Vibrating Screen
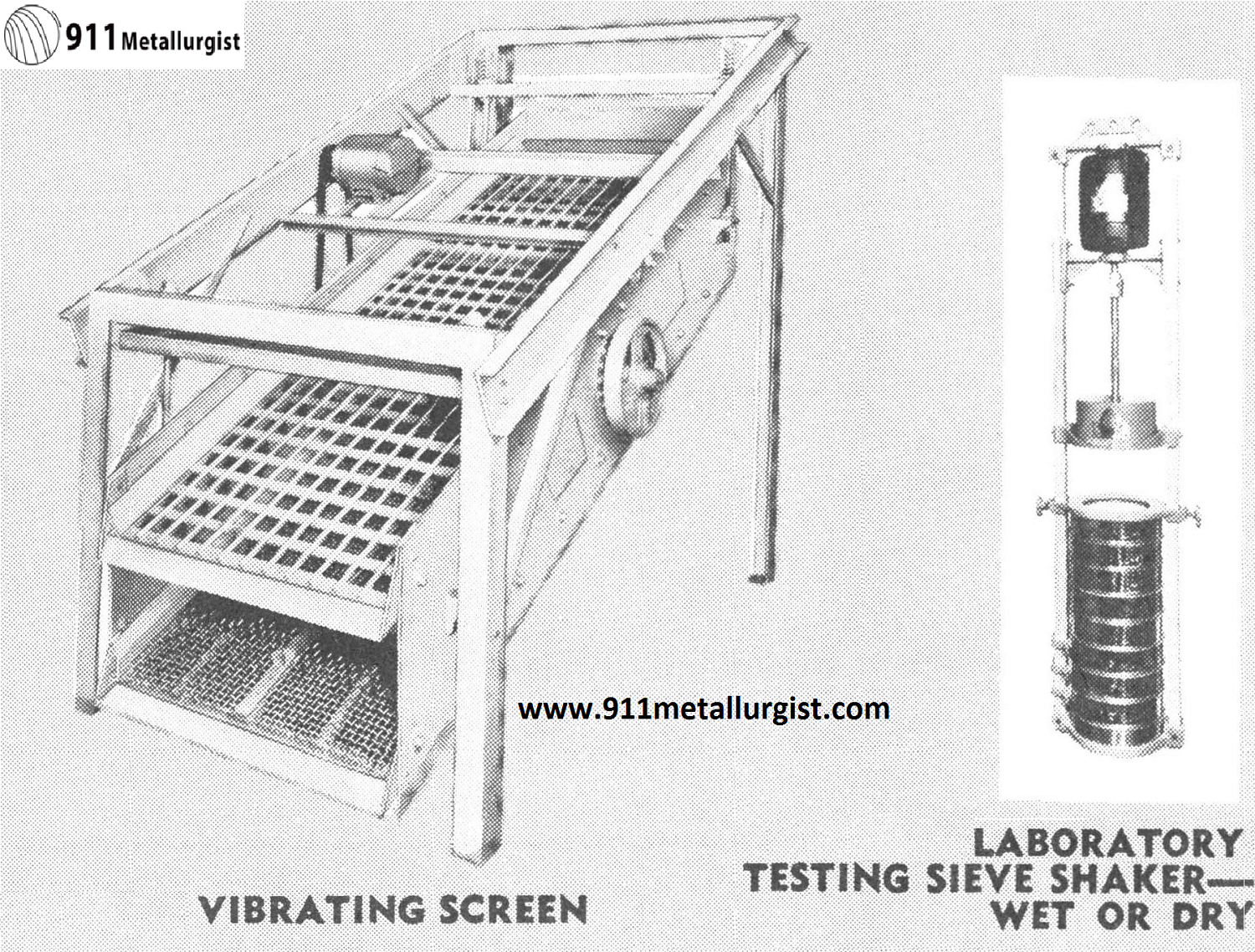
For efficient wet or dry screening—Hi-capacity, 2-bearing design. Flywheel weights counterbalance eccentric shaft giving a “true-circle” motion to screen. Spring suspensions carry the weight. Bearings support only weight of shaft. Screen is free to “float” and follow positive screening motion without power-consuming friction losses. Saves up to 50% HP over 4- bearing types. Sizes 1 x […]
Screw Crusher
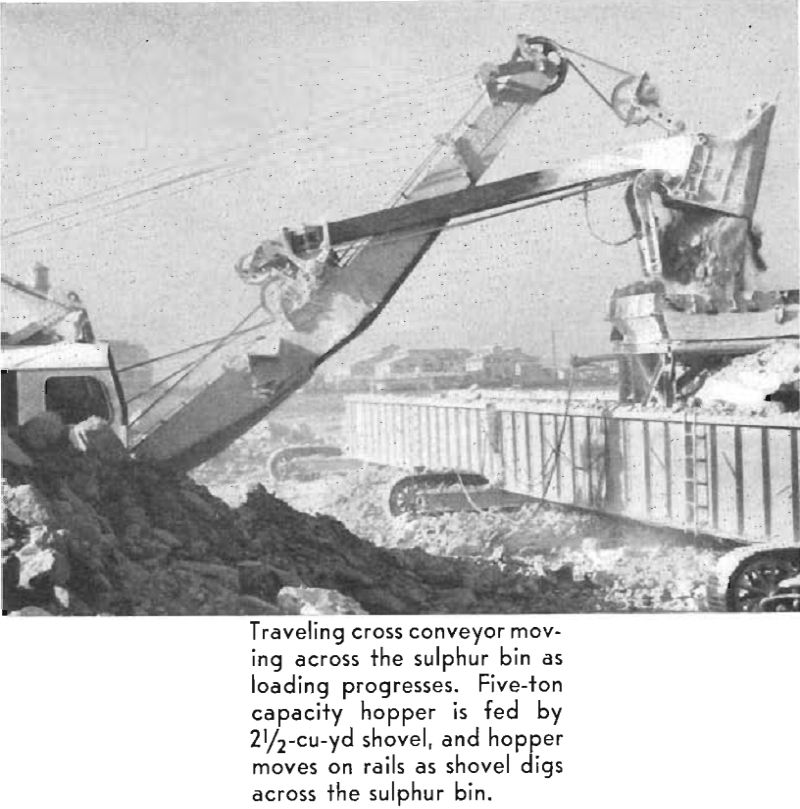
The Freeport Sulphur Co. built a portable screw crusher in 1944 that solved a problem that none of the crusher manufacturing companies contacted were able to do. Two of these crushers have now been in service for 6 years, giving satisfactory service in handling a million tons per year, and having a capacity of over […]
Hardness and Toughness of Rocks
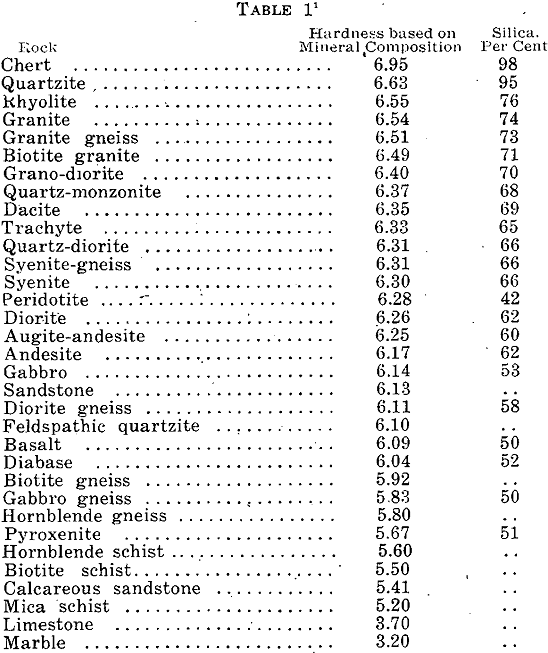
The speed of drilling rock has become an important factor in mining operations, while the placement of holes, kind, and quantity of explosive used are equally important. These are a function of the rock hardness and toughness. Both of these factors must be considered in compiling a table that will enable a mine operator or […]
Concasseur
Le concassage constitue la premiere etape de la comminution. Son objectif n’est pas la liberation des mineraux, mais simplement la reduction de dimension afin de faciliter la manipulation ulterieure du minerai. II est normalement fait a sec en deux ou trois etapes. L’alimentation provient de la mine et a une dimension pouvant aller jusqu’a 1.5 […]
Jaw Crusher Working Principle
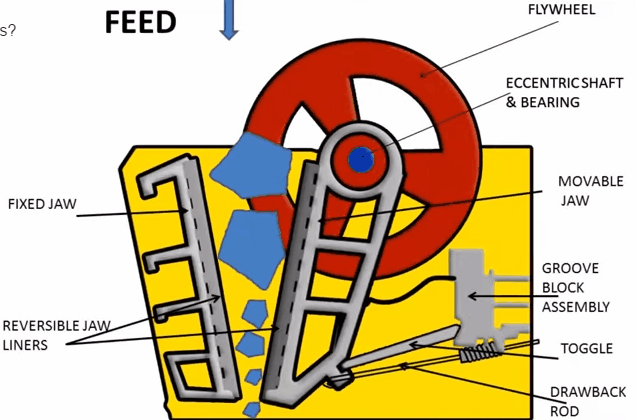
A sectional view of the single-toggle type of jaw crusher is shown below. In one respect, the working principle and application of this machine are similar: the movable jaw has its maximum movement at the top of the crushing chamber, and minimum movement at the discharge point. The motion is, however, a more complex one than the […]
Crushing Chestnut to Produce Buckwheat
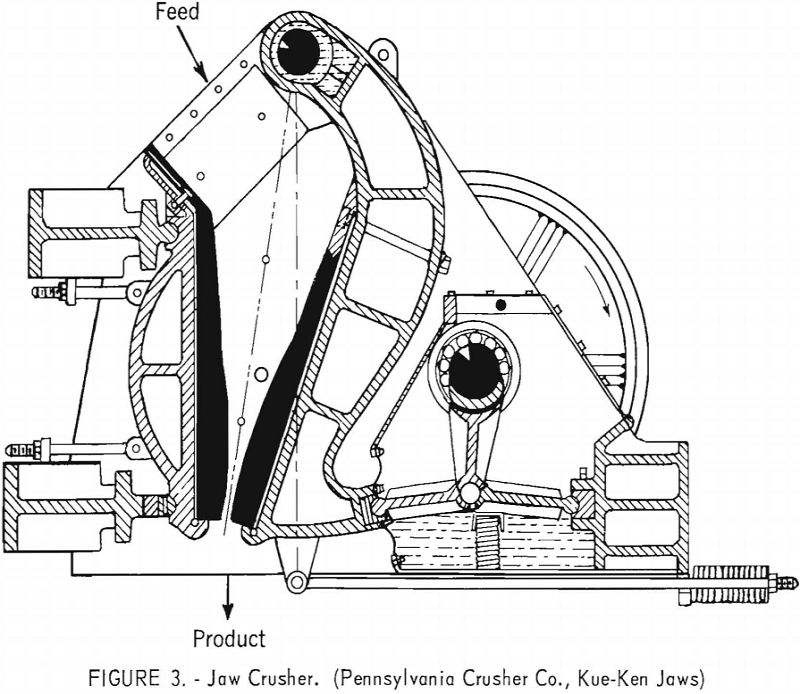
The crushing of chestnut-size (1-5/8 by 13/16 inch) Pennsylvania anthracite in four commercial crushers (impact, jaw crusher, hammer mill, and gyratory types) was studied by the Bureau of Mines to determine which could produce the largest proportions of buckwheat Nos. 1 and 2 sizes (9/16 by 3/16 inch). Single pass dry and wet crushing techniques […]
Crushing Granite
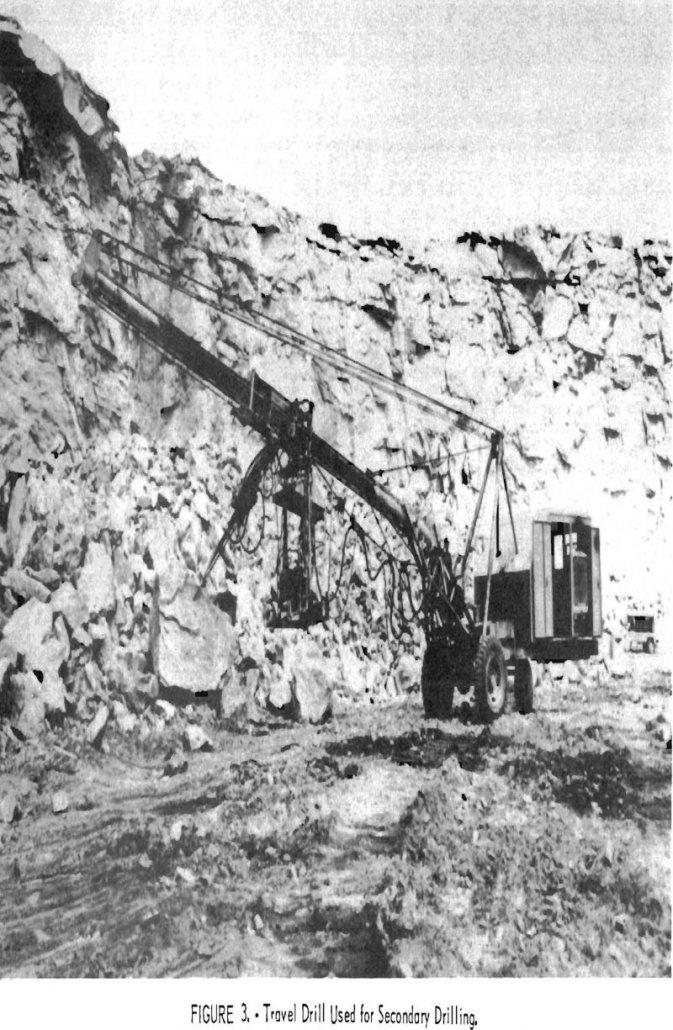
The quarry is located in the western part of the Piedmont Plateau. Geologically, this province is described by Watson as an area of highly metamorphosed sedimentary and igneous rocks of Paleozoic and pre-Paleozoic age. The Piedmont region of South Carolina has extensive areas of granite and gneiss that are suitable for aggregate. The gneisses have […]
Conveyor Belt Fire Hazard
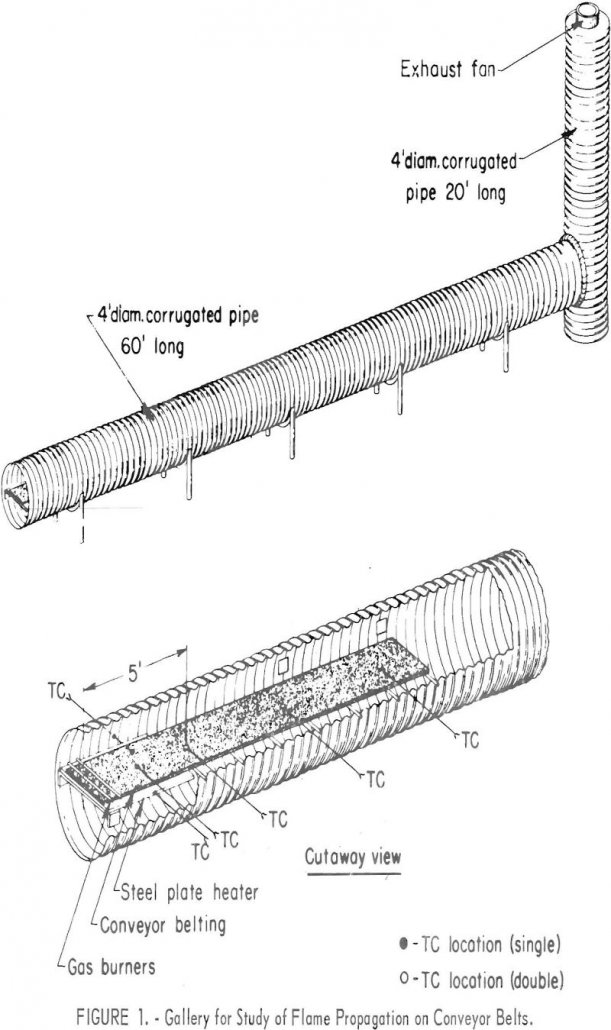
This investigation showed that neoprene, polyvinyl chloride, and rubber belts ignite readily when subjected to an impinging flame. Although pre-heating of the belt is not necessary for ignition, preheating does increase the probability of developing a self-sustaining flame after ignition. The time and total quantity of heat required to ignite neoprene were greater than those […]
Impact Crushing Size Distribution
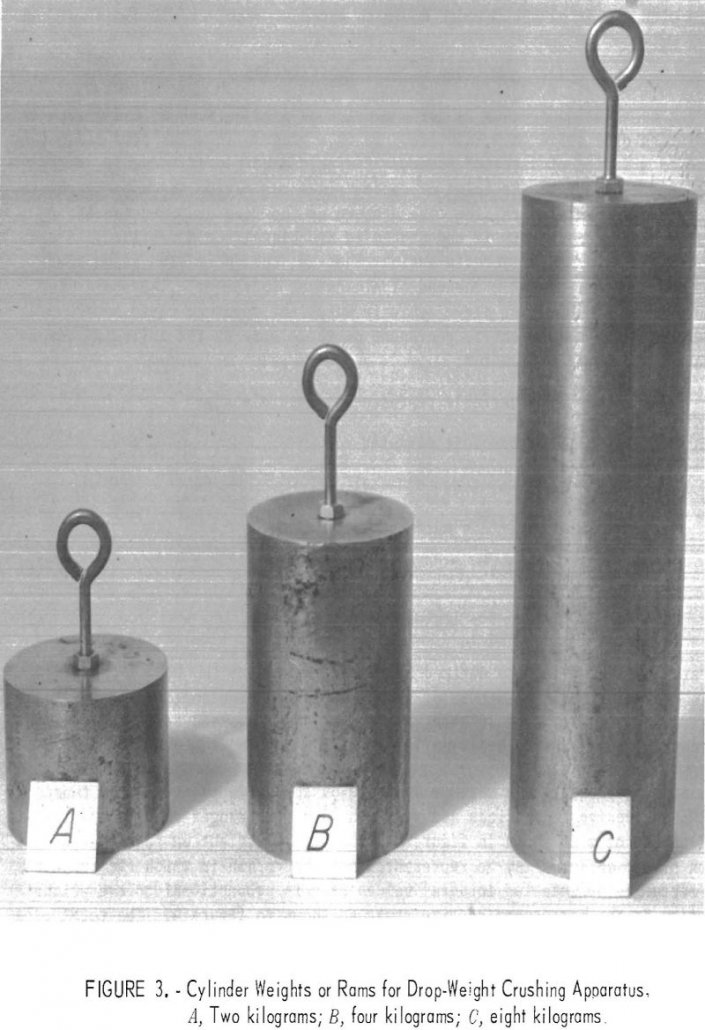
Although the comminution process has undergone much experimental study, there is not yet an adequate theoretical basis for predicting the mean size and size distribution of the product from a comminution machine. This lack is hardly surprising, since most of the considerable body of knowledge concerning the deformation of solids becomes inapplicable when the stresses […]
Bin Hopper Flow Design & Engineering
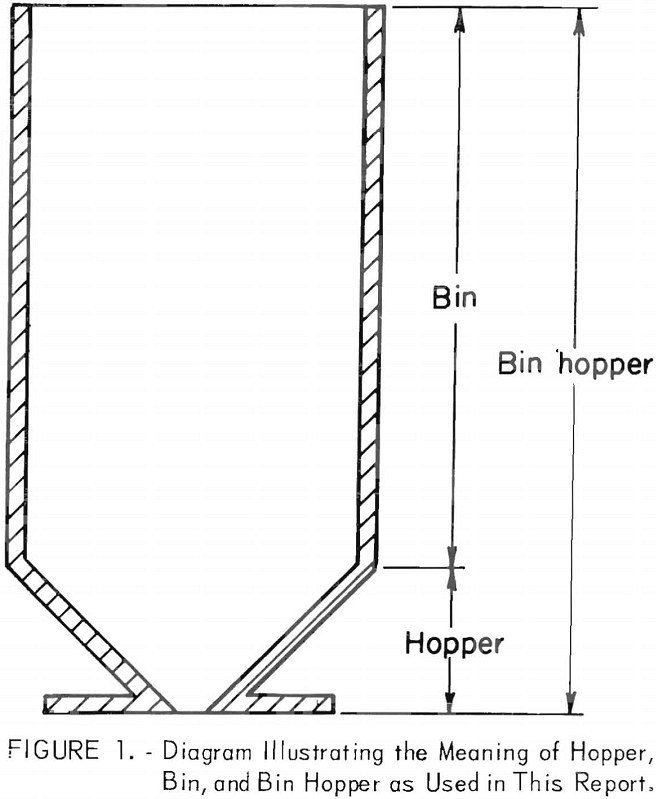
A detailed Bin Hopper Flow Design & Engineering Study: The mining industry in the United States alone produces nearly 4 billion tons of new bulk materials annually that has a mine-mouth value in excess of 20 billion dollars. The potential for realizing substantial savings in mining and processing costs through improved materials handling systems design […]