- To participate in the 911Metallurgist Forums, be sure to JOIN & LOGIN
- Use Add New Topic to ask a New Question/Discussion about Grinding.
- OR Select a Topic that Interests you.
- Use Add Reply = to Reply/Participate in a Topic/Discussion (most frequent).
Using Add Reply allows you to Attach Images or PDF files and provide a more complete input. - Use Add Comment = to comment on someone else’s Reply in an already active Topic/Discussion.
Scales on poly wedge vibrating trash screen (8 replies and 1 comment)
Helen,
Rather than speculating regarding the nature of the scale why don't you just submit a sample for XRF. It could CaCO3, or an aluminate or...
I agree. Additionally I said XRF but was really thinking XRD.
If it is being removed by sulphamic acid in all probability it is CaCO3 scale which is very common in this area in gold plants. Lime added for pH control often contributes to the scale formation but usually the hardness of the water is a major contributing factor. If it is water hardness there is a likelihood that scale is also forming in the water reticulation system around the plant as well. Anti-scalent additions can reduce or control these build-ups. The suppliers of these reagents will often identify scales and potential for water to form scale. Scale formation on the screen is difficult to control because of the agitation and exposure to air that occurs during the screening process. Whilst acid washing will remove some of the scale often a mechanical means such as high pressure water blasting is also used to physically remove the scale providing a quick way of cleaning the screen. Eventually though the screens need to be replaced. With acid washing particularly in-situ there is a risk of HCN gas formation during this.
This is not an isolated case but your problems run significantly deeper than CaCo3, build up , with the presence of a fine salt clogging the wire
Lets look at what your screening and why at what stage of the process , the screening is taking place. What is the feed rate onto the screen and how is the material being fed .
Why did Multotec advise you to use wedge wire panels ?
You will spend time and money doing sampling and your issue will plague you forever, the Caco3 is not presumably affecting the process but rather its build up has manifested itself but a significant decrease in screening open area
How much water is being fed with the material and where is that water coming from ?
Email me a couple of pictures ; your location of plant and i will send you a questionnaire to complete, this will allow me to look at all the related facts ,
When and why did you change to a poly coated wedge wire ? Did you ever have piano wire cross tensioned or self cleaning screen media ?
What make is the screen?
Stewart has asked all the right questions! changing the screen media to a flexi type rubber may retain the open area. This has been my experience drain and rinse applications in coal wash plants. The soft rubber moves and this prevents the buildup on the screens. Not sure about the application but would help in any way i could.
At our "concrete recycling facility" we had expensive time consuming build-up on our fines screens between the jaw and cone. We replaced wire mesh screens with spring steel parallel wire screens (brand unknown but I can find out). The spring steel screens at 3X the cost have been priceless for productivity, had 0 failures since installation and come highly recommended for this issue. In my opinion they should be a #1 solution for well water or hard water issues. Build up on structural members has not yet become an issue in our application.
Hope this helps, Alias
I did a bit of poking around and I wonder if you are using that sort of screen layout, cause if you are - there is absolutely no surprise that you are having issues, that will not work - its way to rigid , you are getting oversize passing through the gaps that are pried open by scaling.
when you send me an email , I will put you in direct contact with a possible solution, that I know, from my own experience has worked in making a difference to screening trash
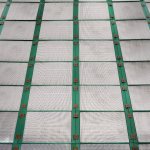
Hello, I work in a gold processing plant where we have a vibrating trash screen in our milling circuit made from a polywedge material. We have a considerable amount of thin scales forming on the screens which are removed every shut down with Sulphamic acid. Recently, the scale formation has increased drastically with increase in width as well. can anyone help me with some reasons why these scales are forming? is there a particular chemical that can cause scale formation on the trash screen?