Recover Hydrofluoric Acid from Fluosilicic Acid Waste
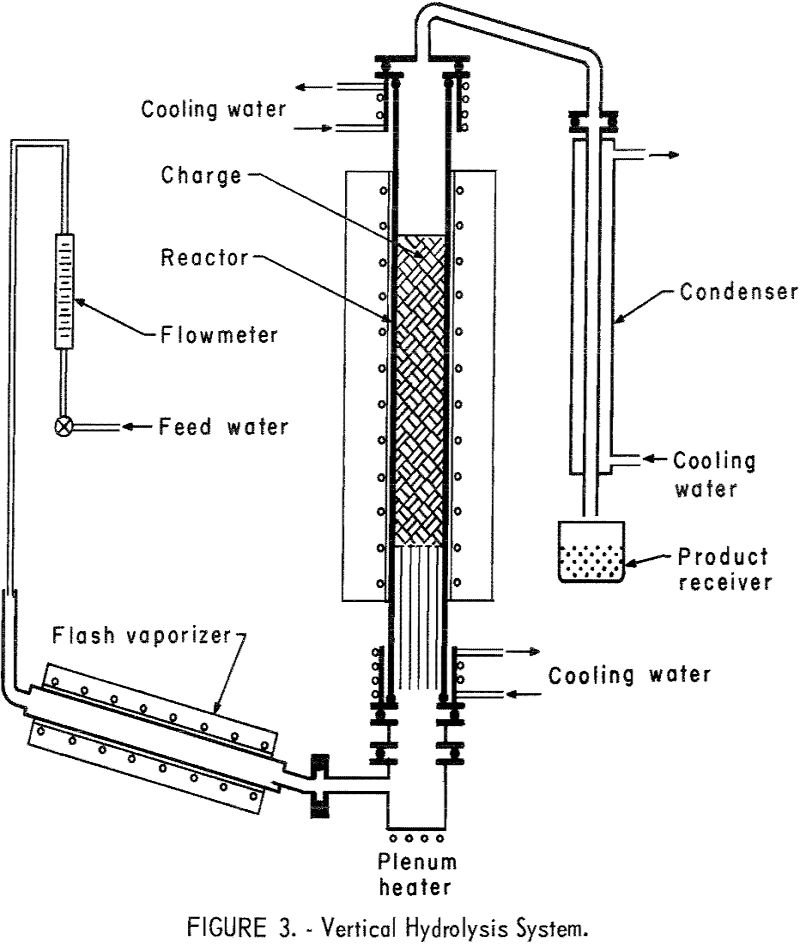
This report describes a preliminary investigation of methods for recovering hydrofluoric acid (HF) from waste byproduct fluosilicic acid (H2SiF6). Fluosilicic acid is generated by plants processing phosphate rock in the manufacture of fertilizer; most phosphate rock contains 3 to 5 percent fluorine in the form of the mineral fluorapatite (Ca3(PO4)3F). When this fluorine-bearing material is […]
Magnetic Separation of Pyrite
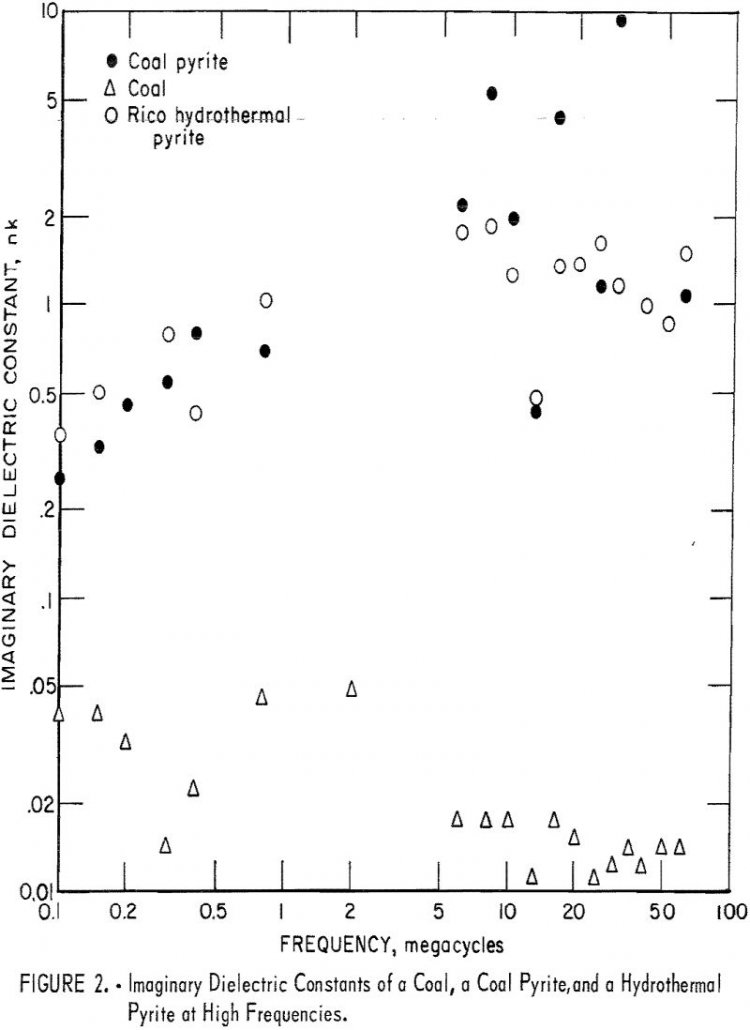
Exploratory measurements of the dielectric constant of coal and pyrite indicate that pyrite in coals can be heated selectively. If about 1 percent of the radiation is absorbed in the process, it would be very attractive from a commercial standpoint. The following recommendations are offered. More precise and systematic measurements of the dielectric properties of […]
Columbium Tantalum Flotation
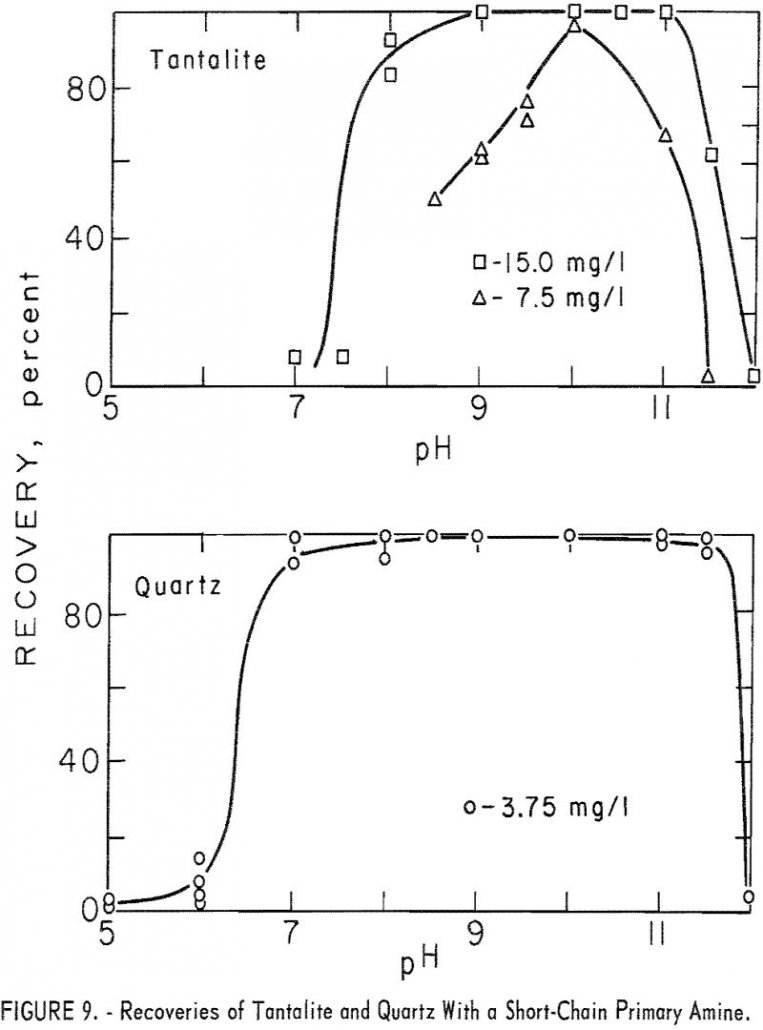
The purpose of this investigation was to determine the flotation characteristics of important columbium / tantalum ore minerals as a guide for the practical concentration of low-grade columbium ores. Placer deposits amenable to gravity concentration have been the major source of columbium; however, these deposits are limited. Therefore, the future of columbium is dependent upon […]
How to Purify & Concentrate a Manganese Leach Solution
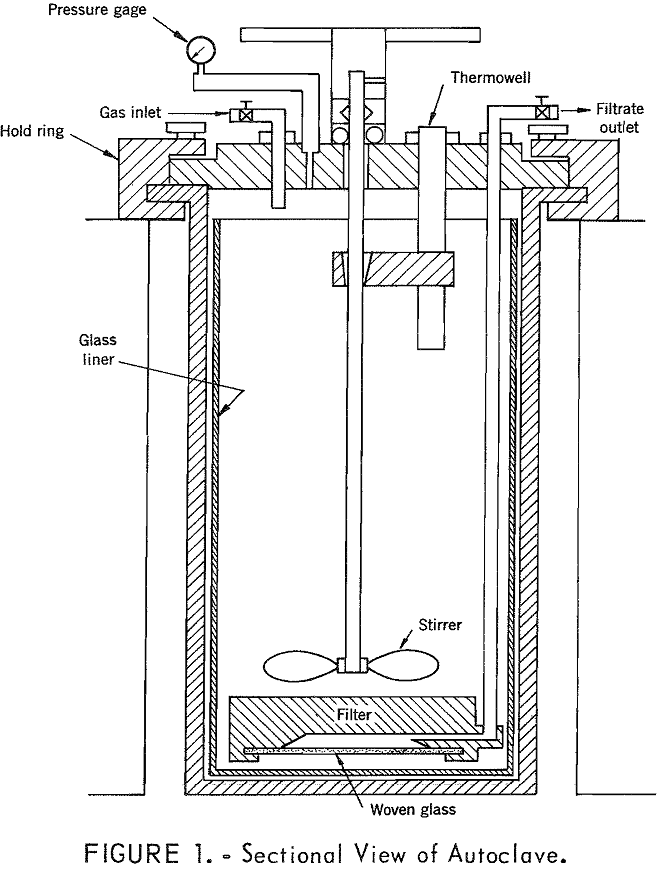
A temperature of 250° to 260° C was found to be satisfactory for simultaneous removal of iron and manganese from the pregnant leach liquor resulting from leaching of low-grade manganese ore. A holding time of about 15 minutes at this temperature was sufficient for maximum iron removal under oxidizing conditions. Using optimum conditions with oxygen […]
How to Identify the Surface Texture of Rock
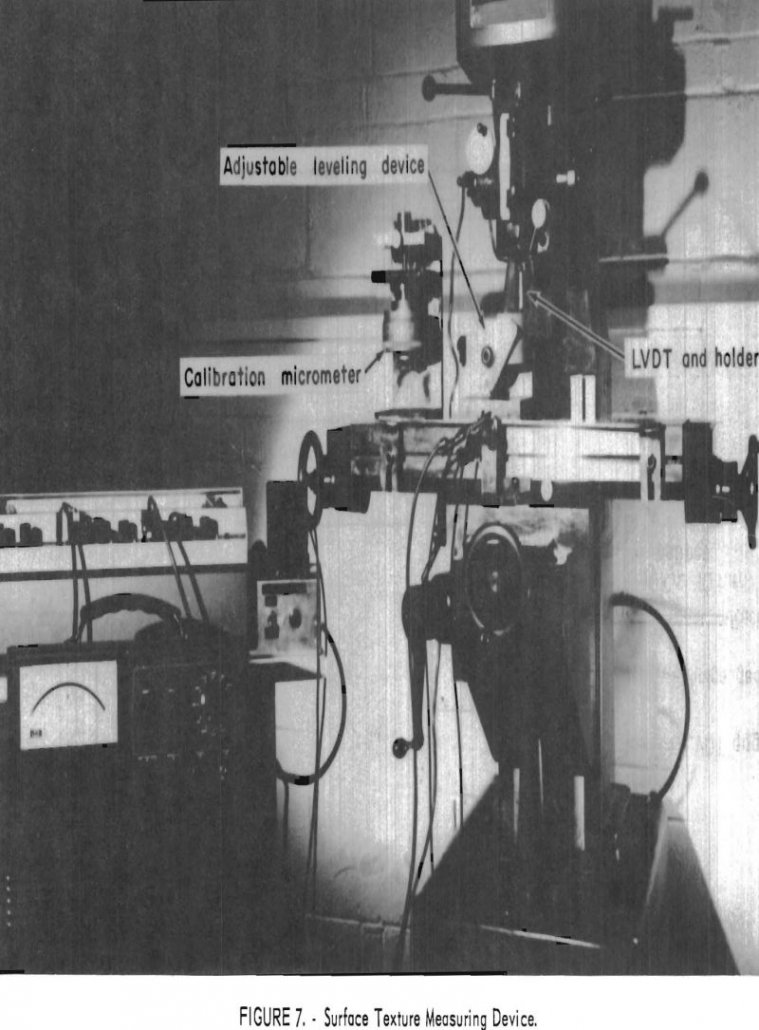
Model studies, using rock, require carefully prepared specimens. Most preparation procedures use some form of grinding or polishing as the last of several steps. During these steps, particularly the final one, the surface formed acquires a configuration defined as texture. Texture is a composite term identifying the physical features called flaws, lay, waviness, and roughness. […]
Chlorination Of Ferrochromium
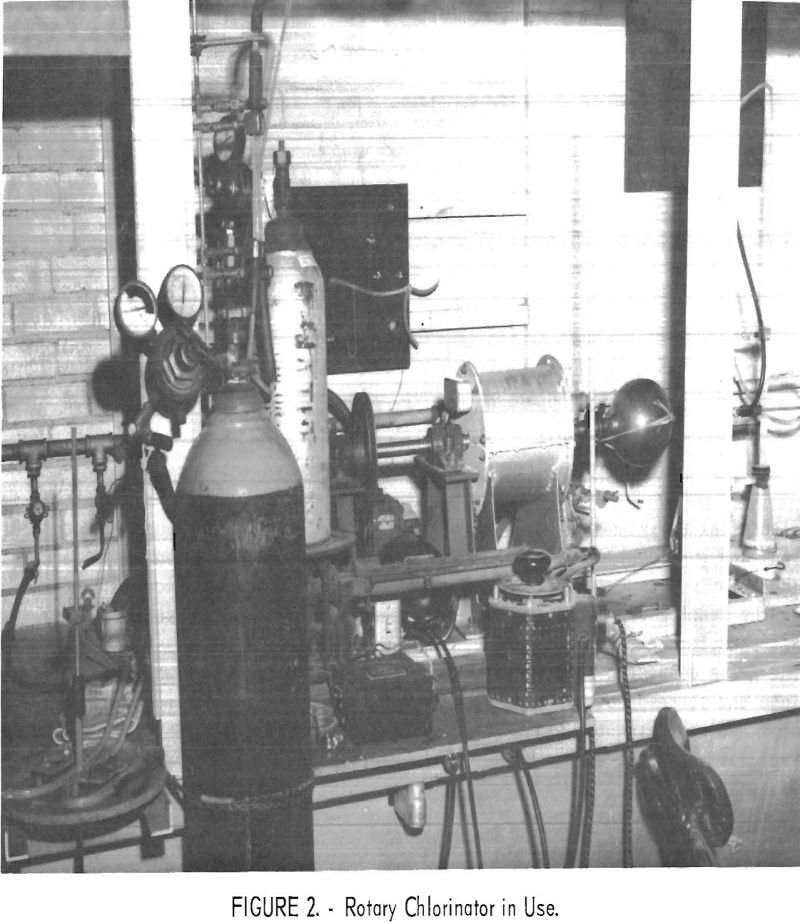
Low-temperature chlorination of three types of ferrochromium at 340° to 525° C chlorinated an average of 89 percent of the chromium and 95 percent of the iron contents of the feed materials. From 81.9 to 91.6 percent of the iron was removed by sublimation as FeCl3. The reactor product was a free flowing material which […]
Zinc Copper Titanium Alloys Cast
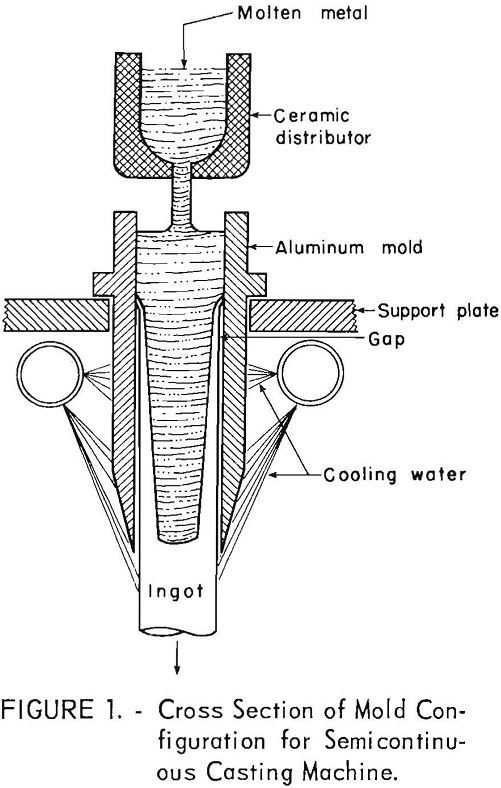
Sound ingots of Zn-Cu-Ti alloys can be semi-continuously cast under appropriate conditions. A modified mold design on a specially constructed, semi-continuous casting stand has permitted casting of ingots having adequate surface quality. With the experimental equipment described, pouring temperatures near 860° F (460° C) produced ingots with better surface quality than when a pouring temperature […]
Ammonium Nitrate ANFO Electric Detonation
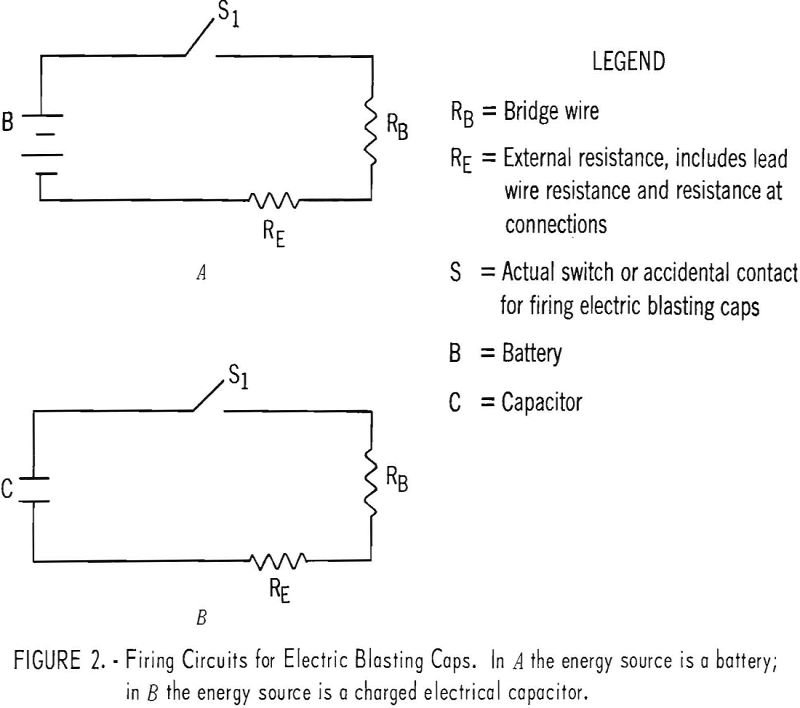
Accidental firings of explosive initiators have occurred occasionally with some uncertain correlation to the pneumatic loading of ammonium nitrate-fuel oil (AN-FO) blasting agents. The exact association, if any, between these firings and static electricity is unknown. This report describes the role of pneumatic loaders in generation or transfer of static electricity and discusses the possible […]
Determining Compressive Strength of Rock
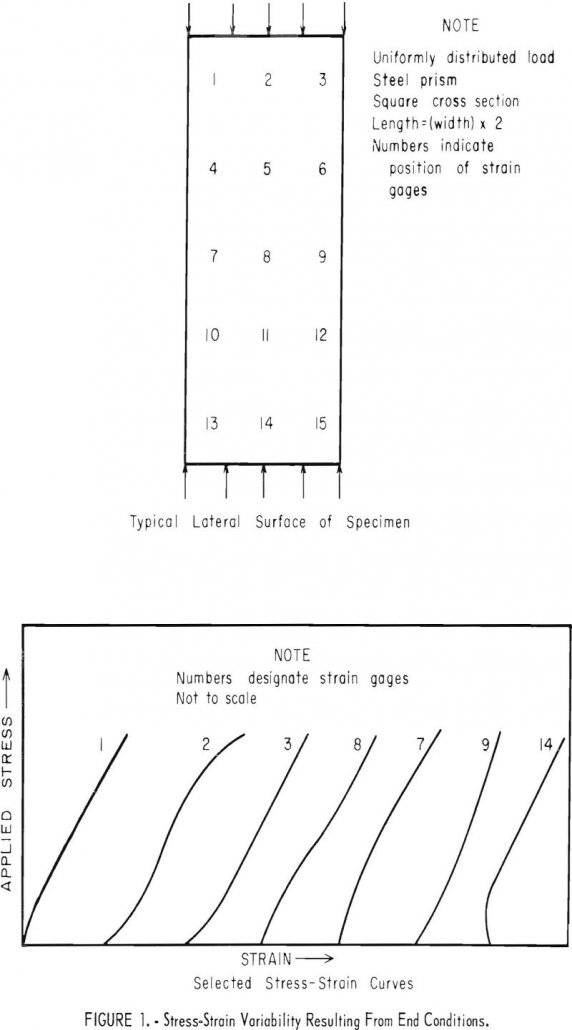
The major conclusion to be drawn from the four series of tests is that reasonable care in preparing specimens and conducting compression tests on a hydraulic machine will provide an acceptable compressive strength value for most applications. For normal uniaxial compression tests, nonparallel ends, end surface texture, steel false end platens, and spherical head friction […]
How to Use Heat to Separate Copper from Steel Scrap
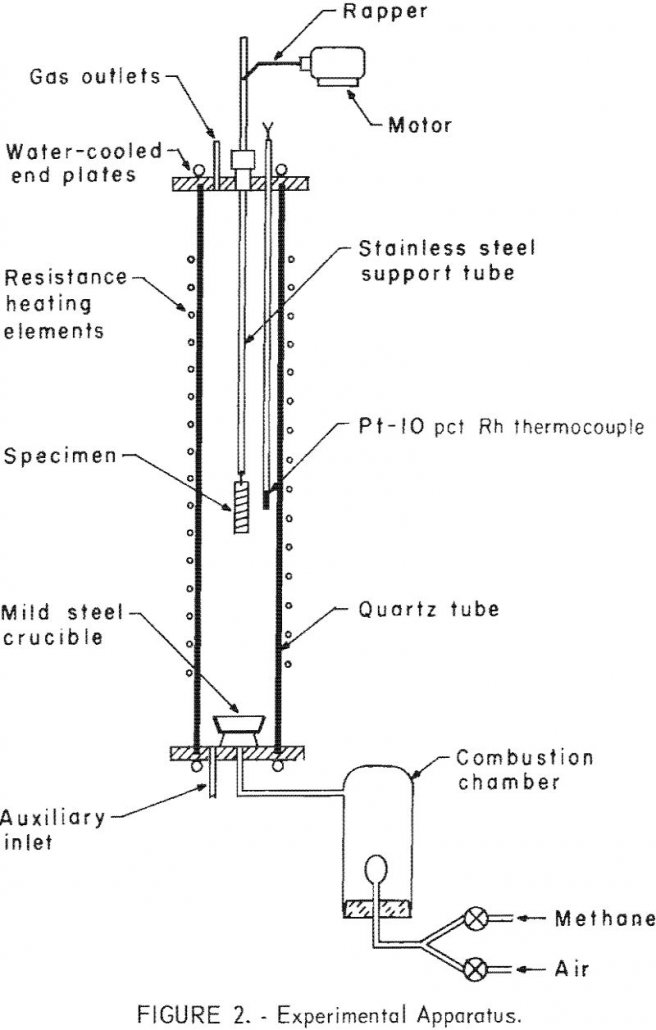
We initiated a program was concerned with the utilization and disposal of steel scrap, as the pollution and unsightliness caused by the accumulation of steel scrap in junkyards. Maybe we could use heat to Separate Copper from Steel Scrap? In the past decade the problem has become increasingly serious; greater amounts of steel scrap are […]