Table of Contents
Concaves on the right illustrate the cross section of a typical gyratory crusher, while the left illustrates the same crushing chamber, except that, in place of the straight-face concave, the non-choking type has been substituted. For the sake of direct comparison we have shown the same discharge setting in both diagrams, although a closer setting would be permissible for the non-choking arrangement.
Inasmuch as the eccentric-throw is the same, and the concaves in the upper part of the chamber parallel those of the standard type, it follows that the successive drops of the material in this zone would be similar. This is true down to line 13. Then we note a difference in the new diagram; the drop per stroke increases much more rapidly than in the former case until, at stroke 16, the line has arrived at the discharge level.
The choke-point has been raised to point 13-14, instead of being at the discharge level. From the choke-point, on down to the discharge level, each successive volume is greater than volume 13-14, and greater than the volume immediately preceding. Therefore, the shape of the crushing chamber in the zone below the choke-point is favorable to choke-free operation. Under certain conditions choking can occur in this zone, however, as will be pointed out later.
https://www.911metallurgist.com/secondary-gyratory-crushers
The ratio-of-volume-reduction between volumes 0-1 and 18-19 in the figure previously discussed is obviously greater than the ratio between volumes 0-1 and 13-14 in the non-choking diagram; actually the ratio in the former case is about 4:1, and in the latter about 1.75:1. Therefore, if we assume an equal percentage of voids in the feed for both cases, it is apparent that the non-choking arrangement will not, when the choke-point is reached, have compacted the material to as low a percentage of voids as the straight-face chamber. Also, the actual volume of 18-19, in the standard chamber, is substantially smaller than that of 13-14 in the non-choking chamber. Inasmuch as these volumes pass the choke-point in the same time-period, the gyratory crusher capacity through the 13-14 zone is obviously the greater of the two.
These two facts account for the superior performance of the standard gyratory and the standard jaw crusher when fitted with non-choking liners. As compared with the straight-face concaves, the salient features of the non-choking variety are:
- They permit the use of smaller discharge settings in any given size of crusher.
- Capacities are considerably higher, particularly so in the range of finer settings.
- Wear of crushing head and concaves is more evenly distributed in the lower part of the crushing chamber.
- The receiving opening is reduced, the amount of this reduction depending upon the crusher setting, and upon the degree of curvature of the concave faces.
- The ratio-of-reduction in the different sizes of standard crushers varies from about 6.75 to 9.5, averaging about 7.9 for the sizes mentioned previously. This is also based upon the use of standard-throw eccentrics.
- The crusher product is more uniform, and will generally contain less fine material.
- Power requirements are very definitely in favor of the non-choking concaves.
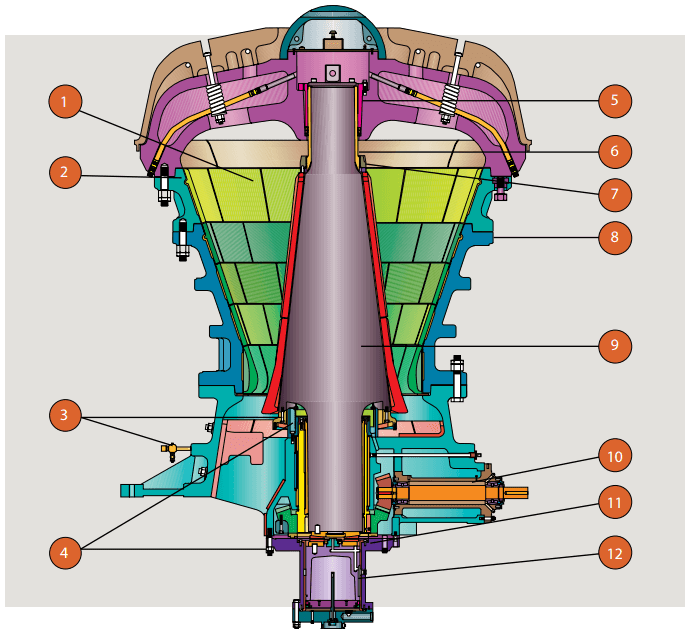
It is obvious that this type of concave has some very desirable features. As a matter of fact, the development of scientifically designed, curved profile crushing surfaces is probably the most important single improvement ever made in pressure-type crushers. The relative performance of non-choking concaves in the standard gyratory crushers is graphically illustrated in the table below. This table contains a complete list of capacity ratings for gyratory crushers, from 8 to 42″ inclusive, for straight-face, and non-choking, concaves.
This table also lists “Modified Straight Concaves.” These are concaves having a lesser curve at the bot-tom partly approaching the non-choking concaves but having the choke-point at the bottom of the chamber. They are used where the open-side setting is large enough to permit the use of straight concaves, but where some of the advantages of non-choking concaves are desired. These include increased capacity, more uniform sizing and the distribution of wear to prevent “belling” of the head.
It should be made clear at this point that these concaves, although they bear the title of “non-choking,” do not afford absolute insurance against choking. In that respect the title is perhaps a trifle misleading. The very fact that a choke-point exists at all within the crushing chamber makes it evident that choking can occur. On the other hand, they do minimize the danger of choking, and their general characteristics are such that their descriptive title is not too far afield.
Concave Materials
Concaves can be cast from a variety of ferrous materials, but the choice usually falls into one of three fundamental alloy categories: austenitic manganese steels, martensitic steels, or martensitic Cr-Mo or Ni-Cr (Ni-Hard) white irons. The terms “austenitic” and “martensitic” refer to the crystalline structure of the predominant constituent (phase), either austenite or martensite, present in the microstructure of that particular type of steel or white iron. Martensitic white irons can be thought of as composite materials containing substantial amounts (typically ranging between 20% and 40% by volume) of very hard carbides surrounded by a matrix of martensitic steel.
The aforementioned structures are produced by melting and casting an alloy of suitable chemical composition and then applying an appropriate heat treatment. For details, the interested reader may refer to numerous published accounts that provide typical chemical compositions, heat treatments, and production practices along with the resulting microstructures, mechanical properties, and wear characteristics (Anon., 1956; Anon., 1962; Fabert, 1974; Tasker, 1982; Diesburg and Borik, 1974; Dodd, 1977; Dodd and Parks, 1980).
The generalization that higher hardness equates to better wear resistance appears to be substantially correct for ferrous alloys used for gyratory crusher concaves. If wear is broadly defined as “metal removal,” two of the three principal components of wear, metal-to-metal impact and corrosion, are largely absent, leaving abrasion as the primary means of metal removal. Laboratory and field tests have consistently ranked alloys from the three categories used for concaves in the following order of increasing abrasion resistances austenitic manganese steels, martensitic steels, and martensitic white irons.
The austenitic microstructure exhibited by manganese steels is relatively soft, around 200 Brinell hardness, but under the right conditions it can work harden to hardness values in excess of 500 Brinell. In concaves, however, the right conditions for maximum work hardening apparently are not achieved consistently. On the other hand, martensitic microstructures will exhibit high hardness, up to 600 Brinell in concaves, simply by virtue of having been heat treated. Work hardening by impact or abrasion is not needed to develop high hardness. The carbide phases in white irons typically exhibit about twice the hardness of martensite.
Among the three alloy categories, the most widely utilized grades of austenitic manganese steel have enormously better impact toughness (resistance to fracture) than alloys from the other two categories. Measured by standard laboratory testing of samples from commercially important section sizes, austenitic 12% Mn steels will typically exhibit five to ten times more impact toughness than martensitic cast steels and as much as 40 times more toughness than martensitic Cr-Mo and Ni-Cr white irons.
On the other hand, austenitic manganese steels exhibit relatively low yield strength, typically one-third that of martensitic steels. As a result, manganese steels are much easier to plastically deform in service. In concaves, plastic deformation, or “growth” as it is often described, will manifest itself as peened over gaps between concaves.
Manganese Steels
The original patent issued to Hadfield in 1883 listed manganese contents ranging from 7% to 20%, but the first commercial grade contained 1.2% C and 12.5% Mn and was water quenched from 1310°K, essentially the same as the grade most widely utilized today. Over the years, incremental improvements have been made in foundry processing, heat treatment, and understanding the role of both potentially beneficial alloying elements as well as potentially harmful residual elements. Together, these improvements allow Hadfield’s manganese to be reliably manufactured in heavier section sizes.
Modified grades containing nominally 6% to 7% Mn, the so-called “lean manganese” steels, provide somewhat better wear resistance but lower impact toughness than conventional 12% Mn grades. Despite having lower toughness than 12% Mn grades, the lean manganese steels are still considerably tougher than martensitic steels. Problems have been experienced in very cold climates; low temperature can actually cause a metallurgical transformation of austenite to martensite, producing a marked degree of brittleness.
Higher carbon, higher manganese grades containing 1.3% to 1.8% C and 15% to 25% Mn have demonstrated better wear resistance than 12% Mn grades in laboratory wear tests, but mixed results have been obtained in actual field tests. They are reported to be cost-effective in some cone crushing applications. Several patented or proprietary grades are on the market.
Martensitic Steels
ME International produces concaves from several proprietary grades of martensitic cast steel. The exact composition and heat treatment are tailored to produce the desired combination of abrasion resistance and impact toughness for the specific application, e.g., upper row concaves that must withstand impact or lower row concaves that require maximum abrasion resistance. Carbon content, which can be within the range 0.3 to 0.5%, controls maximum obtainable hardness of the martensitic microstructure and impact resistance. Alloying elements like Cr, Mo, and Ni are added primarily to control hardenability — the ability to obtain a fully hardened martensitic microstructure throughout the section size.
Martensitic White Irons
In terms of concave wear life, there is little doubt that heat treated martensitic Cr-Mo and Ni-Cr (Ni-Hard) white irons will outperform martensitic steels and austenitic manganese steels. Extensive laboratory-scale abrasion testing as well as several reported field trials have shown that white iron is two to three times more abrasion resistant than either type of steel. However, the question of reliability still remains. Does white iron have adequate toughness to provide dependable service in a machine that in many cases is the only conduit for ore into the concentrator and where failure of the concaves can result in shutdown of the entire plant? Generally the answer is no, but white irons are being used successfully in large primary crushers in a few special applications.
White iron concaves reinforced from within by an internal steel skeleton are also available. “Nordite” concaves from Rexnord were the first commercially available products (Hegmegee, 1974), but white iron concaves based on the same principle are now available from other suppliers. The reinforcement is not intended to prevent breakage but rather to prevent broken pieces from falling out.
Hardfacing
One way to obtain the wear resistant qualities of white iron while minimizing the risk of catastrophic failure is to apply hardfacing to austenitic 12% Mn steel concaves. Many alloy compositions applied by hardfacing are metallurgically similar to Cr-Mo irons produced as castings, and they exhibit similar microstructures and wear rates. The Climax Mine has reported good success with this method (Dunn, 1982). The major drawbacks of hardfacing are that it is very expensive to apply, even with modern and highly automated bulk welding processes, and that only a relatively thin (about 25-mm thick) veneer of material is applied.
Composite Approach
Concaves made from different alloys can and in many cases are used for each row or even within a given row to achieve the desired wear resistance or impact toughness. For example, lower-carbon martensitic steels can be specified for the rows that are subjected to the greatest impact from rock being dumped into the crusher and higher-carbon martensitic steels for the rows that experience the greatest wear. A crusher fed by an apron feeder might use martensitic white iron concaves under the feeder and martensitic steel concaves in the rest of the upper row(s). Under certain circumstances, materials from all three of the fundamental alloy categories might be utilized: austenitic manganese steel for the upper row(s), martensitic steel for the middle row(s), and martensitic white iron for the lower row(s).