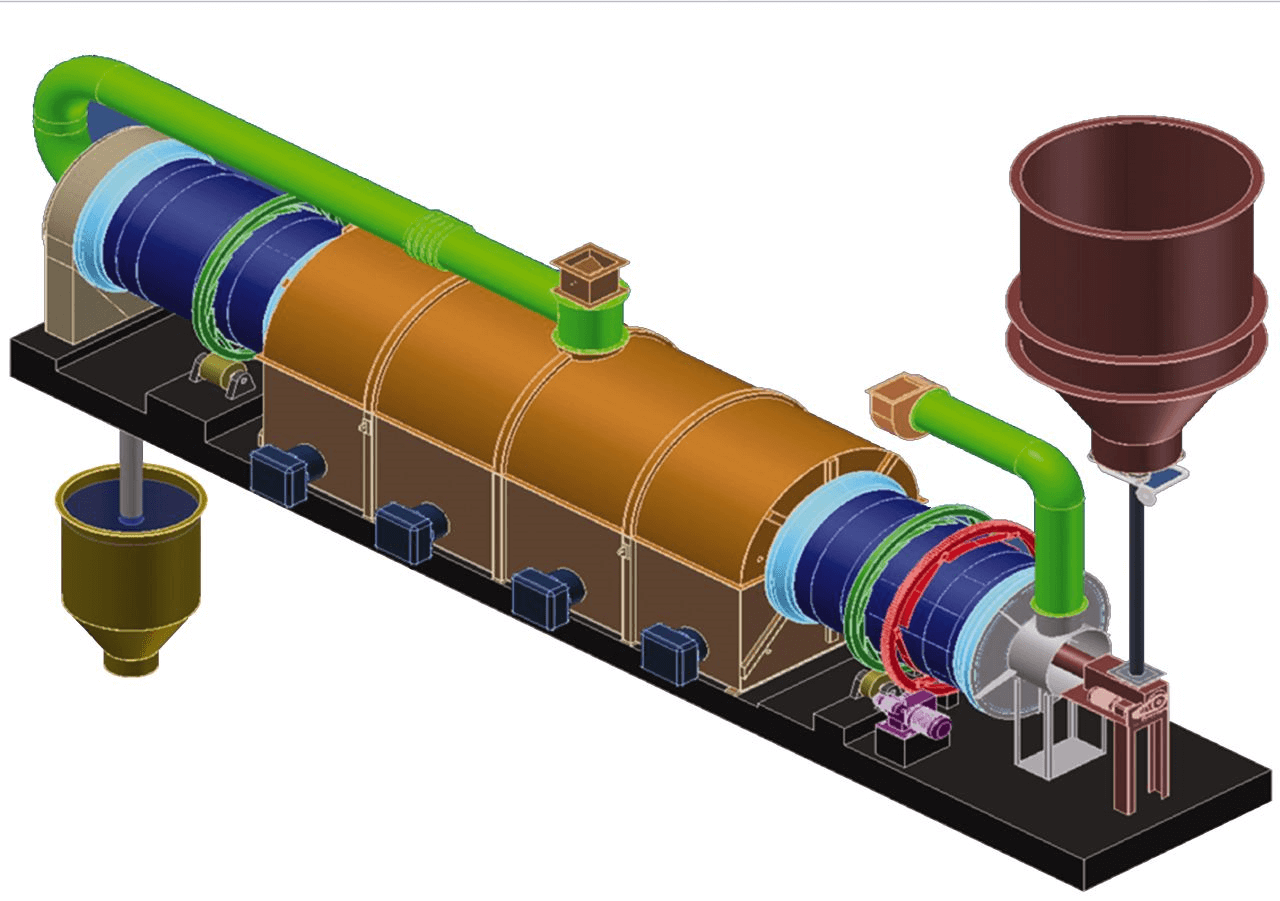
In normal process streams activated carbon is exposed to a variety of chemicals. Organic compounds tend to adsorb readily on the hydrophobic activated carbon, which reduces site availability for gold cyanide. Other compounds such as calcium and magnesium carbonate commonly precipitate on the carbon surface and restrict gold adsorption access. Consequently, the performance of the activated carbon decreases unless it is regenerated. Regeneration generally consists primarily of thermal activation in a rotary kiln at around 650 C in steam to remove organic debris. Thennal activation is preceded or followed by exposure to hydrochloric acid to remove inorganic precipitates such as carbonates.
The carbon reactivation circuit is series of unit processes designed to restore the activated carbon’s ability to recover precious metals from cyanidation circuit solutions. Since each circuit will be treating a unique solution, which will result in unique carbon fouling problems, the reactivation circuit design must consider several variables, which includes the preference of the plant operator.
The main unit operations within the reactivation circuit are acid washing, elution and thermal reactivation. This paper will focus on the design considerations in the acid wash and thermal reactivation circuits, although it should be noted that all three operations must be operated efficiently to ensure proper carbon reactivation and the resultant low soluble gold losses from the cyanidation circuit.
As noted previously, carbon kinetic activity is an important factor in the efficient operation of a CIP circuit. Lower carbon activity will result in higher carbon inventories in the circuit, lower gold loadings on the carbon, and higher soluble gold losses from the circuit. The average carbon activity in a circuit is mainly a function of the efficiency of the carbon regeneration process (i.e.. not the activity of the new carbon).
The importance of returning barren carbon to good kinetic activity has long been known. Despite this knowledge, gold processing operations have generally not been particularly good at regenerating barren carbon. Experience over the past 30 years suggests that on average regenerated carbon has a kinetic activity no better than 50% of new carbon and often only 20-40%. A minority of operations to achieve good regeneration (>70% of new carbon), demonstrating that a satisfactory outcome is possible with proper equipment and procedures.
Obtaining a good kinetic activity for a barren carbon is a function of 3 steps:
- Acid washing to remove inorganic adsorbates. such as calcium
- Elution to remove gold, silver, and base metals
- Thermal regeneration to remove organic adsorbates and refresh active sites
In general, process operations manage the acid washing and elution stages well; however, the thermal regeneration process is often problematic. Lack of focus in this atva often leads to underinvestment in good equipment, poor operating practices (insufficient temperature/residence time/steam), and poor maintenance. Often operations will cease thermal regeneration for an extended period due to equipment failure. While there is often no observed immediate impact, over time a significant degradation in CIL performance will occur.
More recently, there has been a renewed focus on better carbon regeneration, as part of the overall focus on improved carbon management.
During adsorption, many organic and inorganic adsorbates can accumulate within the porous structure of activated carbon. Micropores (up to 3 nm) constitute the primary adsorption sites, and therefore tend to become congested to a greater degree than do mesopores (3 to 60 nm) and macropores (60 to 10000 nm). However, mesopores and macropores also capture adsorbates of relatively high molecular mass and, as a result, there is a progressive decline in adsorption efficiency. Activated carbon that is used to purify water upstream of a carbon-in-pulp (CIP) process—by capturing organic compounds that are likely to foul the carbon in the CIP reactors— needs periodic thermal treatment to selectively remove the organic adsorbates and thus restore its activity. In a CIP arrangement that does not include adsorptive pretreatment, organic adsorbates can be partially desorbed during the elution of the precious metals from the carbon (including pretreatment with hot acid), but a substantial fraction of these adsorbates will remain and will have to be dealt with at regular intervals by thermal treatment.
The objectives during regeneration are the selective removal of the adsorbates that have accumulated on the carbon during adsorption operations, and the restoration of the original porous structure and activity of the carbon with as little damage as possible to the carbon itself.
The first three steps, viz drying, vaporization, and pyrolysis, normally proceed with few complications. However, pyrolysis should not be conducted at temperatures higher than 850 °C in a non-oxidizing atmosphere, since graphitization of the pyrolysed residue can occur, resulting in a structure similar to that of activated carbon and equally refractive. Hence, during subsequent selective oxidation, it would be difficult to remove the residue without extensively damaging the structure of the activated carbon. Pyrolysed residues obtained at lower temperatures are reported to be more reactive, and therefore more readily oxidizable, than activated carbon.
The proper reactivation of carbon does not involve direct oxidation of the pyrolysed residue with oxygen. On the contrary, the atmosphere within that zone of the furnace is deliberately depleted in oxygen so that the following reactions will be minimized.
All thermal regenerations were conducted using a two-inch externally heated rotary Cube furnace. In order to simulate an expected plant condition of 50 percent moisture in the carbon prior to regeneration, 100 g of oven dried material was placed in a 250 ml jar and 50 g of D.I. water was added. The jar was then tightly capped and Che carbon allowed to equilibrate. Additional water, when required, was added by pumping the required volume of water through a steam superheater prior to entering Che rotary furnace. The pump race was adjusted to give the additional water required over the course of the regeneration retention time. The 100 g charge of wetted carbon was placed in a nichrome 60 mesh basket assembly which was then quickly introduced into the tube furnace and the end cap securely fastened. After the required time, the carbon and basket assembly was removed, then cooled in a sealed cooling chamber.