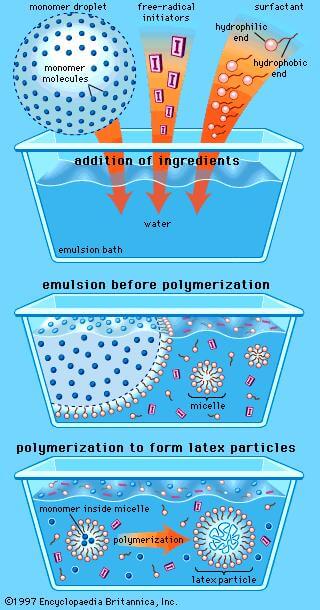
Emulsion polymers are polymer in oil emulsions and are designed to “break” out of this emulsion into a water solution at 0.5 to 1.0% concentration. If water is allowed to get into the bulk storage tank, either by backing up in the feed line or by condensation, gels will form. They may take the form of sheet gels which are typically found on the walls of tanks or gel lumps (from water droplets).
- Emulsion polymers are polymer in oil emulsions. A solution preparation procedure that provides adequate mixing at the right concentration is essential to achieve full product performance and “invert” the emulsion so the polymer goes into the water solution.. The recommended solution concentration is between 0.50 and 1.00%.
- Make the sample bottle is well shaken. Emulsion polymers will separate over time (both a slight oil layer on top and a thickened polymer layer on the bottom).
- Use the same water for laboratory solution preparation that will be used to prepare samples in actual plant situation.
- Calculate the concentration to be made down (ie. For 0.50% measure 1 mL to 199 mL of water).
- The recommended solution preparation mixers are an overhead mechanical mixer (400-700 rpm), a Twister Mixer or a Braun or equivalent blender.
- Use only one syringe per sample. Double pump syringe to remove air then fill to required level and wipe outside of syringe clean.
- Inject the polymer into the edge of the vortex (about 1-2 seconds for injection).
- Let mix (1 minute for overhead mixer, 10-15 seconds for twister mixer or Braun mixer).
- Let samples age unmixed for 20-30 minutes to allow the polymer to uncoil.
- Prior to use gently mix made down solution to ensure homogeneity. Further dilution can now be done, if necessary, using the solution preparation procedure above.
- At room temperature cationic solutions are good for 6 hours while anionic solutions are good for 8 hours.
- If a range of products are being made down start with anionic high charge first going down in charge then thoroughly clean equipment before beginning to make down the cationic solutions going from lowest charge to highest charge.
Emulsion polymers are single component emulsions that must be pre-diluted with water prior to use. In most cases, these products should not be fed neat. Positive displacement pumps (gear or progressive cavity) are recommended for this product. Many commercial systems are available to prepare solutions of polymer via in-line dilution and mixing. One manual method for dilution is to add the neat product into the vortex of a mixed tank at the recommended concentration. Recommended solution preparation concentrations should be between 0.5 – 1.0%, regardless of polymer preparation equipment utilized. Polymer solutions should be aged for a minimum of 30 minutes prior to use. Shelf life of solutions is 8-16 hours. Secondary dilution to 0.05 – 0.1% before the application point can improve product performance.
- Do not store samples in extreme temperatures.
- Adequate mixing is critical to ensure representative results, be sure sample container is well shaken and that mixing energy used to put product into solution is sufficient for the job.
- Always use a fresh syringe for each product. Do not clean and reuse syringes.
It is important to use the best water available to make your polymer solutions. Any solids in the make up water will react with the polymer rendering the solution less effective. Other water characteristics to consider are:
- pH – as the pH of the water becomes more alkaline the cationic products begin to lose effectiveness due to hydrolysis.
- Temperature – the recommended water temperature should be between 40-90º F. Temperatures below this range will typically result in slow or incomplete dissolution of the polymer. Temperatures appreciably above this range can cause hydrolysis of the polymers. In general, warm water allows for improved speed of dissolution and uncoiling but results in slightly shorter shelf life of the solution.
- Conductivity – waters that are very high in conductivity can inhibit the development of molecular weight in the polymer solution.
Check valves should be installed in feed lines to avoid the potential for water to “back up” into the bulk storage tank. Bulk storage tank vent desiccators are recommended for every bulk tank. If the potential for freezing is present the bulk storage tank should be heat traced and insulated.