap? In the past decade the problem has become increasingly serious; greater amounts of steel scrap are […]