Table of Contents
To understand How Does a Gold Dredge Work, we may want to start by looking at California or Alaska. Gold dredging in now practised on the rivers of California, has is now superseded river mining. In river mining, an entire river was frequently deflected from its course so as to lay bare a section of its bed. This was usually done by building two dams from bank to bank, with their foundations on bedrock, the water being carried off in a wooden flume, starting above the head-dam and terminating below the foot-dam.
Sometimes, tunnels were made to drain permanently large reaches and deliver the water at a lower point. Sometimes wing-dams were built out from the bank above and below the part of the river it was desired to work, and a third dam connecting their mid-stream ends was constructed parallel to the direction of the current. The space cut off was then pumped dry.
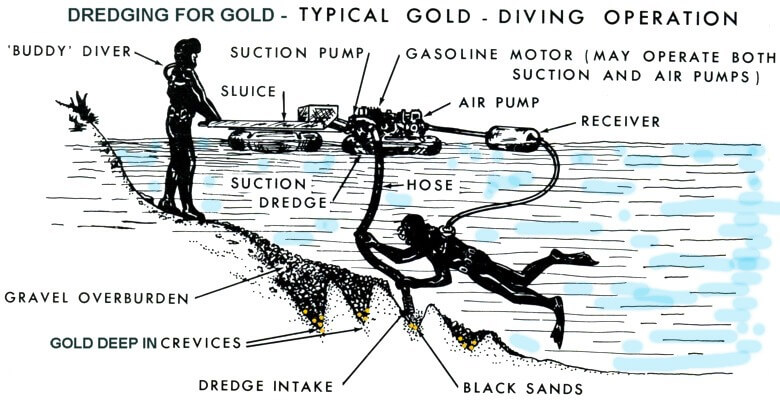
The river bed exposed by such methods was prospected and the pay-dirt when found taken out and washed, particular attention being paid to the surface of the bed-rock. The operations were usually terminated by the autumn floods.
River mining was probably subject to more uncertainty than any other branch of gold mining. The whole capital invested was often lost, and all works and machinery swept away by a flood before the pay-dirt was sighted, while numerous instances are on record in which the alluvium on the river-bed, after having been laid bare at great expense, was not rich enough to pay for sluicing.
River mining consists in the working of auriferous gravels in the channels and beds of existing rivers, and may with convenience be made to include the exploitation of deep bars below the level of the water. It is conducted in three different ways
- A portion of the river bed is laid dry by damming and fluming.
- The gravel is raised by dredgers or similar contrivances, operated from a boat.
- Pits are sunk on the bank, and the gravels below water level excavated and raised to the surface by ordinary mining methods, or by the hydraulic elevator. The gravel won by either of these three methods is washed in the usual way by sluicing.
Gold Dredging
This method of recovering gold from the gravel of river beds has of late years made remarkable progress, and its extension to the working of all flat placers has completely changed the aspect of shallow alluvial mining. A. Grothe states that the first dredge was operated on the Clutha River in New Zealand in 1864, but even in 1891 the method had made but little progress, and was generally looked on with disfavor everywhere except in New Zealand. In dredging, gravel is raised from the bottom of the river and delivered into a barge, and the material is there washed, the gold extracted, and the tailings sluiced back into the river. Dredges may be divided into three classes, according as:
- suction pumps,
- continuous ladder-bucket elevators, or
- a crane and bucket or shovel are used to raise the gravel.
Gold Dredge Suction Pumps
In this system, a centrifugal pump draws material through a large suction hose reaching to the bottom of the river. As long ago as 1891, a Welman suction dredge was in successful operation at Waipapa Creek, New Zealand. The pump was 3 feet 6 inches in diameter, and the suction pipe, which was 13 inches in diameter, could be applied at any point in an area within a radius of 40 feet. The large stones were caught and separated from the fine stuff by a riddled hopper-plate. The gold was very finely divided, and was caught on plush mats which were washed every eight hours. The water for washing was supplied from a reservoir by means of an 18-inch pipe. Stones of 56 lbs. weight were lifted by this pump, but larger ones occasionally blocked up the suction pipe.
It is difficult to regulate the relative amounts of gravel and water raised by suction pumps, the latter tending to be in great excess. The suction pipe is soon worn out, especially by coarse gravel, and the power required per ton of gravel is considerably greater than in the case of ladder-bucket dredges. Nevertheless, dredges of this type are in successful operation on the Snake River, Idaho, where a suction pump was working in 1899 on the material of the bank. A pit, 20 feet deep, was first excavated, and the sides were then sluiced down by jets of water, and sucked up through a hose pipe until a hole 200 feet square had been made, when the dredging apparatus was moved and a second pit excavated, the tailings being discharged into the first pit. The material handled ranged from fine sand to boulders 8 inches in diameter. Suction dredges, however, are not much used.
Ladder-Bucket Dredges
This is, in the majority of cases, the most satisfactory and economical type, and the one in general use. Ladder-bucket dredges are made in great numbers both in New Zealand and in Western America. A typical New Zealand dredge is shown in Figs. 10 and 11. These figures are from drawings supplied to the Department of Mines of New Zealand by Mr. F. W. Payne, of Dunedin. He also gave the following description of the plant.
The hull is 119 feet long, 35 feet 6 inches wide at bow, and 50 feet wide at stern. Depth of hull forward 6 feet 6 inches, depth aft 9 feet 6 inches. The engine is 25 H.P. nominal. The ladder carrying the buckets is of sufficient length to dredge 40 feet below water line. The buckets are of 7 cubic feet capacity, and run at a speed of ten buckets per minute.
The ladder is raised and lowered by a line worked by a winch, and five other winches are designed for a head line and four side lines to moor the dredge to the bank and to move it from place to place. The buckets deliver the gravel into a revolving screen 31 feet long and 4 feet 6 inches in diameter, driven by friction rollers. Thence the coarse material is directed into the main tailings elevator-buckets, and the fine material passing through the screen is delivered on to the gold-saving tables. After running over these, the tailings are deposited in a settling tank, from which they are lifted by a supplementary elevator into the main tailings elevator. The main elevator is no less than 145 feet long between centres, and is capable of stacking tailings to a height of 80 feet above water line. The capacity would be about 120 cubic yards per hour with the buckets three-fourths full. The dredge was intended to work on Fraser Flat, near Alexandria, New Zealand.
The ladder-bucket dredges in use in California bear a close resemblance to the type generally used in New Zealand, where most of the appliances originated. The following is a brief abstract of a description of a dredge placed at Oroville, on the Feather River: —The hull is 80 feet long by 30 feet wide and 7 feet deep. The ladder, carrying the dredger buckets, consists of a heavy lattice girder, and the bucket belt travels on cast-steel rollers. There are 32 cast-steel buckets, each of 5 cubic feet capacity, the lips being made of nickel steel. The ladder runs at the rate of 12½ buckets per minute, giving a capacity of over 100 cubic yards per hour with the buckets three-fourths full. The gravel is delivered into a revolving screen 4½ feet in diameter and 25 feet long perforated with holes of 3/8 inch in diameter. The coarse material is conveyed away by a bucket elevator, but the fine stuff after passing over the gold-saving tables is sluiced into the river at a distance of several yards beyond the stern of the dredge. The dredge is moored by five lines and all power is supplied through electric motors. The crew consists of two men per shift, and about 70 H.P. is used in the various operations. The working costs of Risdon dredges in California are stated to be in certain cases about 4 cents per cubic yard of gravel, but are generally from 6 to 8 cents.
Crane and Bucket Dredges
In these dredges a single large bucket or shovel, with a capacity of 1 or 2 cubic yards, is filled with gravel and hoisted on board a barge by some form of crane. The bucket is sometimes of the Priestman grab type, opening at the bottom as it is dropped on to the gravel bed, and closing automatically when the chains begin to raise it. A large shovel is also sometimes used as in a case on the Fraser River, British Columbia, in 1896-1897. Here there were two barges, one containing the dredging machinery, the other the gold-washing tables. The shovel made 90 trips per hour and raised 1½ cubic yards at a time. Boulders up to 5 or 6 tons in weight could be handled with ease. The Priestman grab bucket does not close completely if a stone lodges between its jaws, and comes up partly empty, but in cases where large boulders, tree trunks, &c., are dispersed through the gravel, it might be used with advantage, instead of the ordinary ladder-bucket which cannot deal with such obstructions. The wear and tear is said to be less with a Priestman dredge than with the bucket dredge. A Priestman dredge is shown in Figs. 12, 13, and 14, which are from drawings supplied by Messrs. Priestman Brothers.
Gold Saving Apparatus
The available space on a dredge is so small that long sluices are out of the question, and it is therefore necessary to disintegrate the gravel thoroughly in trommels or on shaking screens, and to make the gold-saving tables as wide as possible, so as to reduce the speed and depth of the stream of gravel running over them, especially where fine or scaly gold is abundant. The best size for the holes in the trommels is usually considered to be about 3/8 inch, but holes of 1 or 1½ inches are sometimes used. All material not passing through is regarded as worthless, and is not treated on the tables. In New Zealand the inclined tables are generally covered with coir matting or plush, and in the United States with cocoa matting, on which is laid a sheet of expanded metal, the raised edges of which form a series of very effective riffles. On the Snake River in Idaho, the gold consists of thin flakes and is difficult to catch. The gravel is concentrated by passing through sluices lined with perforated steel plates. The fine material is then further concentrated on tables covered with burlap. Similar methods have long been in use in New Zealand. J. P. Smith states that fine gold is lost in most of the New Zealand dredges and gives a table, from which the following details are taken, of spine of the most modern dredges in which fine gold is being saved:
The difference between the value of ground as determined in prospecting by treating samples in a cradle and that found in actual work with a dredge shows that some fine gold is lost in practice. The gold is recovered from the concentrates either by running them over amalgamated plates or by treatment with mercury in a clean-up pan or a rotating barrel.
Disposal of Gold Dredge Tailings
The tailings were formerly always discharged into the water again at some point beyond the stern of the dredge. They are now often piled on the bank to prevent any risk of mixing them with untreated gravel. Coarse and fine tailings are usually piled up separately, and when flat inland placers are being dealt with, as described below, the separated tailings occupy 50 or 60 percent, more space than the undisturbed ground. The bucket elevators for raising the tailings are shown in Figs. 10 to 13.
Treatment of Flat Inland Placers
The advantages of dredges in handling gravel have appeared of late years so great that their use has been extended from the beds of rivers to all flat placer ground wherever situated. The dredge is placed in a reservoir which is filled with water. The machinery is then erected and dredging begun, the tailings being discharged at the stern, so that the reservoir and dredge move gradually forward together. By piling gravel round the reservoir and letting in more water, the dredge is raised and can be made to work its way up sloping ground, as at the Warm Springs, Idaho. According to Postlethwaite clear water is kept flowing into the reservoir to prevent it from becoming too muddy for close gold saving.
Advantages of Dredging for Gold
Investments in dredges have been popular in New Zealand of late years, for the reasons that results obtained have been good, the capital required is comparatively small, working expenses easily calculated and subject to few variations, and, if the claim turns out to be barren, the dredge can be transferred elsewhere or sold. The Government Inspector, in fact, reported in 1900 that in some parts of New Zealand no other form of mining would be entertained as an investment. Dredging on rivers is a far cheaper method of treating the gravel than any other, but the great extension of the future will doubtless be in inland work. The amount of water required is small, the risk of loss by floods or any kind of accident infinitesimal, and the labour costs trifling.
Difficulties in Gold Dredging
The difficulties of raising the gravel due to the occurrence of tree trunks or large boulders can be overcome now that vacuum pumps have been superseded. The chief difficulty now is to save the fine gold in the gravel. The losses of gold are often large, though seldom considered. In one New Zealand dredge, it was found as the result of treating measured quantities of tailings that gold amounting to 2 grains per cubic yard of tailings treated was lost. The yield on the dredge was about 3 grains per cubic yard, so that only 60 percent, of the gold was saved. When there is an “overburden” or layer of clay above the auriferous material, it is found that lumps of clay and water carrying clayey matter in suspension are responsible for the losses of gold. The best method of avoiding these losses is to strip off the overburden of clay before attempting to raise and wash the auriferous gravel.
The bottom on which the gold-bearing material rests is also of importance. A hard bedrock prevents the gold lodged in its crevices from being removed by the dredge. Soft bed-rock partly decomposed in situ is, on the other hand, an excellent bottom for dredging. A soft tenacious clay underlying the gravel causes loss of gold in washing.
What is the Cost of Dredging
The capital expenditure on a dredging plant in New Zealand varies from about £2,500 for a small dredge, with a theoretical lifting capacity of 60 cubic yards per hour, to £10,000 for a large dredge capable of lifting 150 cubic yards per hour. The working cost of a small dredge is given as about 1 ounce of gold per day in New Zealand, or about two-pence per cubic yard of gravel treated. The cost of working in Western America is stated to be about four cents per cubic yard in a case where the power was supplied by steam from coal. Working costs at Oroville, California, are given by Postlethwaite as ranging from 3.66 to 8.7 cents per cubic yard. Much larger dredges, handling 7,000 cubic yards or more per diem, will soon be in operation in California, and the cost on these may be less. The working cost on a dredge of moderate size is given by F. W. Taylor as about £40 per week, and the return may be expected to be from 20 to 30 ozs. of gold per week, so that the profits are often large. A great future for dredging appears to be promised in Siberia, where the industry was started in 1900. The working cost was given by Taylor as about 4.2d per cubic yard in 1904.