Table of Contents
The reason why you need Flash Flotation in a Closed Grinding Circuit relates to “Recovering your mineral as soon as free” which has long been recognized in ore dressing practice. This not only applies to gravity treatment but also to flotation. For this application the Flash Flotation Cell was developed for use in the grinding circuit and has done a remarkable job in many plants.
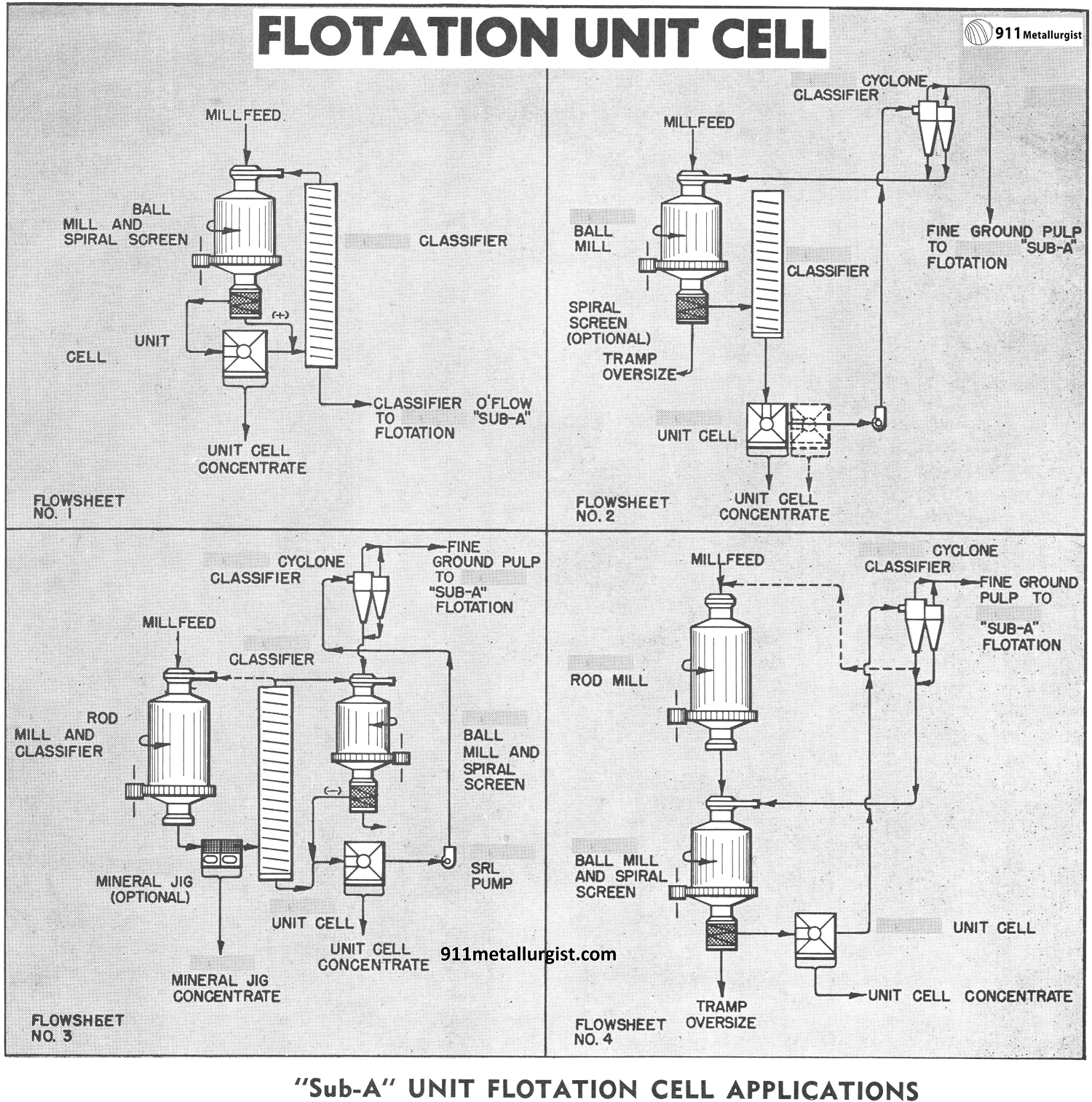
A greater amount of granular higher grade concentrates can be produced and, in general, overall plant recovery is improved by reducing slime losses due to overgrinding and colliding of high specific gravity minerals.
Closed Circuit Grinding Flowsheets with Flash Flotation Embedded
Typical flowsheets are shown to indicate a few of the possible applications of Flash Cells in grinding circuits. In recent years the successful application of hydraulic cyclones, rubber lined pumps, and two stage grinding circuits have enhanced the feasibility of unit cell applications. Cyclones in particular have increased the flexibility of such applications by permitting positive and continuous gravity flow of unit cell tailings to subsequent treatment steps.
Closed Circuit Grinding FLOWSHEET #1
In this flowsheet the Unit Cell is placed between the ball mill and classifier to remove mineral which is free and ready to float.
Molded rubber wearing parts are used exclusively in unit cells. If wear is severe due to coarse abrasive solids, a special molded soft rubber compound is available which greatly extends the impeller and wearing plate life. Conical disk impellers and wearing plates are standard for unit cell applications.
A mineral cone in the bottom of the unit cell is advisable. It acts as a trap for high specific gravity coarse mineral, grinding media fragments and other foreign material.
Closed Circuit Grinding FLOWSHEET #2
Two stage classification is shown in this flowsheet with a Unit Cell between the classifiers. The primary classifier may overflow as coarse as 20 mesh and at densities up to 50% solids. This is ideal feed for the unit cell. Unit cell tailings are classified through a cyclone and the oversize returned to the ball mill for further grinding. The cyclone classifier overflow, 65 mesh or finer, is treated by regular bulk or selective flotation.
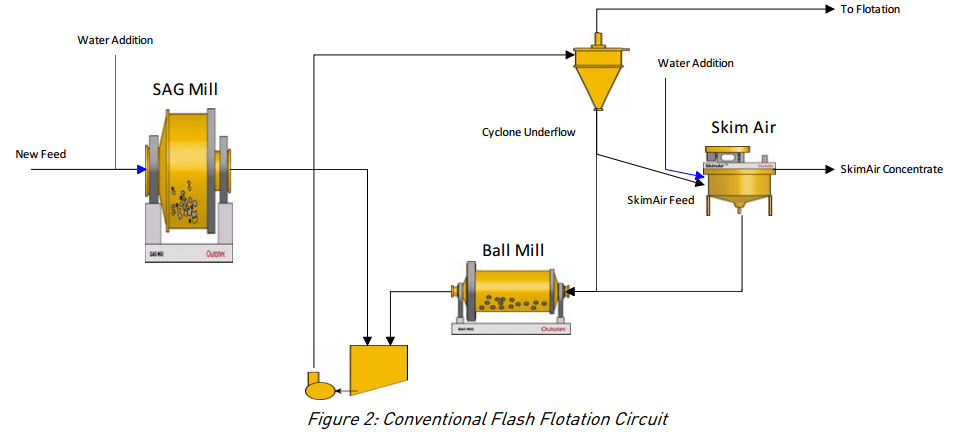
With this two stage classification system the unit cell can be conveniently located to deliver a positive gravity discharge of pulp to the pump feeding the cyclone. The pump sump box can be made a part of the unit cell tank if desired.
Closed Circuit Grinding FLOWSHEET #3
Two stage grinding and classification is provided in this flowsheet which is generally applicable to larger tonnage installations in which a substantial percentage of the values can be recovered directly from the grinding circuit. The primary Rod Mill in open circuit will reduce crushed ore to approximately minus 10 mesh. A Mineral Jig is recommended if coarse mineral and metallics are present.
The spiral or rake classifier overflow passes to the unit cell and on to classification and regrinding. High grade unit cell concentrates can be produced with this system, and on low ratio of concentration ores a substantial increase in mill capacity is possible. Slime losses are greatly minimized with this combination jig and unit cell circuit.
Closed Circuit Grinding FLOWSHEET #4
The trend in many of the large tonnage milling circuits is to completely eliminate conventional rake or spiral classifiers by going to two stage grinding with a rod and ball mill in series. The rod mill discharge goes direct to the ball mill and then on to a pump and hydraulic cyclone classifier. These modern grinding and classification circuits are ideal for including the unit cell as the primary mineral recovery step.
One large copper operation with two stage grinding and cyclone classification, actually treats cyclone underflow, — 20 plus 100 mesh, through Unit Cells. The unit cells recover a substantial percentage of the total copper in final concentrate form. The unit cell tailings at 55% solids return by gravity to the regrind ball mill feed. Since incorporating the unit cells and by careful checking between parallel circuits, it has been established by “recovering the mineral as soon as free” that final mill tailings were reduced by ¼ lb. copper per ton.
LABORATORY TESTING
Unit Flash Cell flotation tests should be made before planning an installation. This will establish if the ore will respond to such treatment to advantage. A 100 lb. representative sample of the ball mill feed is sufficient for the unit cell flotation tests.
Flotation in a Grinding Circuit
The simplest flotation circuit is a comparatively recent innovation. It consists of the introduction of a flotation cell into the grinding circuit between ball mill and classifier as shown below. The discharge end of the mill is fitted with a trommel screen with openings about 4 mesh in size to separate out coarse material, which is laundered direct to the classifier ; the remainder of the pulp passes to the flotation cell where most of the mineral which has been released from the gangue is taken off as a concentrate, the necessary reagents having been added at some previous point in the circuit, usually at the mill feed box. Flotation can be carried out in a pulp containing as much as 65% of solids, but water is added in most cases to bring the W/S ratio to about 1/1. In such a thick, heavy pulp it is possible to float particles as coarse as 10 mesh. At this size, however, only pure mineral will adhere to a bubble, for which reason the concentrate is generally of unusually high grade.
The advantage of this method of flotation is that the valuable minerals are removed from the circuit as soon as they have been released from the gangue, so that their accumulation in the classifier is prevented and the possibility of overgrinding them is reduced. Moreover, the granular nature of the particles floated assists considerably in the subsequent filtration of the combined flotation concentrate. It is a simple matter to instal the cell in the ball mill circuit, since it fits readily into the space between mill and classifier and occasions no loss of head. The only disadvantage is the heavy wear to which the interior of the cell is subjected by the coarse material passing through it, but the modern method of lining both moving and stationary parts with rubber reduces this difficulty to minor proportions.
Mcintyre Porcupine Mines, Ltd., was one of the first companies to practise flotation in the grinding circuit. Their installation is described later in the paragraph headed “Flotation of Gold and Silver Ores . Others soon also adopted the method. In their plant grinding is carried out in a Hardinge Ball Mill in closed circuit with a Dorr Classifier, and a “ Sub-A” Cell is employed as the flotation unit between the two, the pulp being maintained at a density of 65% solids. Under normal operating conditions 60-70% of the copper and 40% of the nickel are recovered in the grinding circuit. Subsequent flotation in “ Sub-A” Machines gives a total recovery of nearly 99% of the copper and over 94% of the nickel. No attempt is made to separate the copper from the nickel minerals.
The process can be adapted to the selective flotation of complex ores. Another mill for instance, where a lead-zinc ore is treated by two-stage selective flotation, the method being very similar to the standard procedure described in the paragraph entitled “ Flotation of Lead-Zinc Ores ”, the installation of a cell between ball mill and classifier has resulted in the removal of most of the galena before the pulp passes to the main flotation circuit. The sphalerite in the ore is so finely intermixed with a portion of the galena that, although a large proportion of the latter mineral is actually liberated at a comparatively coarse mesh, it is necessary to reduce the whole tonnage to 87% minus 200 mesh in order to separate the two minerals at all completely. Before flotation in the grinding circuit was tried, three stages of cleaning were required to make a high- grade lead concentrate, and 96% of the finished product would pass through a 325-mesh screen, only a trace remaining on 200 mesh. The introduction of a “ Sub-A” Cell into the grinding circuit enabled over 70% of the lead to be recovered in one operation without cleaning in a concentrate running 65-70% lead. The concentrate contains only 53% of minus 325-mesh material, 25% remaining on 200 mesh, and, being more granular than that obtained in the main flotation circuit, it gives better filtration. The total recovery remains much the same as before. Reagents are added in the ball mill feed box, and the pulp is maintained in the cell at about 58% solids.
There is no necessity to limit the size of the flotation machine between ball mill and classifier to a single cell, through the use of a multi-cell or a long pneumatic machine would involve changing the relative positions of the three units from the present standard arrangement. The trend of progress indicates that the flotation machine may become in some cases as important a factor in the proper classification of the ore during grinding as the classifier itself is at present.
Flotation in Grinding Circuits
Hydrocyclones are used in many grinding circuits to make a size separation which ideally sends the fine ore fraction to conventional flotation and the coarse fraction back to the mill for further grinding. The separation results not only from particle size but also from particle specific gravity. The result is a cyclone underflow which is higher in grade than the cyclone feed. When comparing sulphides and precious metals to silicates, the floatable size fraction in the cyclone underflow contains higher mineral values than gangue. This results because the lower specific gravity gangue particles tend to follow the water in the cyclone overflow.
Typical grinding mill circulating loads range from 200% to 500% with a large part being particles which should have reported to conventional flotation. These particles, mainly heavy sulphides and precious metals, are being reground sometimes several times before eventually making it to the conventional flotation circuit. With each pass through the mill, the particles are ground finer until they are overground. This produces slimes which are usually lost to tailings. The attempt has been made in the past to recover valuable minerals from grinding circuits by flotation. This method, referred to as a unit cell operation, treated grinding mill discharge with a conventional flotation machine. Until now the success of this method has been limited by the inability of a conventional machine to treat the very coarse, high density slurries associated with grinding mill discharges.
Outokumpu developed a specially designed tank to work in conjunction with its flotation agitation mechanism to recover valuable minerals from grinding and classification circuits before they are overground and lost as slimes. The Outokumpu Skim-air coarse flotation machine has been used successfully to recover values from both grinding mill discharge and hydrocyclone underflow.
The Skim-Air Flash Flotation machine floats only those liberated valuable particles which are quick floating. There is not sufficient residence time in the machine to float the slower floating middlings and gangue particles. Thus, each time a particle with ideal fast floating characteristics reports to the cyclone underflow, it is removed in the Skim-Air.
The feed to the Skim-Air machine is normally in the range of 65% to 85% solids. In most cases optimum results are achieved with little or no dilution water being added to the machine. The concentrate produced in the Skim-Air is normally sent as final concentrate. Because only quick floating mineral particles have time to float in the Skim-Air, the concentrate from the machine is usually higher grade than that produced from the conventional flotation circuit. The higher feed density allows coarser particles to be floated resulting in an overall coarser concentrate being produced in the Skim-Air than in conventional flotation.
Increased Recovery
The overall recovery of valuable minerals can be increased through reduced overgrinding. This results because the quick floating liberated valuable particles in the cyclone underflow are removed from the circuit by the Skim-Air and sent directly as final concentrate. If left in the circuit as part of the recirculating load, these particles will be further ground and reduced in size until they become part of the slow floating slimes fraction. At this point they can easily be lost to tailings. Overgrinding and slimes losses are particularly a problem when processing heavy sulphides such as copper, lead and zinc or precious metals such as gold and silver.
In operations where coarse fraction losses are a problem, the use of a Skim-Air allows the ore to be ground finer without fear of overgrinding the valuable mineral. This is particularly helpful in lead/zinc concentrators where a finer grind may liberate more zinc but also increase lead slimes losses.
Overall recovery increases of up to 25% have been attained in actual plant production with 30% to 60% of all metal values being recovered in the Skim-Air.
Figure 2 shows the narrowing of the particle size range being sent to conventional flotation. The difference between the two curves corresponds to a decrease in relative losses of both the slimes and oversize fractions.
Improved Concentrate Grade
When being fed from the cyclone underflow, the Skim-Air is able to produce concentrate with a grade equal to or better than that being produced in conventional flotation. Much of the floatable size gangue in the hydrocyclone feed passes with the water to the cyclone overflow and on to conventional flotation. This results in a feed to the Skim-Air which is very low in floatable gangue. Coupling this with a particle residence time in the machine of 1-2 minutes which allows only liberated values to float, enables the Skim-Air to produce a high grade concentrate.
- Reduction of Flotation Residence Time
- Elimination of Flotation Circuit Overload
- Lower Dewatering Costs
![]() |
![]() |