Hydrostatic Bearing Type Center Mechanism
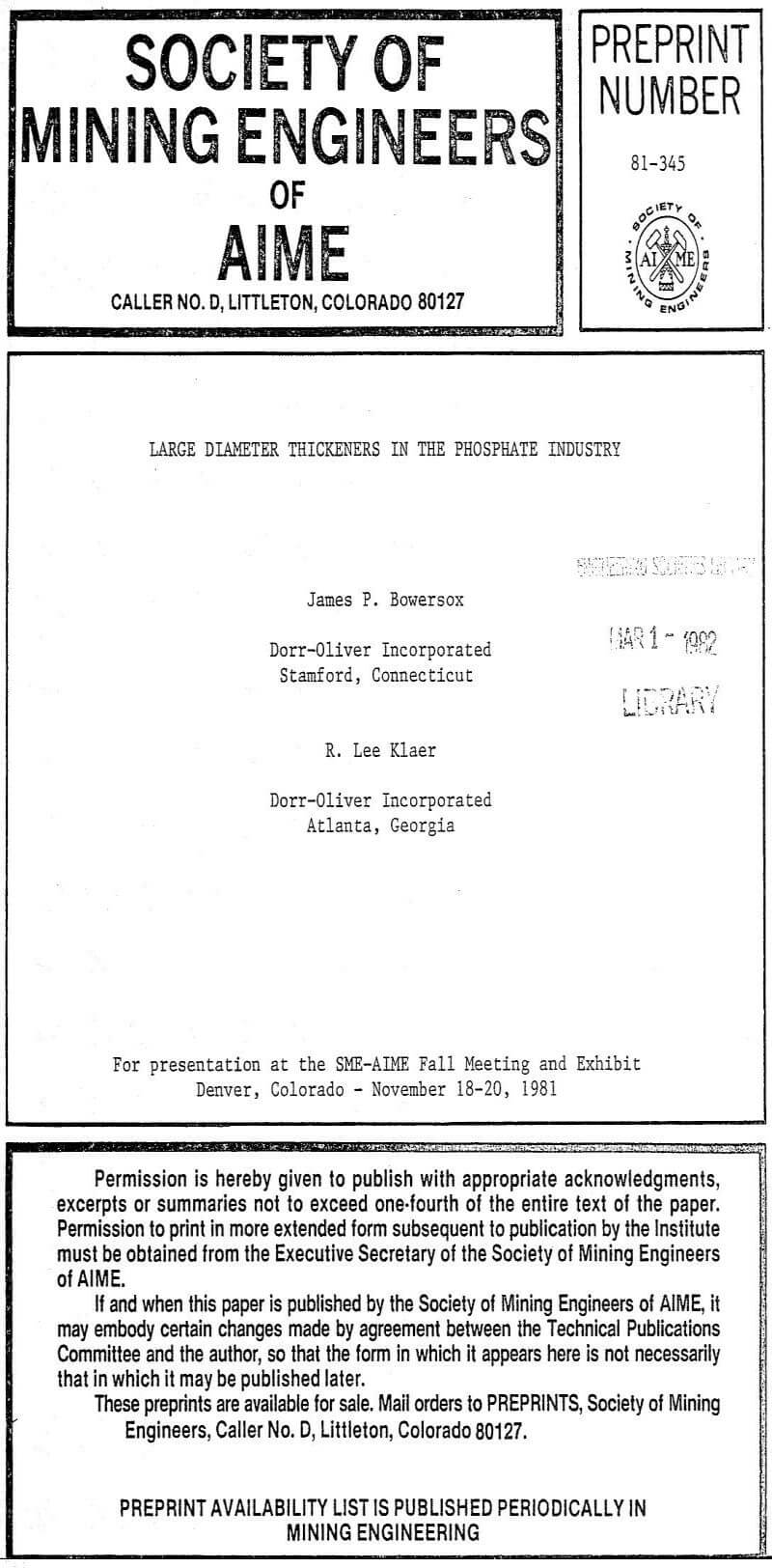
Development of the Hydrostatic Bearing Mechanism evolved from the caisson thickener design. Conventional thickener mechanisms are driven by gearing which rides on ball or roller type anti-friction bearings. It would not be feasible to use this method of support with a very large diameter bearing, especially with high torque, vertical and unbalanced loads. Additional stresses […]
Batch Thickening Theory

Kynch showed that a constant concentration layer propogates upward at constant rate in batch thickening tests under the assumption that settling velocity is a function of only the concentration, as described earlier under Continuous Thickening Theory. His conclusion can be expressed as: Where Ci is the concentration of solids in the layer, and Vi is […]
Selecting Thickener Depth Determination
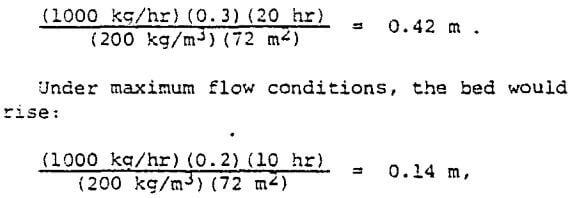
Where there is little significant effect of compression factors, the bed depth can be selected based upon operating characteristics of the thickener installation. In this case, information must be available (or assumed) concerning the normal fluctuations in feed rate and concentration. Also, sludge storage requirements should be considered. For illustrative purposes, the following example of […]
Flocculation
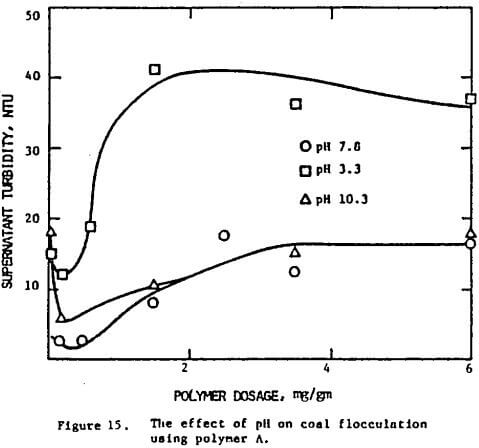
The flocculation behavior of coal, quartz and clay was studied by measuring the turbidity of the supernatant liquid after one hour of settling. Figure 14 is a plot of turbidity and adsorption density against equilibrium concentration. The turbidity of the supernatant liquid decreases until a minimum is reached and tends to rise thereafter. The results […]
Thickener Process Control Strategy
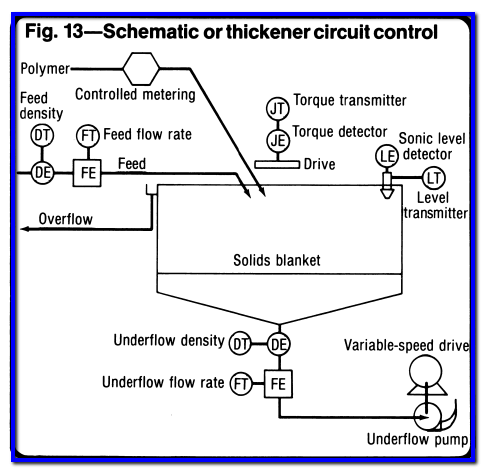
The objectives of thickener control are varied, but in most instances, the objective is to dewater the slurry, reclaim the clear overflow for reuse in the process, and produce a thickened or more dense underflow, which can either be rejected, in the case of tailings, or used as feed for subsequent unit operations. The general […]
Recover Concentrate from Thickener Overflow
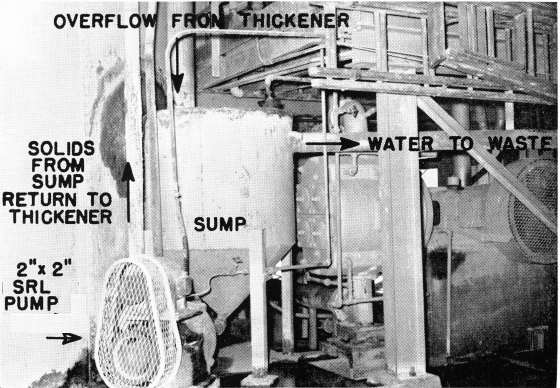
SRL Pump More Than Pays For Itself in Recovery Of Flotation Concentrate From Thickener Overflow Problem: Froth building up on surface of concentrate thickener tends to carry mineral values to waste. Solution: A small combination sump and overflow box was installed at the base of the thickener tank and a 2″ x 2″ SRL Pump […]
CONTROL DENSITY OF THICKENER DISCHARGE
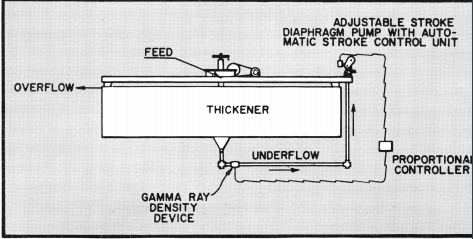
DIAPHRAGM PUMP WITH AUTOMATIC STROKE ADJUSTMENT ACCURATELY CONTROLS DENSITY OF THICKENER DISCHARGEĀ is through his aggressive leadership of our Research and Development Department that many new and improved machines have been developed. Exacting control of thickener underflow density is a critical point in many operations. Normally it is desirable to maintain the highest possible underflow density […]
SAMPLING THICKENER PULP AT VARYING LEVELS
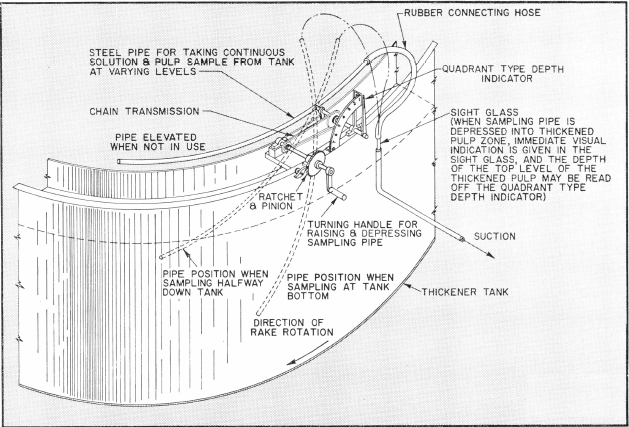
An important potash producer in Europe uses this simple, useful unit for sampling the pulp in their thickeners. It is particularly applicable to any potash operation and its low cost will appeal to many other plants where thickener density must be sampled. The unit is operated manually and the depth from which the sample is […]
Rotary Silica Sponge Filter
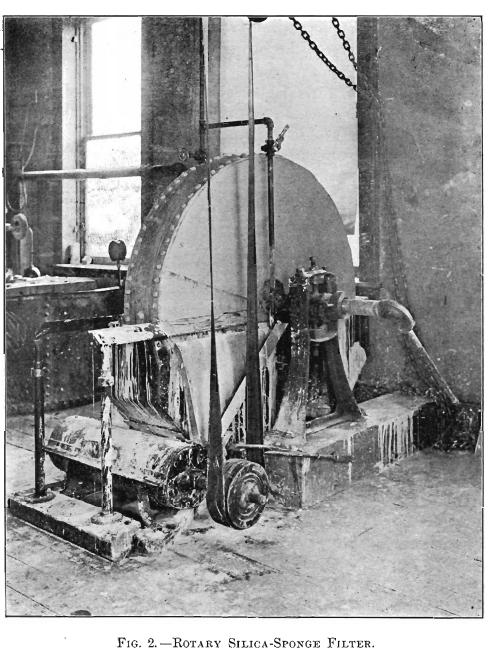
Deslimer
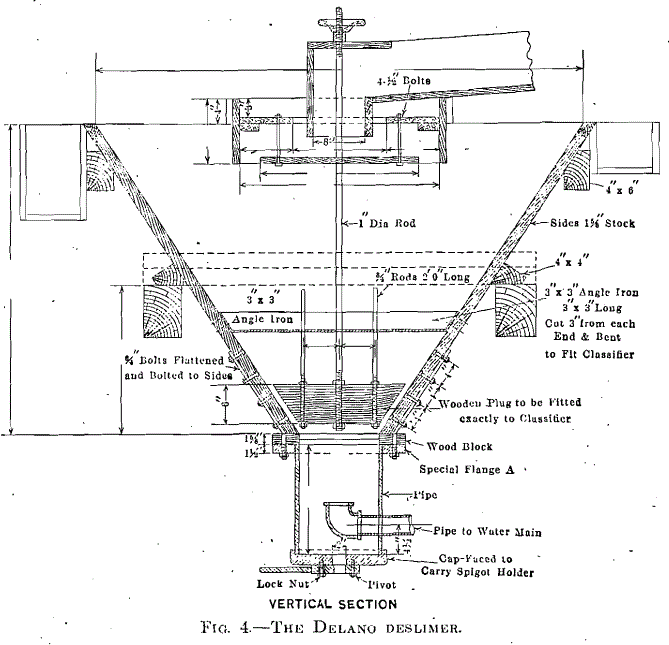
The deslimer is provided with a central feed box, having a baffled bottom to break the velocity of the inflowing pulp. The bottom, or discharge chamber, has a clear-water inlet, which directs, the flow upward along the axis of the deslimer. The spigot is inserted in a movable holder, attached to the bottom of the […]