Vibrating Screen
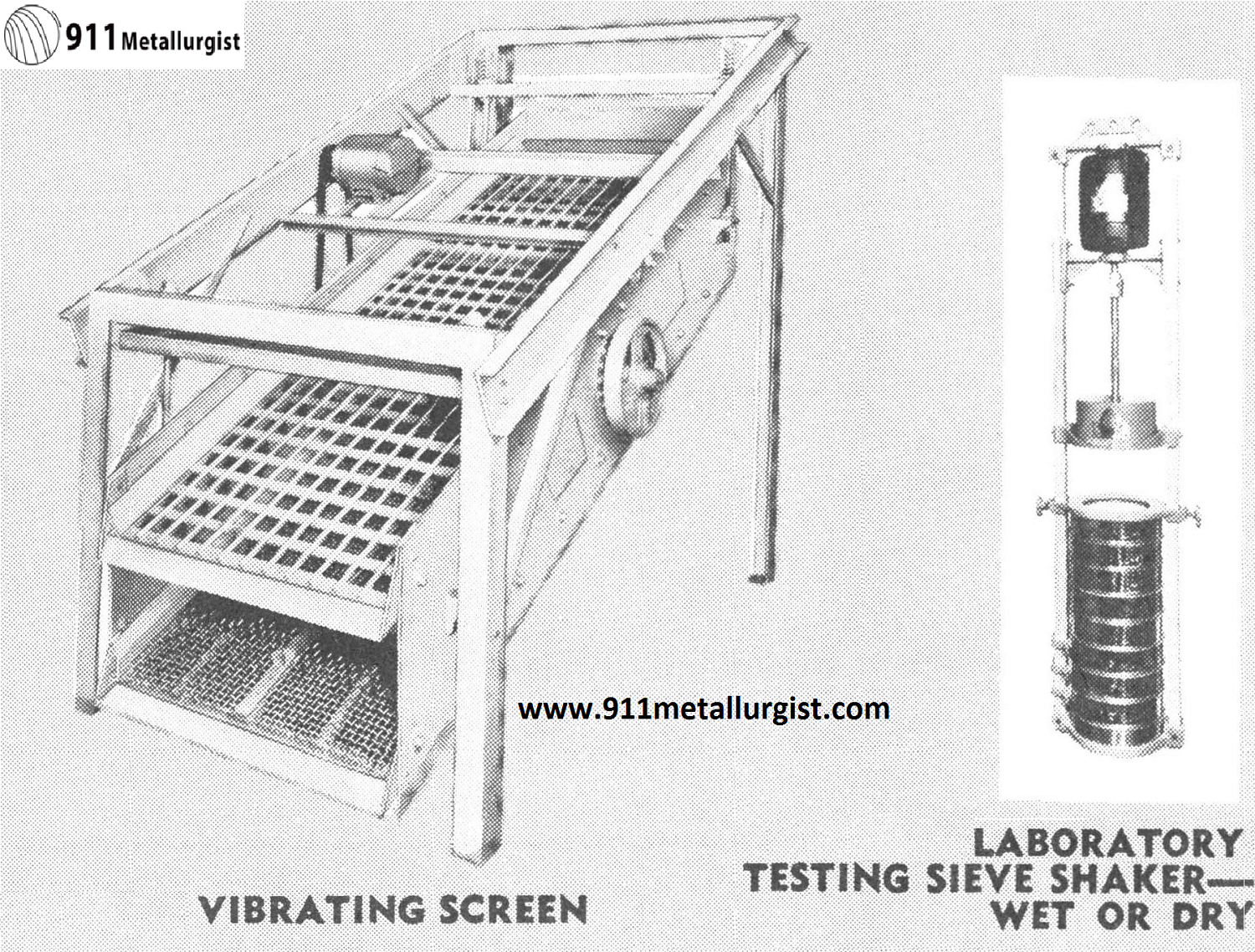
For efficient wet or dry screening—Hi-capacity, 2-bearing design. Flywheel weights counterbalance eccentric shaft giving a “true-circle” motion to screen. Spring suspensions carry the weight. Bearings support only weight of shaft. Screen is free to “float” and follow positive screening motion without power-consuming friction losses. Saves up to 50% HP over 4- bearing types. Sizes 1 x […]
Gold Alloy Melting and Casting
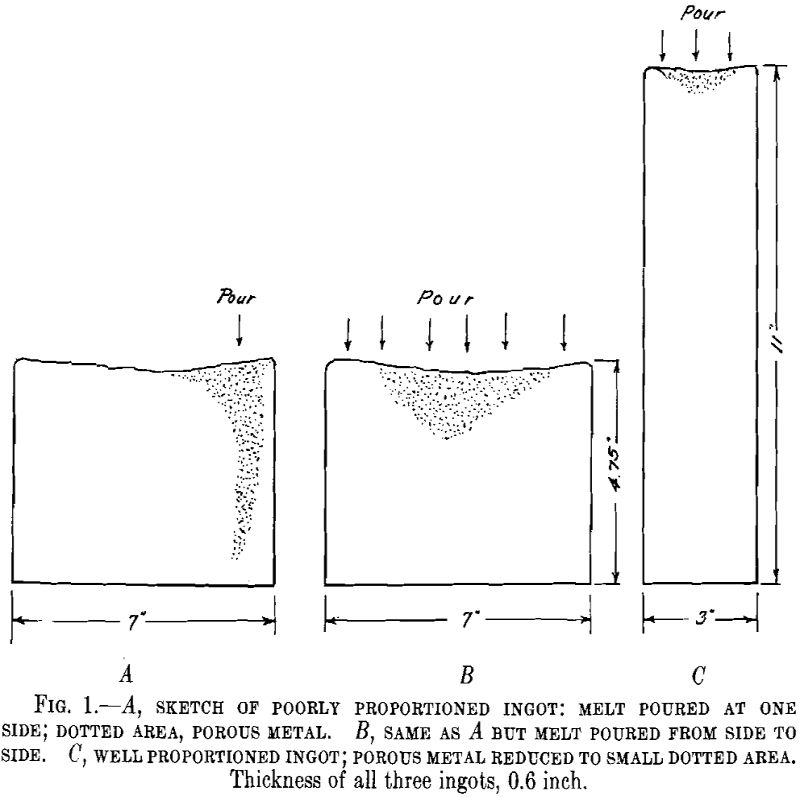
The problem of scrap is probably of greater importance in the production of gold, silver and other precious metal alloys than is the case for base metals and alloys. Remelting of gold and silver scrap in the shop is always a costly process because it involves losses by oxidation of the base metals in the […]
Method for Estimating the Efficiency of Pulverizers
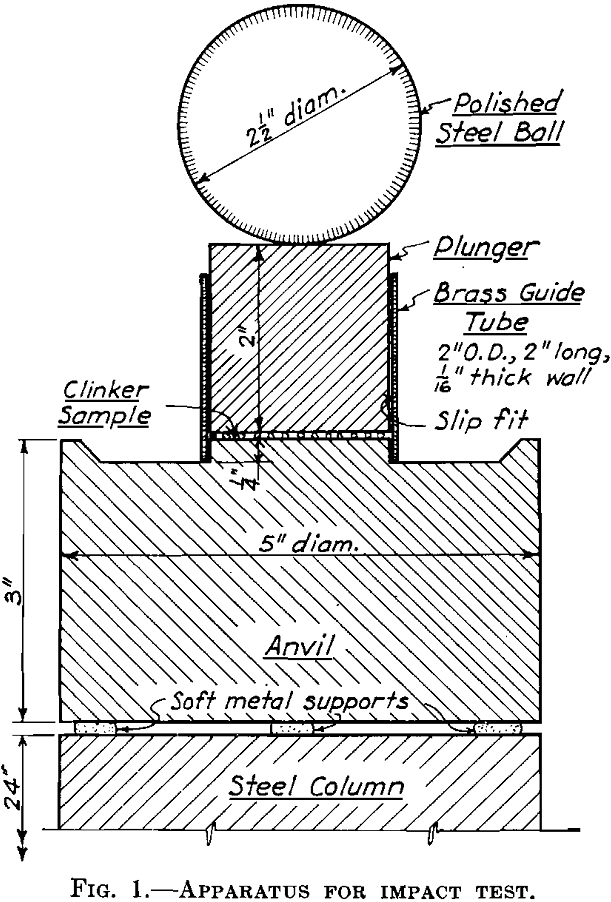
Grinding costs are an important item in cement manufacture, and the cost of power is one of the large items in grinding costs. Even where power is of secondary importance, cost items dependent on mill capacity are influenced by the efficiency with which the mill uses power. Tube mills typify the grinding mills most generally […]
Screw Crusher
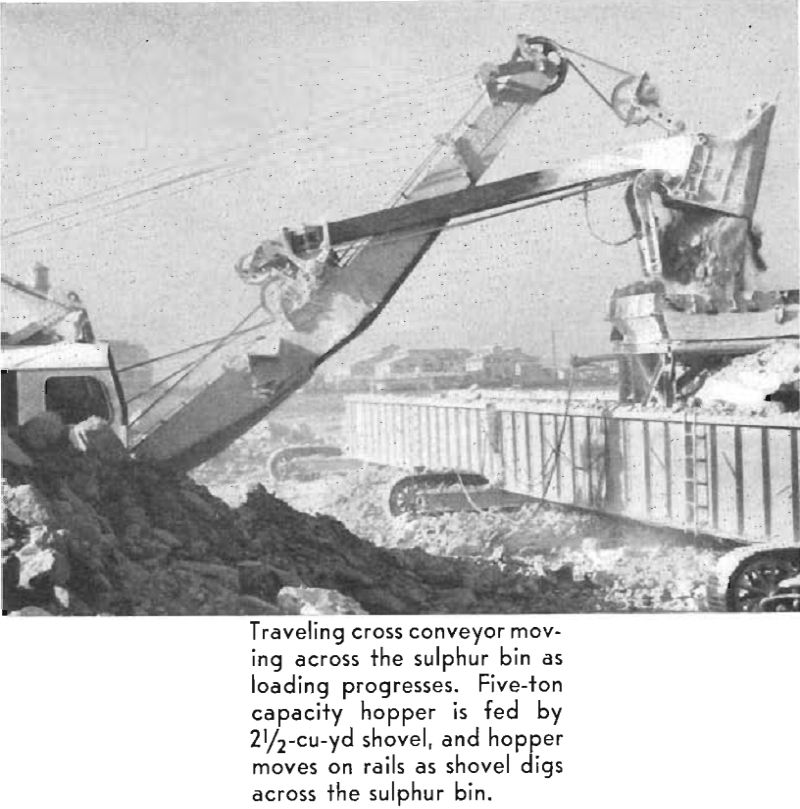
The Freeport Sulphur Co. built a portable screw crusher in 1944 that solved a problem that none of the crusher manufacturing companies contacted were able to do. Two of these crushers have now been in service for 6 years, giving satisfactory service in handling a million tons per year, and having a capacity of over […]
Hardness and Toughness of Rocks
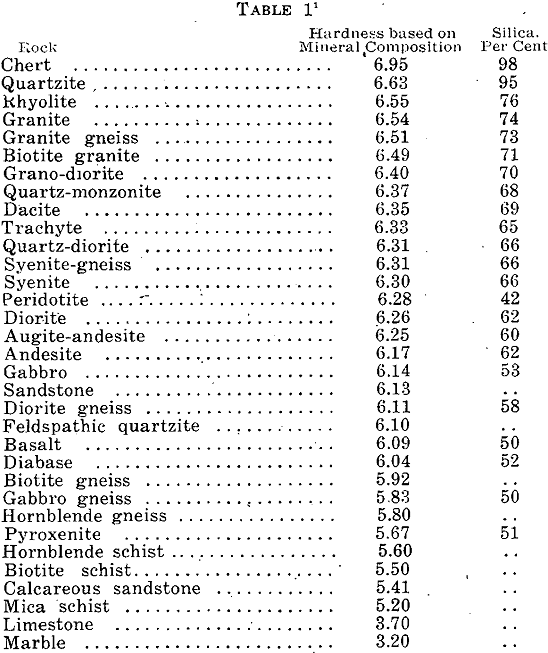
The speed of drilling rock has become an important factor in mining operations, while the placement of holes, kind, and quantity of explosive used are equally important. These are a function of the rock hardness and toughness. Both of these factors must be considered in compiling a table that will enable a mine operator or […]
Concasseur
Le concassage constitue la premiere etape de la comminution. Son objectif n’est pas la liberation des mineraux, mais simplement la reduction de dimension afin de faciliter la manipulation ulterieure du minerai. II est normalement fait a sec en deux ou trois etapes. L’alimentation provient de la mine et a une dimension pouvant aller jusqu’a 1.5 […]
Jaw Crusher Working Principle
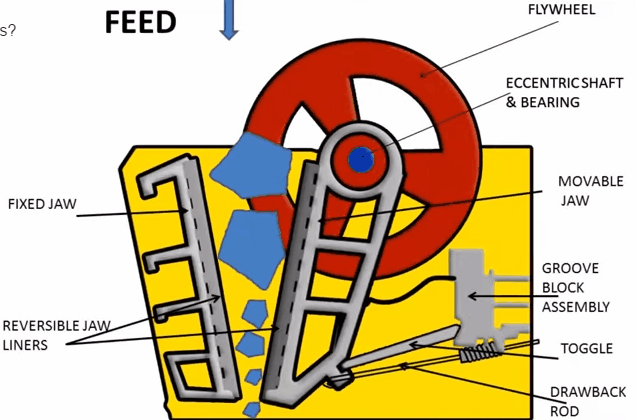
A sectional view of the single-toggle type of jaw crusher is shown below. In one respect, the working principle and application of this machine are similar: the movable jaw has its maximum movement at the top of the crushing chamber, and minimum movement at the discharge point. The motion is, however, a more complex one than the […]
Use of Bleaching Clays in Water Purification
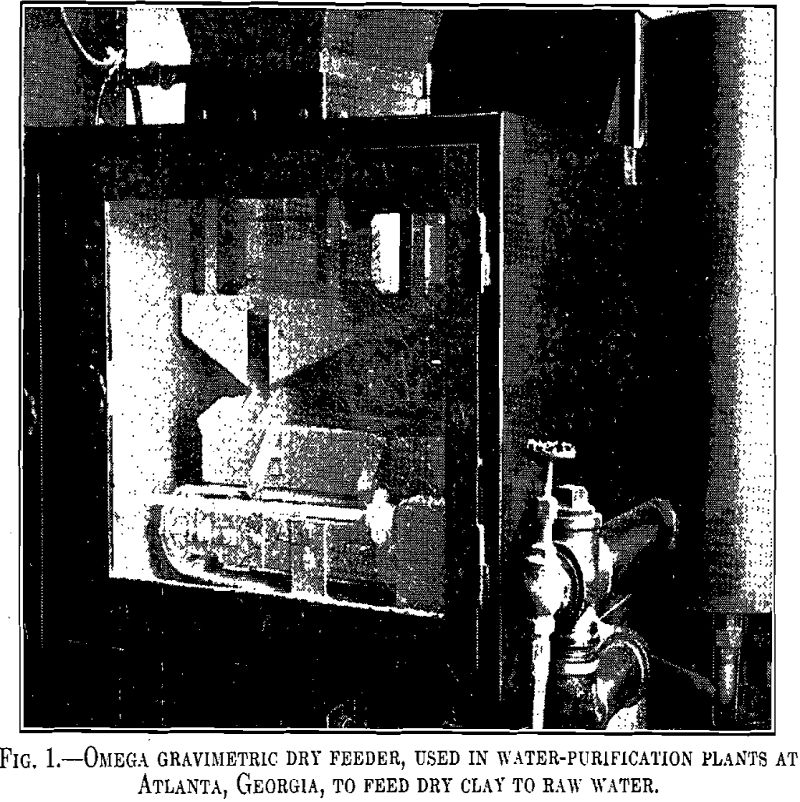
Bleaching clays have been used extensively in the oil-refining industries for a number of years. Their use in water purification is relatively recent and less extensive. They are frequently classified as (1) those naturally active and (2) those active after artificial activation with acid. Fuller’s earths fall within the general group of bleaching clays and […]
Wilfley Table
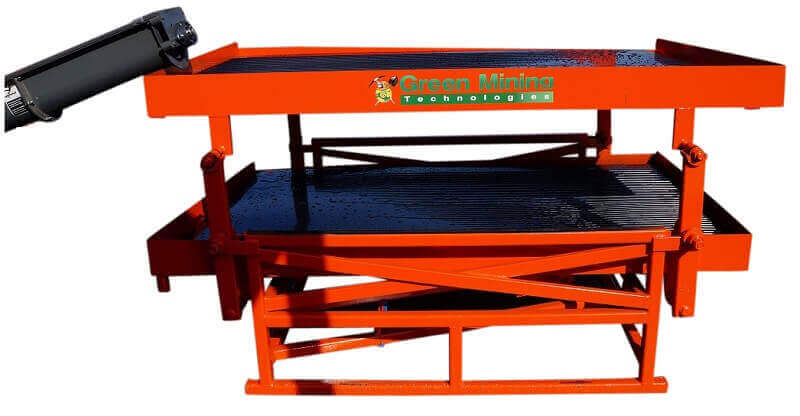
The Wilfley table is a truly remarkable gold concentrating table first built on a preliminary scale in May, 1895. The first full-sized table was built by Mr. A. R. Wilfley, and was used in his own mill in Kokomo Colo., in May, 1896. The first table sold for installation was placed in the Puzzle mill, Breckenridge, […]
Ball Mill Grinding
Three “ores” were used in the Ball Mill Grinding experiments. It is doubtful whether material more resistant to grinding can be found among the world’s ores. When flotation was newer and regarded as the panacea in ore treatment, the Tri-State operators were critized for not grinding the entire mill feed to flotation size and thereby […]