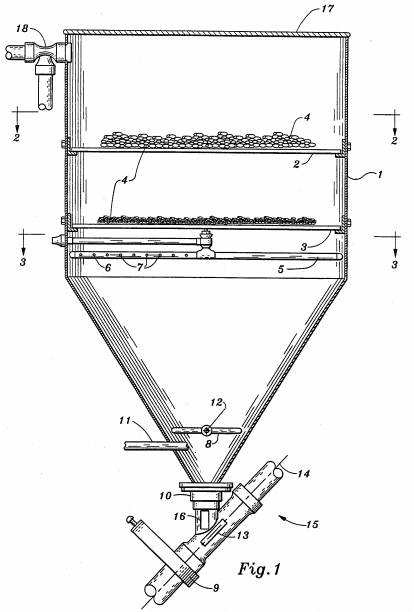
In the search for lower cost methods of recovering copper, the use of sponge iron or particulate iron (as distinguished from iron powder used in powder metallurgy) as precipitants in place of tin cans, detinned scrap iron, or scrap iron is an intriguing possibility. The relatively faster copper precipitation rate obtained with particulate iron as compared to scrap iron promises economic and processing advantages when and if particulate iron becomes competitive cost-wise with available scrap iron. Kennecott has developed a precipitation cone, Fig. 1, utilizing various particulate iron precipitants and has successfully demonstrated it in a prototype at a rate of about 1000 gpm of solution.
Initially, sponge iron produced at the Ray Mines Division for use in a LPF leach-precipitation-flotation process was used in exploratory tests to develop a suitable apparatus to take advantage of the rapid precipitation rate and efficient iron utilization for the recovery of copper from dilute solutions. Here it was demonstrated that when sponge iron was added to a launder, the particles of iron collected in the bottom of the launder and tended to cement together. This resulted in incomplete precipitation of the copper and inefficient utilization of the iron.
Next, sponge iron was suspended in glass columns to study the dynamics of the precipitation reaction. Again it was observed that the particles tended to cement together at low solution flow rates while at higher flow rates large amounts of the precipitant overflowed the column resulting in loss of precipitant and an inefficient process.
The next step was to suspend the copper precipitant in an inverted cone in a rising column of solution.
We were successful: dynamic suspension of the solids was maintained at reasonable flow rates and the copper precipitation rate was rapid and complete with improved iron utilization. The first tests were conducted on a batch basis, and it was determined that a dynamically suspended bed of precipitant was necessary for satisfactory operation. More than 99% of the metallic iron could be converted to metallic copper by careful control of the residence time in the cone, and copper precipitation was essentially complete even when the available iron was almost depleted.