Grinding Mill Surging

The phenomenon of “surging” in a mill is a subject upon which very little has been written; presumably because it is a condition which cannot be tolerated in mill operation and which must be eliminated by variation of some or many of the physical dimensions or characteristics of the mill or mill charge. The phenomenon known […]
Effect of Grinding Media on Milling

In the previous chapter the influence of the various physical quantities defining the mill and mill charge has been studied in connection with the performance of a mill as a device for the creation of new surface in the powder. For some purposes, however, it is also desirable that the product should have a preferred […]
Grinding Mill Power

The power required to drive a tumbling mill is of interest both to the designer and to the mill operator: to the former as a basis of design for the determination of the necessary size of the elements of the machine; and to the latter because all other factors being equal, the most economical machine is […]
Ball Mills
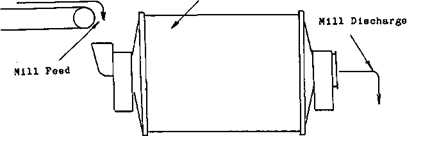
In all ore dressing and milling Operations, including flotation, cyanidation, gravity concentration, and amalgamation, the Working Principle is to crush and grind, often with rod mill or ball mill, the ore in order to liberate the minerals. In the chemical and process industries, grinding is an important step in preparing raw materials for subsequent treatment. […]
How Much do Steel Grinding Balls Weigh

Grinding Media and Liner Wear Rate

The cost of replacement of the metal worn from the working surfaces of the balls and liners of a mill often represents a considerable fraction of the cost of operation of the plant and so is of some real economical importance. In spite of this importance, however, the amount of information in available on this subject […]
Grinding Process
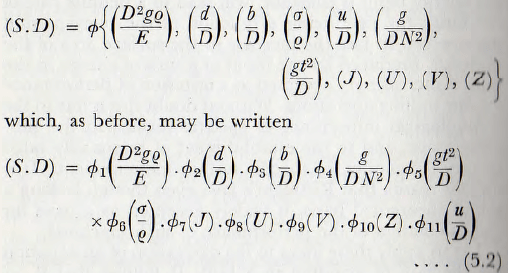
In the previous chapter, the various “laws” of comminution which have been propounded have been studied in relation to the physical process of size reduction and to the available results of experiments into the fracture of homogeneous and heterogeneous materials by impact and by slow compression. In this study it is seen that no satisfactory […]
Comminution
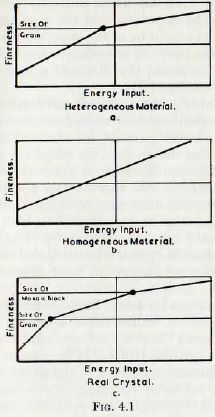
The problems associated with comminution of solid bodies in numerous and complex. In spite of the large amount of investigation which has been undertaken, the present state of knowledge is such that there is no theory by means of which the behaviour during fracture of even a single particle under the simplest possible mode of loading can […]
Grinding Media Charge Motion inside Mill
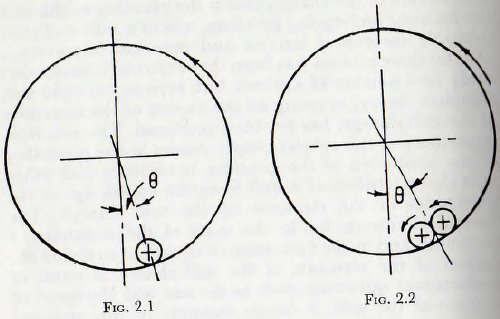
The motion of the charge, that is the grinding media and the material undergoing grinding, within a mill is of considerable theoretical interest and practical importance, and for these reasons, has been the subject of considerable study by a number of workers, but, even so, no rigid and complete theory, covering all the aspects of […]
Grinding Mills – Common Types
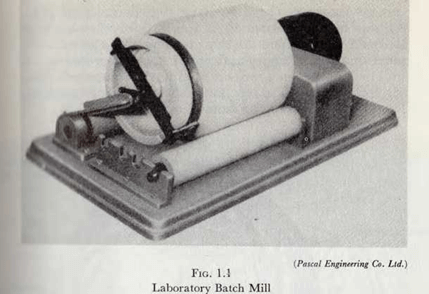
In many industries the final product, or the raw material at some stage of the manufacturing process, is in powdered form and in consequence the rapid and cheap preparation of powdered materials is a matter of considerable economic importance. In some cases the powdered material may be prepared directly; for example by precipitation from solution, a […]