Although its brief period of popularity passed some thirty-odd years since, and only a few sets were installed before interest reverted to other types, the high-speed double roll crusher developed by Thomas A. Edison shortly before the end of the last century warrants a place in any discussion-of crushing equipment. In 1960, the largest machine of this type the 6 x 7 foot “giant” rolls were huge crushers, judged even by present-day standards; they have an unobstructed receiving opening 7 x 7 foot and their capacity on individual skip-loads of stone is enormous, although, as will be explained, they cannot maintain this peak capacity over a period of time.
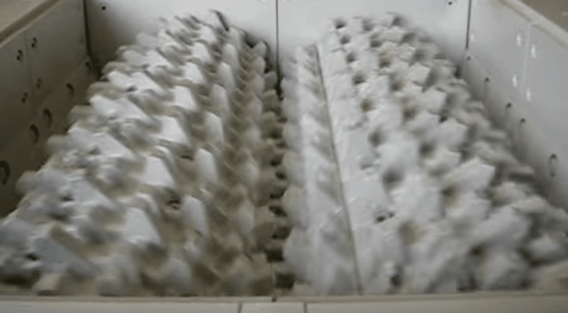
Mechanically, the teethed roll crusher is a very simple machine. The two rolls are carried in bearings, supported on two very heavy and rigid bed castings which are secured on the concrete foundation by a number of large anchor bolts. The bearings, in addition to being bolted to these bed castings, are prevented from spreading by pairs of large tie-rods which pass through them above and below the roll shafts. Unlike the smooth-face crushing rolls we have described, these tension rods are not cushioned by springs. The machine is surmounted by a heavy cast rectangular hopper, all sides of which are vertical. Each roll is independently driven by a flat-belt pulley.
The roll-centres are octagonal in cross section, each face being provided with a spline groove and a series of tapped holes for securing the chilled- iron wearing plates. These wearing plates have the sledging knobs, or teeth, cast on their outer surfaces. Thus we have a roll surface that resembles that of the one roll crusher, except that the faces of all teeth are sloped instead of radial on the advance side. The usual practice is to fit one roll entirely with so-called regular teeth, and the other roll with six rows of regulars and two rows of higher (slugger) teeth.
The peripheral speed, or tip-velocity, of these rolls is much higher than that of any of the machines we have previously described. The range of the smooth-face rolls, for example, is from about 400 ft/min for the small 12-in. rolls, to 2000-2200 feet/minute for the heavy-duty 72″ machine. The single-roll crusher has a tip speed of 400-450 ft/min while the 6- x 7-ft teethed roll crusher has a normal, no-load, surfaces speed of just under 3500 ft/min.
It can be readily appreciated that this high velocity induces an extremely violent crushing action, in conjunction with the 3- to 4-in. knobs which protrude from the roll surfaces. Impact, sledging, and pressure crushing enter into the over-all performance; but impact, in this crusher, plays a far more important role than it does in the slower speed single-roll machine; and crushing, even well down along the roll faces, is more in the nature of a sledging action than it is of pressure crushing, for this action occurs in the lower-velocity crushers.
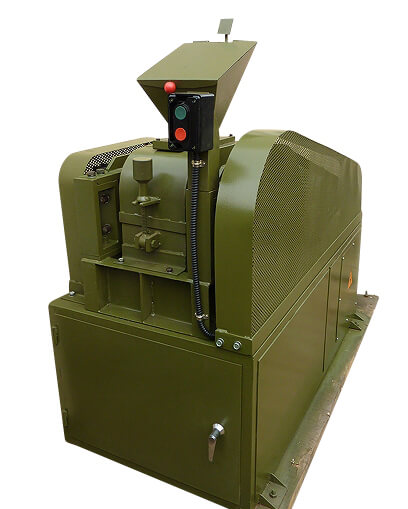
The theoretical maximum size of cube that the knobs will grip, when the rolls are set at minimum spacing, is 24″; but the rolls will reduce any stone that can be introduced into the 7-ft square hopper. Large blocks will span across the tops of the two rolls; immediately the slugger teeth on the one roll so equipped go to work on these blocks and quickly shatter them into pieces that can be gripped between the sets of regular teeth; from this point on, the action is a mixture of sledging and pressure crushing. The same selective segregations which we described in connection with the single-roll machine occur in the double-roll crusher; the smaller pieces are cleared quickly, leaving the roils free to work on the larger blocks.
The entire performance on individual skip-loads of stone takes place in a very short period of time. Ten- ton loads of mixed-size medium limestone will clear the crusher in from 10 to 15 sec.; large single blocks, weighing from 6 to 8 tons, are crushed in from 5 to 20 seconds, depending upon the toughness of the individual piece, and upon the way it happens to land in the crushing chamber. These performances were clocked on ma-chines turning out a 6″ product.
The short-time transfer of energy, especially when crushing large blocks, is very high; so high in fact that it would not be economically feasible to provide sufficient motive power to deliver it. The usual practice, when these rolls are driven electrically, is to drive the slugger roll with a 250 HP motor, and the regular roll with 200 HP, a total of 450 HP. As compared to this motive power, instantaneous energy delivery may run as high as 4000 HP, obviously far beyond the capacity of the motive equipment. But the rolls themselves, when running at normal no-load speed, have a stored kinetic energy of upwards of 4,000,000 ft -lb , and it is this stored energy that does much of the actual crushing, the motors serving to bring the rolls back to normal speed between crushing periods. In crushing a skip-load of stone the rolls may lose anywhere from 30 to 60 RPM in speed; this loss occurs partly through slowing down of the motive equipment, and partly through belt slippage. It requires from 5 to 10 sec. to bring the machine back to speed, during which time the power input will vary from 400 to 600 HP. The power required to run the rolls empty is something less than 100 hp. The average power consumption, when crushing from 3000 to 4000 tons per 10 hour day will run in the neighbourhood of 150 HP on medium limestone.
While the average power consumption of this machine compares favorably with that of other types, the rather violent fluctuation outlined and the relatively high connected horsepower are unfavourable features. It is also natural to expect that the belt slippage we have noted would constitute something of a problem over a period of time. Performance records indicate that belt trouble accounts for about 50% of the total lost time on a set of these rolls, and about 25% of the total maintenance expense.
The type of quarry equipment most commonly used in conjunction with this crusher is the three-sided steel skip, carried on a flat-top truck or flat car. These skips are provided with a shackle on the rear end, which is engaged by a hook actuated by a small hoist. This apparatus slides the skip over against the lip of the receiving hopper, and tilts it to discharge its contents. The skips discharge over a feed-roll which retards the flow of material so that the entire load does not drop into the crushing chamber at once. When the skip is empty it is pulled back on to the truck or car by a counterweight attached to the opposite end of the same cable which performs the hoisting operation.
We have mentioned the heavily ribbed hopper which surmounts the frame and extends up to the level of the feed roll. This hopper serves the double purpose of directing the material into the crushing zone, and preventing stones thrown by the slugger teeth from flying out of the crusher. It is also necessary to cover the top of the hopper with heavy netting to contain flying spalls. The straight-sided, rectangular hopper construction, and the violent agitation in the crushing chamber, tend to minimize blocking and bridging in this crusher. When bridges do occur they are difficult and dangerous to break while the rolls are running.
Applications
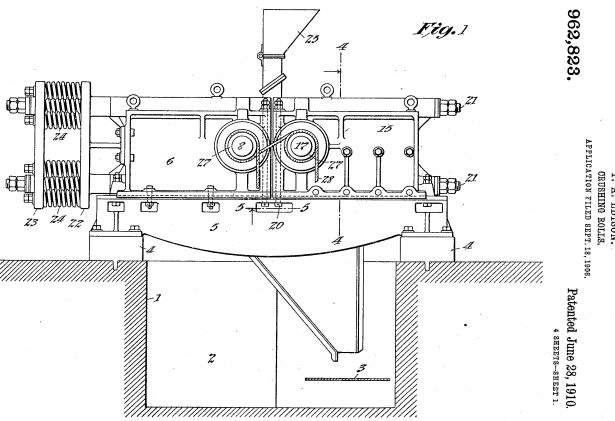
Practically all that we have had to say about the application of the single-roll crusher will apply as well to the Edison toothed roll crusher. It is better adapted to handling blocky stone than is the single-roll machine, because its slugging action is much more vigorous, and it will handle any material that will not build up on the sides of the vertical hopper. It is not as simple a machine to feed as the single roll crusher, because its narrow hopper necessitates the uses of skips, or very short-bodied cars. A heavy- duty apron feeder would of course solve this problem, but so far as we know, none of these crushers were so equipped.
The high peak capacity of the crusher constitutes something of a problem in plants of medium capacity. It is not economically feasible to provide elevating or conveying equipment to handle peak loads of around 4000 TPH in a plant designed to turn out that much stone in an 8 or 10 hr day; consequently means must be provided to smooth out these high surge loads. This can be taken care of by a surge bin and feeder below the crusher, or by passing the roll product direct to a secondary crusher of uniform-capacity characteristic. A feeder ahead of the rolls would smooth out peaks on mixed feed but. once a 10 or 12 ton block of stone is dropped into the crusher, that quantity comes through very quickly as crushed stone, which would render the regulating properties of the feeder of questionable value.Modified forms of this crusher were used by Edison for secondary and tertiary stages. The crushing equipment in one large plant, for example, comprised a set of 6- x 7-ft rolls (8″ product), a set of 4 x 4 feet secondary rolls (3.5″ product), and a set of 4 x 3 ft tertiary rolls (1.5″ product), these last rolls being in closed circuit. These smaller machines were also run at high speeds, their surface velocities being slightly over 3000 ft/min.
mclanahan.com
https://www.youtube.com/watch?v=GA8AJfmzy_Q