A flotation flowsheet should be as simple and flexible as possible, because changes in the ore often necessitate changes in treatment: the more flexible the flotation machine, the easier and quicker the changes can be made, not only in regard to flexibility in arrangement of cells, but also the ability to treat coarse as well as fine material. The flexible points of a “Sub-A” which should be convinced in flowsheet design are:
- Any cell can be used as a rougher, cleaner or recleaner.
- Middlings can be returned to any cell from any other cell without the use of pumps or elevators.
- There are no blowers or air pipes to change or regulate.
- Use of Flotation Cells makes it possible to install units between ball mill and classifier, or to add in any part of the circuit.
- Due to the distinctive gravity flow principle, the “Sub-A” Cells will treat a coarse product as efficiently as a fine product, which often becomes necessary where dumps, tailings or low grades ore are floated when their values do not permit the high cost of fine grinding.
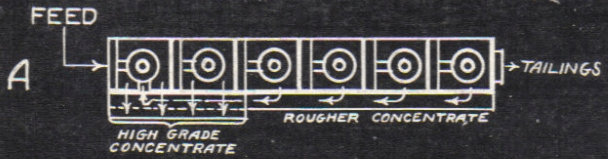
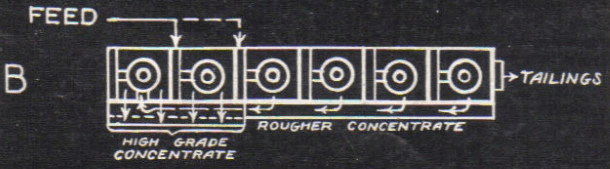
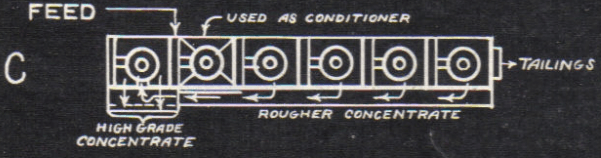
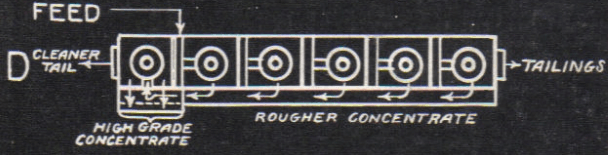
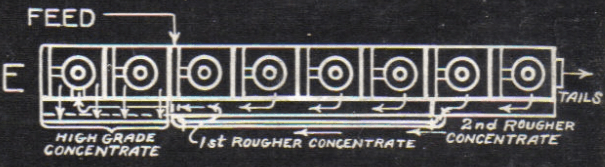
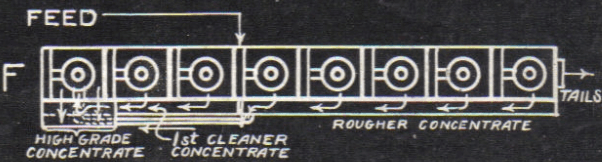
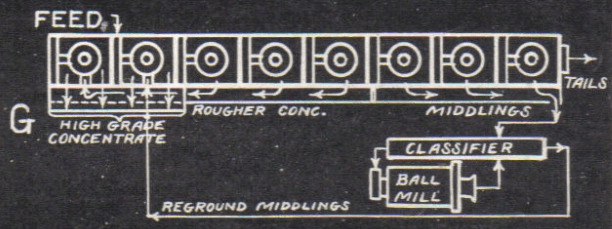
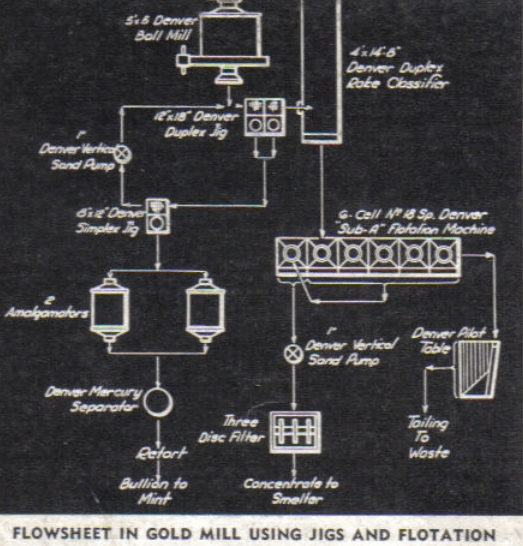
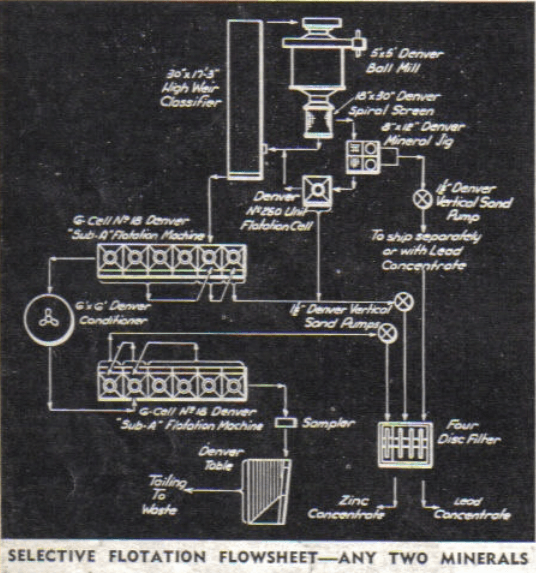
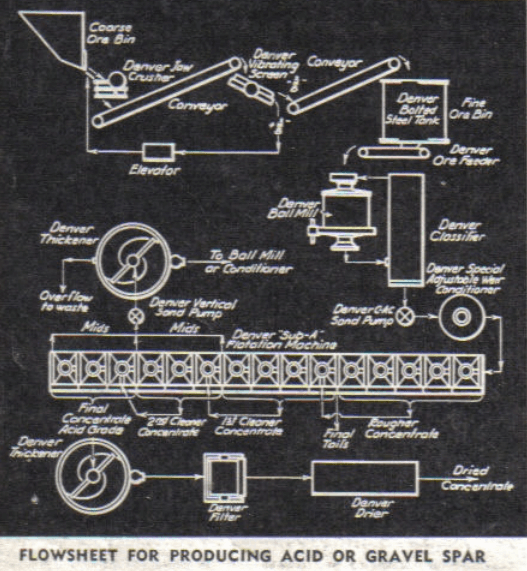