Surfactants & Mine Dust Control & Effect on Flotation
Dust measurements in mines clearly indicated that the major mineral dust exposure is due to loading and transport of the ore from the mining areas. One approach to the solution of this dust problem is the application of water sprays to reduce dust dispersion. Wetting of broken rock is very effective in preventing fine dust […]
L / D Ratio in Overflow Ball Mill Design & Operation
Ball mill shape factors in the period prior to 1927 averaged 1.1/1 for 29 center discharge mills and 1.0/1 for 30 peripheral discharge mills. With the resumption of new plant construction after the 1930’s depression, the Morenci concentrator continued the 1/1 ratio with its 3.1 x 3.1 m (10 x 10 ft) mills. The ratio […]
Column Flotation Cell Residence Time Distribution RTD
We present the results obtained in a study of the residence time distributions of solids and liquids in two and three phase systems in a column flotation cell. The effects of various flotation parameters on these residence time distributions of the collection and cleaning zones are also reported. The data obtained was fitted to various […]
Selling a Mining Property
Very few mineral properties spend their entire lifespans from discovery to depletion in the hands of one owner. More likely, properties will have several owners, and partial interests may change quite often. Similarly, mineral companies are bought and sold with frequency, in recent years at what appears to be an accelerating rate. The reasons for […]
Factors Affecting Ball Mill Grinding Efficiency
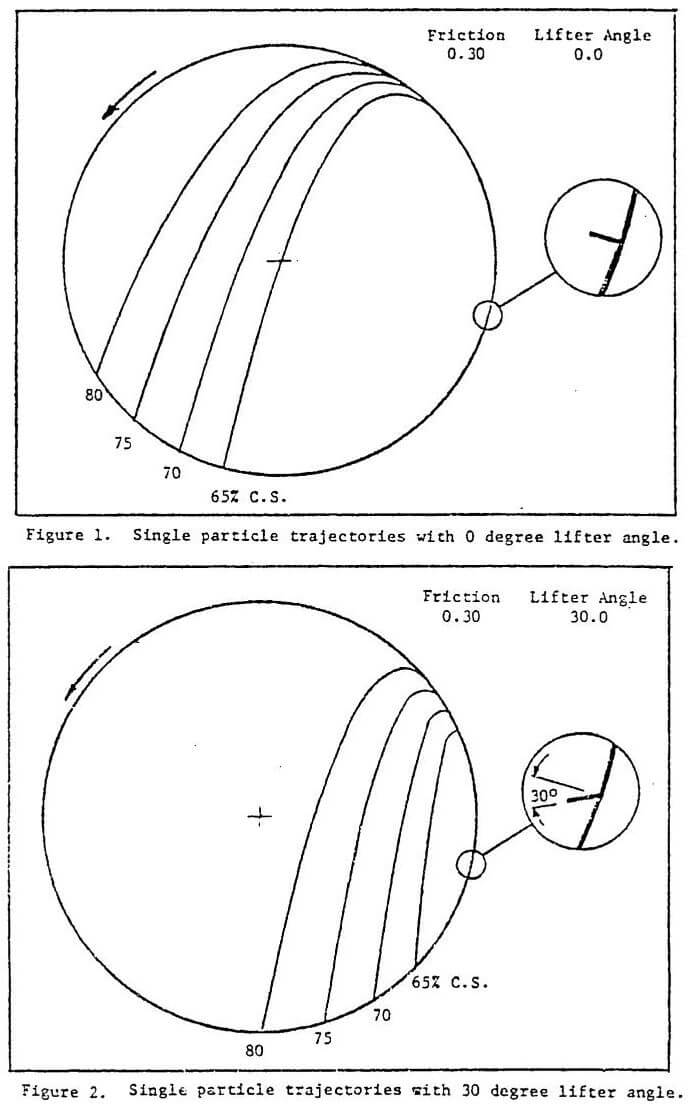
The following are factors that have been investigated and applied in conventional ball milling in order to maximize grinding efficiency: a) Mill Geometry and Speed – Bond (1954) observed grinding efficiency to be a function of ball mill diameter, and established empirical relationships for recommended media size and mill speed that take this factor into […]
Recommended Ball Mill Speed & Liner Configuration
With particular reference to mill size, it is apparent that a change in diameter in a large mill is relatively far less significant than the same change in diameter for a small one. For example, using well established relationships between power draw and mill diameter and speed, 50 mm (2 inches) of liner wear results […]
Silver Refining
Precipitates mixed with diatomaceous earth from the precipitation filter unit are dried in a filter press and mixed with borax and soda ash. This mixture is then melted in a diesel-fired furnace and cast in a silver dore cone. This cone is then melted in another furnace into an anode 7 inches by 9 inches […]
Froth Washing in Mechanical Flotation Machines
Floatable and non-floatable particles follow different sequence for transport from the pulp to the froth and from the froth out of the cell. For floatable particles, the principal mechanism is true flotation (i.e. bubble attachment and levitatlon). Non-floatable particles arrive to the slurry-froth interface by hydraulic entrainment (i.e. wake carry over), mechanical entrainment (due to […]
How to Improve Ball Mill Performance
Application of value engineering techniques to grinding process modelling led to the identification of two basic functions of the ball mill-classifier circuit. In terms of a specified circuit product size which is used to differentiate between “coarse” or oversize material and “fines” or undersize material, these basic functions are (a) breakage of the coarse material […]
Organic Flotation Depressant
These depressants are organic mixtures reacted with inorganic salts. They have found application for depression of oxidized pyrite, marcasite and pyrrhotite during the flotation of Cu, Cu-Zn, Cu-Pb-Zn and Pb-Zn ores. Some of these depressants have been adapted for depression of zinc during sequential copper zinc flotation. Depressants from the DS series have been successfully […]