Table of Contents
A crusher’ surge pocket, sometimes called a “rock box“, is found directly below the primary gyratory crusher. It provides limited storage, normally about two truckloads, to enable smooth feeding of crushed product from the bottom of the crusher onto an apron feeder and takeaway belt conveyor.
Pocket Level
Level instruments measure “high-high”, “high”, and “low” levels in the surge pocket. Normal operating practice is to keep the pocket about half full at all times. A “high-high” level alarm indicates the box is too full to receive any more product. All dumping into the crusher must stop until the “high-high” alarms are cleared and the pocket level is sufficiently low to accept more feed. A low level alarm indicates the box is almost empty enough that rock can drop directly onto the feeder. This should be avoided over prolonged periods to avoid damage to the feeder. The feeder should be stopped, and dumping should proceed cautiously, until the low level alarm is cleared.
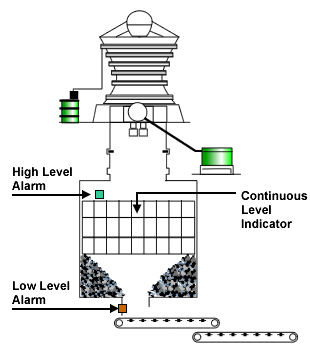
Safety
- General: follow lockout and tagging procedures to disconnect the crusher and feeder from electric power.
- Clearly post and barricade the dumping area to notify others that personnel are working under the gyratory crusher.
- Post an observer at the access door of the crushed ore pocket.
- Wear approved safety belts and lines.
- Ensure there is adequate ventilation and lighting.
- Clear any overhanging material before entering the pocket.
Additionally, the use of a truck dump hopper at the apron feeder creates a large surge pocket between the mine and the crusher, making the flow of ore through the crusher more uniform and continuous.
Advantages of indirect feed using an apron feeder include:
- Low bench height for dumping ore,
- Reduced truck queue time due to the surge pocket,
- Improved control of oversize material fed to the crusher, and
- Reduced crusher downtime due to bridging of large lumps.
Disadvantages of indirect feed using an apron feeder include:
- Increased total capital cost,
- Increased maintenance costs associated with adding an apron feeder, and
- Increased maintenance costs associated with the crusher from using an apron feeder. Due to the nature of the feeder, ore tends to impinge upon small areas within the crushing chamber, causing premature localized wear of the concaves and mantles. The use of alloy steels has mitigated the problem, although the cost of alloy steel components remains higher than manganese steel, and availability is limited.
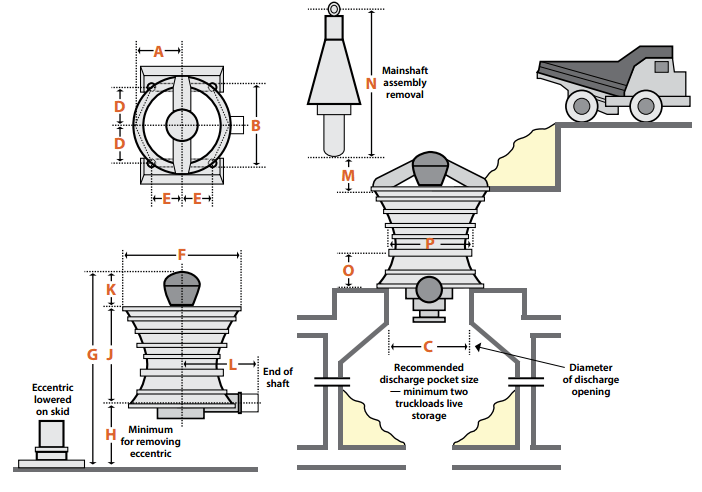
Crushed ore pockets under gyratory crushers generally have their upper walls lined with steel to prevent wear on the concrete, while many pockets are lined with cast manganese steel plates which require much complicated embedded metal for anchoring. Impact on these liners by crushed ore is usually light, and large sheets of AR plate make for a more economical and just as good installation as the smaller plates of cast manganese. Eye bolts installed in the ceiling of the crushed ore pocket near the walls are vely useful in installing these liner plates.
The capacity of the crushed ore pocket should follow that of the dump pocket and should be not more than 1% times that of the largest truck contemplated. More capacity than this only adds extra expense. in deepening the entire crusher structure. Level controls in the pocket are generally of the radioactive type and the source can best be suspended in a pipe cast into the concrete wall of the pocket. In the Palabora crusher, the radioactive source is suspended in a steel-protected enclosure in the back of the pocket wlth the detector installed outside the front wall. Sonic detectors for measuring high levels are much improved and are frequently used.
To aid in cleanup around the crusher itself, a hole covered with a steel plate can be installed in the ceiling of the crushed ore pocket. Spills then need not be hoisted out of the enclosure by the crane. The entrance door to the crushed ore pocket can take many forms.
At Lornex, it is hinged at the bottom, has eccentric cart rails mounted on its outer face, and is let down by a winch into the pocket to rest on two steel-protected concrete walls. At Bougainville, where there are two crushers, each crushed ore pocket has two doors on opposite sides which let down to form a bridge for the eccentric cart under the crusher. In other cases, the cart rails are permanently in place, as at Butte, Cuajone, and the Climax Henderson operation. At these two latter crushers, the eccentric carts are underslung from the wheel carriages and roll into the crushed ore pocket on permanent rails. In most instances, the rails are stored outside the pocket and are Installed in the crushed ore pocket only when the eccentric is being removed.
At most crushers, the eccentric is lowered to the cart by the crane above the crusher; but in some of the newer installations, as at Palabora for example, the cart is equipped with a hydraulic platform which raises up under the eccentric and then lowers it for removal. Handling of the eccentric in this manner is easier, faster, and safer; and it frees the crane for other work.