Effects of Velocity and Orientation on HydroCyclone
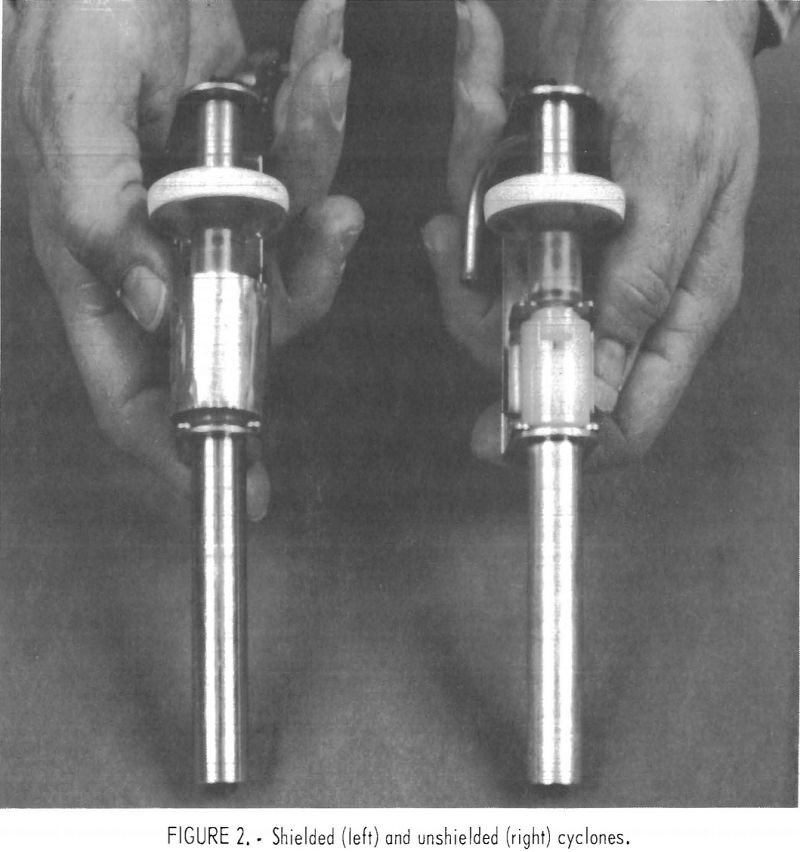
The 10-mm Dorr-Oliver cyclone is used for dust compliance sampling, which includes both stationary and personal sampling. The cyclone classifies “respirable” size particles, which are particles that reach the alveolar regions of the lungs, usually considered to have aerodynamic diameters (AED) of 10 µm or less. Although there are believed to be no instruments that […]
How to Remove Mercury from Flotation Concentrate by Leaching & Electrolysis
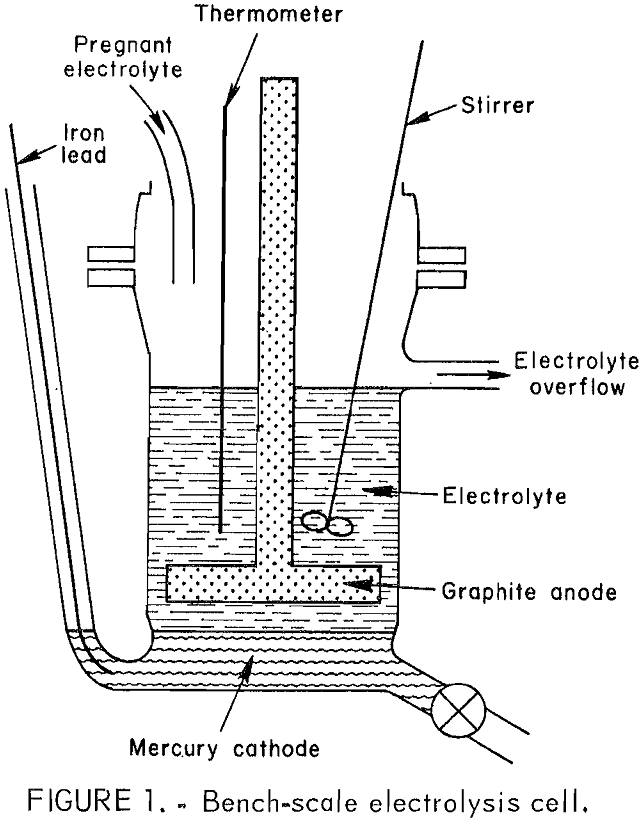
Primary mercury metal is produced commercially by heating mercury sulfide concentrate in furnaces to vaporize mercury metal, which is cooled and recovered in a condensing system. Potential health and safety problems exist because mercury vapors can escape from the furnace and condenser. The Bureau of Mines and McDermitt Mine, operated by Placer Amex Inc., the […]
Nickel Electrowinning
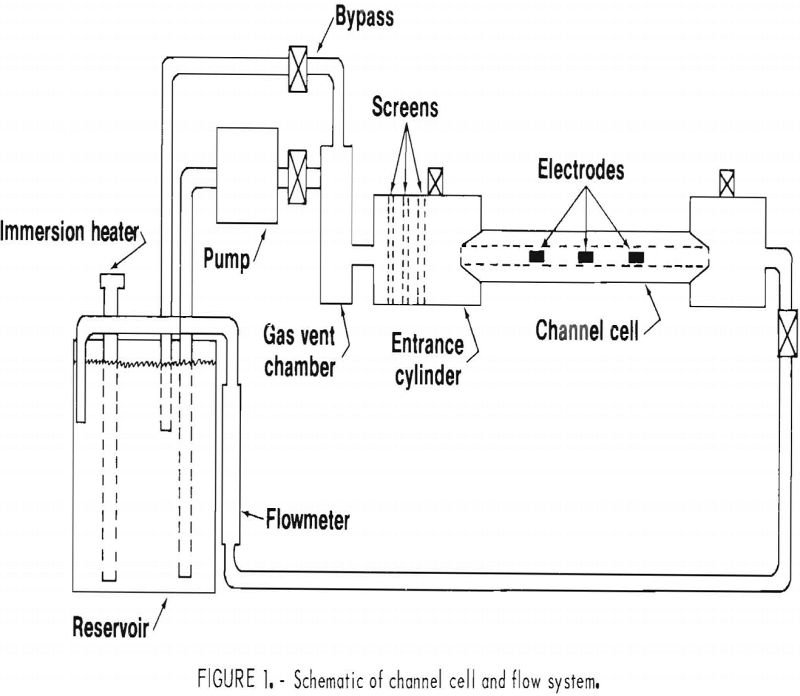
Increasing the relative motion of the electrolyte with respect to the electrode surface has long been recognized as a means by which the mass transport of ions to the electrode can be increased to allow operation at higher current densities. Basic theories and early experiments were discussed by Nernst, Brunner, Lin, Denton, Gaskill, and Putnam, […]
Copper Chalcocite Derimming of Pyrite with Cyanide
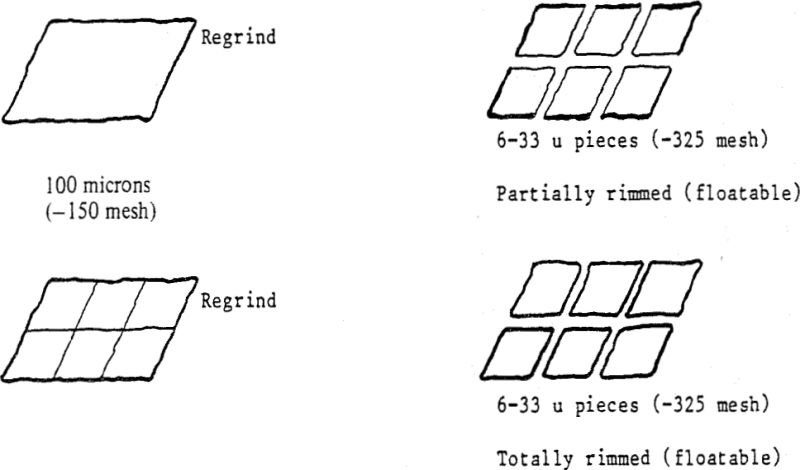
Many of the major copper ore bodies throughout the world contain chalcocite (79.9% Cu) as the principal copper mineral, yet the grades of copper concentrates produced from these ores rarely exceeds 25 to 28% Cu and in one known instance went as low as 13%. The low grade has traditionally been attributed to the presence […]
Titanium & Hydrometallurgy
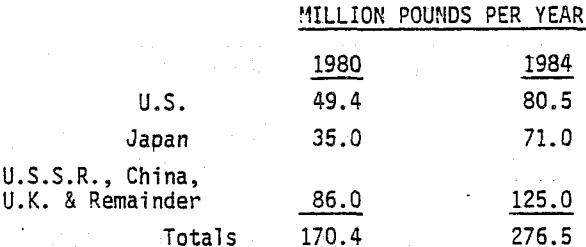
Titanium’s performance characteristics in acidic oxidizing and mildly reducing environments make it applicable to numerous currently defined and many projected hydrometallurgical applications. With titanium’s current and projected availability and price stability increased use in pressure leach, piping systems and electrorefining is practical. Titanium has a low density, .163 lb. per cubic inch, versus iron, as […]
Critical Surface Tension of Wetting of Sulfide Minerals
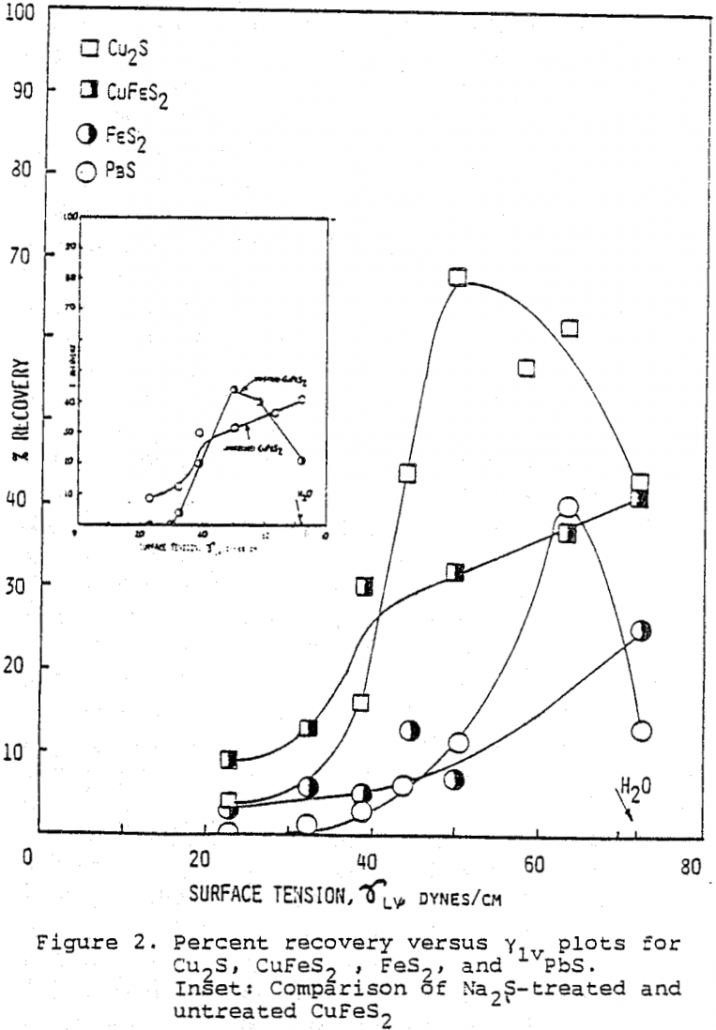
The critical surface tension of wetting (vc) of Cu2S, FeS2, PbS, and M0S2 were determined by plotting flotation recovery versus γLV which was arranged by methanol, and extrapolating to % R = 0. γc values ranged from 26 dyne cm-¹ for M0S2 to 49 dyne cm-¹ for PbS and elemental sulfur gave a value of […]
Influence of Flocculants on Filtration of Iron Concentrate
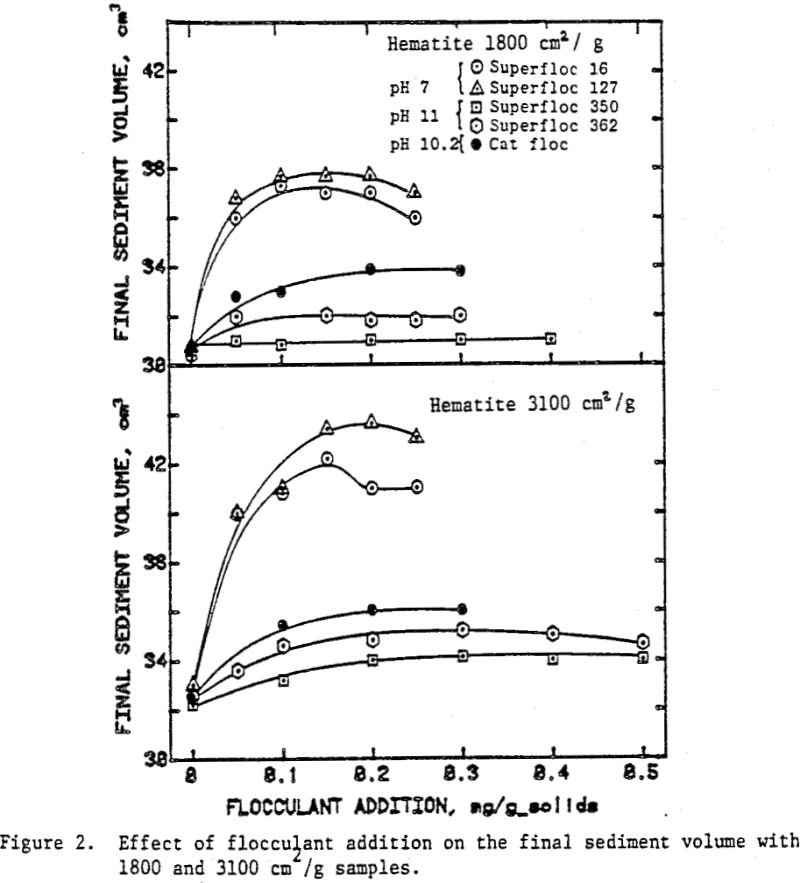
Experiments were conducted with the addition of several types of flocculants and surfactants. The filtration response of the slurries was studied in terms of the cake formation rate and the residual cake moisture. An analysis of the results is presented in ascertaining the role of flocculants and surfactants during filtration A specular hematite concentrate (67% […]
Mineral Processing Circuit Simulator
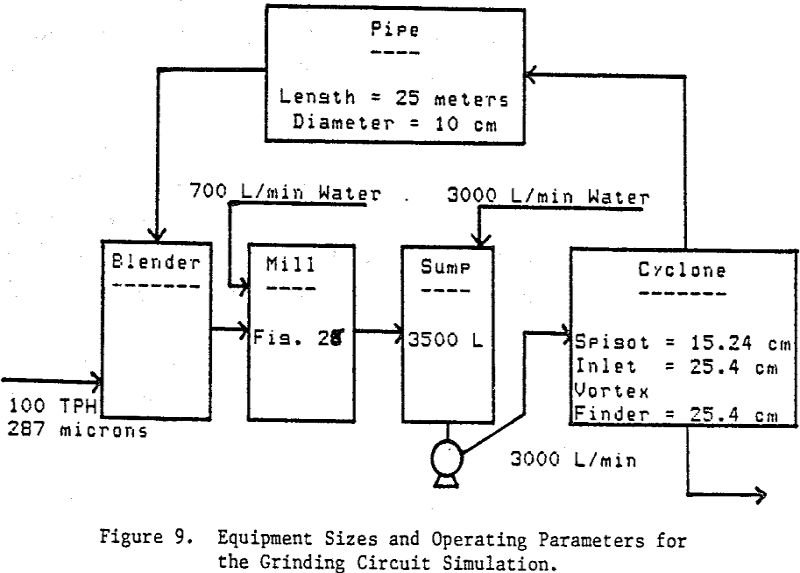
The fundamental design philosophy was based on meeting three criteria: flexibility, modifiability and usability. Flexibility refers to the ease of using the simulator to study a variety of flowsheets. A stream and unit operation numbering scheme was developed as a means of meeting this requirement. This scheme, in conjunction with modularized unit operation programs, made […]
Grinding Mills for Remote Mining Sites
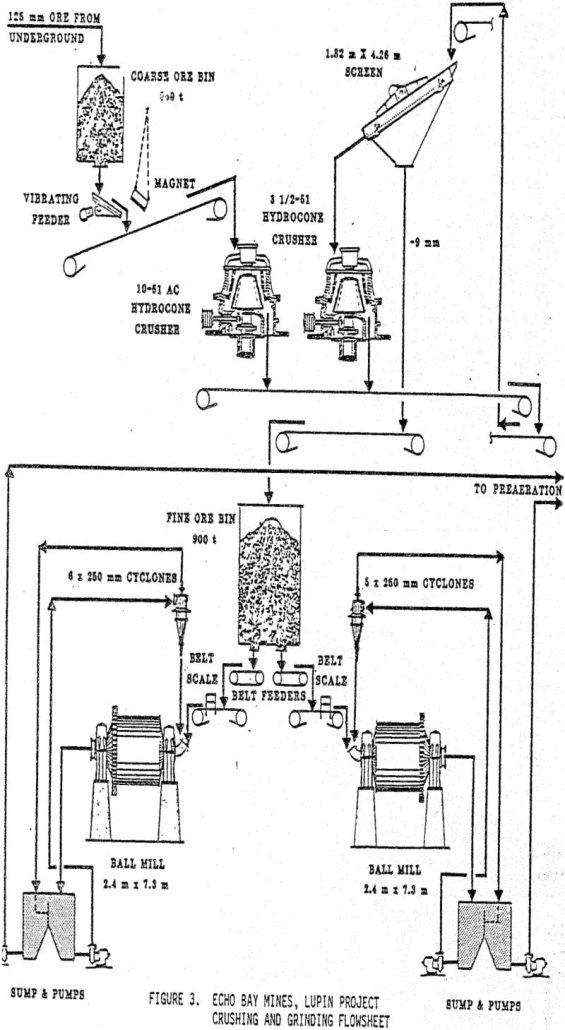
A number of challenges are faced when a mine is established at a remote site in northern Canada. The distance from suppliers, accessibility to the site, constraints on transportation of men and materials, and mining frozen ore are considerations which influence design. Mine Sites The Polaris Project of Cominco Limited of Vancouver is located on […]
Practical Mining Geology
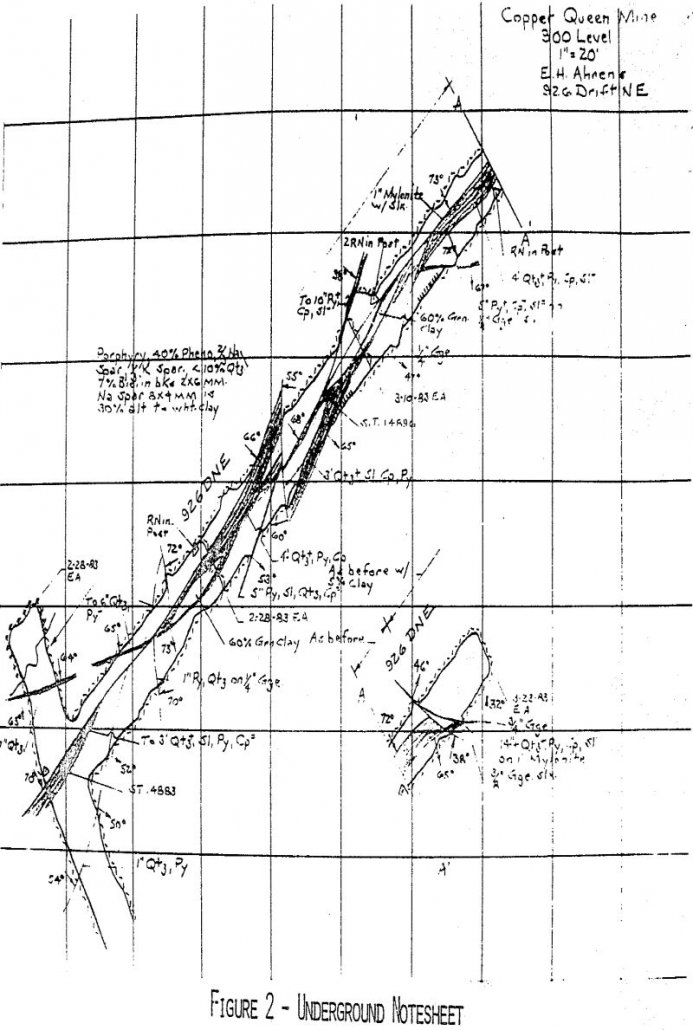
Operating geology may not seem as exciting and glamourous as exploration, especially to recent graduates, but it has its advantages as listed below: Stability: Exploration is generally the first activity curtailed in recessive periods. Satisfaction: The results of good work are visible sooner and more often. Family life is relatively normal. Geological work at an […]