Table of Contents
The general procedure is as follows. The sample is placed in the liquid of lowest specific gravity and is split into two fractions. The float fraction is set aside to be weighed and assayed. The sinks fraction is washed in a suitable solvent, dried and placed in the liquid of a higher specific gravity. This process is continued in steps of suitable S.G. differences until a small final sinks fraction is obtained. This is also dried, weighed and assayed.
After assaying the fractions for metal(s) content, the distribution of material and metal in the density fractions of the sample can be tabulated as in the table below:
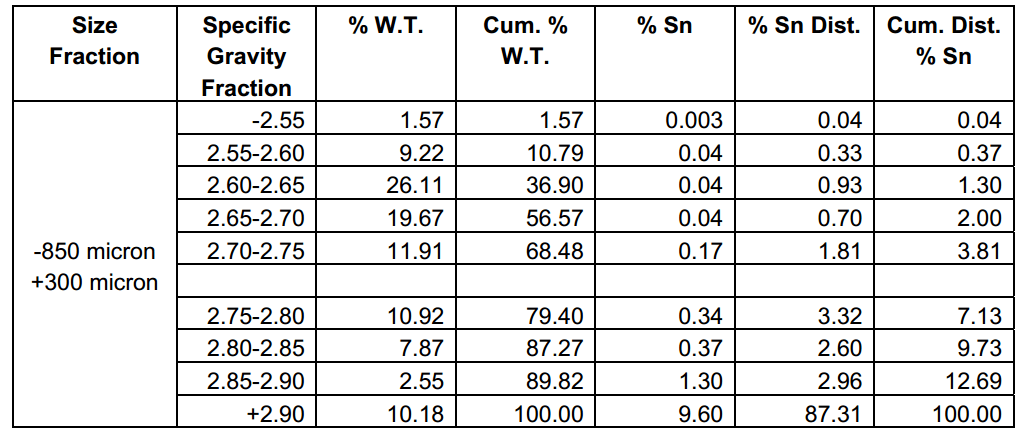
This data is presented in aĀ Tromp Curve Example (AKA Partition Curve).
Heavy Liquid Separation
Heavy liquid techniques for the separation of minerals with organic liquids were developed in the laboratory many years ago. More recently, the laboratory use of heavy liquids in the separation of minerals has been reported. The nearest approach to commercial success in the use of heavy liquids has been reported by Foulke. The Weston Coal Company at Shenandoah, Pa., in cooperation with E. I. du Pont de Nemours & Co., Inc., installed a commercial size plant for the sink-float treatment of coal. After a short period of operation the plant was closed.
The use of a heavy liquid with uniform chemical and physical properties potentially offers the best method for gravity separation of fine particles of relatively close specific gravity. The primary reasons that organic heavy liquids have not been commercially used widely are that they are expensive and a fully effective or cheap method for their recovery from mineral particles has not heretofore been developed. New and improved heavy liquid recovery systems are under consideration with present emphasis on solvent extraction, thermoevaporation, and water washing.
Although experience with heavy liquids in industry has not been completely successful it has demonstrated the need for such a process proven its technical feasibility, and examined some of its economic aspects. The brightest prospects appear to be the direct concentration of minerals to yield marketable products or preconcentration of ores ahead of a final separation. However, the ultimate commercial use of heavy liquid separation (HLS) will depend strongly on process economics and continuing research.
Relatively few research programs have dealt with the different aspects of the heavy liquid mineral concentration. Interest is presently centered around adopting fluid cyclones to the process. Hydrocyclones are a recent innovation in the industry; the cyclone classifier was introduced to this country about 15 years ago. Since this time, engineers and scientists have initiated numerous practical applications and academic studies using cyclones. Although many generalities on hydrocyclone classification were established, these investigations have not formulated any universally accepted cyclone theories.
In the past ten years, cyclones have evolved from classifiers to concentrators. The research and development staff at the Dutch State Mines were the first to adopt the cyclone to heavy media separation (HMS). Previous heavy media separations were limited to plus 4-mesh ores but with the introduction of the HMS cyclone, ores down to about 14 mesh can be processed. HMS cyclones are now used extensively in some coal preparation plants and iron ore concentrators. Because of the short time in operation, little information is avail¬able on the heavy media cyclone beneficiation of ores.
Published data on the subject of heavy liquid cyclone concentration are limited since HLS research investigations are rare. Therefore, the scope of this paper is intentionally limited to a portion of the process and its purpose is directed toward the practical cyclone application of HLS. A concentrated effort is placed on a few of the more important factors, including (1) cyclone feed pressure, (2) cyclone feed density, (3) feed grade, (4) particle size, and (5) cyclone construction. Both single-stage and multistage cyclone systems were studied to demonstrate the flexibility of the process.
Research is in progress to study methods of separating fine-ground minerals by sink and float in organic heavy liquids and to develop new and improved methods for recovering the heavy liquids from mineral particles. Reports covering various aspects of these investigations will be issued as the studies progress.
Description of Materials
Ore
Spodumene (Li2AlSi2O6) is an aluminum silicate mineral which theoretically contains 8.1 percent lithia, 27.4 percent alumina, and 64.5 percent silica. Although the theoretical lithia content of spodumene is 8.1 percent the content of commercial material usually ranges from 5 to 7 percent. Almost all spodumene is sold through private contracts as ore concentrates containing 80 percent spodumene or higher at a price between four and five dollars per unit of LiO2. The domestic indicated and inferred ore reserves which contain one percent lithia or more are estimated at 1.4 million tons of LiO2 and for the present are adequate to meet the market demand anticipated from the chemical and space industries. Ore deposits are generally found in granite pegmatites and associated with quartz, feldspar, mica, and often beryl. Although trace amounts of heavy minerals are sometimes present in the ores, spodumene with a specific gravity of 3.1 is significantly heavier than the major gangue minerals whose densities range between 2.5 and 2.7. Preliminary tests revealed that this type of ore is well suited for beneficiation by heavy liquids.
A composite sample of spodumene ore was obtained from the Kings Mountain region of North Carolina. A description of the ore is given in table 1, including the size distribution, mineral composition, and chemical analysis of the test sample. Petrographic examination showed that the spodumene crystals were completely liberated at all sizes.
Heavy Liquid
Prior work on heavy liquids has shown tetrabromoethane (TBE), also known as acetylene tetrabromide, to be suitable for the separation of a variety of minerals and is adaptable to the types of liquid recovery schemes that have been proposed for natural ores. Spodumene has been separated from its gangue in the laboratory using pure tetrabromoethane and was selected for this investigation because it represented the simplest heavy liquid system with commercial potential.
One of the more common heavy liquids, TBE is domestically priced at about 65 cents per pound. Large-scale production from the Dead Sea brines by the Israel Mining Industries has implied that a price of 20 cents per pound is possible with a large industrial demand. When pure, it is colorless, nonflammable, relatively stable, immiscible with water, and has a specific gravity of 2.96. The important properties of 1,1,2,2 tetrabromoethane (C2H2Br4) are given in table 2.
Acetylene tetrabromide is toxic and hazardous, and heavy liquid separations should always be made under a well-ventilated hood. The fumes of the liquid should not be breathed nor the liquid allowed to contact the skin. Information regarding the toxicity and hazards of the liquid is quoted from Patty:
The threshold limit of acetylene tetrabromide was established by the American Conference of Governmental Industrial Hygienists, In April 1959, at 1 p.p.m. (14 mg./cu. meter).
Acetylene tetrabromide is a central nervous system depressant. If given in sufficiently large doses, it may cause narcosis and coma, and eventually death from respiratory failure. There is lung irritation and pathological changes are observed in the liver and kidneys.
As the vapor pressure is exceedingly low at room temperatures, the material may be easily handled with reasonable precautions and ordinary ventilation.
Ordinary contact with the open skin does not result in any skin reaction if it is washed off in a reasonable period of time. If the material is bandaged into the skin and allowed to remain there for a period of hours, a slight redness will appear. In 24 hours, there will be some edema and blistering. It can be concluded that ordinary contact would not represent a skin problem. However, clothing or shoes that may contain the material should be removed and cleaned before reuse.
The Bureau of Mines is working in conjunction with the U.S. Public Health Service to develop safety precautions and methods of overcoming toxic conditions when using heavy liquids. Results of this work will be reported in a later publication.
Apparatus
Figure 1 depicts the 0.4-inch diameter cyclone which was used in this investigation. The unit was designed after a typical commercial model with modifications and improvements to better fit the application. The different parts were made interchangeable, with various size openings of the vortex finders, apex, and feed inlet in order to permit maximum flexibility when studying these parameters. The cyclone size limited the maximum particle size that could be tested to about 28 mesh and set the minimum operating pressure near 20 psig. For durability the cyclone components were molded out of a non-porous, wear-resistant ceramic material, AlSiMag 614 because high feed pressures were anticipated and spodumene is abrasive. A stainless steel mount held the cyclone together. Figures 2 and 3 show a closed and exploded view of the unit.
Figure 4 shows the closed-circuit, semicontinuous cyclone rig in which tests were conducted. The unit was constructed for use with either one cyclone (single-stage separation) or for two cyclones in series (two-stage separation). Because the feed pulp was under high pressure and the liquid was toxic, the cyclone was totally enclosed in a vented housing to protect the operator. The outside housing was fabricated from stainless steel, and the entire unit was coated with a corrosion resistant epoxy paint. A positive displacement stainless steel Moyno pump with a butyl rubber stator was mounted with a variable speed Vickers hydraulic transmission drive to control the cyclone feed pressure and pulp flow. Pressure settings were maintained within ±2 psig by inserting a standpipe reservoir in the feed line to level out any pump surges. A laboratory mixer was installed in the sump box to prevent the test sample from stratifying. Figures 5 and 6 are photographs of the unit.
Procedures
Experimental
Prior to running a series of tests, the cyclone was mounted with the appropriate vortex finder and apex disk. Because the small openings in the cyclone components limited the maximum particle size which could be tested without plug-ups, the ore was rescreened at 35 mesh to remove any tramp over¬size particles. A predetermined quantity of ore was added with enough tetrabromoethane to obtain the desired pulp density, and the slurry was mixed in the sump box. The feed pressure was adjusted by means of the variable speed drive of the pump and the pulp was recycled through the cyclone until conditions came to equilibrium. The cyclone throughput rate at various pressure settings is given in table 3. Ideally the heavier spodumene particles are thrown against the cyclone’s conical sides and out the underflow apex while the lighter tailing gangue is swept out the cyclone overflow through the vortex finder.
Samples were taken of the pulp flows from the cyclone for evaluating the process. The pulp samples were weighed, filtered to recover most of the TBE, washed with triehlorethylene to remove the remaining heavy liquid, and dried in a hooded oven. The dry samples were weighed and analyzed for their spodumene content. From this information the distribution of the pulp and solid flows were determined, the pulp densities were calculated, and the efficiency of the spodumene separation was computed. The cyclone feed analysis was calculated from the products and checked against the original feed sample.
Analytical
Sink-float methods for estimating the percent spodumene in a product has been used for some time in commercial production plants for control purposes. For simplicity, speed, and economy, all the samples were analyzed by sink-float methods using pure TBE at a density of 2.96. Petrographic examination of the ore showed that only trace quantities of minerals other than spodumene existed in the sink fraction, and it was considered to be 100 percent spodumene.
Standard sink-float centrifuge procedures were used. Approximately 10 grams of the material was cut from each cyclone product sample, and was placed in 50-milliliter conical tubes together with 25-30 milliliters of TBE. The samples were stirred with a small glass rod and the sides of the tubes were washed down with a small quantity of the heavy liquid. The tubes were then placed in a laboratory centrifuge, and whirled at a speed of about 3,500 peripheral feet per minute for 10 minutes. The tubes were removed from the centrifuge and the stratified mineral layers were again stirred to release any mechanically entrained particles. The tubes were replaced in the centrifuge and whirled again for 10 minutes at the same speed. The sink and float fractions were removed from the centrifuge tubes, filtered to recover the tetrabromoethane, washed several times with trichloroethylene to remove the remaining heavy liquid, and dried in a hooded oven. The percent sink was calculated from the weights of the two products and reported as percent spodumene..
Although this investigation is based on spodumene concentration, it is noteworthy to mention that a mathematical correlation was obtained by Browning and Gayle between the usual chemical determination of Li2O and sink-float results. They proposed the following equation for estimating the lithia composition of spodumene products from sink-float analysis:
Percent Li2O = 0.0757 (percent sink at 2.96 specific gravity).
Data Evaluation
In almost any process the efficiency of the system is a function of three criteria: (1) The quality or grade of the product, (2) the quantity or recovery of the product, and (3) the resultant cost of obtaining these first two goals. The concentration of spodumene by heavy liquid cyclones is no different, but in a pioneering research program the monetary aspect of the problem must be minimized in order to reveal a broad view of the process over a wide range of conditions. Nevertheless, it is important that the economical limitations of the system are kept within the scope of the investigation.
Whenever possible the tests were carried out until the maximum recovery and grade were determined. But often the conditions required to obtain these two optimum values were not identical, and usually the means of increasing the recovery subsequently resulted in decreasing the concentrate grade or vice versa. Here it became necessary to establish arbitrary efficiency standards based on practical judgment. In this instance it was assumed the concentrate must contain at least 85 percent spodumene to be marketable, and the recovery must be above 85 percent for the process to have any economical consideration. Throughout this report, an 85/85 result is termed the minimum acceptable separation standard.
A Study of the Influence of Particle Size, Feed Density, and Feed Pressure
This test series was to attain the maximum HLS at the lowest probable cost by coordinating the cyclone feed pressure, feed density, and mineral particle size. Cyclone construction remained constant with a 0.11-inch apex opening and a 0.08-inch vortex finder.
One of the prerequisites for effective ore concentration is the liberation of the different mineral components. The separation of the pure mineral crystals often necessitates grinding the ore to extremely fine sizes, but every attempt is normally made to minimize grinding, as it is usually the highest single cost operation in beneficiation. Although the spodumene in this particular ore liberates in the coarse mesh fractions, the effect which particle size has upon heavy liquid cyclone separation at different feed pressures and pulp densities was investigated. For this study, the ore was screened and separated into five closely sized samples: (1) 45 x 65 mesh, (2) 65 x 100 mesh, (3) 100 x 200 mesh, (4) 200 x 325 mesh, and (5) minus 325 mesh. All the samples contained approximately 20 percent spodumene.
A large quantity of liquid stored in a HLS system entails a considerable capital investment and the greatest quantity of solids handled in the smallest amount of liquid represents the most economical condition. Tests were conducted on the ore samples with different pressures at 5, 10, 15, and 25 per-cent solids to determine the maximum feed density the cyclones could operate without an appreciable loss in efficiency.
Feed pressure is known to affect cyclone performance; but it is desirable to keep this as low as possible because operating costs rise rapidly with increasing pressures. Pressures between 20 psig and 100 psig were tested to optimize separation with pressure.
Figures 7, 8, 9, and 10 summarizes the relationship between cyclone pressure, particle size, and feed pulp density to the grade of the concentrate and the mineral recovery.
Effect of Particle Size
The 48- x 65-mesh spodumene sample responded best to heavy liquid cyclone separation and produced the highest concentrate grade with the greatest recovery. At 5 percent solids, the concentrates contained approximately 95 percent spodumene with recoveries exceeding 95 percent when the feed pressure was over 50 psig. Although tests using all four pulp densities yielded good results, to maintain an 85-percent concentrate with an 85-percent recovery, it became necessary to step up the pressure as the pulp density was increased. For instance, to make this separation the pressure had to be above 60 psig at 25 percent solids but only 20 psig at 5 percent solids.
The 65- x 100-mesh ore test results showed that the average concentrate grades and recoveries were about 13 percent and 5 percent lower than the corresponding results using the 48- x 65-mesh ore, respectively. Ninety percent
concentrates were achieved with 90 percent recoveries when the pressure was above 70 psig and the pulp density was 5 percent solids. At 5, 10, and 15 percent solids, acceptable concentrates and recoveries were produced, but the minimum cyclone pressure was greater than the pressure needed to obtain similar results with the 48- x 65-mesh sample. An 85/85 separation was not obtained at 25 percent solids as the improvement in separation caused by higher pressures could not overcome the drop in efficiency caused by the increased feed density.
The particle size effect on HLS separation was more pronounced with the 100- x 200-mesh ore. Neither 90 percent concentrates nor 90 percent recoveries could be made under any of the conditions tested and only at the topmost feed pressures and lowest pulp densities were 85/85 separations attained. At 15 percent solids the best grade and recovery was only 80 percent and at 25 percent solids the concentrate grade was only 50 percent. When compared to
the 48- x 65-mesh ore test results, the average grade had fallen about 25 per-cent and the average recovery had dropped 14 percent.
The ores below 200 mesh did not respond satisfactorily to heavy liquid cyclone concentration. In these samples, the influence of cyclone feed density was almost completely obscured and the effect of feed pressure was substantially reduced.
Effect of Pulp Density
Regardless of the particle size, the best heavy liquid cyclone separation occurred using the lowest feed density. At 5 percent solids the 48- x 65-mesh, 65- x 100-mesh, and 100- x 200-mesh ores produced 85/85 spodumene separations with minimum pressures of 20, 40, and 70 psig, respectively. Beneficiation of the 200- x 325-mesh and the minus 325-mesh ores was unsatisfactory at any pressure.
When the pulp density was raised from 5 to 10 percent solids the cyclone selectivity dropped slightly. This decrease was not enough to warrant any serious concern as the average grade and recovery was only about 4 percent lower. At 10 percent solids the minimum acceptable separation standard was met on the plus 200-mesh ores but the minus 200-mesh samples were not amenable to cyclone concentration.
The cyclone results were noticeably lower when the pulp density reached 15 percent solids. Comparing test results at 5 percent solids and 15 percent solids, the average grade and recovery diminished approximately 10 percent using the higher feed density. To yield an acceptable separation at this density the pressure had to exceed 40 psig with the 48- x 65-mesh ore and 90 psig with the 65- x 100-mesh ore. The minus 100-mesh samples did not meet the prescribed concentration standards.
At 25 percent solids the shape of the recovery curve changed; instead of a recovery maximum, a point of inflection developed followed by a continuing increase in recovery. This leads to the supposition that the pulp changed to a more fluid state at this pressure. Nevertheless, even with high feed pressures the efficiency of the best separation was so poor it is not practical to consider heavy liquid cyclones at this density. Only the 48- x 65-mesh ore significantly responded to HLS separation.
Effect of Feed Pressure
As the cyclone pressure increased the separation efficiency increased to a maximum value where pressure has little additional effect. The maximum concentrate grade and recovery depended upon both the mineral particle size and the cyclone feed density. Pressure had a stronger influence on concentrate grade than on recovery and under a given set of conditions the maximum recovery would be attained at lower pressures than the maximum grade. Thus, for an 85/85 separation the concentrate grade dictated the cyclone operating pressures.
At the low and high pulp densities, the pressure was less effective in improving the separation. This relationship between feed pressure and these densities is twofold. In one case, 5 percent solids, the response to pressure was rapid but because of the excellent separation already at low pressures, little improvement was noted at high pressure. In the other case, 25 percent solids, the response to pressure was slow but the detrimental effect caused by pulp viscosity was more intense than the enhancing effect caused by increasing the feed pressure.
Similarly, the feed pressure was less effective in improving the cyclone separation of the coarse and fine ores. The 48- x 65-mesh sample results were so good at low pressures it was difficult to improve the grade and recovery. Below 200 mesh the mineral particles were too fine to respond to the pressures tested.
Summary
The range of the variables tested encompassed an optimum operating condition which was essential to produce the specified spodumene grade and recovery. Nevertheless, an interrelationship existed between the pulp density, particle size, and cyclone pressure which necessitated selecting an area of operation rather than specific conditions. Table 4 gives the level of each parameter required to effect an 85 percent concentrate with an 85 percent recovery. For best heavy liquid cyclone beneficiation of spodumene; (1) the feed pulp density should be between 10 and 15 percent solids for efficient separation and high throughput, (2) the ore should be essentially plus 200 mesh because of the very poor results obtained from finer particles, and (3) the cyclone feed pres¬sure should be maintained about 60 psig to insure high concentrate grades in all the mesh fractions.
Since pressure caused the different sized ores to reach a maximum grade and recovery at each pulp density, it is possible to relate these variables. Table 5 predicts the estimated maximum concentrate grade and recovery which can be expected from each ore and each density when pressure no longer affects the separation. This is depicted graphically in figure 11.
In addition to establishing operational limits, the data revealed the following information:
- Particle size is the most important factor affecting the mineral separation.
- For each particle size and pulp density a minimum pressure is needed for maximum separation. Above this, pressure has little effect.
- Under any of the conditions tested, the minus 200-mesh ores did not respond satisfactorily to HLS cyclone separation.
- When the feed density reaches 25 percent solids or more, the pulp becomes too viscous to effectively separate fine size mineral particles.
- Concentrate grade is more sensitive to changes in pressure, density, and particle size than is recovery.
Influence of Feed Grade and Pressure
Ore beneficiation utilizing heavy liquid cyclones may require several concentration stages to achieve the desired product analysis and mineral recovery. The multistage cyclone system becomes more complex in operation, analysis, and evaluation because of the middling products. When the middlings are continuously recycled in the circuit not only will the materials balance change but the cyclone feed grade may be radically different than the original ore analysis. This test series investigated the effect feed grade has on the heavy liquid cyclone separation of spodumene. The apex and vortex finder openings were standardized at 0.11 inch and 0.08 inch, respectively. Feed pulp density remained constant at approximately 15 percent solids and the cyclone pressure was varied.
Normally, it is not possible to preset the ore grade but it is important to know what effect a change of feed analysis has on the process. Mine-run ore from a spotty mineral deposit could randomly upset the HLS cyclone system, making it impossible to stabilize the circuit or maintain continuous product specifications. In all likelihood an optimum feed grade exists for a given set of operating conditions, and for this purpose six samples were investigated. Table 6 gives the size distribution and spodumene analysis of the ores whose average grades are: (1) 7 percent, (2) 18 percent, (3) 37 percent, (4) 54 percent, (5) 80 percent, and (6) 88 percent. Except for the 18 percent sample which is a natural ore, the samples are synthetic blends of different spodumene products.
The influence of cyclone feed pressure was previously investigated on various mesh fractions but usually an ore contains a weighed combination of these particle sizes. In this series of tests the “total ore” was examined and a single pressure was determined which best fit all the associated mesh fractions. Nine cyclone feed pressures were tested between 20 psig and 100 psig.
Figures 12 and 13 show the HLS cyclone separation of the six spodumene ores at different feed pressures.
Effect of Feed Grade
Heavy liquid cyclone beneficiation of the 7 percent ore was not satisfactory as all the underflow concentrates fell below 85 percent. The highest concentrate contained only 60 percent spodumene and pressure had little effect on the product grade above 40 psig. Recovery yielded better results but responded more slowly to pressure variations. At 50 psig feed pressure the recovery was 85 percent and achieved a 91 percent limit at 70 psig. Inside the cyclone the spodumene particles apparently had little difficulty segregating through the gangue minerals and discharging out the cyclone apex. Presumably the tailings contamination of the underflow was because the vortex finder was physically unable to handle the large volume of float material. The lowest overflow analyses, one-half percent spodumene, were probably the least that can be determined because of experimental error and particle entrainment.
When the feed grade raised from 7 percent to 18 percent, the average concentrate analysis increased about 24 percent, yet the average recovery declined only 3 percent. An 85-percent grade was made at 80 psig but only 60 psig generated an 85-percent recovery. Mineral beneficiation improved slightly above 60 psig as both the grade and recovery increased to 89 percent.
The 37-percent spodumene tests resulted in the best overall separation at the lowest pressure. The concentrate grades ranged from 85 percent at 30 psig up to 92-percent maximum at 100 psig. With 30 psig cyclone pressure, the recovery was only 50 percent but climbed to 85 percent at 70 psig and reached a 90-percent maximum at 90 psig. At equal pressures the grade exceeded the recovery, and consequently it was the recovery which dictated a 70 psig minimum pressure was needed for an 85/85 separation.
Because of the large quantity of spodumene in the 54-percent sample, the underflow concentrates ranged from 87 percent up to 97 percent. Recovery reached 85 percent at the topmost cyclone pressures and dropped off rapidly below 70 psig. An acceptable spodumene heavy liquid separation was achieved at 90 and 100 psig.
HLS cyclone tests were conducted on the 80 and 88 percent spodumene to find the highest possible concentrate. The resulting 98 percent spodumene concentrates proved that a high purity mineral product can be continuously produced with heavy liquid cyclones. Neither of the ores made an 85/85 separation because of the low recoveries. During these tests the particle flow pattern within the cyclone was probably reverse as occurred during the low- grade 7-percent testing. The quantity of spodumene in these high-grade samples was too much to flow through the cyclone apex opening and was forced out the vortex finder with the tailings.
Effect of Feed Pressure
Feed pressure had generally the same effect on the heavy liquid cyclone separation of the “total ore” as it had on the “individual mesh fractions” contained in the ore. As the previous particle size data implied, with greater cyclone feed pressures the concentrate grade and recovery increased to a maximum value where additional pressures had little further effect. Each ore tested reached a maximum grade and recovery at about 40 psig and 70 psig, respectively. Thus, when the cyclone pressure remains above 70 psig no pressure adjustment is needed to insure maximum cyclone separation if the feed grade fluctuates.
It had been hoped the data from the test work on the individual mesh fractions and this study could be correlated to predict the HLS cyclone separation. But the results from the ores differed from those of the mesh fractions. This is shown in figure 14 and table 7 where a calculated concentrate grade and recovery was mathematically computed and compared to the actual cyclone separation of the 18-percent spodumene ore. The grade and recovery
values from the particle sizing tests were used to calculate the expected cyclone separation of each mesh size fraction in the ore. The results were proportionately combined according to the size distribution of the ore to arrive at the predicted separation.
It seems unlikely that experimental error caused the deviation between the “calculated” and “actual” data since all the tests followed the same trend, showed little variation within each test series, and the calculated feed analysis checked closely with the original feed grade. There are several possible explanations to the deviation: (1) the different mesh fractions influence one another when beneficiated as a mixture, (2) because the particle sizing tests reused the same sample, the pulping mixing and cycloning attrition ground the ore finer than indicated, (3) the individual mesh-sized samples were insufficiently screened, or (4) an uncontrolled factor varied during the test work.
Summary
This study disclosed that an optimum feed grade existed for a given set of heavy liquid cyclone operating conditions, but the practical working range was quite wide. The value where the concentrate grade and recovery are highest depends upon feed grade and in part on the cyclone feed pressure. Table 8 and figure 15 gives the estimated maximum spodumene recovery and concentrate analysis for each ore assuming the cyclones will operate at feed pressures above 70 psig. On the graph the recovery and concentrate analysis curves cross each other near 30 percent feed grade with a 90-percent recovery and concentrate. Although this establishes an optimum feed grade, the two curves are relatively flat between the 20 percent and 80 percent ores. Below 20 per-cent, the grade of the concentrates fall off sharply, and above 80 percent the recovery declines. Using 85 percent as the acceptable recovery and concentrate analysis, the heavy liquid cyclone can produce a satisfactory spodumene separation on 20 percent to 60 percent ores.
The data from this investigation also revealed the following information:
- Mineral beneficiation in a heavy liquid cyclone is complex and not enough information is presently available about the system to predict a HLS cyclone separation.
- The “total ore” responded to separation in a similar but not identical manner as did the “individual mesh fractions” within the ore. With increasing cyclone feed pressures the concentrate and spodumene recovery increased to a maximum value where additional pressure had little further effect.
- Changes in the cyclone feed grade did not alter the minimum operating pressure required to maintain the maximum possible grade and recovery.
- The higher the cyclone feed analysis, the higher the underflow grade but the lower the recovery.
Selected Cyclone Parameters and Feed Density
Several physical parameters of the hydrocyclone have been found to influence classification and various mathematical theories proposed. Figure 16 shows the more important cyclone parameters including the (1) apex opening, (2) vortex finder opening, (3) vortex finder length, (4) feed inlet orifice, (5) included angle, (6) cylindrical diameter, and (7) cylindrical section length. None of these have been thoroughly examined to determine their effect on the heavy liquid cyclone beneficiation of minerals. Since it is impractical to
study all the design features of the HLS cyclone, the two factors which are most often varied in plant practice were investigated. Different apex and vortex finder openings were tested at various feed densities on the spodumene ore described in table 1. Cyclone feed pressure was maintained constant at 50 psig.
The apex size can shift the classification strata in a hydrocyclone. Reducing the apex opening increases the pulp density in the underflow product while simultaneously crowding more and coarser solids out the overflow. In a heavy liquid cyclone the underflow concentrate analysis was anticipated to increase when the apex opening was reduced but force additional losses out the overflow. To discover if this actually happened in the small cyclone units, four apex disks were installed in the cyclone and tested. The diameter of each opening was (1) 0.094 inch, (2) 0.086 inch, (3) 0.076 inch, and (4) 0.067 inch. The vortex finder opening was standardized at 0.125 inch. The individual test results are shown graphically in figure 17.
Changing the vortex finder opening of a cyclone can bring about several effects. In a classification unit, decreasing the diameter lowers the overflow pulp density and can reduce the cyclone capacity by restricting the throughput volume of the vortex finder. Generally, the smaller the vortex finder size, the finer the overflow particle size. Similarly, changing the vortex finder opening in a heavy liquid cyclone was expected to alter the mineral separation. By reducing the overflow opening, the amount of sink materials in the tailings should diminish and thereby increase the recovery. The underflow concentrate grade would subsequently drop. To study the influence that different overflow openings have on the HLS cyclone separation, five vortex finders were studied with diameters of (1) 0.125 inch, (2) 0.111 inch, (3) 0.098 inch, (4) 0.082 inch, and (5) 0.067 inch. The apex opening remained constant with an 0.094-inch diameter opening. Individual test results are shown graphically in figure 18.
In order to determine if cyclone feed pulp density had any effect on the separation at the different size vortex finder and apex openings, the tests were conducted at 5, 15, and 25 percent solids.
Effect of Apex Opening Size
At each pulp density, the greatest recoveries and the lowest concentrate grades resulted from using the largest cyclone apex opening, 0.094 inch. The recovery was nearly 82 percent with a feed density of 5 percent solids but the underflow contained only 71 percent spodumene. The higher the cyclone pulp density the less efficient the mineral separation.
Decreasing the apex opening from 0.094 inch down to 0.086 inch did not materially reduce the separation efficiency. The average grade and recovery changed less than 4 percent.
However, at all pulp densities with the 0.076-inch apex, the average recovery fell approximately 10 percent while the average cyclone underflow analysis rose only 4 percent. For example, the concentrate grade was 80 per-cent and the recovery was 69 percent at 5 percent solids .
The highest concentrate grades and the lowest recoveries resulted from using the smallest apex opening, 0.067 inch. At 5 percent solids the recovery was only 63 percent, but the grade had reached 82 percent spodumene. These values are nearly opposite the results from using the 0.094-inch apex.
By determining graphically where the recovery and grade curves cross each other, an apex size was selected which gave the highest concentrate analysis with the greatest recovery of the mineral. At 5 percent solids with an 0.079-inch apex opening, the grade and recovery should be near 75 percent. At 15 percent solids, a recovery and grade of 67 percent occurs with approximately an 0.072-inch apex opening. Because of the poor heavy liquid separation, the curves at 25 percent solids failed to intersect but it is estimated that an 0.062-inch apex would result in a recovery and grade slightly under 50 percent.
Effect of Vortex Finder Size
As expected, the largest diameter vortex finder produced the highest cyclone underflow concentrates and the lowest recoveries. Using a feed pulp of 5 percent solids, an 80-percent concentrate and an 84-percent recovery was made with the 0.125-inch vortex finder. As the pulp density was increased from 5 percent solids to 25 percent solids, the heavy liquid separation became worse. For instance, the concentrate contained only 44 percent spodumene at 25 percent solids and the recovery fell to 77 percent.
Tests with the 0.11-inch, 0 .098-inch, 0.082-inch, and 0.067-inch vortex finders showed that the smaller diameter openings generated lower spodumene concentrates. The recovery was less susceptible to variations in the opening size but rose slightly as the diameter diminished. The greatest increase in recovery, about 7 percent, occurred between tests using the 0.125-inch and 0.111-inch vortex finder.
The smallest vortex finder opening yielded only a 50 percent concentrate at 5 percent solids and a 35 percent concentrate at 25 percent solids. The recoveries at these two pulp densities were 94 and 88 percent, respectively.
Examination of the data at each of the three pulp densities revealed the average recoveries were increased about 10 percent when the vortex finder opening was reduced from 0.125 inch to 0.067 inch. This same size variation decreased the average concentrate grade approximately 27 percent at 5 and 15 percent solids. Although the grade drop was slightly less at 25 percent solids, it was insignificant since the heavy liquid separation was extremely poor.
Effect of Pulp Density
In the test studying the influence of the cyclone apex opening, the average underflow concentrate was approximately 10 percent lower when the pulp density was increased from 5 to 15 percent solids. The average recovery fell less than 2 percent. By comparison, at 25 percent solids, the spodumene in the cyclone underflow was lowered 32 percent and the recovery was lowered 9 percent.
Similarly, in the test series showing the influence of the vortex finder size, the average concentrate was reduced 10 percent and the recovery 1 percent when the cyclone feed density was raised from 5 to 15 percent solids. At a pulp density of 25 percent solids this same comparison indicated a 24-percent difference in concentrate grade and 5-percent variation in the recovery.
Previous test work on the “individual mesh fractions” proved that increasing the feed density hindered the effective heavy liquid separation in cyclones. Investigation on the “total ore” followed the same pattern and the lowest pulp density produced the highest grade and the greatest recovery. The decline in concentrate grade due to pulp density variation was nearly the same in the ore as it was in the mesh fractions. However, at equal pulp densities, the ore samples yielded better recoveries than the mesh-sized samples. This difference, about 8 percent, was not accounted for and additional research is needed.
Summary
Varying the apex and vortex finder size alters the internal classification pattern of large cyclones but cyclone manufacturers implied that this was not necessarily true in small cyclones as used in this project. Contrary to their supposition, changing the openings as little as 0.09 inch influenced the heavy liquid cyclone separation of spodumene. Thus, it becomes important to determine the size openings needed and design the cyclone to fit the specific application. The orifices should be periodically calibrated and the parts replaced when worn oversize.
These tests were not intended so much to make an acceptable 85/85 spodumene separation but actually to determine if the apex and vortex finder size influenced heavy liquid cyclone concentration. It had been hoped that by correctly setting these two parameters an effective spodumene separation would be achieved at 50 psig. An 85/85 separation was not obtained, but from the experimental data it appears the cyclone vortex finder opening should be about 0.111 inch and the apex opening about 0.075 inch for maximum beneficiation.
In addition to proving the significance of the parameters in a small cyclone, the following information was disclosed:
- Decreasing the vortex finder diameter increased the recovery but reduced the concentrate analysis. The grade responded more to opening variation than the recovery.
- Decreasing the apex opening increased the cyclone underflow grade but reduced the recovery. The recovery responded more to size variations than the concentrate analysis.
- Fluctuation in the concentrate grade caused by changing the pulp density was about the same using the “total ore” as previously experienced in tests using the “individual mesh fractions” of the ore.
- Fluctuations in the recovery caused by changing the pulp density were less using the “total ore” than previously experienced in tests using the “individual mesh fractions” of the ore.
Multistage Cyclone Systems
Heavy liquid beneficiation in a single-stage cyclone produced concentrates containing over 85 percent spodumene, with recovery of over 85 percent of the contained mineral. Although this separation closely approximates industrial results in flotation plants, several cyclones in series were investigated to yield even higher results. Figure 19 is a schematic flow diagram of the three multistage cyclone circuits studied: (1) two-stage overflow, (2) two-stage underflow, and (3) three stage. The 18-percent spodumene ore described in table 1 was tested at 15 percent solids. The apex and vortex finder opening of each cyclone was standardized at 0.08 and 0.11 inch, respectively.
Two types of multistage circuits were considered: (1) without pumps between each beneficiation stage, and (2) with pumps between each beneficiation stage. In this study, the cyclones were directly connected to one another without the pumping step. The circuits without the intermediate pumps were easier to operate, simpler to control, and required less equipment.
However, the pressure drop between the cyclones was excessive. The feed pressures were lowered about 40 psig in the secondary cyclones which subsequently reduced their separation efficiency. This pressure differential can be partly overcome in a commercial application through the proper design of the cyclones. To compare the two types of circuits, the data from the investigation on the various feed grade samples were used to estimate the results in a multistage circuit using pumps.
A study of multistage heavy liquid cyclone circuits is complex due to the recycle of a middlings material. The only positive method of determining the effect of a circulating load on the process is a continuous test. That is, a steady-state process with a constant feed rate and the uninterrupted discharge of the tailings and concentrate products. Batch tests, as conducted here, can only give an educated guess at the final results but the system is normally assumed “in balance” when middlings samples approximate the new feed entering the system.
Results of Two-Stage Overflow Circuit
Test results from the two-stage overflow circuit are given in table 9 and figure 19. In this circuit the overflow discharging from the first cyclone is fed directly into the second unit for an additional scavenging step. The first underflow product is the spodumene concentrate. The overflow from the second cyclone is considered the tailings with the underflow middlings either recycled or removed as a secondary spodumene product.
This HLS system resulted in only an 8 percent recovery loss through the second-stage cyclone overflow. Although the tailings analyzed about 3 percent spodumene, the 51-percent concentrate product was well below commercial standards. It appeared that the second-stage cyclone middlings was an ideal material to recycle back and combine with the original feed. The 15-percent middlings had nearly the same spodumene analysis as the cyclone feed and represented only 13 percent of the total feed comprising 6 percent of the spodumene. Because of the low-grade concentrate, this circuit does not appear promising as a method for spodumene production.
Table 9 also shows a comparable two-stage overflow circuit using a pump between the concentration and scavenger stages. The 82-percent concentrate was substantially higher than resulted from the direct connected two-stage overflow circuit. Spodumene losses in the cyclone overflow were only 5 percent in the 1 percent tailings product. The 50 psig feed pressure in the second cyclone accounted for a good scalping separation but yielded a 40 percent middlings material containing 16 percent of the total spodumene in the ore. Nevertheless, the quantity of middlings is probably small enough so that it will not abruptly change the results if recycled to the new feed.
Results of Two-Stage Underflow Circuit
Test results from the two-stage underflow circuit are given in table 10 and figure 19. In this circuit, the underflow discharging from the first cyclone unit is fed directly into the second unit for an additional upgrading step. The overflow tailings from the first cyclone goes directly to waste. The underflow from the second cyclone is considered the concentrate with the overflow middlings either recycled or removed as a secondary product.
The data show that the 95 percent concentrate accounted for only 25 percent of the total spodumene in the ore. About 35 percent of the mineral values were lost in the first stage overflow in a 7-percent tailings product. The second stage overflow was too high grade to be recycled back to the feed and was considered an intermediate 82-percent product. Because of the high tailings losses, this circuit does not appear promising as a method for spodumene production.
Table 10 also shows a comparable two-stage underflow circuit using a pump between the concentration and cleaning stages. Because of the lower tailings, the spodumene losses in the cyclone overflow material were less than those experienced in the direct connected HLS circuit. Yet this loss, 21 percent, is too great to be commercially feasible. Although the concentrate analyses in both systems were above 90 percent, approximately twice as much spodumene was recovered in the underflow product when a pump was used between the first and second stages. This was presumably caused by the greater feed pressure and perhaps by the higher feed grade in the cleaning cyclone. The middlings sample was relatively high grade, 68 percent spodumene, and additional investigation would be necessary to determine if this material could be satisfactorily recycled within the circuit.
Results of the Three-Stage Circuit
The test results from the three-stage HLS circuit are given in table 11 and figure 19. In this circuit, the second and third cyclones function as a scavenging and cleaning step, respectively. The overflow from the first cyclone unit is fed directly into the second unit for an additional scalping step while the underflow is sent to the third unit for an additional cleaning step. The overflow from the second cyclone is considered tailings and the underflow from the third cyclone is the concentrate. The two middlings may be combined or separated into either a recycle material or a secondary product.
While neither of the two-stage circuits produced a high-grade concentrate with a high recovery, the three-stage circuit showed definite possibilities. The concentrate product analyzed 93 percent spodumene and the mineral losses in the tailing were only 7 percent. The two intermediate middlings products can probably be recycled without upsetting the cyclone circuit. The combined middlings from the second and third cyclone units assayed about 18 percent spodumene, accounted for 29 percent of the total weight, and contained approximately 21 percent of the spodumene values.
Table 11 also shows a comparable three-stage HLS circuit using two pumps, one between each separation stage. The 92 percent concentrate and 1 percent tailings indicated an excellent separation, but the 55 percent spodumene middlings would require further testing to determine its influence when continuously recycled within the circuit. These results compared favorably with the test work without the intermediate pumps except for the higher combined middlings grade and the spodumene distribution. The spodumene distribution in the underflow concentrate was only about 50 percent.
Summary
Although continuous tests are necessary to fully examine any system with a circulating load, it is possible to estimate the results from batch tests if enough information is known concerning the process. In the same sense, two different continuous systems can be evaluated from equivalent semicontinuous tests. Assuming that the amount of the middling recycle material is small and is reasonably similar to the new feed in the circuit, the influence of the circulating load may be considered insignificant. Realizing that this is a precarious assumption which can be very misleading, it remains a possible analytical solution. Table 12 shows the calculated recovery values of the multistage HLS cyclone circuits tested assuming the middlings do not influence the product analyses. The indicated recovery for the overall circuit was computed using the formula:
Percent recovery = Concentrate analysis (feed grade – tailings analysis)/Feed grade (concentrate analysis – tailings analysis)
The feasibility of multistage heavy liquid cyclone beneficiation of spodumene was successfully demonstrated in this test series. Using a natural ore, both the concentrate analysis and spodumene recovery exceeded 90 percent in the three-stage circuit. The two-stage circuits were unable to produce these results simultaneously, but the separation could possibly be improved with additional testing. The versatility of these and similar circuits should provide a wide field of potential applications, especially in custom operations where several products with varying specifications are required.
Some data obtained from the single-stage cyclone investigations can be used to reasonably approximate the influence of various operating factors on a multistage cyclone separation, for example, pulp density, particle size, and feed grade. But the effect of others, such as recycle material, cyclone back pressure, and apex and vortex finder openings, are mere supposition. For example, what happens when the apex opening of the first cyclone is reduced and the vortex finder of the second cyclone is enlarged? The concentrate grade may remain unchanged, the circulating load diminish, the feed pressure drop, or there may be any number of simultaneous process changes. The analysis of multiseries HLS cyclone beneficiation is complicated enough to warrant a detailed examination and large enough to constitute an independent project. The continuous heavy liquid process, cyclone separation circuit coupled with the liquid recovery system, provides an outstanding challenge for an engineering research program. Future research efforts concentrated in these areas of heavy liquid mineral beneficiation appear justified from the results obtained in this investigation.
Conclusions
A detailed summary of the four studies on the beneficiation of spodumene using heavy liquid (TBE) cyclones is given at the end of each section. The more pertinent results of the experimental work revealed the following:
- The mineral particle size is of prime importance in the effective HLS cyclone beneficiation of spodumene from its quartz gangue. The smaller the particles the more difficult the separation. Below 200 mesh, the detrimental effect of size was sufficient to prevent a satisfactory concentration of the mineral. A 48- by 65-mesh sample resulted in a 96 percent spodumene concentrate with a 97 percent recovery, but a comparable minus 325-mesh sample yielded only a 40 percent concentrate and a 64 percent recovery.
- As the cyclone pressure increased, the separation improved to a maximum value where pressure had little additional effect. The maximum concentrate analysis and spodumene recovery was found to depend upon particle size, pulp density, and feed grade. However, the operating range of the cyclone was determined to be approximately 70 psig for best overall results. Pressure had a stronger influence on concentrate grade than on the mineral recovery.
- Regardless of the particle size or cyclone pressure, the separation efficiency diminished as the pulp density increased and the best results occurred at 5 percent solids. Only a slight drop in the concentrate grade and the spodumene recovery was noticed when the pulp density was raised to 10 percent solids. However, at 25 percent solids the pulp was so viscous that only the 48- by 65-mesh ore sample responded to HLS beneficiation. The most economical pulp density was estimated to be approximately 10 to 15 percent solids. None of the investigations provided any promising leads toward an effective separation at densities near 25 percent solids.
- Although the test work disclosed an optimum feed grade of 30 percent spodumene, the practical operating range of the HLS cyclone is quite wide. Satisfactory concentration of the mineral occurred between feed grades of 20 and 60 percent spodumene. Below 20 percent, the grade of concentrate falls off rapidly and above 80 percent the recovery declines. As expected, the higher the feed analysis, the higher the underflow grade but the lower the recovery,
- Changing the apex and vortex finder opening as little as 0.09 inch influenced the heavy liquid cyclone separation. Decreasing the vortex finder diameter increased the recovery but reduced the concentrate analysis. Decreasing the apex size increased the underflow grade but reduced the spodumene recovery. Design conditions for maximum spodumene beneficiation using the 0.4-inch cyclone were estimated to be with an 0.111-inch vortex finder and an 0.075-inch apex opening.
- The feasibility of multistage heavy liquid cyclone beneficiation was successfully demonstrated using a three-stage circuit. Both the concentrate grade and the indicated recovery exceeded 90 percent. Using one cyclone, the spodumene concentrates and mineral recoveries were between 80 and 90 percent.
In conducting future research on heavy liquid cyclone concentration, the following recommendations and guidelines are proposed:
- Investigate various mixtures and combinations of particle sizes in an attempt to formulate an equation to predict the HLS separation from the mesh size distribution of the ore
- Continue to explore the effect that the various cyclone parameters have on mineral beneficiation in an effort to improve the structural design of the unit.
- Initiate test work using larger cyclones.
- The multistage cyclone circuits should be thoroughly studied. Continuous tests should be conducted to determine the effect of a middling recycle material.
- Research investigation would be informative on different ores with varying particle shapes, specific gravities, and other physical characteristics.
- Research investigations should be considered on different heavy liquids with varying physical and chemical properties.
- A feasibility study and economic evaluation of the applicability of heavy liquid cyclones in mineral dressing is needed to determine the commercial potential of the process.