At a mining operation, a project was designed and implemented to develop a process for controlling lead recovery in the flotation plant. The metallurgical program consisted of two parts:
- A survey of the current plant process streams was conducted first to assess the performance characteristics of the existing flowsheet and equipment.
- A comprehensive program of laboratory scale metallurgical studies was commenced on a sample of future ore to assess how lead deportment could be controlled.
The operation was processing blended ores from two distinct mining areas, designated as the WHM, and the MGB. The reported average grades of these two mining zones are summarized here below.
Over the future 5 years, ore production from the WHM w is expected to decrease as the reserves are depleted resulting in a significant increase in the proportion of MGB. Hence, the lead content of the plant feed will also be at elevated levels. It is anticipated that the lead content in the ore will increase from an average of 0.30% lead, from ore currently being processed, to about 0.55% over the remaining life of the mine.
A plant modal survey, representing the 1st Phase of this project and the current concentrator operation, was designed to assess the metallurgical performance characteristics of the minerals in the copper rougher-scavenger circuit and the copper cleaner circuits while processing relatively high lead content ores.
The principal objective of this survey was to assess the recovery by size profiles of liberated and composite minerals down the rougher-scavenger bank and around various units in the cleaner circuit. This information will provide important clues regarding the deportment of minerals in the process which can be used to further investigate various treatment options. These processing options would be investigated during a metallurgical test program planned for 2nd Phase.
The plant survey was conducted for a total of 33 process stream samples taken from around the mill’s copper rougher-scavenger and cleaner flotation circuits. Only 9 samples were subjected to mineralogical analysis.
The schematic flowsheet shown in below indicates the sample points and a metallurgical balance at the time the survey was taken.
In addition to chalcopyrite measurable levels of bornite, chalcocite and covellite were also observed in the process stream samples. However, for ease of presentation all copper sulphide minerals will be identified as chalcopyrite.
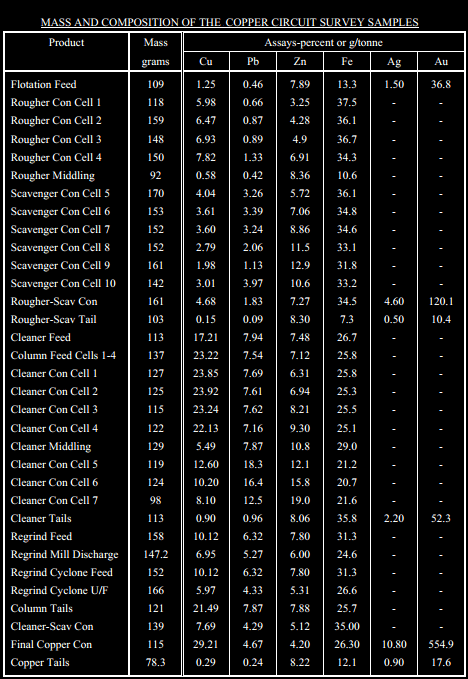
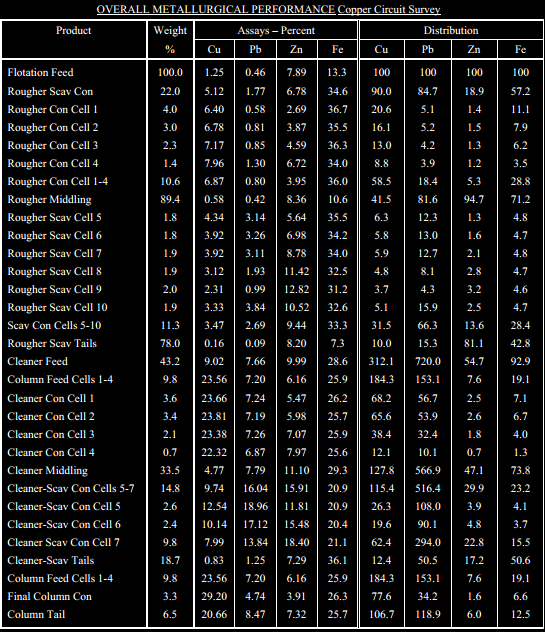
- Flotation Process Development and Assessment
- Mineral Composition and Fragmentation
- Evaluating Copper Rougher-Scavenger Flotation Circuit Performance
- Measure and Evaluate Flotation Scavenger and Cleaner Tail Losses
- Effect of Regrinding
- Evaluating Copper Flotation Cleaner Circuit Grade/Recovery Results
An evaluation of the modal analyses performed around this copper flotation circuits revealed the following:
During the plant survey the copper rougher circuit recovered about 60% of the copper, 20% of the lead and 5% of the zinc into the rougher concentrate. Most of the remaining copper and lead was recovered into the scavenger concentrate.
Better than 95% of the copper sulphides in the flotation feed were present as chalcopyrite. The remainder was distributed between bornite, chalcocite and covellite. If the amount of these secondary enriched copper sulphide minerals increases in the feed, then a significant reduction in chalcopyrite-sphalerite selectivity in the copper flotation circuits should be anticipated.
At a nominal P80 = 125µm primary grind size about half of the chalcopyrite was liberated and displayed strong flotation response in the rougher-scavenger circuit. About 75% of the liberated chalcopyrite was recovered in the rougher circuit with most of the remainder being recovered in the scavenger circuit.
Most of the unliberated chalcopyrite particles present in the flotation feed were of reasonable quality and could be considered appropriate targets for regrinding. In fact, regrinding the rougher-scavenger concentrate from P80 = 83µm to 32µm, increased chalcopyrite liberation from 63% to 90% in the cleaner feed. This level of liberation may exceed the requirements for a successful cleaner circuit operation as very fine liberated chalcopyrite was the primary form of copper lost to the cleaner-scavenger tail stream.
Similar to chalcopyrite about half of the galena in the flotation feed is liberated. However, in contrast to chalcopyrite, only 15% of the liberated galena was recovered into the rougher concentrate. Most of the remaining liberated galena is recovered in the scavenger circuit.
The remaining galena is distributed principally between galena-sphalerite binaries and as galena bearing complex multiphase structures. It is important to note that only 3% of the galena in the feed is in binary form with chalcopyrite.
Based on these observations the rejection of galena from the copper flotation circuit is a viable option worth considering. This could be accomplished by employing a sequential flotation circuit where separate copper, lead and zinc rougher and final concentrates are produced. Another option would be to utilize a more regressive depressant scheme in the copper circuit to more efficiently direct galena to the zinc circuit feed via both the copper rougher tail and cleaner scavenger tail streams. A final option would be to consider reprocessing of the cleaner scavenger concentrate to remove the recirculating load of galena from the current copper cleaners.
The dominant source of chalcopyrite losses to the copper scavenger tail stream is distributed between chalcopyrite in binary form with sphalerite and gangue and as chalcopyrite multiphase structures. This rougher-scavenger circuit is operating efficiently and any attempt to recover additional sparsely mineralized chalcopyrite binary and multi-phase particle would be deleterious to subsequent copper cleaner circuit operation.
About 60 percent of the sphalerite in the flotation feed stream is liberated. This level of liberation is adequate to ensure a successful flotation response in the zinc rougher circuit.
The copper first cleaner circuit was operating to recover 59% and 37% of the chalcopyrite feeding the circuit into the first cleaner and cleaner-scavenger concentrate respectively. It is interesting to note that galena and sphalerite are preferentially recovered into the cleaner-scavenger concentrate where it is recycled back to the head of the cleaners. An option worth considering is to preprocess the cleaner-scavenger concentrate to help reduce contamination of the copper concentrate with galena and sphalerite. This improvement in concentrate quality will, however, occur at the expense of some copper recovery.
The column circuit in the concentrator appears to display an atypical behavior. In this circuit all classes of particles are poorly recovered over the entire size spectrum. Normally columns display recovery profiles where liberated minerals are well recovered in a narrow band in the mid size range. Perhaps the reason for this unusual response profile is the large circulating loads present in the circuit at the time the survey was taken.
At the time of the survey the overall copper cleaner circuit was operating to recover about 85 percent of the chalcopyrite in the cleaner block feed.
This recovery level is considered low when compared to other operations where 90 percent of the chalcopyrite in the cleaner block feed stream is present as liberated grains.
About two thirds of the losses to the cleaner scavenger tail stream are attributed to the rejection of liberated chalcopyrite sized finer than 15µm in equivalent diameter. Undoubtedly regrinding of the rougher-scavenger concentrate to a P80 of 32µm is responsible for the production of these relatively difficult to recover finely sized liberated chalcopyrite grains.
Recommendations: Perform a series of laboratory batch cleaner and locked cycle tests and modal analysis of locked cycle test products to assess the flowsheet options suggested in this study. These options would include:
Producing selective copper, lead and zinc concentrates. – Reprocessing the cleaner scavenger concentrate to attempt to remove the recirculating load of galena from the copper cleaners. – Redirect galena, currently reporting to the copper concentrate, to the copper rougher and cleaner-scavenger tail streams. This option could be accomplished by using a more regressive depressant scheme.
Continue to perform modal studies around the copper circuits of this mill. These surveys are required to confirm the results of this initial survey and to establish the reasons for the atypically low cleaner circuit performance, particularly around cleaner column circuit.
Perform a program of modal studies designed to quantify the amount of secondary copper sulphides in various ore zones. The amount of secondary copper sulphides present in the flotation feed will have a profound effect on the flotation response of sphalerite in the copper rougher and cleaner circuits. A program of locked cycle tests would then be used to assess the metallurgical responses of the selected ore zones.