A striking feature of the non-choking concave, is the character of the product. So far we have been dealing with crushers whose eccentric speeds are low enough to permit the material to fall, with each receding stroke of the active crushing member, the full distance allowed by the close CSS and open side OSS physical proportions of the crushing chamber, regardless of the shape of the concaves. In such crushers, the maximum one-way dimension of product particles is governed by the open-side discharge setting; therefore it is customary to predicate
both product and capacity upon that setting. Actually, the sizing is done by the closing stroke of the crusher on the material in the zone just above the discharge opening; in other words, upon that material which will be discharged during the next opening stroke. It follows that the shape of the chamber immediately above the discharge opening must have some influence upon the product gradation, and we should expect that non-choking concaves, by virtue of the smaller angle they afford between head and concaves in, the discharge zone, would make a more uniform and somewhat finer product than straight concaves. This is true, and it is an important and favorable feature of these concaves, particularly so as applied to the production of commercial crushed stone.
As the percentage of voids decreases in the crushing chamber, the amount of very fine material produced at each stroke is apt to increase, due to the crushing of particles against each other as they become more and more closely packed. Therefore the ratio-of-volume-reduction has a definite influence upon the amount of fines in the crusher product. This is especially true of friable materials. On such materials the substitution of non-choking concaves for those of the conventional type will usually result in marked decrease in the percentage of extremely fine material in the crusher product.
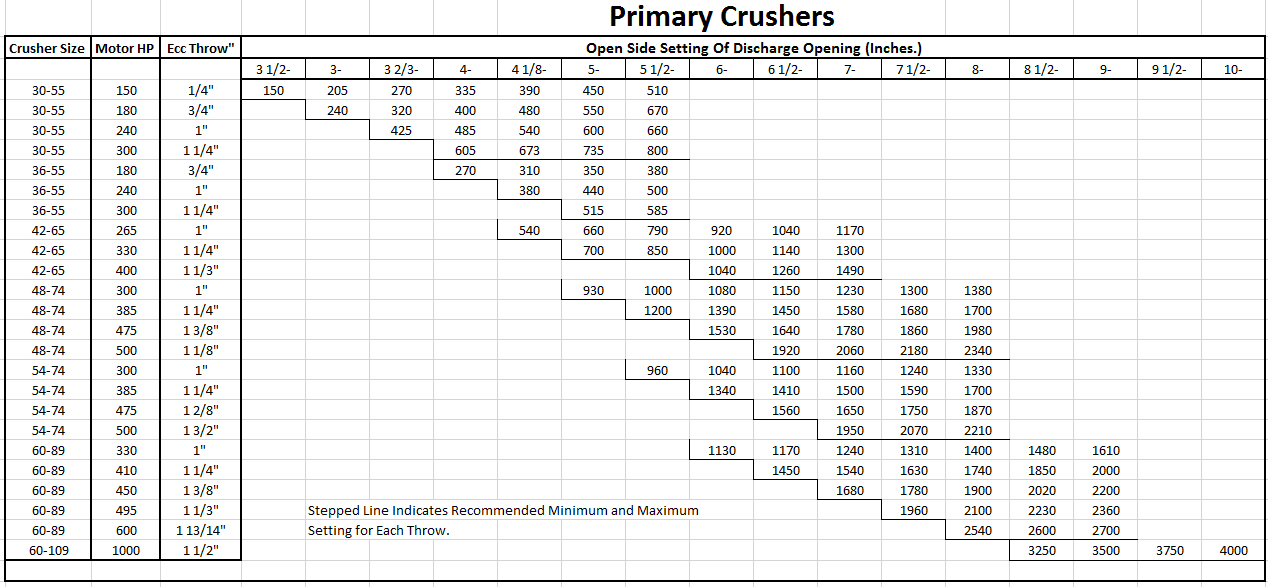
From the standpoint of power consumption, the best machine is the one that does the least amount of unnecessary work. A certain amount of non-productive work is expended by any pressure-type crusher in “pushing around” material which is already small enough to pass the discharge opening but which is prevented from doing so because the particles are trapped in the surrounding body of material.
As the percentage of voids decreases the number of such trapped particles increases, the amount of non-productive work likewise increases, and the material becomes harder to move as it becomes more compacted. Actually, there is some work being accomplished on this small material which might properly be classed as productive work; but, from the viewpoint of the commercial crushed stone producer at least, it is undesirable work: the attritional production of fines, mentioned in the preceding paragraph. The clean-breaking crusher is the economical crusher, both from the standpoint of power consumption, and general wear and tear.1 And, because the non-choking concaves make for cleaner breaking, they benefit the crusher in both of these respects. At comparable discharge settings the power saving may run as high as 20%.
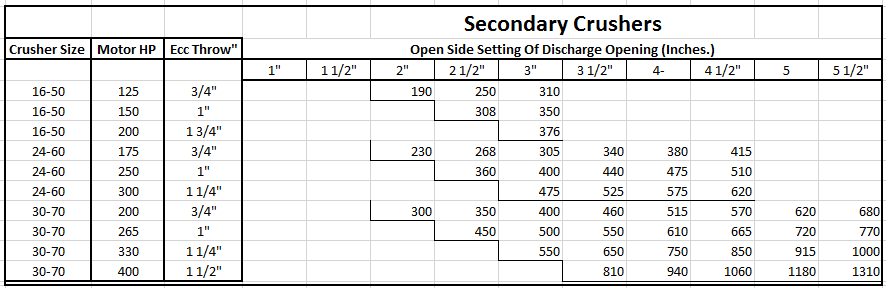