Table of Contents
Gold can be concentrated and recovered by applying different gold refining process methods and the final product has variable quality. In this way, it is necessary to have a better marketable product so that the incomes can be improved. Then, we have two smelt and cast the gold into bars called bullion or Dore. The name bullion is restricted to the precious metals, refined or unrefined, in bars or ingots that contain small contaminants.
For many years, the term bullion made reference to coins and the name base-bullion is for pig-lead or copper bottoms obtained in smelting operations of lead and copper concentrates. The last product is characterized for containing small amounts of gold and silver. The treatment of these products depends on the metallurgical extractive process of lead and copper.
It has been shown that concentrates obtained by gravity devices and cathodes can be smelted directly most the time. Silver-gold concentrates can be smelted too. Under this consideration, a concentrate must contain at least 20 oz/t of gold. Obviously, if the higher grades are better and 50 oz/t is a good average value. It is important to mention that a silver-gold concentrate obtained by flotation has a high silver content. For example a concentrate assaying 1400 oz/t Ag and 8 oz/t Au can be smelted directly. The smelting process involves several operations, retorting, smelting and refining.
Gold Alloys
The most known gold alloys are made with silver. The proportion between gold and silver changes the alloy color. In this way, there are yellow and white alloys and the last ones present different metallurgical properties. Alloys are influenced by the presence of other minerals or metals. The next table shows the melting point of many elements and minerals that usually are in gold concentrates.
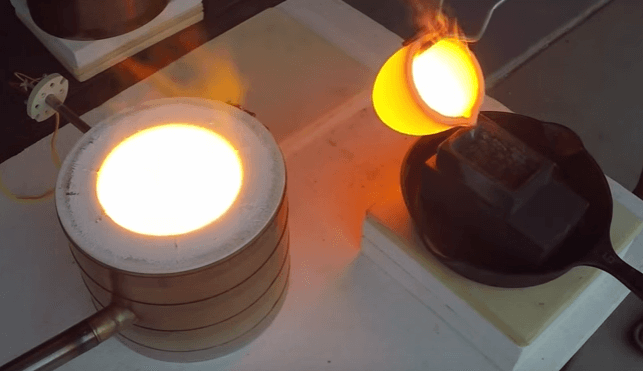
Gold Melting Points
Basically, gold can form alloys with the metals mentioned in the table. There are other metals, but the alloys are no stable. For example, arsenic and antimony are decomposed by mercury. Only some metals such as zinc, silicon, iridium and cobalt can be used to prepared good alloys without modifying the gold properties too much.
Metal/Mineral | Au | Ag | Cu | Hg | Zn | Pb | SiO2 | FeS2 | Al2O3 |
Melting point, oC | 1063 | 960 | 1081 | -39 | 419 | 327 | 1725 | 1170 | 2075 |
Alloys based on the gold-silver-copper system can be employed for many applications. They can be rolled, flattened and stamped easily. It has been investigated the effect of different elements and compounds on gold bullion properties. For example, deoxidizers are added in order to minimize the formation of oxides (e.g. copper can be oxidized easily) when is necessary. The presence of zinc or silicon reduces the formation of oxidized copper compounds, but other oxides more stable are produced.
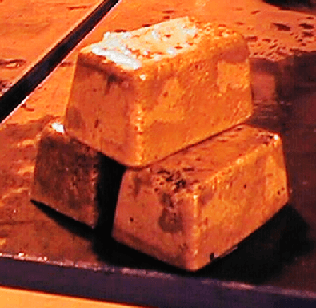
Especially zinc oxides that are difficult to eliminate. Phosphorous and boron are good deoxidizers, but an excessive addition or presence is a problem because the metallic product can be brittle. So, we have to analyze the gold concentrate and the additives to be added in order to have a good alloy.
Elements have influence on the grain size. For example, large grains tend to create a peeling effect, this can produce losses when the bar is transported and handled. The presence of barium salts is good due to acts as a grain refiner. In general, some elements and compounds form fine disperse centers where the crystallization starts.
Silicon is not very soluble in gold and silver. In this way, a low melting eutectic point is produced which modify the melting point of the alloy. Normally the compound is formed on grain boundaries making the alloy a little brittle. If the gold concentrate has copper, silicon can form alloys with copper easily avoiding or minimizing the brittle effects. Other problem with silicon is the grain size, it tends to grow. When some corners are brittle, they were cause by silicon. Brittle points or located areas will produce gold losses. Then, it is important to know the material to be smelted and the fluxes or additives to be added.
Au-Ag-Cu Ternary diagram
Amalgams are other important group of alloys. Quicksilver (Mercury) reacts with gold at ordinary temperature, and forms alloys of variable composition. An amalgam containing 90% Hg is liquid, 87% Hg is pasty and 85% Hg is solid. Amalgams with smaller contents of mercury can be produced by heating the alloy at different temperatures. When amalgams are heated near of the boiling point of Mercury, the gold content is higher and reaches the maximum point when all the mercury was distillated.
Retorting
Gold concentrates, precipitates, and Merril-Crowe product can have mercury is variable proportion. If we smelt the charge directly at 1100 oC, mercury will be released to the environment and the smelting place can be a dangerous place. In order to avoid this situation, is necessary to eliminate mercury by retorting. The same considerations taken in the amalgamation process are valid for this stage. The small amount of elemental mercury that is extracted from the host rock can affect workers health. Considering the fact that cyanidation is the main gold recovery process and indirectly mercury by a factor of 2,000 – 5,000. The last one needs a small volume of high grade gold solution that is suitable for final recovery. Elemental mercury vapor is released when the pregnant leach solution undergoes the recovery process required to produce dore bars.
The hazards associated with mercury exposure include inhalation, absorption and ingestion. As an air contaminant, the main concern is inhalation of vapors as results of releases. Acute exposure to high levels can lead to severe lung damage and death. This poisoning has three phases, initial exposure results in flu like symptoms lasting between one to three days, followed by signs and symptoms of severe pulmonary toxicity; the final phase is mouth sores and ulcers with memory loss, depression and insomnia. It must be mentioned that these symptoms are characteristic of high exposures. Then, this step is very important. OSHA has established a permissible exposure level of 0.05 mg/m3 based on eight hours average time.
Retort
There are several types of retorts and the final selection is based on gold production, mercury recovery system, and safety conditions. The charge is heated slowly until boiling point of mercury is reached. At this point the mercury is eliminated and condensed in cooling tubes passed through water. Obviously, some losses can be produced and this can be estimated as 0.065 grams per 255 grams of mercury. The process takes two to three hours. The final product is composed by gold, silver, sulphides and base metals.
Although the process is simple, the elimination of mercury is not totally perfect. The problem has two causes; first, flouring or tiny mechanical reduction of size during grinding. The second cause is due to chemical reactions that forms coatings or layers of some impurities. These coatings can be oxides, sulphides, or sulphates of some base metals that present in the ore. The employment of mercury which contains with base metals improves mercury elimination. Oxides are formed by weathering and they are not soluble in mercury, and then float on its surface. Gangue minerals are other possible source of coatings due to recovery and concentration processes are no totally efficient.
Retorting Process
The mercury retort must be located in a special place. Basically, the room should be kept under a negative pressure with respect to the rest of the building, which can be accomplished by using either fans or local exhaust ventilation. The makeup air vents for the room exhaust ventilation system must be located on the wall opposite the refiner fresh air supply plenum. The retort has to be operated and maintained in accordance with the vendor recommendations. Test must be performed to know the optimum operating parameters prior to start its service. This will minimize the potential of sending mercury contaminated to the flux mixing station and furnace section. During the operation the retort must work under vacuum and the air exiting the water condensation system has to be scrubbed with a mercury vapor removal system such as a filer with activated carbon. Then, the flow can be introduced into the vacuum system. The scrubber system is required due to the water condensation system is not efficient.
The condensed mercury vapor is trapped in a condensation pot. Normally, liquid mercury can be removed from the container by opening a valve and draining into another container. The mercury is then poured into a flask. This procedure must be done carefully.
Mercury Bottles
Gold Smelting
Once performed the retorting process, the product obtained is heated in a furnace in the presence of slag forming fluxes at temperatures over the melting point of all the components of the change, commonly between 1150 to 1450 oC. This operation is performed for around two hours to ensure complete separation of impurities from the precious metals. Gold and silver form an alloy that is heavier than the slag and sinks to the bottom of the furnace. Once the smelting is complete, the slag is removed and the precious metals are casted in ingots. The slag contains gold and silver and must be reprocessed in order to minimize the losses of precious metals.
A very important element in the smelting process is the flux, which is added to charge in order to remove base metals and other impurities from the Dore bar. The mixing of charge and fluxes has to be done in ventilated areas. A good practice is to vacuum the flux and charge from the retort pans either directly into the furnace or into a hopper that will feed the mixture into the crucible. In this way, personnel will not be in direct contact with the flux or any residual mercury vapor. In general, the flux and the retorting product must be mixed with safety.
Electric Gold smelting Furnace
The flux is a mixture of several reagent chemical such as borax, silica, sodium nitrate, sodium carbonate and fluorspar. Borax is a white crystalline mineral used in glass and ceramic enamel mixes. In the smelting process, borax helps to reduce the gold smelting point of the charge and capture metallic oxides. The addition of this reagent must be controlled; otherwise the slag will be extremely hard and non-homogeneous. Other negative effect is to avoid the separation of phases into the molten charge. Silica is an acid flux and reacts with metallic oxides forming stable silicates. Excessive addition creates slags with high viscosity and metallic oxides are no trapped with efficiency. Normally, the borax/silica ratio is 2/1. Sodium nitrate is an oxidant for iron, copper and zinc. When the charge is near 500 oC, sodium nitrate produces oxygen. Sodium carbonate is an alkaline flux whose melting point is 850 oC and reacts with silica forming sodium silicate. The latter reacts with oxides and produces other oxidized compounds. Sodium carbonate must be added with caution due to an excessive addition creates sticky slags that are difficult to remove. Fluorspar modifies slag viscosity because modify the silicates formed during the smelting process. An excessive addition attacks the crucible and reduces borax action on metallic oxides.
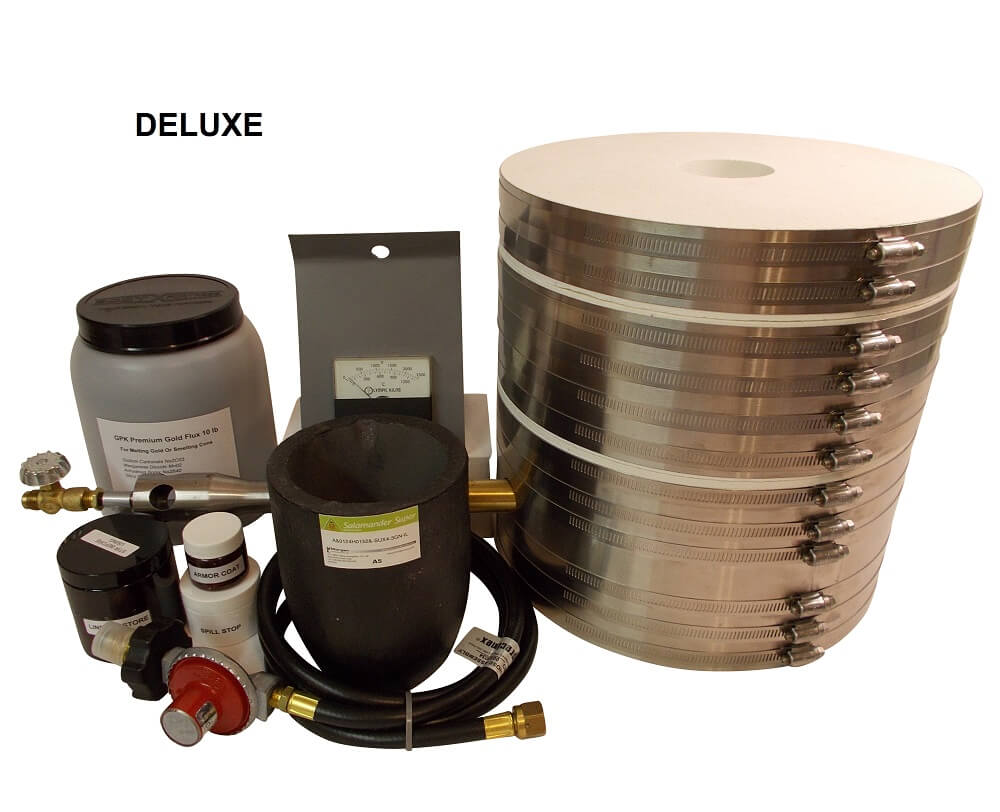
When the flux and the charge are mixed in the right proportion, the slag will take the right smelting point, density and viscosity are low, fluidity is good, metallic oxides are eliminated easily; precious metals losses are reduced at minimum and can be broken easily. Separation efficiency between precious metals and slag is evaluated by taken slag samples and perform assays for gold and silver. The performance depends on the charge properties, gold and silver content and fluxes efficiency.
During the smelting process, any residual mercury contained in the concentrate will be eliminated in the first moments. An exhaust hood must be placed over the furnace to extract mercury and other fumes released during the heating process. In the market exists two types of hood, one considers and annular hood mounted on the top of the furnace, and the other design considers an enclosure around the furnace. Depending on the silver content, the process can produce silver fumes. Then the Dore bar should be allowed to cool in the molds to facilitate removal of the bars after they have cooled. An exhaust hood must be considered in case silver fumes can be a problem.
The molten charge has to be sampled by using a glass vacuum tube or a simple ladle to take a deep sample. Dore bars are cooled after they are poured and then chipped to remove slag. This step can be done by using a pneumatic chipping gun or automatic descaler. Probably, considering the daily production, the best option must be chosen.
Once the slags were removed and cooled, will be stored for further processing. Precious metals can be recovered by gravimetric devices and cyanidation. A common practice is to crush the material until 100% passing 20 mesh. The material is processed in a shaking table and the concentrate is smelted again and the tails is crushed again in order to have a finer size, which must be appropriate for cyanidation. Intensive cyanidation is a good option, but obviously, the material can be sent to the leaching process employed to treat the raw ore. Gold and silver recoveries are between 99.5 to 99.7%. Although slag production weight is variable, a typical operation can generate 10 kilos of slag per 1000 oz of gold.
The precipitate obtained in the Merrill-Crowe process is very sensitive during the smelting process due to the process employ diatomaceous earth as a filtration medium. This material contains silica. Then, it is important to know the silica content in the cement so that the fluxes can be added in the right proportion in order to avoid unexpected problems in the process. Also the final product quality is influenced because the silver/gold proportion is modified. Other very interesting point is the degree of oxidation generated by the flux. If the oxygen liberated is high, there will be produced a foaming effect during the smelting process. The foam contains water vapor, metallic oxides fumes and combustion products and creates an appropriate environment to trap gold and silver into the slag. When this happen, it is necessary to observe the molten charge so that we can be sure the foam disappeared. This operation can takes time, but the losses are minimized.
Pouring molten charge into molds
The recipe to be used in variable and is based on the charge composition. For example, 1 ton of concentrate or cement can be mixed with 300 kg borax, 100 kg silica, 10 kilos sodium carbonate, 5 kilos sodium nitrate and 0.5 kg fluorspar. As was mentioned before, the flux has influence on the slag properties and Dore bar composition. Precious metals contents are between 98 to 99%.
There is an alternative process that employs fluxes, carbon and lead oxide (litharge). In this case carbon helps to reduce oxides and distribute the temperature correctly in the crucible. Flour is the most known source of carbon. When the charge is taken high temperatures lead oxide is reduced and metallic lead is produced. This metallic lead in liquid state traps gold and silver. As slag and metallic charge have different densities, lead and precious metals go to the bottom of the crucible and the slag floats. In other words, lead reduces the losses of precious metals into the slag. The mixture of heat, fluxes, carbon and lead assure an appropriate reducing environment. When the smelting process is complete, the charge is poured into a mold. Once the slag is cool, this can be separate from lead and precious metals by using a hammer or any device than can break the slag. The metallic product is named button and have to be processed in the other smelting process called cupellation. By this second stage, lead and precious metals are separated. The button is placed in cupels which are porous containers. These empty spaces will absorb lead oxide and the Dore metal is formed. Cupellation is performed under oxidation environment in order o oxide metallic lead to PbO.
Gold Refinery Slag
A brief description on slags was mentioned briefly in the previous item. Slags are a very important part of the process because they may tell us if the smelting was carried out in the right way. As was mentioned, in the making of Dore bars (Gold Bullion) oxides and other impurities are eliminated by means of high temperature reactions with fluxes. Most of the impurities and fluxing agents combine to form a liquid silicate called slag that float above the liquid Dore metal and is removed from the crucible. Normally, crucibles are fed with a retorting product and reprocessed slags from previous operations due they can contain precious metals in variable proportion. Slags are glassy, stony, hard and compact; and their properties mainly on how the material was cooled. The cooling procedure has influence on how a particular slag can be reprocessed.
In general, slag from smelting process arises from extraneous materials such as rust and oxides; oxidation of elements in the charge (e.g. iron, copper, zinc); residues from fuels; fluxes employed in the process (silica, borax, sodium nitrate, sodium carbonate, fluorspar); crucible erosion. Then, slag can vary in appearance and chemical composition.
Slags can be categorized in three groups. The first one is formed by allowing the molten slag to cool relatively slow under ambient conditions and the final cooling can be accelerated with water spray. The second one is cooled through a water jacket that leads to rapid steam generation and formation of several cavities within the slag. These cavities modify the slag density. The third group is formed by granulated slag that is formed by quenching molten slag in water. The very rapid cooling causes solidification of the slag as sand sized particles of glass.
Refining Gold
Refining processes are employed to improve the gold product quality. There are several types of refining procedures employed, but some of them are selected according to the daily production. It is important to mention that the gold purity is variable according to the process employed and the worker’s experience. If the final content is important, some assays must be performed. This point is valid when there is a previous commitment on gold quality. Other aspect very important to mention is about impurities, if they are difficult to remove, the process selected must be changed. Ensuring that most of gold is recovered is a very important aspect so that the production cost can justify the operation. Finally, there are aspects related to health, safety and contamination that have certain influence in the process.
Impure Gold from Electrowinning Process
The techniques employed are Cupellation, Inquartation and Parting, Miller Chlorination Process, Wohwill Electrolytic Process, Fizzer Cell, and Aqua Regia Process. The final election is based on the initial gold content. For example, the Whohwill Process is selected if the gold content is not less than 98%, the Aqua Regia process is a good option when the silver content is less than 5%. It the charge to be refined contains platinum group metals such as platinum and palladium, the Inquartation and Parting Process can be selected. In general the final selection is not easy and is good practice to equip a facility to perform more than one process.
The Cupellation process is employed in very small scale and is based on the fire assay process. The final product can collect gold and platinum group metals. Perhaps, small miners can considers this option when there are economical restrictions and the final product quality is not very important. The Inquartation and Parting Process is based on the solubility between gold, silver and copper. Initially there is an impure product obtained by smelting that must be grained to improve the surface area so that the metallic product can be attacked with nitric acid in order to dissolve copper and silver and the leaching residue is metallic gold. During the acid attack, platinum and palladium forms part of the rich solution. However, Iridium, Ruthenium, Rhodium and Osmium are not dissolved. The gold purity is close to 99.99% when the platinum group metals content is very low.
The Miller chlorination process is well know and has been practised for a long time in the gold refining industry. The process consists of chlorine addition into the molten Dore by using an immersed tubing system. Initially there is a slow reaction of chlorine gas with base metals forming volatile compounds. Once is complete the initial reaction, there is a fast generation of non-volatile compound called Miller Salt that must be removed from the surface of the molten charge. It is important to avoid the formation of gold chlorides in order to avoid losses. One solution is to the problem is to cover the molten charge with mixture composed by borax and silica. The end of the process is noted when appear purple fumes of chloride gold. Platinum group metals are not removed and gold purity is between 99.5 to 99.8%. Although this technique is old, the process has to be operated by skilled workers and the facilities must have an excellent exhaust system in order to avoid contamination by chlorine.
Other process used for a long time is the Wohlwill Process and is considered as the second part of the Miller process due to refine its product. This is an electrolytic process based on the dissolution of gold in an acid bath prepared with chlorine gas and hydrochloric acid. The final product is a gold cathode with 99.99% purity. Although the process is efficient, there is an issue related to the cost due to it is necessary to heat and apply a specific current density such as 110 amperes per square foot. Platinum group metals and silver are reported on anode slimes and the remaining base metals are in solution.
Wohlwill Process
The Fizzer Cell Process is an improved Wohlwill Process whose main change is the cathode design. There is a porous ceramic container that works like a membrane whose purpose is to avoid gold losses and adhesion of some impurities on cathode surface. The electrolytic cell is drained and filtered. A very important aspect of this process is referred to the possibility of treating impure anodes, basically when the silver content is as high as 10%.
The Aqua Regia Process is appropriate to be employed in small scale and the metallic gold to be obtained is as pure as 99.9%. The main steps of the process are to dissolve the precious metals and some impurities. Since the Aqua Regia is a mixture between nitric acid and hydrochloric acid, part of the silver will remain in solution and other part will form a silver chloride precipitate. Then, it is important to be careful with the silver content. It must be mentioned that the silver chloride formation has a negative effect on gold dissolution. Once the dissolution is performed, the solution and the precipitate are separate by filtration operations. The solution contains gold and is treated with reducing agents such as ferrous sulphate, sulphur dioxide or sodium bisulphate. Gold powder of high purity is obtained and can be melted later. When gold precipitates, platinum group metals remain in solution and have to be recovered by other procedure.
Gold Assay
Metallurgical processes need to know the metallic content of the different products obtained in recovery and refining processes. If we have to know about gold assay, it is important to mention the Fire Assay Process that has been employed in the mining industry for a long time. Basically the ore is mixed with a mixture of fluxes and during the smelting process precious metals are liberated and most of heavy metals are trapped by the fluxes. However, lead is the key element due to collect precious metals. The latter product is reprocessed by a cupellation stage so that we can have a gold-silver alloy that will be leached selectively to calculate the gold content.
Furnace Crucible Cupel
One aspect very important is to know the minerals present in the sample to be assayed due to they have influence on the flux to be added. Obviously, this knowledge is fruit of experience and study. Basically, minerals can be identified by specific gravity, color, streak, luster, hardness, magnetic susceptibility, and reaction with any special reagent such as hydrochloric acid. The number of minerals is large and assayers have to be focused in the main minerals such as sulphides or sulphides. Carbonates react easily with nitric or hydrochloric acid and this is a common characteristic of alkaline samples.
A good procedure to estimate the minerals is to perform a gravimetric separation by using a watch glass or a curved plate. This procedure is called vanning. In this case, is necessary to take 10 to 30 g of sample and mix it with water in the watch glass. The idea is to separate minerals according to their specific gravity like a panning gold operation. Heavy minerals stay in the center and the lighter minerals at the border. When the vanning is well done, it is possible to identify minerals of different color and densities due to they are distributed in different zones. The size of these zones will tell us the main minerals and the possible nature of the sample.
Identifying Minerals by Vanning
Flux
This is a substance added to a material to aid in its fusion. Other action is to act as a reducing agent to dioxide or decompose impurities and remove them as slags. In this way, we can insure complete decomposition of the ore. One of the components is a lead oxide that is reduced to metallic lead. This metallic element collects gold and silver. The weight of flux is 25 grams. Basically, the flux must be able to control viscosity, degree of acidity, change the melting point of the ore and decompose the ore. The main fluxes are listed below:
• Calcium oxide. This is an alkaline flux that modifies the viscosity and fluidity of the charge. Also reacts with alumina.
• Lead oxide. Litharge is the yellow lead monoxide is a desulphurizing flux and provides lead to the process.
• Potassium carbonate. Is employed with sodium carbonate in order to modify the melting point of the sample.
• Sodium carbonate. This flux can be added alone or not and its main action is to react with sulphides. Kt can be replaced with sodium bicarbonate.
• Borax. This is an acid flux and is appropriate to separate metallic oxides. If the addition is excessive, part of gold will be lost and the remaining part reacts with alkaline fluxes.
• Silica. This is other acid flux that changes the melting point. Excessive addition creates a molten charge with excessive viscosity.
• Fluorspar. This a neutral flux that improves decomposition and fluidity. Refractory ores needs fluorspar to avoid gold losses.
• Sodium nitrate. It is an oxidizing agent whose addition is oriented the oxide base metals. Excessive addition changes dramatically the lead button size.
• Reducing agents. They help to convert lead oxide to metallic lead. There are several types of reducing agents, some of them are flour, and charcoal.
The weight of sample is based on the called one-assay ton (29.166 g). Laboratories normally employs one assay ton, and other half assay ton. Obviously, the experience is the best tool to estimate the weight. The fluxes to be added are the remaining part of the charge. The mixture of fluxes must contain lead oxide and sodium carbonate. Typically the lead bottom weight is between 18 to 25 grams. The other fluxes are added is minor proportion. The main criterion is to consider the weight of metallic lead to be produced; otherwise there will be more than one problem with the Dore metal obtained at the end of the process. The oxidizing and reducing properties of the sample have influence on the lead button weight. Some minerals such as hematite, magnetite and pyrolusite have direct influence on oxidizing properties. Similarly, galena, chalcocite, chalcopyrite, pyrite, sphalerite and arsenopyrite change the reducing properties according to its sulphur content. It means more sulphur content, more reducing power.
A recipe can be composed of 25 g litharge, 20 g sodium carbonate, 1 g flour, 8 g silica, and 25 g ore sample. This proportion can work for a neutral ore and the components can be modified in order to test other samples. The lead button is the best proof of the mixture fluxes efficiency.
Black sand samples must follow a special smelting procedure due to they are difficult to melt at common temperatures. The fluxes to be used must be chosen with detail in order to avoid wrong results. The sample preparation is other problem since these materials contains free gold. A good recipe has the following composition, 30 g litharge, 30 g sodium carbonate, 25 g borax, 5 g flour, 8 g fluorspar, 30 g silica and 20 g ore sample.
Adding fluxes Mixture non-homogeneous
Melting Gold
First and foremost the crucible (scorifier) must be preheated, and then add the mixture sample-fluxes. Ore sample and fluxes melt at different temperatures and the order of these reactions has a very important role in the efficiency of the process. Once the charge is totally melted, it is important to add 15 to 30 more minutes in order to assure a good diffusion of the button and precious metals collection.
When temperature is near 550 oC, lead metal is formed from a reaction between lead oxide and flour. The charge forms a porous mass with borax and sodium carbonate. Sulphides react with carbonates and forms alkali sulphates that replaces gold in the crystalline structure. Borax melts at 740 oC and reacts on metallic oxides. At 850 oC, sodium carbonate is melted and reacts with silicates. Since part of the lead oxide was not smelted, when temperature reaches 885 oC, all the lead is transformed in oxide. At this moment the remaining free gold and silver particles are collected and go to the bottom of the crucible. The final point is near 1068 oC and is expected that all the reactions are complete.
Crucibles must be preheated
There are several factors that affect the efficiency of the melting process. Some of them are the following: ore sample particle size must be very fine in order to have the right surface area and the reactions can be favored. Then, the ore must be pulverized in the right way. Other aspect is the right addition of fluxes. If they are not in the minimum amount, reactions will be completed and some of gold and silver will be trapped into the slag. The excessive addition of fluxes is not a good choice due to melting of the charge and the lead metal formations are under different phases. This situation creates losses of gold and silver. The temperature must increase its value in the proper way. It means if the final is reached very fats, the reactions are not complete and lead metal is formed to fast without having enough time to collect precious metals. In order to assure the right order of reactions, the sample and the fluxes have to form a homogenous mass without segregations. The contact between ore particles and fluxes is very important.
Introducing crucibles into the furnace
During the melting process is expected to obtain several layers of different material due to reagents have different solubility and density. Under this consideration, at the top there is an alkali layer composed oxidized sulphides (sulphates). The following stratus is formed by heavy metal oxides and chemically is a borosilicate. This layer must not be thick or lumpy; otherwise some minerals will not be dissolved and melted. The balance of silica and borax is very important. Sometimes, there is a matte layer and is produced when the flux is inappropriate. This layer is composed by lead, zinc, iron and copper sulphides. Also, when the flux was selected wrongly, some compounds of arsenic and antimony with iron and copper are formed. This layer is called speiss. At the bottom is located the lead button with gold and silver.
Slag appearance is a good indicator of the process. Although iron minerals have influence on color slag, it is possible to draw some conclusions according to the color. For example, a blue color is symptom of copper minerals. The presence of manganese minerals is note for a lavender color slag. Green is synonymous of iron minerals and most of slags present this color. If the iron minerals are not a very important part in the sample, a yellow color indicates presence of lead and a white color is typical of silicates of calcium or magnesium.
Pouring molten charge Slags
Cupellation
This is an oxidizing process that must separate lead metal and precious metals. The lead button obtained is placed in cupels that absorb lead oxide. The process is based in the fact that lead can be oxidized at high temperatures and precious metals no. under this consideration, the separation is possible. The initial temperature is 860-880 oC and the final is at 900-920 oC. Cupels must be capable of resist high temperatures, absorb oxides, but no liquid metals. Typically, cupels are fabricated with magnesia, calcium sulphate, lime and clay, and a mixture between calcium sulphate and lime-clay.
The initial step is to preheat the cupel at 860 oC. Then the lead button is placed on the cupel and after 30-40 minutes the oxidation and absorption process is complete. During this process is necessary to check the temperature and the lead button condition. The final point is obtained at 900 oC. When the cupel is cooled, the surface condition around the Dore metal let us know if the smelting process was performed efficiently. For example, cracks mean an excess of antimony, residual slag is an indication that lack of cleaning, and stains are sign of impurities.
Gold-Silver Separation
The initial step is to weight the Dore metal. Since silver is leached by nitric acid and gold no, the next step is to attack the Dore metal with a hot diluted solution of nitric acid. The acid dissolves the silver and leaves the gold that has to be rinsed, dry, and weight on a scale of high sensibility such as 0.001 mg. We need a capsule to perform the acid attack.
HNO3 Capsule
The gold content is expressed in ounces per ton (oz/t). With the sample weight and gold metal weight can be calculated the proportion of gold in the sample.
Gold content (oz/t) = gold weight (mg) x [29.166/sample weight (g)]
Gold Refining Book
For example, if the fire assay reported 0.1 mg of gold and the initial weight of sample was 20 g, the gold content is 0.14583 oz/t or 4.54 g/t.