Mill Liner Handler

SAG Mill Liner Design
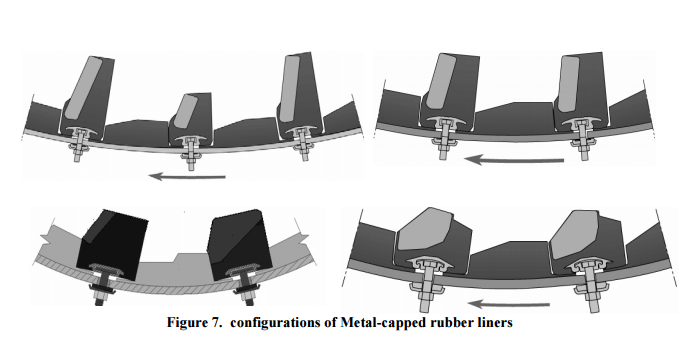
To a more significant degree than in other comminution devices, SAG Mill Liner Design and Configuration can have a substantial effect mill performance. In general terms, lifter spacing and angle, grate open area and aperture size, and pulp lifter design and capacity must be considered. Each of these topics has had a considerable amount of research, […]
SAG Mill Grinding Circuit Design
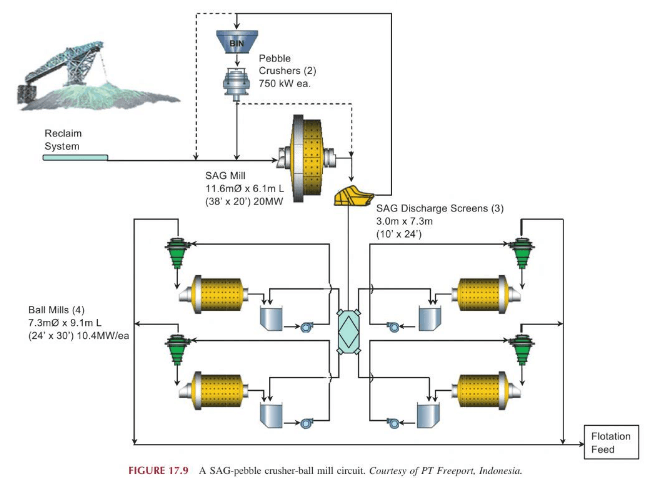
AG and SAG mills are now the primary unit operation for the majority of large grinding circuits, and form the basis for a variety of circuit configurations. SAG circuits are common in the industry based on: High single-line capacities (leading to capital efficiency) The ability to mill a broad range of ore types in various […]
Ball Mill Liner Design

There are many different designs and styles of ball mill liners. As with grinding balls local economics and ultimately operating costs determine the best design and material to use. The initial set of liners is rarely the final design selected. Based upon individual experience, mill superintendents develop preferences for liner designs. The following is given […]
Gibson Roll Ball Mill

CRUSH, GRIND and CLASSIFY in a single pass! YOU Will save time, money and labor with the Gibson combination Elliptic Roll and Ball Mill.• It is the first successful mill put on the market that will take the mine run of ore. Crush grind and classify in a single pass. • Horsepower consumption over one […]
Estimated/Approximate Steel Liner Wear Life/Rate
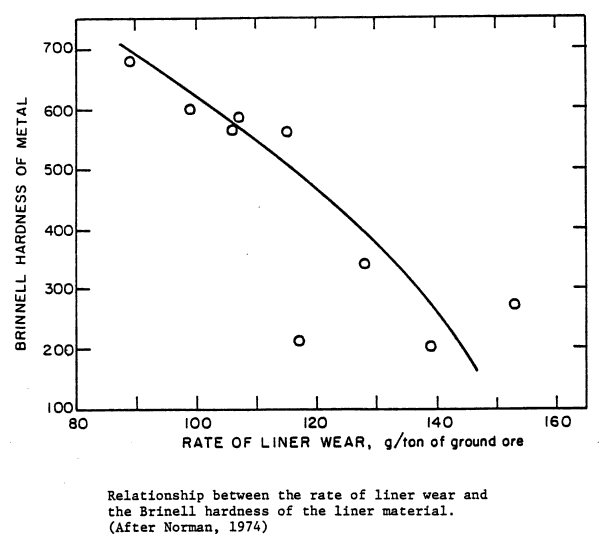
A mill’ steel liner wear rate and total useful operating life is a function of its hardness (mostly). Here is a chart displaying Liner Hardness on the Brinell Scale as a function of the tonnage of ore/rock milled/processed. Not showed here is the impact a mill’s RPM has on the liner’s wear rate. Comminution and Energy Consumption: By […]
Estimated/Approximate Rubber Liner Wear Life/Rate Cost
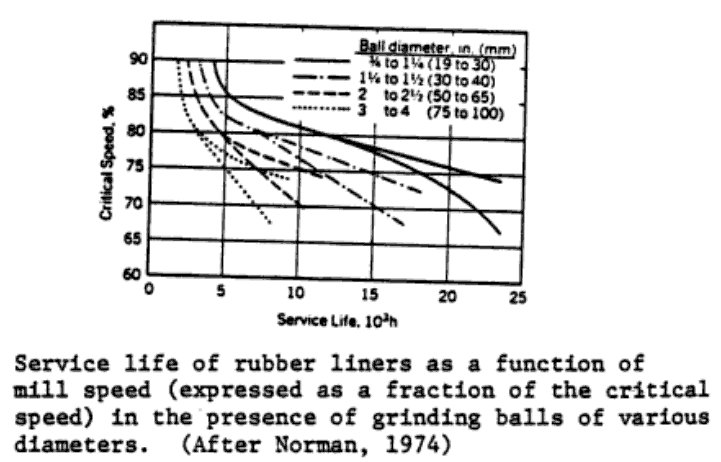
In a Ball Mill (particularly) the wear rate or wear life of Rubber depends much on the Ball Size/Diameter used in that mill. The grinding media size which itself is much of a function of the ore/material P80 feed size into that mill. The other primary and addition factor contributing to a mill rubber liner […]
How a Grate Discharge Ball Mill Works
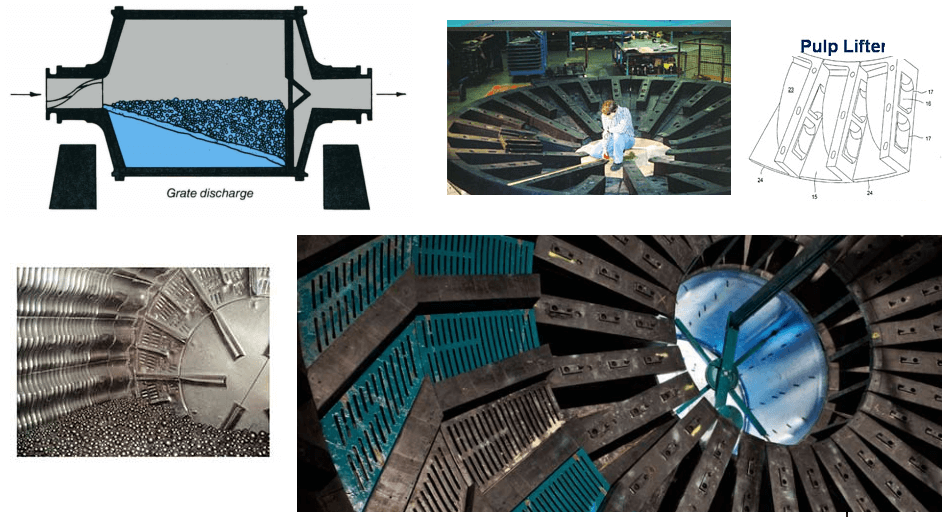
Here I try to explain how ground slurry is discharged from a grate ball mill (or SAG). How it works is, the slurry flows across the grate as it would a screen panel. On the other side of the grate/screens are veins like a pump impeller. As the mill turns/rotates the slurry is “pumped” out […]
Grinding Mill Liners

There are basically two groups of Grinding Mill Liners. Ones with a HIGH PROFILE and those with a LOW PROFILE. The high profile liner is designed to give the media the higher lift. This type will be used in mills that are designed for primary grinding and as a result require the impact of the […]
Rod Mill Liners
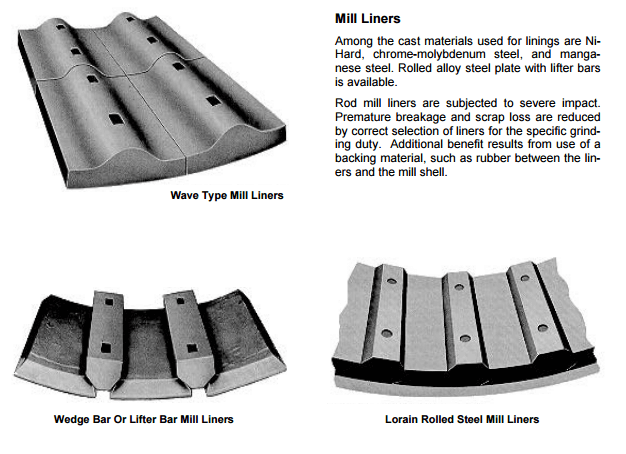
Among the cast materials used for linings are Ni-Hard. chrome-molybdenum steel, and manganese steel. Rolled alloy steel plate with lifter bars is available Rod mill liners are subjected to severe impact. Premature breakage and scrap loss are reduced by correct selection of liners for the specific gnnd-mg duty. Additional benefit results from use of a backing […]