Table of Contents
Here I try to explain how ground slurry is discharged from a grate ball mill (or SAG). How it works is, the slurry flows across the grate as it would a screen panel.
On the other side of the grate/screens are veins like a pump impeller. As the mill turns/rotates the slurry is “pumped” out and discharged.
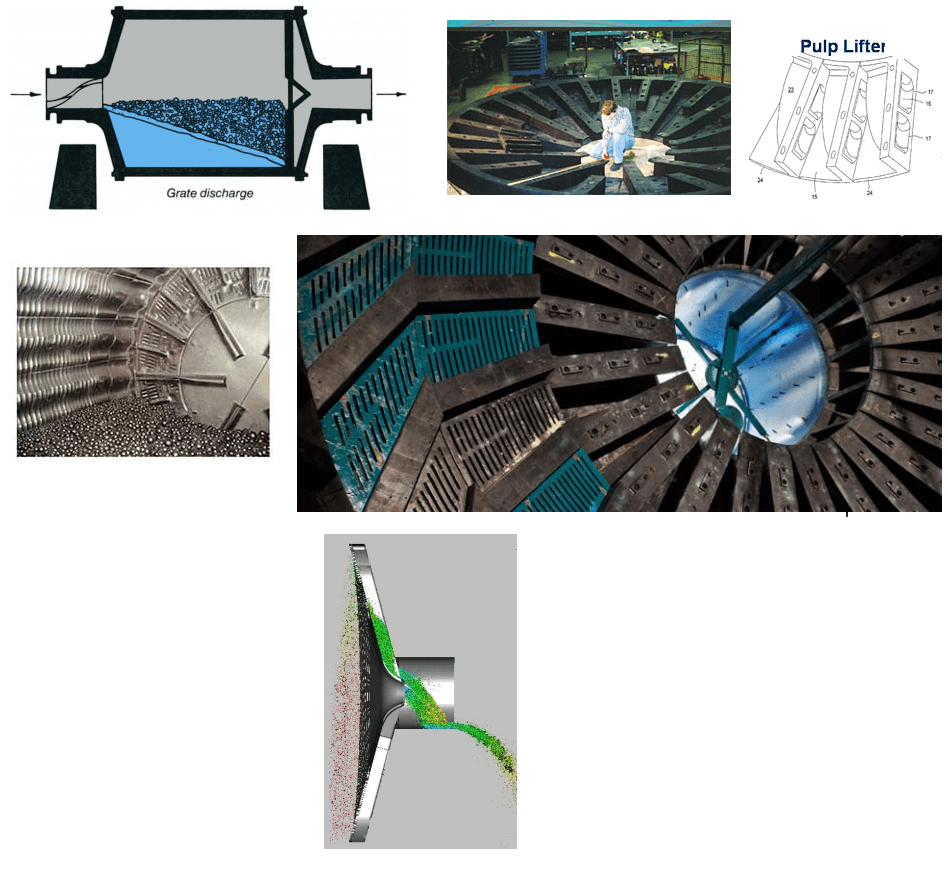
Discharge Grates
The natural flexibility of rubber has allowed rubber manufacturers to produce grates that are less prone to plugging than the traditional metal grate.
The main reason for this is the flexing or diaphragming action that a rubber grate is subjected to as it goes through its rotational cycle of a rotating mill.
Each time the grate enters the mill charge, the horizontal force of the load in the mill deflects the grate. This stretches the rubber and forces any large material caught in the grate opening along through the grate slot.
As the grate leaves the charge, the rubber assumes its original shape. This diaphragming action works the large particles that enter the grate through to discharge and produces a near zero blinding of grate wall. The pieces of media or feed seen in a grate when a mill is shut down are particles either in the process of being discharged or returning to the mill. A grate discharge mill that is “ground-out” would show the desired near zero blinding.
The slots in the early grates were designed around the traditional types found in proven concepts of metal grates.
Typically a slot (fig. 2) was designed with a selected rectangular, circular or square opening and then tapered out in all directions to release oversize material. The distance between the slots was determined by the structural strength required in the grate.
Our design or what we like to refer to as a “funnel type slot” was developed to take advantage of the characteristics of rubber (fig. 3). In cross section the slot design has parallel wall sections of up to 1 inch in depth and then tapers out and meets the second parallel wall section. This design has two main benefits. First and foremost, it produces a constant sized product throughout a major portion and the most productive life of the grate, unlike the traditional slot design which gives a larger product as soon as there is any initial wear on the face of the grate.
Secondly the cone section of the “funnel type slot” provides a quick release of the oversize product, thus reducing potential for blinding the grate.
The key feature in this design is the oval cross section which reduces the potential of stress cracks forming and propagating from the corners, a problem which occurs all too frequently in the sharp traditional 90° corners.
In order to allow the grate to flex and remain clear, the rubber is not reinforced but instead is supported by a stress relieved steel frame that is embedded in the rubber. This frame is designed to leave large enough “windows” to allow the rubber to work and at the same time to provide sufficient support to prevent excessive sagging or tearing of the rubber. The size and location of this support frame is very specific to the grinding application.
Rubber grates will continue to develop as more demanding applications are designed and as rubber technology continues to improve.
Pulp Lifters
The support of the grate wall is critical in any mill liner design. There are a variety of designs on the market now ranging from cast iron to molded rubber. A basic design is a fabricated metal structure with a protective coating of abrasion resistant rubber.
The pulp lifters have three main functions. First they must provide adequate support for the grate wall, secondly they must efficiently discharge the product from the mill and finally they must protect the mill structure from wear.
In the fabricated pulp lifter, the basic structure is a box type rib. This is fully enclosed on all four sides and forms a support for the grate wall. Lifter bar bolts pass through a heavy wall pipe that is welded inside the box structure. This pipe acts as an additional support mechanism and permits the lifter bar bolt to be properly torqued down. The pipe also protects the pulp lifter from slurry damage in the event of a loose or leaking bolt. The slurry is retained in the pipe so that it cannot race up and down inside the pulp lifter.
The base of the pulp lifter is a curved fabricated plate that lies flat against the mill head. In order to prevent any exposure of slurry to the mill head, the joint is overlapped.
The pulp lifter sections are held in place with bolts that are independent of the liner bolts. This means that the grate wall can be removed and replaced with no fear of the pulp lifters shifting. The location of these separate attachment bolts is dependent upon the location of available holes in the mill head.
For wear protection, the exposed surfaces of the pulp lifters are covered with rubber or in some cases urethane. The covering is usually 25 mm in thickness but can vary depending upon wear areas.
The pulp lifters are all tied together with a fabricated centre cone that is bolted to each of the pulp lifters. This cone is also protected from wear on both sides with rubber or urethane.
Although a lot of development and design work has gone into rubber grate walls and pulp lifters, there is still one major factor that causes a significant decrease in the life of the products.
Tramp metal in the ore such as scaling bars and rock bolts cut the rubber and can become lodged in the grate openings. This puts an excessive strain on the grates. When the mill rotates the metal is pushed and twisted by the ore. This stretches the rubber and can cause severe damage to the face and the back of the grate. Also if the metal is pushed through far enough it can cut and tear the rubber on the pulp lifters.