Table of Contents
The object of this Concentrate Marketing post is to draw attention to the benefits of modern milling practice, thus enabling the miner and mill operator to plan their operations so as to net the highest commercial return. By making such products as will be in demand, they may thus take advantage of conditions existing in the various smelters where the concentrates must be sold.
As the science of ore dressing advances, the flotation process assumes its rightful position as the most important. The progress made during the past decade has been due to intensive research resulting in the development of better reagents and the marked improvement in flotation machinery.
Flotation, though primarily used in the recovery of copper, lead, zinc, gold, and silver minerals, is also being applied to many non-metallics such as coal, sand, potash salts, talc, etc., as well as to ores of the less common metals such as molybdenum, nickel, antimony and mercury. The products of such operations are nearly always used or further processed in the same plant in which they are produced and, therefore, present no problem in the marketing of concentrates as such. When concentrates of the less common ores must be sold, it is necessary to make special contracts with the comparatively few buyers who are in the market for such products.
These 1955 numbers can be indexed by multiplying by 8-10X t obtain 2016 values.
GOLD & SILVER Marketing
It is well understood that the production of gold and silver in the form of bullion, or as cyanide precipitates, is ordinarily more profitable than the sale of even a rich flotation concentrate. The United States Mint will accept bullion containing 20% or more of gold and silver combined, while in Canada the minimum is 50%. Refining charges are only a few cents per ounce. Similar conditions prevail in other countries. Cyanidation and amalgamation of both crude ore and concentrates have long been used to advantage, and during recent years, the Mineral Jig followed by amalgamation of the concentrates, preferably in an amalgam barrel, has, increased the recovery in the form of profitable amalgam in many plants. This modern modification of amalgamating practice can be profitably applied to most gold ores, whether the subsequent treatment be flotation or cyanidation.
On the other hand, some ores are not amenable to these processes alone, and in order to obtain the best commercial return, it is often profitable to market a concentrate containing a portion of the precious metals, which is not directly recoverable as bullion. Moreover, in view of the present value of gold and silver, several important producers of these metals are investigating the possibilities of flotation to recover values not now being extracted by mercury or cyanide, and thus improve the overall recovery. Although in a few cases a highly siliceous concentrate containing gold and silver is shipped to a smelter, such a product can usually be further treated in the mill by cyanidation or other methods. Barrel amalgamation preceded by fine grinding in the same unit will usually recover the major part of this gold and silver. Concentrates containing little or no lead, copper, or zinc, sometimes carry sufficient gold and silver to be valuable. Such products usually consist principally of iron sulphides and may be classified as iron concentrates.
BASE METAL CONCENTRATE Marketing
In addition to iron, the important concentrates normally shipped to smelting plants are those of lead, copper, and zinc, so these four are the principal ones in which the average producer is interested. In treating ores of these base metals, containing gold and silver, the ore in the mine is the raw material and the refined bars of gold, silver, lead, copper, and zinc are the finished product, as far as the metallurgist is concerned. The process of selection and separation begins underground, continues in the mill, is further carried on in the smelter, and finished in the refinery, so the milling operation is but one step in the whole process.
It may be stated as a general proposition that the smelting process is more efficient than milling and the ores could be smelted without milling, but as smelting is also much more costly, only high grade ores permit direct smelting and to enrich the lower grade ores, milling methods were introduced. This is one of the two important reasons for the establishment of the flotation plants; the other is transportation. Since few mines are located very near the smelter, it is necessary to concentrate the values into as small a bulk as is consistent with good recovery in order to reduce to a minimum the cost of delivery to the market and of the subsequent treatment processes required. Milling not only increases the grade of the products to be marketed, but may be used to separate one type of mineral from another as illustrated by selective flotation applied to lead-zinc ores.
MILLING
In the development of any mine, the metallurgical processes are of prime importance. As soon as sufficient ore is developed to justify even a small mill, the matter should receive careful consideration. Consider a hypothetical case which is typical of many situations. Assume that the gross value of an ore is $20.00 per ton; mining and development cost $5.00; marketing cost including freight, treatment, and smelter deductions $13.00; interest and amortization on plant investment $1.00—therefore, net profit per ton is $1.00. If a mill is built at a cost even double that of the investment in the mining plant, making a 90% recovery and a concentration ratio of ten into one, the picture would be about as follows:
Gross Value…………………………………………………………………………………$200
Mining and Development………………………………..$50
Milling………………………………………………………….$20
Marketing Cost……………………………………………….$13
Loss in Milling Tailings…………………………………….$20
Interest and Amortization…………………………………$30
Total……………………………………………………………….$130 $130
Net Profit per ton……………………………………………………………………………$ 67
Another phase of the question is illustrated by the case of a mine which is shipping about one hundred tons of gold- silver-lead-zinc ore per day to a custom mill. While the milling charges are reasonable, the custom plant cannot rearrange its flowsheet for this particular ore, and does not recover the zinc. At present market prices the net returns from the mill, after paying transportation, treatment charges, and royalty, are about $150 per ton.
Recoveries and concentration ratios, based on exhaustive laboratory tests on this ore, indicate that net smelter returns from concentrates produced in a selective flotation mill on the property, especially designed to treat this ore, would amount to $17.25 per ton of heads. This is the net return after allowing the conservative charge of $15 per ton for milling cost, and deducting the transportation and smelter charges on the concentrates, and the royalty. This saving or added profit of approximately $22 per ton or $225.00 per day is due to three factors:
- Better all around results in a mill designed and operated for treating a specific ore.
- The milling profit now being made by the custom plant.
- The production of a marketable zinc concentrate.
We may conservatively estimate and confidently predict that the saving would pay for the plant in less than one year.
There are many instances of which the above examples are typical; yet it must be realized that the cost of milling will vary greatly, depending upon the tonnage treated. However, even a small mill of ten to fifteen tons per day can be operated profitably as has been proven many times, when standard methods and machinery are used. The profit per ton from a small mill will naturally be less than that from a large one, but in addition to the profit earned, the small plant will also determine the correct metallurgy for the larger operation.
GROSS VALUE OF CONCENTRATE
The term “gross value” refers to the total value of all marketable metals contained in an ore when priced on the basis of refined bars delivered at some standard market. It is perhaps unfortunate that many custom assayers follow the method of translating metallic contents into gross values in dollars and cents. While this custom is not misrepresentation, it is nevertheless misleading to the uninformed. The farmer who raises sugar beets well realizes that his marketable product is not finished and still must be processed before it is salable to the general public. If sugar is five cents a pound and the beets contain 15% sugar, he will not receive $150 a ton for them. Yet he endeavors to produce as many tons with as high a sugar content as possible. The manufacturer of any commodity strives not only to keep down costs and keep up production, but to present to his market the kind of commodity which that market will buy at the best price. Likewise, it behooves the mill operator to be familiar with the market upon which he must sell, and to keep himself informed not only of price changes, but of varying local conditions which may affect that market. Frequently, it becomes advisable to alter plant practice and flowsheets. It is for this reason that we have always strongly advocated flexibility in mill design and operation, together with the use of standard proven equipment.
SMELTER Treatment Charges & Penalties
It is not our intention to publish any specific smelter schedules for several reasons; first, these vary in different localities although they are all based on similar principles. In some markets, such as the Joplin district where lead and zinc concentrates contain no precious metals and vary but little in character, the procedure has been greatly simplified. Such cases, however, are the exception, not the rule. Second, schedules at the same plant vary from time to time, not only on account of prices, but with the varying needs of the plant for different classes of material. Third, a steady producer can always secure a better rate than that offered to the spasmodic operator, because the buyer obtains a distinct advantage in being able to plan operations in advance. Nevertheless, the reasons behind the various clauses in the contracts offered by the purchaser are important to the seller.
The following examples illustrate typical provisions of smelter schedules. They do not represent any definite settlement data, but are what might be called synthetic schedules which show approximately the payments and charges usually made. If the shipper is in a position to furnish a definite minimum tonnage, arrangements should always be made with the buyer on that basis, as better rates will be obtained. In order to offer a contract, the smelter must know the complete details with reference to the assay and analysis of the concentrate and it is best to submit a sample.
General Provisions:
Delivery: Shipments are paid for f.o.b. smelter. Freight charges must be paid or guaranteed by shipper and if not paid in advance, will be deducted from smelter settlement.
Taxes: Any government taxes are paid by shipper.
Moisture: Actual moisture will be deducted with the understanding that the minimum deduction is 1%.
Weighing and Sampling: To be done by the buyer in presence of seller’s representative—standard methods to be used. After sampling, all but the plate reject may be disposed of as buyer sees fit.
Settlement: In the event that buyer’s and seller’s assays do not check within the limits stipulated in the contract, an assay shall be made by a third party selected from a list of umpire assayers previously agreed upon. If the umpire exactly checks either previous result, the assay not checking will be disregarded. When three different results are obtained, the one between the other two will govern.
Sacks: $1.00 per dry ton will be charged for concentrates delivered in sacks.
Small Lots: A sampling charge of $75 will be made for each lot of less than ten tons dry weight.
Weights: All calculations are based on dry weights. A ton is 2,000 avoirdupois pounds. An ounce of gold or silver is a troy ounce. A unit is one percent of a ton or 20 pounds. (In Mexico and other countries using the metric system, a ton is 1000 kilograms, while gold and silver are reported in grams. A unit is then, of course, 1% of 1000 Kgs. or 10 Kgs.)
Weight Units: The grain is the basis of avoirdupois, troy and apothecaries weights, and this unit is the same in all three systems.
1 pound (lb.) Avoirdupois = 7000 grains (gr.)
1 pound (lb.) Apothecaries = 5760 grains (gr.)
1 pound (lb.) Troy (12 oz.) = 5760 grains (gr.)
1 kilogram = 15432 grains (gr.)
1 grain = 64.8 milligrams (metric)
Ore and base metals are weighed in Avoirdupois long or short tons or in metric tons. 1 metric ton = 1000 kilograms. 1 long ton = 2240 pounds. 1 short ton = 2000 pounds.
Precious metals are weighed by metric or troy weights. The common weights in the metric system are the following:
1 metric ton = 1000 kilograms (kgs.)
1 kilogram = 1000 grams (g.)
1 gram = 1000 milligrams (mg.)
1 metric ton = 2204 pounds = 1.102 short tons (Avdp.)
1 kilogram = 2.204 lbs. (Avdp.) = 32.15 oz. Troy
1 gram = .03215 ounce Troy
In the Troy system of weights:
24 grains = 1 pennyweight (dwt.)
20 dwt. = 1 oz. =1.0971 oz. Avoirdupois = 31.1035 grams
12 oz. = 1 lb. = .8229 lb. Avoirdupois = 373.24 grams
With gold worth $1200 per Troy ounce:
1 gram (metric) = 40
In England, one ounce of gold is worth approximately 12½ pounds.
U. S. Metal Prices: Gold payments are based on realized mint price of $1200 per troy ounce.
Silver payments are based on realized mint price provided affidavit is furnished to qualify silver for U. S. government purchase, or, if seller elects, prices can be based on Handy & Harmon, N. Y., silver quotations for week during which last car of lot arrives.
Zinc payments are based on East St. Louis price for Prime Western Zinc quotations in Engineering and Mining Journal averaged for the week.
Lead payments are based on N. Y. quotation for desilverized lead.
Copper payments are based on Engineering and Mining Journal quotation for electrolytic cathodes averaged for the week.
What to do why CONCENTRATES
Before investigating further those provisions of smelter contracts which refer to assays and analyses, let us consider the handling, transportation and sampling of concentrate shipments. A good mill is always a clean mill and this applies especially to the section in which the concentrates are handled, on account of the high grade of the products. Due care should be taken to prevent washing or blowing away of the enriched products. In small plants settling boxes are often employed instead of vacuum filters and the values lost in the overflow are often found upon investigation to be surprisingly high.
Drying:
The drying of the concentrates should also receive careful study, and no concentrates should ever be so dry that there is danger of loss in transit from dusting. The finer the concentrate the more water must be left in it to prevent this. It is much better to pay freight on a little water than to lose valuable concentrate in the form of fine dust. On the other hand, if the cost of drying is not too great, a saving can be made by removing unnecessary moisture. Moderate drying also facilitates sampling at the smelter, so that mill and smelter assays are easier to check. Concentrates as discharged from the filter usually contain from 10 to 15% moisture. About half of this water can be removed without danger of dusting, thus making an ideal shipping product. This can be done in any drier, but the rotating type using steam or hot air is best. Unusually wet concentrates may be penalized at the smelter on account of difficulties in handling, especially in freezing weather.
When concentrates are absolutely dry, there is always a dusting loss at the smelter, and for this reason a minimum moisture deduction of 1% is applied. It is, therefore, evident that when concentrates contain less than 1% of water, part of the deduction will be actual values, which is excellent reason for not carrying the drying process too far.
Sacking:
If concentrates must be handled by pack animals or airplane, it is necessary to ship in sacks. Rich concentrates should always be packed in double sacks, even though the smelter makes a small additional charge for the extra cost of handling sacked material. The usual method of packing is to put a closely woven canvas sack inside of a heavy gunnysack. Some shippers in order to reduce spillage and dusting to a minimum use an inside sack of heavy paper. Cloth sacks are always returnable to the shipper. If concentrates are shipped in bulk, either in railroad cars or trucks, care must be taken to see that all cracks in floors and sides are tightly sealed by means of suitable lining. Shipments in trucks should also be covered.
Freight Rates:
When shipments are made by rail, the freight charges per ton increase with the value, and the rate is based on the value per wet ton, which is determined by dividing the total value of the carload by the wet weight in tons. As railroad calculations are not infallible, it is advisable to check freight charges to see that dry ton values are not applied to freight bills.
Weighing:
Shippers to custom plants are entitled to watch the weighing and sampling of shipments, or to appoint a representative for that purpose. It is the duty of such representative to see the weighing of cars and trucks, both gross and tare, to make sure that tare weight is taken within a reasonable time and to insist that cars are properly cleaned.
Sampling:
The moisture sample is always taken at the time the car is weighed. Samples for assay pulps may be taken later. Pipe samples are usually satisfactory for carload shipments that are too wet or too tightly packed to be properly mixed by shoveling. The sample is then cut down by standard methods of coning and quartering and splitting. Since the smelter is as vitally interested in obtaining an accurate sample as is the shipper, great care is exercised and methods are constantly studied and checked so that no mistake will be made.
Since smelter charges are based upon tons treated and almost as much work is required to sample a small lot as a large one, a sampling charge for small lots is customary However, there should be no such charge for shipments from the average mill, except in case of special high grade products, when the added cost is insignificant compared to the value.
From one to four samples may be taken from a lot for checking purposes, but in the majority of cases, there will be an original and a duplicate. It is customary to retain the rejects from samples until the lot is liquidated, so that a resample may be taken if required. The final pulp consisting of a few pounds from each sample is carefully dried at a temperature slightly above the boiling point of water, all screened through a fine screen, commonly 100 mesh, and divided into four portions, one for the buyer, one for the seller, one for umpire and the fourth as a reserve to replace possible loss of any of the first three. The shipper’s pulp is delivered to his representative for independent assay and analysis. Results are compared with those obtained by the smelter, and if reasonably close, settlement is made according to the contract. If results do not check, the pulp reserved for the purpose is sent to an umpire assayer. When the three results are obtained, it is customary to settle on the result between the other two or on the one the umpire may check exactly. Should there be discrepancies not remedied by repeating the assays or if the original and duplicate samples are far apart, the lot is resampled.
Metallics:
Concentrates are obviously more homogeneous mixtures than crude ore and, therefore, easier to sample accurately, provided that they contain no metallics too coarse to pass the screen used in preparing the pulp. The smelters are not at all enthusiastic about receiving lots containing appreciable amounts of metallics on account of the difficulty of obtaining accurate samples and the shipper is at an even greater disadvantage for two reasons:
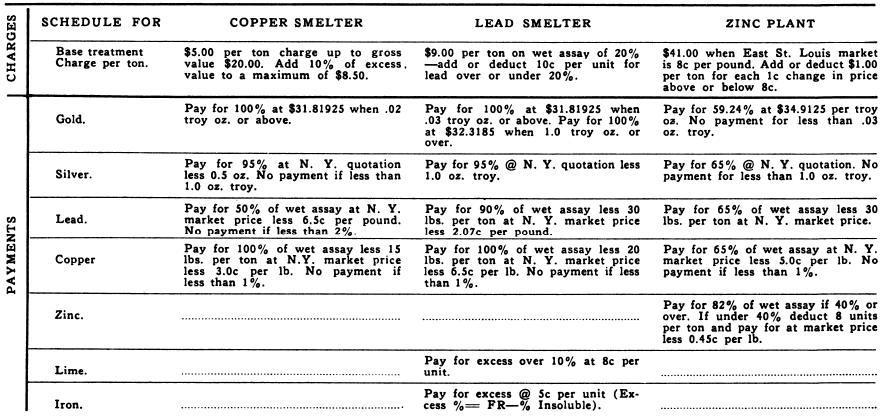
First, it is impossible to split the metallics equally between the four pulp samples, so there is no opportunity for a check assay; and second, the loss in handling of even a few particles of gold will make an appreciable difference in the liquidation.
In the early days of such camps as Leadville and Cobalt, large amounts of native silver were mined and shipped to smelters, but today gold metallics are more important, so the operator will profit by removing them from the concentrate by amalgamation. This results in not only getting a better sample, but also obtaining a better price for gold. There is the added advantage of being able to market the gold promptly, thus avoiding the tie-up of operating capital in concentrates or in various places in the plant, from which it may or may not be eventually recovered. The Amalgam Barrel and Amalgam Separator are now performing this duty efficiently in many mills. The Mineral Jig, located in the ball mill-classifier circuit, removes the metallics in the form of a high grade hutch product which is subsequently treated by amalgamation.
SMELTING BUSINESS
Like any business institution, every smelter is in business to make a profit. It is confronted with the same problems of overhead, insurance, taxes, obsolescence, etc. The item of interest on investment and stock is greater than in the average operation of the same magnitude on account of the high values of the raw material ordinarily in stock. Likewise, the amortization charge is large because the life of the plant is limited by the life of the mines tributary to it. Nevertheless, in order to stay in business, a smelter must give the best service possible to the shippers, and arrange its schedules to attract the maximum quantities of ore and concentrates which can be treated profitably.
The basis of payments is the gross value of the metals which can be extracted and refined, and in addition to a base treatment charge of so much a ton, deductions are made from the gross values to cover the costs. The base treatment charge is the approximate cost of handling and smelting one ton of ore. This charge should theoretically include the smelter’s profit, but rarely does include more than a small part of the legitimate profit to which it is entitled. Deduction from gross values take many different forms but may be roughly classified as follows:
- Percentage deductions, which cover the losses by spillage, dust, slag, and re-treatment of by-products.
- Deductions per pound or ounce to cover the cost of refining and transportation. These deductions include the cost of separating the gold and silver from the lead bullion or blister copper to produce bars of refined metals, as well as the cost of shipment from the smelter to the market where the metals are priced. Also when a metal such as lead at a copper smelter or copper at a lead smelter is recovered in the form of a by-product, deductions are made to pay for the additional processing required.
- Minimum deductions, for the purpose of protecting against losses in slag which the ore will form, thus carrying out some values contained in the other ores with which it is smelted, and which otherwise would not be lost.
Most of the smelter’s profit is included in the percentage deductions, which places a premium on efficient metallurgy. In other words, if the metallurgy is bad, the profit vanishes; if good, the profit is earned. The success of any smelter depends greatly upon its staff of metallurgists, and most important, upon its honest and diplomatic management. The penalties and premiums for constituents of an ore or concentrate which are not actually finally recovered as metal are calculated according to their beneficial or detrimental effect upon the smelting and refining processes. These are computed as modifications of the base treatment charge.
ZINC CONCENTRATE MARKETING
As previously stated, zinc, iron, copper and lead concentrate are the ones in which the mill operator is interested. Consider first zinc which is a special case, in fact technically there is no such thing as a zinc “smelter”. Zinc distillery would be a better term, because the zinc is distilled and condensed, and is the only metal recovered in the plant. Other values, if present, remain in the residue and have not been benefited by the treatment except insofar as the removal of most of the zinc makes them more amenable to further treatment. Base charges for zinc concentrates are very high, comparatively speaking, on account of the cost of the process, particularly the item of fuel, which is usually gas. In fact, zinc smelters are ordinarily built near the gas supply, because it is cheaper to transport the ore than the fuel.
Moreover, recovery by this process is not so high as in lead or copper plants, and the percentage deduction is therefore greater. It is also easily understood that on account of the fuel cost and lower percentage of recovery, low grade material cannot be profitably treated. Gold, silver, lead and copper, if present, will be paid for; but the percentage deductions from their market values are greater. Notwithstanding the distillation operation, the percentage of zinc remaining in the residue is always higher than desirable for subsequent smelting and the residue must be shipped to a lead or copper smelter for treatment, hence the lower payments for gold, silver, lead and copper. The electrolytic process for zinc is quite different, but involves a large capital output, low electric power cost and also a most competent metallurgical staff. Costs and other factors which affect schedules are comparable, so detailed discussion of this method would be superfluous.
IRON CONCENTRATE MARKETING
Iron sulphide concentrates may be shipped to either a copper or lead plant, but the transportation cost is usually the deciding factor. Base treatment charges are approximately the same. At lead plants, the iron present in excess of silica is desirable for mixing with siliceous ores, but the premium for iron is offset by roasting charges, so there is but little difference in net returns from the two classes of smelters.
Whether or not to produce an iron concentrate at all is a question that warrants careful study. In some mills it has been found that the production of iron concentrates following other flotation circuits, such as lead and zinc, is profitable at higher gold prices, while formerly such a product would not pay expenses. On the other hand, at some plants it is better to float a richer concentrate containing copper or iron sulphides or both, and allow a part of the iron to go into the tailings, although it could be floated, thus discarding that part of the sulphide which would not pay its own way to and through the smelter. Both of these profitable alterations in flowsheets have been accomplished using Flotation Machines with selective flotation methods.
COLLECTORS FOR GOLD AND SILVER
The recovery of precious metals in base metal smelters is accomplished by means of a collector, either lead or copper. In the lead blast furnace the particles of molten lead absorb the gold and silver as they settle through the melting mass, so the precious metals will be found in the base bullion produced, and will later be separated at the refinery. In copper smelting, the furnace product is matte, a chemical combination of sulphur, iron and copper, which although not as heavy as lead bullion, is still heavier than the slag and collects the gold and silver in the same manner. The matte is subsequently treated in convertors by a strong air blast to burn off the sulphur and with the addition of siliceous flux, to slag the iron. The resultant product is impure metallic copper, containing gold and silver, which is known as blister copper. This is cast into anodes for the electrolytic refinery.
COPPER SMELTER
The schedules offered by lead and copper smelters will be more easily understood by first explaining the principal differences between them and then discussing the lead smelter schedules in more detail. Modern copper smelting is performed in reverberatory furnaces, while lead smelting is accomplished in blast furnaces. As the reverberatory is an oxidizing unit, much of the sulphur is eliminated during the operation, so there is normally no roasting charge, although some plants penalize fine material. Production of matte permits the use of much more siliceous slags than the production of lead bullion, that is to say, a highly siliceous slag cannot be as thoroughly cleaned of lead or as easily controlled in the blast furnace; therefore, the copper smelter has a much greater range available in the balance between silica and principal bases which are iron and lime. Hence there are no adjustments made for iron or silica at the average copper smelter, although there are exceptions. Abnormal flux balances may affect the situation; in fact, one smelter assesses a small penalty for iron and another penalizes silica in excess of 35%. The higher gold price has encouraged the production of siliceous ores, thus creating a demand for iron and favoring the concentrate producer. Better copper prices resulting in more concentrates will tend to readjust the flux balance.
Copper plants pay more for copper than lead plants for the simple reason that copper as recovered in the latter is in the form of low-grade matte carrying some lead, a by-product requiring additional roasting, a second smelting step and transportation to the copper smelter before it is ready for the convertor. On the other hand, many copper plants make no payment whatever for lead, as the lead is driven off as fume. Plants having accessory equipment for recovery of the fume, make only small payments because the lead that is saved is in a form that is very expensive to re-treat and also contains large quantities of undesirable impurities such as arsenic. It is, therefore, obvious that when transportation facilities permit, both a lead and a copper concentrate should be produced, if possible, when treating lead-copper ores. Many ores can be so treated to produce more profits, and the flexibility of the “Sub-A” type makes it especially valuable in such flowsheets. Except for the points noted, the provisions in copper and lead schedules are for the same reasons quite similar, and differ slightly only in degree.
LEAD SMELTER
Some lead smelter schedules are more involved than others. This is partly due to following early customs and partly to the attempt to cover all contingencies. The sampling and handling of shipments and deductions from gross values have already been described. There still remain to be considered the penalties and premiums which respectively increase and decrease the treatment charge. One common provision is the graduated increase in the base charge according to value up to a maximum charge, but this is partially offset by increasing the gold payments within certain limits. The increase in gold payments is logical because the gold is practically all recovered in the smelter. The increase in base charges helps to defray the added interest charges involved. It normally requires about ninety days to process the metals after receipt of the concentrates. When the values exceed those provided for in maximum charges, the smelting company can afford to give the material special routing through the plant.
Concentrate Penalties and Premiums:
The constituents of the concentrates as determined by analysis affect the treatment charge insofar as they influence:
- the preparation of the blast furnace charge;
- the collector;
- the formation of the slag;
- the refining of the base bullion.
SULPHUR
Sulphur is always penalized, although in some schedules applying only to high sulphides the penalty is not shown and is included in the base charge. Direct smelting ores, i. e., ores containing little or no sulphur can be charged directly to the furnace, when not too fine, but sulphides must be roasted so that the furnace will produce bullion instead of matte. A small percentage of sulphur is usually free of penalty and the excess graduated to a maximum of two or three dollars to cover the sintering costs. In many modern plants, the concentrates are sintered twice or even three times to insure maximum sulphur elimination and provide a porous material more suitable for smelting. Formerly it was customary to make a charge for fine material in oxidized ores, but as these fines are now actually beneficial in the sinter charge, the shipper has been relieved of this penalty.
LEAD
Lead is the collector of the precious metals and a minimum of about ten percent is necessary for proper silver recovery. In recent years, the production of lead concentrates increased to the point where the average smelter ceased to be concerned about the percentage of lead on the charge, but greater production of dry ores (ores without lead) due to the higher gold price, altered the situation again. Illustrating the divergent conditions found in the various markets, there is one plant that pays premiums for lead, because the normal ore supply is deficient in that metal, and at the other extreme, another smelter actually penalizes the lead in excess of 50%, because the normal ore supply contains all the lead that can be conveniently treated in the blast furnace.
In the early days of lead smelting, the lead content was determined by fire assay, but the more satisfactory wet method which shows more lead is now used. During the transition period, it became customary to adjust the difference by deducting one to one and a half percent from the wet assay, and although this deduction might be easily absorbed in the other adjustments, the custom is still followed at many plants.
SMELTER SLAG
As already pointed out, the lead smelter must maintain the balance between iron and silica within fairly close limits and as it is necessary to add barren or almost barren iron flux at times in order to maintain this balance, iron commands a premium and silica is penalized. Manganese is considered equivalent to iron, but is rarely present in concentrates. The silica penalty is expressed as insoluble. Since the insoluble determination is less expensive for both the shipper and the smelter, and since the small amount of other elements, principally alumina, which are included in the insoluble are also detrimental, the insoluble is on the whole a perfectly fair basis of settlement. With the increasing production of iron concentrates, there is no assurance that the present situation with respect to iron and silica will last forever, but at present iron, as a rule, still gets a premium and silica a penalty. Lime, being a necessary constituent of the blast furnace charge, also receives a credit at most plants, inasmuch as it replaces a part of the barren limerock that otherwise would be necessary as flux. Lime goes out with the tailings in the production of base metal concentrates and this premium therefore does not apply.
ZINC
Zinc has probably caused the lead metallurgist more grief than any other one element, hence the stiff penalty. When the zinc is completely oxidized, furnace operation can be improved by using more iron, which increases the smelting cost and the slag losses, but zinc in the form of sulphide is much worse. It causes the formation of zinc “mush” of low specific gravity, which cannot be separated from the slag and this mush always absorbs silver. Also zinc sulphide rapidly forms incrustations in the furnace which greatly reduce efficiency. Zinc sulphide is, therefore, the reason for going to extreme in roasting practice in order to convert as much of it as possible to the oxidized form. As zinc in most concentrates is all sulphide, we now find the smelters have reduced the amount of zinc admitted free of penalty to as low as 5% in many instances.
ARSENIC, ANTIMONY, TIN
Arsenic when present in the blast furnace charge is largely volatilized and when condensed, contaminates the dust chamber by-products. Retreatment of the flue dust and fume is expensive, but is a source of salable arsenic in most cases and this tends to offset the added cost of recovering the other values in the dust. Arsenic also tends to form speiss, a by-product usually rich in gold and very difficult to re-treat. Some of the arsenic is always found in the base bullion along with the antimony and tin, which metals react similarly to lead in the furnace. The penalty on these three metals is, therefore, based principally on the added burden on the refinery. They must be removed in the softening furnace and the more of these impurities present in the base bullion, the more fuel will be required, the longer the equipment will be tied up and the more lead-bearing by-products will be formed. The arsenic, antimony and tin can also be removed by means of molten caustic soda, but this process is also expensive, and not extensively used.
BISMUTH
Bismuth goes with the lead throughout the standard smelting and refining process and can only be removed by special methods in the refinery. If sufficient bismuth is present in the lead bullion, the refined metallic bismuth recovered will pay the cost of special treatment, but it is not removed by standard processes and a very small amount contaminates the refined lead to a point where it is not marketable at standard prices. For this reason, most smelters reserve the right to reject any shipment containing appreciable quantities of bismuth.
MANGANESE
MAGNESIUM OXIDE
CADMIUM
Marketing or sale of concentrates is a problem of primary consideration for any potential producer. It is a complex matter that requires thorough study and investigation. Careless assumption in regards to marketing returns has resulted in the failure of many ventures with substantial losses to investors.
The location of a mineral deposit is one of the controlling factors since transportation costs can either limit possible profits or make the operation uneconomical.
The grade and nature of a mineral deposit as to its market potential together with the degree of treatment or beneficiation to meet specific requirements must be clearly established. Usually laboratory test work is necessary to investigate methods of treatment, yield or recovery, grade and other factors. Such test work is essential in the development of estimates as to costs of production, capital needs as well as providing samples which can be submitted to possible market outlets.
The marketing of crude ores or mine run minerals, whether metallic or non-metallic, generally present difficult problems unless the mine is located within economic distance to processors, custom mills or smelters having a demand for the particular ore or mineral. It is usually necessary for the miner or producer to concentrate the mineral either to reduce shipping weight or to bring the mineral to meet specifications as to grade, size or other requirements established by the buyer.
Outlets for metallic minerals or concentrates such as copper, lead, zinc, gold and silver are well established and most producers have a choice of several smelters or possible buyers. Other less common metallic and non-metallic minerals may be more difficult to sell since comparatively fewer buyers are in the market. Separate tabulations are given herein showing both “Major Metals” and “Non-Metallic Minerals” to briefly outline usage, treatment, market requirements and price range during the year 1964. Market requirements and selling prices are often dependent on localized demand. In most cases contracts for sale should be negotiated in advance of production to reduce risk. It is often necessary for the producer to develop a market by selling to a final user or processor.
Many metal mines during development stages, through necessity must either ship crude ore to custom mills or direct to smelters with resultant reduced returns due to transportation costs, high treatment charges and smelter losses. Usually only higher grade ores, those selectively mined or hand cobbed, can be profitably shipped to a smelter. It is generally changing character of the ores being processed. Custom mills may permit a greater return than direct shipment to smelters due to increased grade, separation and reduced weight of products shipped together with a higher rate of payments by smelters.
Since few mines are located near either a custom mill or smelter it is necessary for the miner to arrange for a treatment plant at, or adjacent to, the mine for best returns where ore reserves and grade justify capital outlay. Such a mill should be designed for the specific ore and should be based on results of reliable test work. In this way much of the risk is eliminated and maximum recoveries, high grade concentrates and low operating costs result. Advances in methods of ore dressing has broadened the range of economic recoveries by improved selectivity in mineral separation by flotation and other means thereby reducing losses and assuring improved returns.
It is important to the producer or seller of metallic minerals or concentrates to be familiar with various smelter schedules and smelting processes in order to control the grade and character of products to obtain maximum returns. While certain impurities may be penalized, others may lead to bonus payments being advantageous to smelting process. Lead, zinc and copper smelters each having different smelting practices either give a low return, no payment or a penalty for metals adverse to the particular process. For instance, copper contained in a lead concentrate is paid for at or near the price paid for lead while lead in a copper concentrate will return less than 50% of lead price. Zinc contained in lead or copper concentrates is undesirable and is usually penalized when in excess of minimum amounts allowed by smelters.
Smelting Processes
Smelters have the problem of converting base metal ores and concentrates and precious metal contents to bullion products at a reasonable profit. The smelter buys ores based on current market prices subject to charges to cover handling, sampling, smelting, refining, bullion freight and marketing. Such charges or deductions must of necessity cover smelting losses and profit. Smelter schedules must make allowance for the full cost of smelting to cover labor, fuel, return of capital costs, depreciation, insurance, taxes, plant and other overhead costs. Payments to the seller vary widely due to type of ore being shipped and according to smelting processes employed. Penalties are assessed on ore constituents that affect smelting costs. If the ore treated will not produce a fluid slag, fluxes such as silica, iron or lime must be added and a penalty charge made for such added expense.
High grade concentrates from jigs, concentrating tables, or other recovery methods and those containing metallics as native gold or silver should be sold separately from lower grade products for best returns. It is possible that actual values may not be fully reflected in final sampling due to segregation or inadequate mixing or blending. It is usually profitable to remove gold and silver metallics from high grade products in the form of amalgam through use of amalgamation methods. The Amalgamation Unit with amalgam separator is ideal for the recovery of such metallics especially from the high grade hutch products from Mineral Jigs in ball mill-classifier circuits.
Gold and silver as metallics or in the form of bullion obtained from amalgamation or cyanidization methods are readily sold to the United States Mint when containing 20% or more in gold and silver combined. Mint refining charges are low being only 8.75 cents per troy ounce of gold.
COPPER SMELTING
The smelting of copper ores differs from that for lead and other metals in that the operation is done under oxidizing conditions with siliceous slags not conducive to the recovery of lead for which little or no payment is made.
Oxide ores as malachite, cuprite, azurite and native copper are easily reduced in a blast or reverberatory furnace with coke and flux to produce copper in the range of 95-98% containing impurities as sulphur, iron and antimony together with precious metals. The copper is drawn from the furnace at intervals and cast in ingots for further refining. Sulphide ores and concentrates are given a preliminary roast to remove part of the sulphur, arsenic and antimony prior to smelting in a reverberatory furnace to yield a copper matte. The grade of matte produced ranges from 16% to 60% copper, dependent upon the amount of sulphur remaining in the furnace charge. The sulfur unites with iron and copper oxides to form the matte which also acts as an efficient collector of gold and silver together with impurities such as arsenic, antimony and bismuth. The molten matte is tapped from the furnace from time to time and fed with silicious ores as a flux to a converter for oxidization of the sulphur associated with the iron and copper. Blister copper, produced in the converter, is cast in ingots for further treatment by fire refining or electrolytic methods or both.
Losses in copper smelting are low with loss of copper being between 4.5% to 6%; silver 3 to 5% and gold 1 to 2%.
Most copper concentrates smelted are very fine which result in high dust losses during roasting and smelting operations. Such dusts together with smelting fumes and gasses containing lead, arsenic and other impurities are recovered from dust chambers and the Cottrel electrostatic precipitators. Collected dusts are either sintered with coke or briquetted with suitable binders for smelting to recover valuable by-products.
LEAD SMELTING
Lead ores and concentrates, mainly lead sulfide (Galena) as the most common mineral, generally contain some silver, gold, zinc and copper together with such impurities as antimony, tin, cadmium and bismuth, all of which cause difficulties in both smelting and refining processes. Lead sulfide concentrates must be roasted or sintered, commonly in Dwight-Lloyd sintering machines to reduce sulphur content in order to control the amount of matte formed in the blast furnace during smelting. The amount of coke and flux added under controlled conditions depends on the composition of the roasted or sintered concentrates in the charge to the blast furnace. The matte produced may range as high as 40% copper and unless sulphur content in the charge is carefully controlled, may contain a high percentage of lead. Copper mattes are effective collectors of silver and gold from the charge. Most mattes are further treated in copper blast furnaces for recovery of copper and by-products or are sold to copper smelters. Lead is reduced in the blast furnace and is collected beneath the slag and matte, all three products being tapped from the furnace at intervals, with the lead bullion cast in bars of about 80 pounds each. The lead may be refined through several processes, depending on the end use and the contained amounts of silver, gold and impurities such as copper, iron, arsenic, etc.
ZINC SMELTING
Zinc is produced from concentrates of Calamine, Smithsonite, Zincite, Franklinite with principal production being from the sulfide mineral Sphalerite. The main smelting method for many years has been the process of distillation both batch and continuous, however demands for high purity metal have led to the development and rapid expansion of leaching and electrolytic methods.
The demand of zinc smelters for cheap fuels such as coal, natural gas, or electrical energy has controlled smelter locations.
Zinc ores, as sulfides, must be roasted or sintered to reduce sulfur content before reduction is possible. Zinc oxide ores are calcined to eliminate carbon dioxide and moisture before retorting. Impurities of lead, cadmium and iron must be held to low limits to reduce brittleness and to improve corrosion resistance.
In the batch distillation of roasted or calcined zinc ores, a furnace built with 200 or more closed clay retorts is used, each retort holding a charge up to 135 pounds. The charge is made up with 40% or more crushed anthracite coal or coal and coke combined as a reducing agent. Upon heating of the retorts, the charge reaches a temperature in excess of 1100°C to reduce the zinc oxide to zinc vapor which is expelled from the retorts through a system of tubes to condense and collect the zinc. This metal usually containing up to 98.5% zinc together with impurities is refined either by re-distillation or by melting in a small reverberatory furnace where oxides and impurities are skimmed from the surface as a dross. The lead and zinc-iron alloys settle to the bottom for removal.
Zinc losses through batch distillation range up to 15% depending upon impurities contained in the ores.
The development of continuous distillation methods through the use of vertical retorts has lead to improved recoveries of zinc and lower costs due to complete mechanization, high thermal efficiency and lower maintenance costs. In the continuous process, the roasted zinc ore mixed with carbonacious material and suitable binder is briquetted to make up a porous charge for feeding to the vertical retort.
Briquettes are heated by exit gases to coking temperatures up to 900°C and are fed in batches to the top of the vertical retorts which are discharged continuously from the bottom after retorting. Since the retorts produce a steady flow of gases containing vaporized zinc, condensation can be readily controlled with smaller amounts of zinc oxide dusts being produced. The condenser rapidly cools the vapor and controls the cooling of molten zinc to prevent further oxidation. Exhaust gases are scrubbed for recovery of zinc dusts which are returned for re-treatment. Usually 92-96% of zinc is recovered through vertical retorts.
THE IMPERIAL SMELTING PROCESS
This process developed by the Imperial Smelting Corporation, Ltd., is progressively being expanded into the zinc smelting industry. It is a process for smelting sinter-roasted zinc concentrates with coke in a blast furnace. The blast furnace gasses typically contain 5-6% Zn and 8-10% CO2 are brought into contact with a shower of molten lead to condense the zinc vapor for recovery as metal. The zinc being separated from lead in a zinc/lead separation chamber both through cooling and through the difference in gravity between the two metals. The process is also applied to mixed lead-zinc concentrates with the lead being tapped from the furnace bottom. The carbon consumption is about 80% of the weight of zinc volatilized with no extra carbon being required for lead production since the lead oxide formed is exothermically reduced by carbon monoxide. Some of the condenser gas is burnt for preheating the air blast to the furnace to 600°C and the charge to 800°C.
The process has the ability to handle a wide range of materials such as bulk concentrates of lead and zinc and, providing the sinter contains 10% or more lead, recovers gold and silver in much the same way as a lead blast furnace. Copper in minor amounts can be recovered in the form of matte and speiss.
Lead bullion produced compares in grade to that from a lead blast furnace when treating similar concentrates and is subject to conventional refining for market quality.
Zinc slab conforms to Prime Western Specifications and contains about 1.3% lead.
The diagramatic flowsheet shown below illustrates the Imperial Smelting Process.
Handling and Shipment of Concentrates
Concentrates are usually shipped by either truck or rail. Consideration should be given to prevent losses in shipment through leakage from truck bodies or from railroad cars. Box cars are preferred to gondolas to prevent losses due to dusting. Truck bodies are also covered or enclosed to prevent losses. In cases of high shipping costs, it may be economical to dry concentrates prior to shipment where drying costs can be offset by freight savings. Filtered concentrates average about 12% moisture, and drying to 5 to 6% moisture can be done at low cost by rotary dryers. The cost of drying increases greatly as moisture content approaches zero. However, in freezing weather additional savings in handling and sampling may be effected by drying to 1 to 2% moisture. Since smelters deduct for a minimum of 1% moisture concentrates should contain at least this amount and preferably 5 to 6% to prevent losses through dusting.
When concentrates are to be transferred and re-handled in shipment it may be advantageous to ship in sacks for ease of handling and to prevent losses, even though an extra charge is made by smelters for such shipments. High grade ores are best shipped in sealed steel drums to prevent loss through leakage, dusting or pilferage.
Freight charges by rail increase with value and are based on value per wet ton determined by dividing total value by wet weight in tons. Freight bills should be checked to avoid charges based on dry ton values.
Shipments are weighed upon arrival at the smelter and the seller or seller’s agent is entitled to watch the weighing and sampling. Both gross and tare weights should be observed and the cleaning of cars or trucks checked to prevent losses through careless unloading practice.
Samples for moisture determination and pulp assays are taken after the shipment has been weighed, usually by pipe sampling methods, although modem practice rails for automatic sampling of the entire lot. The sample for assay is reduced and cut into four portions: one for the buyer, one for the seller, one for the umpire and one to be retained in reserve. The seller’s sample is assayed and analyzed by an independent laboratory of seller’s choice for comparison with buyer’s results, and if reasonably close, settlement is made according to contract.
Smelter FEE Schedules
Smelter schedules are generally similar but vary to a degree because of conditions prevailing at different locations due to smelting practices, labor rates, fuel, power costs and distance from final metal markets. Schedules at any plant vary due to metal prices, smelter requirements for certain classes of ores or concentrates, and grade, character and quantity of ores or concentrates available from various shippers.
The smelter schedules and general conditions listed in this report are only intended to be typical, being adequate for preliminary estimates of probable returns and general information as to charges, payments and penalties. Final estimates on any particular ore should be made on the basis of actual samples, or assays being submitted to the smelter together with estimates of intended shipments to secure a smelter contract.
GENERAL CONDITIONS:
DELIVERY: F.O.B. smelter. Freight charges to be paid or guaranteed by seller. If not prepaid will be deducted from smelter settlement.
MOISTURE: Up to 10% free but deductible from shipping weight, with excess subject to a charge of 5 cents per unit or fraction.
HANDLING: Charge of $1.00 per dry ton for shipment in sacks or drums.
SAMPLING: Sampling and weighing to be done by buyer according to standard practice. Seller or agent may be present. In case of disagreement on assays, an umpire may be selected whose assay will be final if within limits of buyer’s and seller’s; if not, assay of party nearest to umpire shall govern. Losing party is to pay umpire costs. A charge of $10.00 is to be made for sampling lots of less than 10 tons.
DEFINITIONS: A ton is 2000 pounds avoirdupois. Gold and silver are stated in troy ounces. A unit is 1% of a ton (20 pounds). Delivery date is the date of arrival of the last carload or truck load of each lot.
SMELTER TREATMENT CHARGES: Usually based to include bullion freight charges from smelter to New York for lead and copper, and to East St. Louis for zinc. Contracts are subject to change with wage rates, freight rates and variations in quotations for metals.
SMELTER CHARGES
Gold: Paid at a percentage of realized mint price of $34.9125 per troy ounce ($35.00-$0.0875 refining charge).
Silver: Payment based on average of the Hardy and Harmon, New York quotations for the week following date of delivery to smelter.
Lead: Payment based on domestic lead, F.O.B. New York as published in the Engineering and Mining Journal, averaged for the week following delivery.
Copper: Payment based on cathode copper price, F.O.B, refinery, as published in the Engineering and Mining Journal, averaged for the week following date of delivery at smelter.
Zinc: Payment based on East St. Louis price as published in the Engineering” and Mining Journal for Prime Western Zinc averaged for the week following date of delivery.
The following tables show five possible methods of handling a complex sulphide ore and the returns based on the typical smelter schedules shown herein. This form of presentation is based on an article, “Marketing Concentrates” by Graham Lamb, Equipment Company (1937). Costs of handling, hauling or freight for ores or concentrates have not been deducted from the returns shown. Calculations are based on gold @ $35.00 per troy ounce; silver @ $1,293 per troy ounce; copper @ $0.32 per pound; lead and zinc @ $0,135 per pound.
FIVE POSSIBLE METHODS FOR HANDLING A COMPLEX SULPHIDE ORE
Typical Smelter Treatment Charges |
||||
SCHEDULE | COPPER SMELTER | LEADS SMELTER | ZINC SMELTER | CRUDE LEAD-ZINC MILLING ORE |
TREATMENT CHARGE | $ 12.50 per dry ton | $ 12.50 per dry ton on lead content 25% wet assay plus 10c per ton for each unit under 25%. | $ 51.50 per dry ton based on 12c market price. Add $1.25 per net ton for each 1c or fraction above 12c | $4.00+ per dry ton. |
Payments
Gold |
If .03 Troy oz. per ton or over to 5oz.pay$31.8183
per oz.; $32.3183 per oz. from 5 oz. to 10 oz. and $32.3183 for 10 oz. Or more. |
If .02 Troy oz. per ton or over to 5oz.pay$31.8183
per oz.; $32.3183 per oz. from 5 oz. to 10 oz. and $32.3183 for 10 oz. Or more. |
if .03 Troy oz. Per ton or overpay for 70% at $34.9125 per oz. | if .06 Troy oz. Per ton or overpay for 65% at $34.9125 per oz. |
Silver | if 1 Troy oz. or more pay
95% of market price less 1c per oz. |
if 1 Troy oz. or more pay
95% of market price less 1c per oz. |
If 1 oz. Or over pay for 70% at market price. | If 1 Troy oz. Or more pay for 70% at market price. |
Copper | Deduct 20 lbs. copper per ton and pay for 100% at market price less deduction of 2.75 cents per lb. | Deduct 20 lbs. copper per ton and pay for 95% at market price less deduction of 10c per lb. | If 1% or more copper pay for 65% at market price less 2c per lb. | If 2% or over pay for 70% of sulfide lead and copper combined at market price for lead less 3.27c per pound. |
Lead | Pay for 50% at market price less 3.5 cents per lb. | Deduct 3o lbs. lead per ton from wet assay and pay for 90% of balance at
market price less 2.77c per lb. |
Deduct 3o lbs. lead per ton from wet assay and pay for 65% at market price less 2c per lb. | |
Zinc | If 40% or over pay for 85% at market price less .583c per lb. If under 40% deduct 80 lbs. Zinc per ton and pay as above. | If 2% or over pay for 100% of sulphide zinc at 70c per unit on 12c market price. Add or deduct 6c per unit for each 1c change in market price. | ||
Cadmium | Pay 30% at 75% of market price. | |||
Lime | Pay 5c per unit if 5% or more. |
Typical Smelter Schedules |
||||
SCHEDULE | COPPER SMELTER | LEADS SMELTER | ZINC SMELTER | CRUDE LEAD-ZINC MILLING ORE |
DEDUCTIONS
Moisture |
5c per unit over 10%. | 1% minimum deduction
from total weight. |
||
Zinc | 30c per unit over 6% | 30c per unit over 8%. | ||
Iron | 50c per unit over 6% Fe + Mn combined | |||
Insol | ||||
Lime &
Magnesia |
$1.00 per unit over 1% combined | |||
Sulphur | 25c per unit over 3% $2.50 maximum. | |||
Arsenic | 50c per unit over 1%. | 50c per unit over 1%. | ||
Antimony | 1.00 per unit over 1% | $1.00 per unit over 1%. | ||
Bismuth | 50c per pound over .05%
|
Non-Metallic Minerals |
||||
MINERAL | PRINCIPAL USAGES | TREATMENT | MARKET REQUIREMENTS | PRICE RANGE |
Asbestos | Short fiber In asbestos cement products, asphalt
and vinyl tiles. Spinning grades in brake linings fire proof cloth, insulation and gaskets. |
Screening and air separation
after crushing. |
Many types and grades as to fiber length, strength, color, etc. | $43 to $1400/ton |
Barite | Oil well drilling muds-white paint pigments-chemical, glass and rubber industries. | Gravity and Flotation methods. | Varied grades 83 to 97½
BaSO4 with limits on Fe and impurities. |
$11 to $24/ton
—325 mesh $26 to $49/ton |
Clay | Kaolin in paper, rubber, pottery and refractories.
Other types as fire clay. Fullers earth, etc. |
Varied as to type—selective mining
—washing—wet or dry classification. |
Varied. | $3.50 to $18.50/ton |
Corundum | Combined with artificial abrasives in grinding
wheels—grinding and polishing agents. |
Gravity and varied methods. | 82% to 92% AI2O3 crude. | Up to $75/ton. |
Diatomite | Filter medium and aids—insulation—absorbents-carriers for insecticides, etc., scouring and
polishing compounds. |
Size reduction, wet or dry
classification. |
Filter, filler, insulation grades,
abrasive grades. |
$32 to $60/ton
to $138/ton. |
Feldspar | Glass, pottery, cermaics and enamels—abrasives—
scouring soaps and compounds. |
Grinding—classification—flotation. | Crude—hand sorted ground 40-200 mesh. | $7.50 to $10.50/ton
$13.50 to $21/ton. |
Fluospar | Hydrofluoric acid production—glass—ceramics—
enamels—ferrous metallurgical fluxes. |
Washing—gravity concentration
flotation. |
Metallurgical 60 to 72% ceramic +93%;acid +97%
CaF2. |
$32to$39/ton
$42 to $49/ton |
Garnet | Abrasive papers—sandblasting media—cleaning and polishing agents—gems. | Sink—float—gravity concentration
—sizing—classification. |
Conc. ±90%—sized. | $45 to $89/ton |
Graphite | Graphite crucibles, retorts, lubricants, pencil lead, carbon brushes and foundry facings. | Amorphus type selective mining
flake by flotation and sizing methods. |
Flake & crystalline 85 to 97% C;
amorphus+80 C. |
$80 to $675/M ton
$15 to $21/M ton |
Gypsum | Building lath and wallboard, sheating and plaster
—farm use—Portland cement retarders. |
Crushing and screening. | Usually-1½” high purity crude. | $3.50 to $5/ton |
Kyanite | Refractory brick, cements, plastics, ceramics,
spark plug cores, etc. |
Hand sorted—crushing-magnetic
separation and sizing. |
35 to 200 mesh 70 to 80%
grade. Iimported crushed or boulders +60%. |
$44 to $55/ton
$76 to $81/ton |
Limestone | Building stone—aggregates—Portland cement metallurgical
flux—lime production. |
Varied as to usage—
crushing and pulverizing. |
Varied requirements. | $3.50 to $26/ton |
Mica | Electrical insulation—electronic tubes and capacitors—asphalt roof and paper coatings. | Sheet by hand preparation
other by flotation-grinding. |
Flat sheets—varies as to size
and color. Ground. |
7c to $8/lb.
$34 to $180/ton |
Perlite | Expanded perlite in building plaster and light weight aggregates-filter aids-insulation. | Crushing, grinding and sizing. | Crude—crushed and sized
expanded. |
$8 to $9.50/ton
$48 to $57/ton |
Phosphate | Fertilizers mainly as super-phosphates. Production of phosphorus and phosphoric acid. | Washing and screening—flotation. | Pebble 66 to 77% BPL Rock 60 to 80% BPL. | $7 to $10.25/ton
$5 to $7.50/ton |
Potash | Fertilizers—salts wide industrial usage as cyanide,
caustics, bicarbonates, etc. |
Varies as to occurrence
Flotation—acid leaching. |
20 to 60% K2O content | 17c to 85c unit K2O |
Pumice | Concrete admixtures—aggregates—abrasives—
R.R. balast—highway surfacing. |
Crushed, dried, pulverized
and sized. |
Lump or powder. | 3c to 8c/lb. |
Quartz | Piezoelectric crystals and other electronic and optical usages. | Varied as to characteristics.
Crystals hand selected. |
Selected crystals
Varies as to size & grade. |
$4.50 to $150/ton |
Salt | Production of chlorine, caustic soda and soda ash
—snow removal—road stabilization, etc. |
Rock salt—mined and sized. Other
by evaporization & crystallization. |
Rock and pressed block evaporated. | $7 to $28/ton
$22 to $28/ton |
Silica | Foundry sands—glass and ceramics unlimited usage. | Silica and glass sands by washing,
classification and flotation methods |
Glass sand.
92-99½% SiO2 |
$1.50 to $5/ton
$22 to $35/ton |
Sulphur | Sulphuric acid production—insecticides, paper, rubber, plastics. | Frash process for underground
deposits—other by retorting, flotation and melting methods. |
+99.5 % sulphur crude | $18 to $22/ton |
Talc | Manufacture of ceramics, paint, asphalt roof coatings and insecticides. | Wet or dry grinding, air
separation or classification |
Crude-crushed.
98-100% ground—200 mesh |
$5 to $8/ton
$10.50 to $14/ton |
Vermiculite | Exfoliated as building plaster, insulation, carriers for insecticides—soil conditioners. | Crushed, sized and dried. | Crude-sized
Exfoliated |
$9.50 to 18/ton
$62 to $73/ton |
Major Metals |
|||||
NAME | MINERAL OR SOURCE | PRINCIPAL USAGE | TREATMENT | MARKET REQIREMENTS | PRICE RANGE |
Aluminum | Bauxite
Cryolite (rare) |
Aluminum metal alluminium chemicals abrasives | High grade ores reduced to metal by electrolysis | Metal 99.5 to 99.9 +AI Bauxite 50 to 60% AI2O3
Bauxite abrasive 86% |
23c to 24c/lb.
$13 to $14/ton $25 to $36/ton |
Antimony | Stibnite
Smelter by product |
Hard lead alloys—type metal-babbit—
chemical forms in glass, rubber, plastic industries |
Ores hand picked or upgraded by
gravity—refined from smelter dusts |
Conc. 50-60% Sb Metal 99% | $3.90 to $8.75/unit
Metal 33c to 55c/lb. |
Arsenic | Arsenopyrite (rare)
Smelter by-product |
Weed killers, insecticides—
pigments—glass industry |
Oxides refined from smelter
fumes & dusts |
+99% As2O3 | 4c to 5c/lb. |
Beryllium | Beryl
Phenacite |
Ceramics—electrical porcelain—
berylium metal &alloys for high strength and heat resistance |
Mechanical concentration,
flotation & chemical methods |
10 to 12% BeO
Metal98% |
$30 to $35/unit BeO
Metal $54 to $66/lb. |
Bismuth | Native bismuth Bismuthinite | Low melting alloys with tin, lead, etc. Pharmaceuticals &
industrial chemicals. |
Refined from tin-lead smelter
by-products |
Conc. 65% Bi
Metal |
$1 to $1.20/lb Bi
Metal $2.25/lb. |
Boron | Kernite
Boron compounds |
Glass—ceramics—porcelain
coatings—soaps—metal alloys |
Dissolution & crystallization of borate compounds—metal by electrolysis | Compounds Acid forms | Variable
$50 to $425/ton |
Cadmium | Zinc Smelter
By-product |
Electroplating automotive &
electronic parts, alloys and pigments |
Refined from zinc smelter
by-product |
Metal
Chemical forms |
$3 to $3.50/lb. |
Chromium | Chromite | Stainless steels & ferroalloys-refractories—
Pigments-plating |
Hand sorting & mechanical
concentration |
44.4 to 48%Cr2O3 | $18 to $36 L.T. |
Cobalt | Cobalt sulphides
and arsenides |
Permanent magnet alloys—high
temperature & strength steel alloys |
Concentration by gravity &
flotation |
10 to 12% Co
AAetal99%+ |
60c to 80c/lb. Co $1.50+/lb. |
Columbium &
Tantalum |
Columbite &
Tantalite |
Additive to semikilled steels-high
temperature alloys and magnets |
Mechanical concentration | 65% Cb2O5+Ta2O5 | 10:1 ratio 90c to $1
8½:1 85c to 90c/lb. |
Copper | Sulphide & oxide
ores |
Wire for electrical machinery &
transmission. Brass & bronze-chemical forms as germicides & fungacides |
Flotation—leaching & precipitation
—direct smelting |
See smelter schedules | Electrolytic metal
30.6c to 33.6c/lb. |
Germanium | By-product zinc
smelters |
Electronics—used in diodes,
transistors & rectifiers |
Refined from zinc
Smelter by-product |
Metal | 29c to 32c/gram |
Gold | Native gold—Tellurides
& in metal sulphide & oxide ores |
Monetary—decorative arts dental
& medical supplies— electronics—industrial applications |
Gravity—amalgamation cyanidation-
flotation |
Bullion or in metal
concentrates—See smelter schedules |
Up to $34.91
troy oz. |
Iron | Hematite—Magnetite | Cast iron and steel | Direct smelting or concentration
by washing—gravity—flotation or magnetic methods |
51½% Fe with size &
SiO2 limitations |
$8 to $14/long ton
Varies with type & delivery point |
Lead | Galena
Many other |
Antimonal lead & lead oxides for storage batteries—tetraethyl lead
—paint pigments—sheet & cast forms |
Gravity concentration—flotation | Concentrates
See smelter schedules |
12c to 14.5c/lb. |
Lithium | Spodumene
Lepidolite |
Glass—ceramics—greases-welding
compounds—metal alloys |
Flotation & sink float.
Metal by electrolysis |
Lithium ores etc.
99.5% metal |
Variable
$9 to $11/lb. |
Magnesium | Magnesite, dolomite/
Seawater |
Aluminum+magnesium alloys aircraft
tooling plate—sand and die castings |
Electrolysis of high grade
Compounds |
99.8% Mg metal | 35 ¼C to 37 ½c/lb. |
Manganese | Pyrolusite
Psilomelane |
Production of steel—high grade
MnO2 in dry batteries- |
Washing—gravity concentration—
flotation—metal by electrolysis |
Ore 46 to 48% Mn
99.8 Mn-metal |
65c to 85c long ton
unit 33 ¾c to 36 ½c/lb. |
Mercury | Cinnabar | chemical industry
Electrical apparatus & controls-agricultural— Pharmaceuticals |
Ores roasted to yield Hg—
mechanical methods & flotation to upgrade lower grade ores |
Mercury metal | $206 to $417
76/lb. flasks |
Molybdenum | Molybdenite | Alloyed with steel in production
high speed/ stainless, and other steel & iron products |
Flotation from both ores &
copper concentrates |
95% MoS2 | $1.40 lb/Mo |
Nickel | Niccolite
Millerite Pyrrhotite ores |
Temperature, electrical chemical,
& abrasion resistant steels & Alloys |
High grade direct smelted.
Flotation—magnetic separation on lower grade ores |
Concentrates
Electrolytic nickel Nickel sinter |
Varied
79c/lb. Ni 75c to 76c/lb. Ni |
Platinum | Native platinum
By-product Ni-Cu ores |
Chemical ware—catalyzers electrical
contacts—resistance wire—dental & jewelry |
Placer methods with gold, etc.
By-product Cu-Ni smelters |
Refined metal or
high grade concentrates |
$80 to $90/troy oz. |
Rare Earths | Monazite, bastnasite.
Group of 15 rare metal oxides |
Glass polishing—steel alloying for
reduction of grain growth-additives to arc-light carbons —metal research |
Varied—gravity separation from
sands—magnetic & chemical methods |
Monazite concentrates
55%+rare earth oxides |
Variable
10c to 15c/lb. |
Selenium | Smelter by-product | Diversified use in glass & ceram
ics—color and decoloring agent photoelectric cells—electronics —rectifiers |
Refined from anode muds from copper electrolytic cellsa | Metallic and
chemical forms |
$5.25 to $6.25/Ib Se |
Silver | Numerous minerals
Argentite, etc. with base metal ores |
Wide usage—coinage—electronic
parts—jewelry-silverware— photography |
Flotation—cyanidation of primary
ores. By-product lead, zinc, copper smelters |
Concentrates
Metal |
See smelter schedule
$1.29 +/troy oz. |
Tellurium | Gold & silver
Tellurides Smelter by-product |
Coloring agent glass & ceramics. Improves machinability stainless
steels, ductile irons & copper |
Refined from anode slimes copper
electrolytic cells & flue dusts from telluride ores |
Metal slab and
powdered metal |
$6 to $30/lb. |
Thorium | Monazite—associated
with uranium & rare earths |
Electronic devices—photoelectric
tubes—controls grain size in metal alloys—tungsten filaments |
Chemical methods | Metal
Compounds |
$19 to $54/lb.
$3 to $8.50/lb. |
Tin | Cassiterite
Stannite (rare) |
Tin—plate, solder, important alloy
with lead, copper, antimony or zinc |
Placer methods for aluvial.
Gravity method on lode ores |
Metal
Tin concentrates |
$1.27 to$2.04/lb. sn |
Titanium | Rutile
Ilmenite |
Titanium dioxide paint pigment &
filter, metal corrosive resistant applications—electrochemical industry—spacecraft |
Rutile & ilmenite by gravity,
magnetic & electrostatic methods |
Concentrates
(short ton) |
54 to 59% TiO2
$21 to $26/T. 94% TiO2 $102/T. |
Tungsten | Scheelite,
Woltramite & other |
High speed tool steels—rolled
metal for missle & spacecraft usage, resistant non-ferrous alloys |
Gravity—flotation &
magnetic methods |
Concentrates | 65% WO3 $10 to
$19 short ton unit |
Uranium | Pitchblende
Carnotite, uraninite |
Material for nuclear weapons &
fuel for reactors |
Selected ores sold under contracts
—treatment mainly solvent Extraction |
High grade ores &
Concentrates |
±$8/lb. U2O3 |
Vanadium | Mixed uranium
vanadium ores |
Alloying element in tool steels,
high strength steels, hard aluminum alloys—catalyst for H2SO4 production |
Leaching & solvent extraction
methods |
Concentrates | 31c/lb. V2O5 |
Zinc | Sphalerite | Galvanizing—brass products—die
casting alloys—pigments |
Gravity & flotation methods | See smelter schedules
Concentrates |
12.5c to 14c/lb. |
Zirconium | Zircon—beach sands | Ceramics—foundry sands—refractors—chemical & temperature resistant metals & alloys | Gravity methods | 65 to 66% ZrO2
Ores & concentrates |
$47 to 50/short ton |
Source: This article is a reproduction of an excerpt of “In the Public Domain” documents held in 911Metallurgy Corp’s private library.