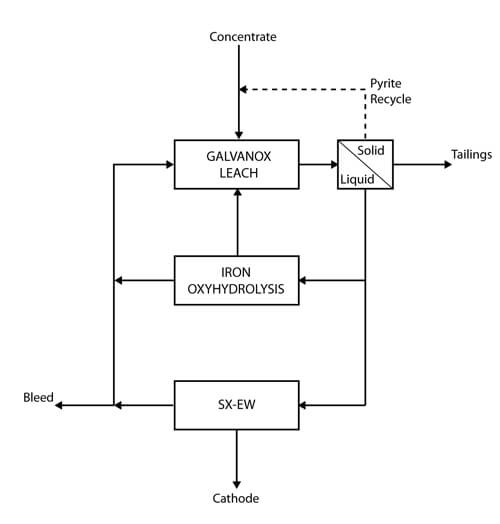
The following is a description of the testing procedure for scoping studies for candidate Galvanox Process materials and concentrates. This document will cover both the procedure for individual tests as well as considerations and strategies for testing regimes.
Galvanox testing regimes will be different depending on the mineralogy, grade, particle size distribution, pyrite:chalcopyrite ratio and gangue level of the concentrate.
First the candidate material(s) should be characterized with XRD-Rietveld, multi-acid digestion/ICP analysis, and particle size distribution analysis (either manually with sieves, or with mastersizer type machines). The data from this analysis is invaluable. Understanding the results of any tests without this characterization data is impossible.
The first test for any material should be as received. This will establish a baseline for kinetics, pyrite suitability, and gangue reactivity. If a separate pyrite concentrate is provided, a test should be done where an appropriate amount of pyrite con is added to yield a pyrite:chalcopyrite ratio of 2-3. If this pyrite con has a significant copper concentration, it should be leached separately beforehand in another test. This will insure that copper from the pyrite does not “drown out” the copper in the major material.
The second test should be with a proven pyrite. Active pyrite is the A standard. If the candidate material reacts to pyrite or another proven pyrite but does not react with the pyrite already in the con, have a look at where in the flotation process the pyrite is being produced. Generally, the less flotation the pyrite has undergone the better. The pyrite that reports with chalcopyrite in flotation is often of the anhedral or subhedral variety, rather than the less reactive and more effective euhedral type.
The effect of pyrite:chalcopyrite ratio has a marked effect on Galvanox kinetics. Typically the higher the ratio, the better. In order to test this a series of recycle tests can be done. Take an initial charge of material and leach under standard conditions. When this test is complete, decant the solution and rinse 2-3 times to remove residual copper bearing solution. Add fresh water and acid, and another charge of material. At this point the pyrite:chalcopyrite ratio is twice as high as original. The process can be repeated to look at a pyrite:chalcopyrite ratio 3 times as high, or further. In this case, the kinetics should speed up with increased ratio. When doing recycle tests, be aware of the amount of gangue in the slurry, and remove it via decantation if necessary.
The particle size of chalcopyrite has little to no effect on Galvanox kinetics. The particle size of pyrite is very important – generally the finer the better. Fresh pyrite surface area also speeds kinetics. Quick regrinding of the whole material often speeds kinetics, as does regrinding of just the pyrite fraction (in the case of separate materials for each mineral). If a pyrite concentrate is obtained through gravity concentration or any other method that selects for larger particles, a grind to get the P80 <100 microns is a good idea.
The mineralogy of the copper in the sample will have a strong effect on the kinetics. Secondary sulphides like covellite and chalcocite leach very quickly (within 1-2 hours). Primaries such as chalcopyrite, bornite, and enargite leach slower. If you see a tiering effect in your recovery versus time data it is because the different minerals are leaching in series, not in parallel.
So we figured out that the ORP probes used for consistently reading 60-100mV below the actual value of the solution, verified by a probe that we knew was good. While some of this discrepancy was taken care of via the one point calibration on the controller, solution potential is a highly nonlinear function and a simple 1 point calibration can only go so far.
In addition, some modifications to the oxygen sparger and impeller were suggested to improve gas liquid mixing and to insure that the kinetics measured in the setup are always chemistry limited rather than mass transfer. Specifically, smaller holes in the sparger, and lowering both the sparger & impeller to have more effective depth. I suspect that the lower kinetics in the previous tests are almost entirely due to the poor ORP probes, but improving gas liquid mixing never hurts.