Ball Size Quantity Target Weight (grams)
-2” + 1 ½” 61 28030
-1 ½” + 1” 32 14290
-1” + 7/8” 17 6060
-7/8” + ¾” 13 6045
-3/4” + ½” 8 3575
Machine Instructions for Laboratory Batch Mills
Location
The first thing to consider when selecting a suitable location for your Laboratory Batch Mill is the arrangement with respect to the other machines. Enough clearance should be allowed for installation of the mill.
Starting and Driving New Mill
Ensure all operating guards are in place and properly secured.
Before starting the mill, jog it slightly to see if the direction of rotation is in accordance with that shown on the drawings. If not, reconnect the motor in order to reverse the rotation.
Operation – Loading Mill
Ensure power is off
Release locking clamp on guard and open guard
Release locking pins on mill and turn mill into vertical position
Remove head
Put material to be ground into mill
Reinstall head and tighten locking handle
Return mill to horizontal position and tightening locking pins
Close guard and fasten locking clamp
Start mill and run for desired grind time
Operation – Un-loading Mill
Ensure power is off
Release locking clamp on guard and open guard
Release locking pins on mill and turn mill into vertical position
Remove head
Install wash screen if using grinding media
Turn mill 180 degrees in vertical position and empty contents in to pail
Remove opposite head and wash out with hose if required
Spare Parts
The Laboratory Batch Mill is a rugged piece of equipment built to give continuous service. It’s seldom that it will need any work done on it, but to insure proper maintenance or prevent costly shutdowns it is well to keep the following parts on hand to account for the normal wear.
1 – Set locking pins
1 – Set heads
When ordering spare parts, identify these giving the description, size, and serial number of the mill.
We maintain permanent engineering, purchasing and manufacturing files for each and every machine built. With the information supplied by you and with the help of these files, we are always able to give you the best service when furnishing spare parts for your mill.
LABORATORY BALL MILLS
A Laboratory Ball Mill is used for grinding in laboratory flotation test work, wet grinding is necessary in several stages in order to approximate the actual grinding conditions of a ball mill and classifier in plant operation. With this small ball mill it is possible to grind successfully in several stages without dilution, because the large feed opening and discharge hole (which retains the balls while the mill is being discharged) permits quick and thorough draining with the use of a minimum of wash water. Used in conjunction with a (Closed) Ball Mill, and a laboratory batch classifier saves time.

BATCH LABORATORY BALL MILL
The (Open) Batch Mill makes possible simulation of grinding in a ball mill-classifier circuit by grinding a fixed time, then hand classifying with a sieve and a bucket and returning the sand to the mill for further grinding. Pulp volume can be kept at a minimum by control of wash water since the ball load does not dump out. Thus fine or coarse grinding is accomplished with ease of manipulation. The mill is used considerably as a regrind unit for further size reduction of flotation concentrates, table concentrates, middlings, and other mill products.
Air may be introduced to the pulp, if desired, through the open end of the cast steel drum.
The (Open) Laboratory Ball Mill can be used for the amalgamation of table and flotation concentrates, by using one 4″ ball during the grinding action. A few slight changes provide for mounting an Abbe Jar on the driving shaft opposite the drum. This affords an excellent combination laboratory grinding unit.

BATCH OR CONTINUOUS LABORATORY BALL MILL
Laboratory Ball-Rod Mill is for grinding large quantities of ore in batch or continuous work. A grate discharge allows quick emptying for batch work; and a trunnion discharge, for continuous work. This flexible unit can also be used as an amalgamator.
The welded steel base can be provided in lengths suitable for supporting one, two, or three drums. One drum constitutes a ball mill; two, a rod mill; and three, a tube mill. The construction permits easy and rapid addition or removal of drums for conversion from one type to another, the trunnion being moved along the channels to accommodate the various lengths. The grinding drums are made with thick walls, thus eliminating the necessity of liners and the possibility of salting samples.
This grinding mill has many commercial applications, since special acid resisting drums and heads can be furnished. Hard iron or alloy steel replaceable liners are easily inserted where wear is an item as in continuous use.
For continuous pilot test plants utilizing No. 7 or No. 8 “Sub-A” Flotation Machines, ball mills with larger grinding capacities are required. The 30″ Convertible Ball Mill is ideal for this application. Capacity of this mill with single section is 3 to 5 tons per 24 hours while the double section mill, illustrated above, has a capacity of 6 to 9 tons per 24 hours.
BUCKBOARD AND MULLER LABORATORY BALL MILL
The Buckboard and Muller ball mills are an extremely useful addition to most ore dressing or industrial laboratories. It accomplishes the quick reduction of small quantities of ore or other crushable materials to a fine powder. The unit consists of a chilled iron buckboard grinding surface, two sides of which are rimmed, and the desired type and weight of muller. The buckboard grinding surface is planed smooth and standard mullers have rounded crushing faces. Mullers may be purchased separately from either standard types shown or special from the three sizes of each type listed in the table and classified by rounded or flattened crushing faces. Rounded face mullers as listed have hickory axe type handles and flattened face mullers are equipped with hickory pick type handles.

BRAUN-WELSCH LABORATORY BALL MILL
MILL, Ball, Braun-Welsch—A laboratory ball mill particularly suitable for the metallurgical laboratory for flotation, cyanidation or amalgamation tests, but useful for any type of fine grinding. Will grind either wet or dry.
The ball mill body, or shell, is of gray cast iron, 12 inches inside diameter, 7 inches between the two machined driving ribs. Openings in the centers of heads allow free access of air during the grind, duplicating commercial scale plant conditions. The driving power is peripheral, applied frictionally through the supporting rollers. For loading, discharging and cleaning, the mill body is raised from the rollers by a rack and pinion device. This allows it to be turned, bringing its axis into the vertical position shown above. Removing the upper head by loosening five lug screws makes the inside completely visible and accessible. Pulp can be discharged through the lower opening, the balls being retained by a spider. Discharging and cleaning are rapid and thorough. All possibility of salting is eliminated, provided advantage is taken of the facilities for thorough cleaning.
The capacity is from 10 grams up to 12 pounds. Preliminary crushing to minus 10 mesh is recommended. The time for reducing an average sample to minus 65 mesh is about 15 minutes. Iron balls are used. The usual ball charge is 22 pounds, assorted sizes, 1¼, 1½ and 2 inch being used. Steel rods 1½ inch diameter may be used with good results. The mill operates at 50 R. P. M. and is driven by a 1/6 H. P. 110 volt, belt-connected motor. Mounted on steel table; floor space required, 30 x 30 inches. Height over all, 51 inches. Net weight, including balls, 270 pounds. Gross shipping weight, approximately 350 pounds.
Complete with 35 pounds of iron balls, assorted sizes; steel table; 1/6 H. P. motor for 110 volts, A. C.; drive pulley and belt. Steel Balls, Extra
A Ball Mill of Laboratory size, for grinding wet or dry material. Specially recommended for experimental flotation work where the oil or reagent is mixed with the samples, and gives results in harmony with those obtained in regular practice. Can be used for any type of fine grinding.
The maximum capacity is 25 pounds of ore. An assortment of iron balls ¾ inches, 1 inch and 1¼ inch sizes are included. The sample should be ground 20 mesh or finer (preferably with a Braun type U A Pulverizer) before being placed in the ball mill.
Designed for laboratory needs with ready access for charging and discharging the sample. The oval opening measures approximately 10 x 4 inches, and is large enough for all practical purposes. The receiving pan is in two parts, the upper portion being fitted with a screen to catch the iron balls while the ground materials fall through into the lower pan.
Ball Mill Dimensions: Cylinder, 12 x 12 inches ; floor space 27 x 13 x 22 inches ; pulley, 12 x 2¼ inches. Speed recommended, 40-50 RPM. Shipping weight, 300 pounds. Iron Balls, Extra—For use with above. Receiving Pan, Extra. Source
ABBE PEBBLE LABORATORY MILL
The Abbe Pebble Mill is particularly adapted to pulverizing or mixing either dry or wet materials.
This unit is of the batch or intermittent type. The cylinder is approximately half filled with flint pebbles, porcelain balls, or metal balls; the material is put into the cylinder; a tight cover is fastened securely, to seal the mill hermetically; and the cylinder is then revolved until the fineness required is obtained. After that the tight cover is replaced by a grate discharge cover and the cylinder is revolved until the material is discharged, the grate retaining the pebbles or balls. For dry grinding it is customary to enclose the cylinder to prevent the spread of undesirable dust and also to preserve all of sample to insure accuracy of testing procedures.
In wet grinding, the same directions are followed except there is no casing required; and instead of replacing the tight cover with a grate cover, a special wet discharge cover, or the Abbe patented discharge valve, is used for emptying the mill.
In requesting recommendations for jar or pebble mills, please state:
- Material to be reduced.
- Size at which it will be fed to the mill.
- To what mesh it is desired to grind to produce the finished product.
- Capacity (lbs. or gals.) desired per hour.
- Whether material is to be ground wet or dry.

LABORATORY JAR MILL
The Abbe Laboratory Jar Mill pulverizes materials by friction and the fall of pebbles or balls contained within a rotating jar. In operation the jar is filled almost to the center plane with pebbles, and enough crushed material is added to fill the interstices between the pebbles and bring the charge to about 3/5 of the capacity of the jar. Usually a coarse screen is used to separate the pebbles from the material after grinding.

This unit is particularly adapted to pulverizing and mixing dry or wet materials and is manufactured in many sizes and styles for various capacities and conditions. Number of jars handled varies with mill size.

Jars are manufactured in many sizes and are of the best material. The three kinds available are: (1) Porcelain Jars— carefully molded and fired to obtain the proper degree of vitrification so as to give acid and wear resisting qualities for grinding and agitation. (2) Metal Jars—made of the metal most resistant to the action of a grinding charge, such as Monel, stainless steel, cast steel, and bronze. (3) Pyrex Jars—are transparent and enable observation during grinding or agitating action.

PORCELAIN LABORATORY JAR MILL
The Jar type Laboratory Ball Mill is ideal for use in pulverizing, mixing of dry and wet materials, and agitation of all types of pulps. Two large bottles or as many as six small bottles can be used at the same time, thus providing a very flexible type of jar mill. When used for agitation, large ammonia bottles filled with pulp can be agitated continuously for any length of time.
The unit is compact and sturdy and the speed reducer with chain drive mechanism is positive, as shown in the illustration. The entire unit is on a steel base. Idler roll is adjustable to bottle size.
Low initial cost and reliable continuous or intermittent operation make this machine a desirable unit for laboratories of any size.
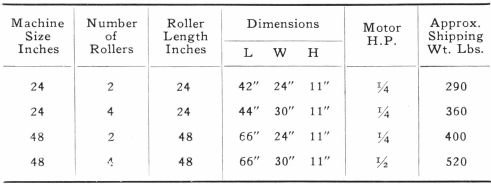
LABORATORY PEBBLE MILL
The Laboratory Pebble Mill is a simple, efficient laboratory batch grinding unit. This machine is also an effective laboratory bottle type agitator for use on all types of pulps especially cyanide pulp. Two large bottles or jars or as many as six small jars may be used at the same time. This provides a wide range of capacity for batch laboratory grinding, and, at the same time, affords a very flexible unit for batch agitation. The speed reducer and chain drive mechanism is positive and the entire unit is mounted on a steel base. Idler roller is adjustable to various bottle sizes. Data on jar sizes and types given under Laboratory Agitator, (Bottle Type).

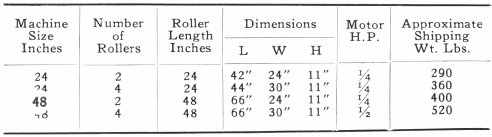
PORCELAIN LABORATORY BALL MILLS
Pulverizing is effected in these ball mills by the friction and fall of balls or pebbles contained within a rotating porcelain or glass jar. In general practice, the jar is filled to a little below the centre plane with pebbles; well crushed material then being added to fill the interstices and bring the charge to about three-fifths of the total space in the jar. After the operation, the pebbles and ground material are usually separated by means of a coarse grid.
Either hard or soft material may be ground, but it should not be moist to the extent that it will pack in the cylinder. If sufficient liquid is present, this method is superior to others for fine pulverization. Equipment is supplied complete with porcelain jar and flint pebbles.
MILL, Bail, Porcelain—Grinding capacity, taking sand as a unit, 1½ pounds. For belt-drive.
SPECIFICATIONS
- Fluid capacity of jar: 1 quart.
- Horse-power required: 1/12.
- Single tight pulley: dimensions, 9 x 1 inches.
- Floor space required: 9 x 11 inches.
- Proper speed of rotation: 80-120 RPM
- Shipping weight: 50 pounds.
Complete, with porcelain jar and 2 pounds of pebbles.
MILL, Ball, Porcelain—Grinding capacity, taking sand as a unit, 5 pounds. With tight and loose pulleys.
SPECIFICATIONS
- Fluid capacity of jar: 1 gallon.
- Horse-power required: 1/12.
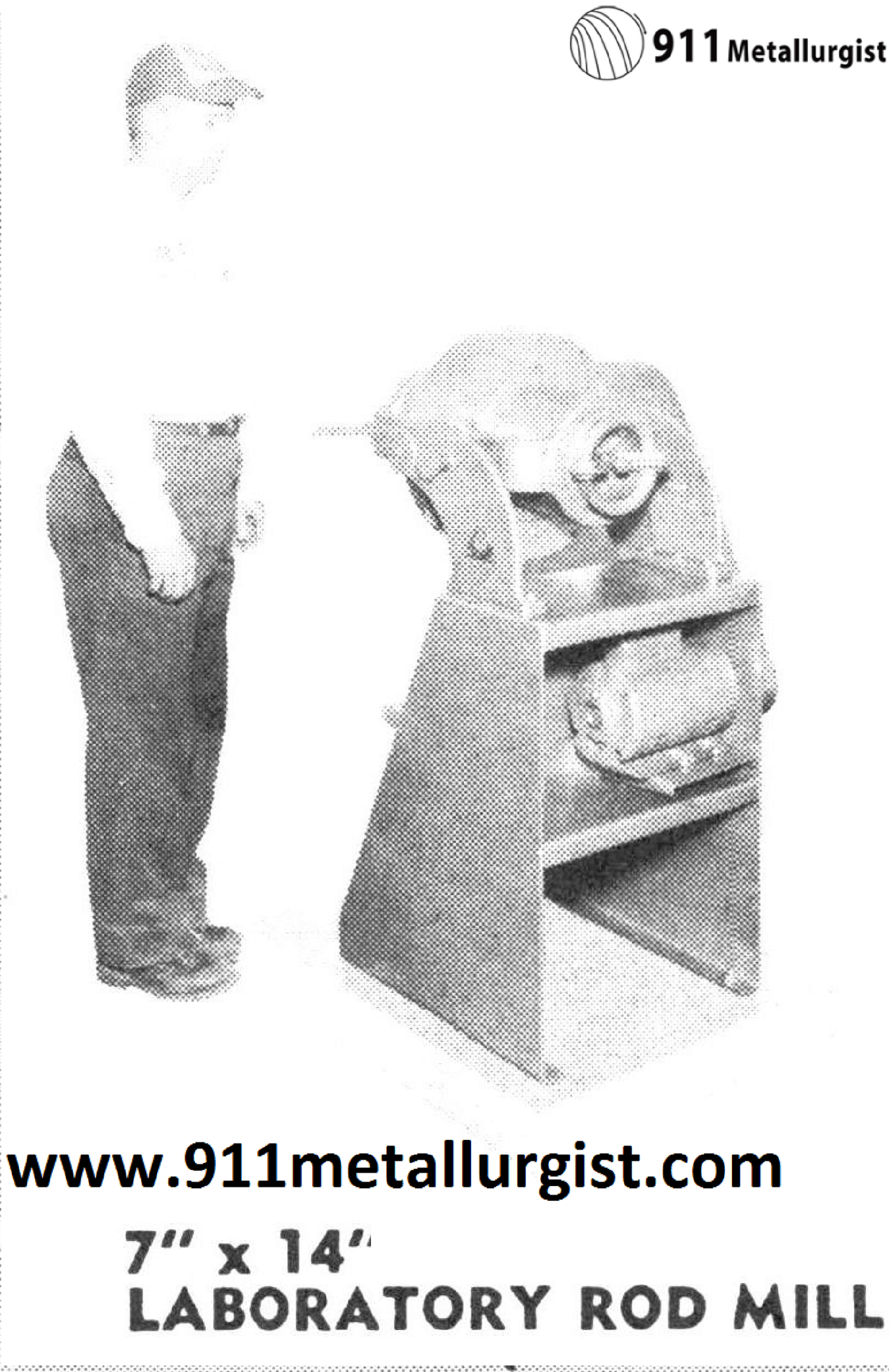
- Tight and loose pulleys: dimensions of each, 9 x 1 inches.
- Floor space required: 14 x 25 inches.
- Proper speed of rotation: 55-75 RPM
- Shipping weight: 135 pounds.
Complete with porcelain jar and 8 pounds of pebbles.
- MILL, Ball, Porcelain—Same as No. 39520, but with single tight pulley and handle. Shipping weight, 125 pounds.
- Complete, with porcelain jar and 8 pounds of pebbles.
- MILL, Ball, Porcelain—Grinding capacity, taking sand as a unit, 15 pounds. With tight and loose pulleys.
SPECIFICATIONS
- Fluid capacity of jar: 4 gallons.
- Horse-power required: 1/6.
- Tight and loose pulleys: dimensions of each. 15×2 inches.
- Floor space required: 22×30 inches.
- Proper speed of rotation: 40×50 r. p. m.
- Shipping weight: 250 pounds.
Complete, with porcelain jar and 25 pounds of pebbles.
LABORATORY GRINDING TESTS AND LABORATORY BALL MILLS
A complete laboratory service that includes preliminary examination, batch or pilot-grinding test, open or closed circuit grinding, both wet and/or dry—provides important data for determining accurate mill size, for determining circulating loads, sizing accessories, grindability indexes and power requirements. Preliminary tests are made at no cost to you. Send 100 lb. sample of material prepaid.

Source: This article is a reproduction of an excerpt of “In the Public Domain” documents held in 911Metallurgy Corp’s private library.