Closed Circuit Grinding VS Open Circuit Grinding

The simplest grinding circuit consists of a ball or rod mill in closed circuit with a classifier; the flow sheet is shown in Fig. 25 and the actual layout in Fig. 9. This single-stage circuit is chiefly employed for coarse grinding when a product finer than 65 mesh is not required, but it can be […]
Small Ball Mills

A PULP level sufficiently high to interpose a bed of pulp, partly to cushion the impact of the balls, permits a maximum crushing effect with a minimum wear of steel. The pulp level of these Small Ball Mills can be varied from discharging at the periphery to discharging at a point about halfway between the trunnion and […]
Ball Mill & Rod Mill Design
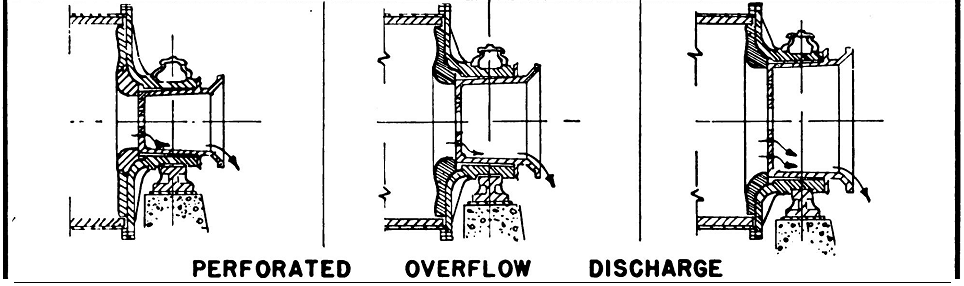
In all ore dressing and milling processes, including flotation, cyanidation, gravity concentration, and amalgamation, it is necessary to crush and grind, often with rob mill & ball mills, the ore in order to liberate the minerals. In the chemical and process industries, grinding is an important step in preparing raw materials for subsequent treatment. In present day […]
Single & Double Stage Grinding Circuits

The comparison between single stage and double stage grinding has received much attention in the past few years. In order to submit information for use of mill operators, we have prepared comparative flowsheets for 50 Ton, 100 Ton, 200 Ton, 350 Ton and 550 Ton/24 hour plants, showing both single and two-stage grinding in typical […]
Flash Flotation with Closed Circuit Grinding
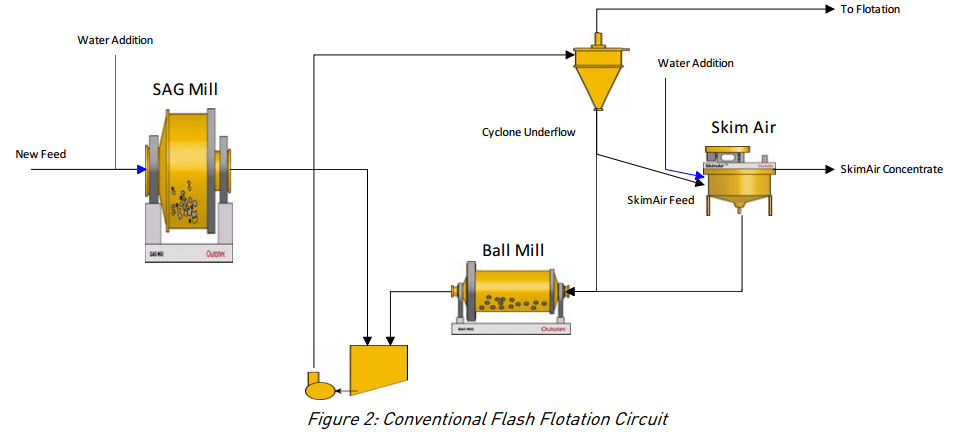
The reason why you need Flash Flotation in a Closed Grinding Circuit relates to “Recovering your mineral as soon as free” which has long been recognized in ore dressing practice. This not only applies to gravity treatment but also to flotation. For this application the Flash Flotation Cell was developed for use in the grinding circuit and […]
What is the Weight of a Steel Grinding Ball

Typical Ball Mill Charge Levels

Here is a table that approximates how much steel charge, or how many tonnes to steel balls are needed to obtain a given type of grind in a specific size mill. The table assumes you are running the mill at 50% charge.
Large Ball Mill

Ball Mill Drawing
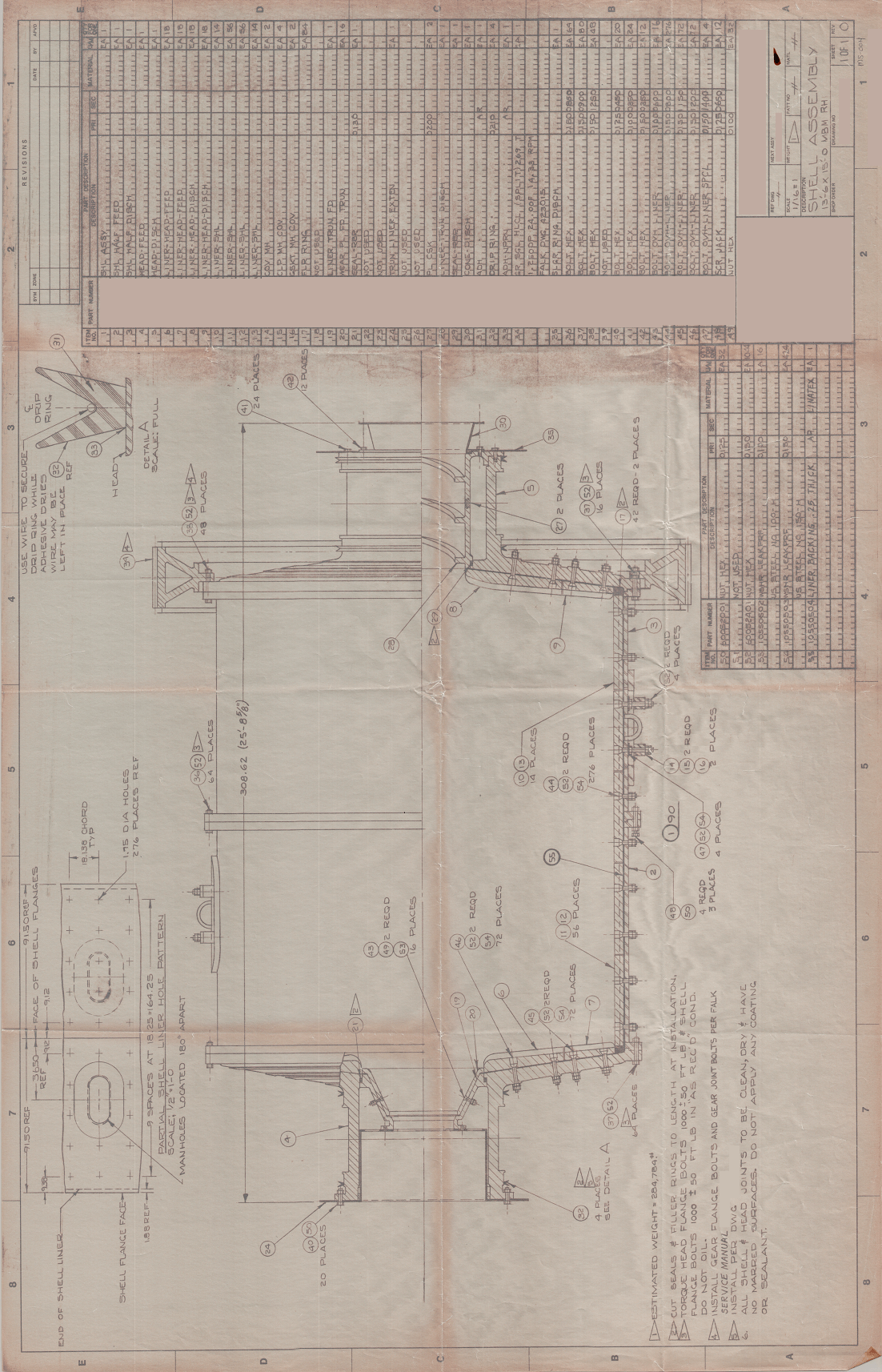
Ball Mill Crushing

Until the advent of the porphyry coppers and the introduction of flotation which soon followed, crushing and grinding for many years proceeded along somewhat stereotyped lines, without important alteration in type of machinery. For the finer crushing and grinding, stamps, rolls, and various patterns of Huntington and Chilean mills were in general use. Ball mills […]