Table of Contents
HPGR or high-pressure grinding rolls have made broad advances into nonferrous metal mining. The technology is now widely viewed as a primary milling alternative, and there arc a number of large installations commissioned in recent years. After these developments, an HPGR based circuit configuration would often be the base case for certain ore types, such as very hard, abrasive ores.
Though long established in the cement industry, penetration to the hard-rock mining industry was slow , and hampered by high maintenance requirements both for wear surfaces in general, and in particular, high wear on the edge of rolls. HPGRs first made inroads into diamond processing (where rock fracture along grain lines favored a reduction in diamond breakage during comminution), and in the iron-ore industry. Over the course of the past 20 years. HPGR based circuits have become a circuit commonly evaluated, and there are now many circuits in operation.
This industry acceptance has been based on a reduction in the level of overall maintenance effort, an increase in the available size of the units, and the unit operation’s ability to improve overall comminution efficiency (particularly for harder ore types that can be problematic in a typical SAG circuit). Improvements to wear life and overall availability decreased the overall maintenance effort required. Incorporation of studs on the surface of rolls to allow formation of autogenous wear surfaces, and implementing edge blocks of a long-wearing material for edge protection, have allowed HPGRs to break into the mainstream of mineral processing. These wear-retarding innovations were the focal point of a full-scale trial at Lone Tree (Seidel ct al., 2006). Successful completion of this trial marked somewhat of a turning point in interest in HPGRs for hard-rock applications. Manufacturers have also paid special attention to the bearings, wear surfaces, and the handling of tramp metal through the rolls to improve operational reliability, reduce maintenance, and obtain longer service lives.
The most common HPGR based circuit involves feeding primary crusher product to a secondary crushing circuit with of cone crushers in closed circuit with screens, followed by tertiary crushing with HPGRs, also operating in closed circuit with screens. The product of these two stages of crushing and screening then passes to secondary milling. In hard-rock metals mining applications, HPGRs are currently in use in tertiary and quaternary crushing applications, as well as in secondary pebble crushing. In many respects, HPGRs replace crushers as a unit operation.
However, from a process standpoint. HPGRs produce a product with substantially more lines (for a given P80) than a crushing circuit. In this regard, the size distribution of an HPGR circuit is much more similar to the product of an SAG circuit than a conventional crushing circuit, reducing the amount of pow’er in the ball-mill circuit required (relative to a crushing circuit).
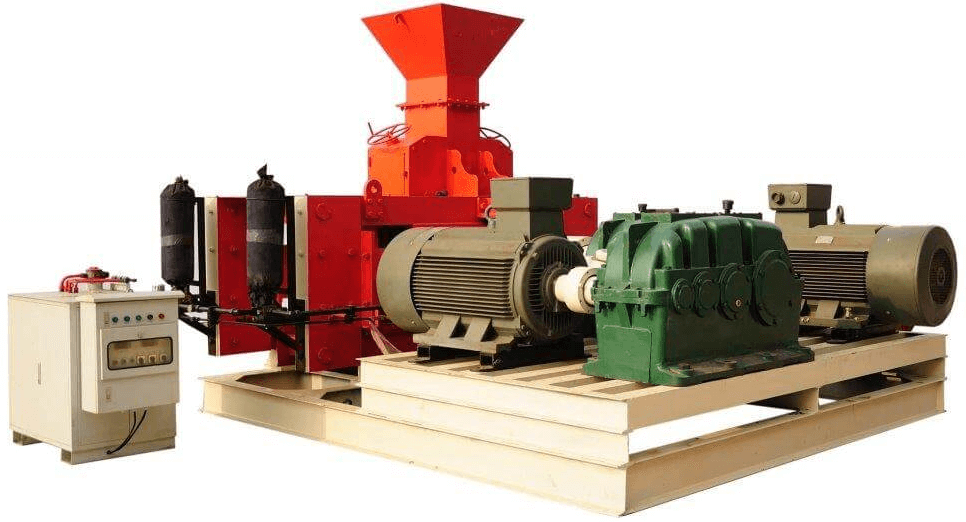
While HPGRs replace crushing as a unit operation, they represent a much larger installation of power in a given footprint relative to conventional crushers. As such, larger single-line capacities relative to a conventional crushing circuit can he attained. Freeport McMoRan’s (Freeport) Cerro Verde operation was a ground-breaking installation in that a combination of secondary’ crushing (using MP1000s), tertiary crushing using HPGRs, and screens replaced what would have been more typically been a large SAG mill feeding a multiple ball-mill circuit (Vanderbeek, 2006). The circuit, commissioned in 2006. w’as a significant step, and presented an alternative to conventional crushing plants or AG/SAG milling for primary’ milling applications (see Figure 17.10). Indeed, among the lessons learned for the Cerro Verde circuit w ere techniques to address rolls w ear, maintenance techniques, and elements of the art of operating a comminution circuit of this configuration (Koski et al., 2011).
Newmont Mining Company’s Boddington gold project followed on the heels of the Cerro Verde project and, after considerable care and study, selected HPGR comminution, with circuit commissioning in 2009 (Hart et al.. 2011). Using Boddington as a reference for comparing an SAG-based circuit to the selected HPGR-based circuit was widely documented in the literature. The project was commissioned with a similar comminution flowsheet to the Cerro Verde (and also employing four 2.4 x 1.7-m units).
A Cerro Verde expansion used a similar flowsheet as the 2006-commissioned circuit to triple circuit capacity. The expansion circuit includes eight MP1250 cone crushers, eight HPGRs (also 2.4 x 1.7-m units, with 5 MW each), and six ball mills (22 MW each), for installed comminution power of 180 MW. and a nameplate capacity of 240,000 tpd. The expansion circuit was under commissioning and ramp-up in Q4. 2015; combined, the original and expansion Cerro Verde HPGR-based circuits are the largest throughput mill in world.
Discrete Element Modeling (DEM)
Like trends in mills, larger equipment sizes continue to evolve. Freeport’s Morenci operation, for example, commissioned a 3.0 x 2.0-m Metso HPGR (called the hydraulic rolls crusher, or HRC) in an expansion mill circuit in 2014. The circuit has a single-line capacity of over 60,000 tpd. with the single HRC having 11.4 MW of installed power, and operating in conjunction with twin MP1250 cone crushers to feed twin 24 x 40-feet ball mills (26 MW for each of installed power). This single-line capacity approaches that of the larger SAG circuits, with a substantially reduced number of material handling units (feeders, conveyors, screens, chutes) relative to a typical crushing plant, and a more straight-forward plant layout. Notably, the HPGR in this installation (the Metso HRC) made a substantial step forward in process performance with a flanged roll set, w hich eliminates material bypassing the full crushing effect on the edge of rolls, as well as other innovations.
Of note, an HPGR circuit’s mode of operation is fundamentally different to that of SAG mill. As a largely volumetric machine, the comminution specific energy in an HPGR is a function of the power drawn by the machine at a given rolls pressure setting, divided by the throughput. This has two related effects: firstly, HPGR throughput has relatively little variation based on ore hardness, but it also implies that the specific power input for the HPGR stage is also relatively fixed. As a result, for harder ore types, the product of the HPGR circuit the grind coarsens with harder ore at equivalent throughput. This is typically a positive effect relative to an SAG circuit (where throughput drops with harder ore. but typically achieving an overall finer grind)—a coarser grind typically has less impact on revenue (based on a shift on the grind—recover)’ curve) than a drop in throughput for an SAG circuit. Stated another way, HPGR circuits are more accommodating of ore variability. Amelunxen et al. (2011) captured this impact well, and converted this variability to NPV estimates relative to an SAG mill circuit (assuming that the SAG was designed based on median ore hardness). Sizing of the secondary milling circuit needs to consider this variability in comminution response in primary milling.
The wear on a roll’s surface is a function of the ore’s abrasivity. Increasing roll speed or pressure increases wear with a given material. Studs allowing the formation of an autogenous wear layer, edge blocks, and cheek plates. Development in these areas continues, with examples including profiling of stud hardness to minimize the bathtub effect (wear of the center of the rolls more rapidly than the outer areas), low-profile edge blocks for installation on worn tires, and improvements in both design and wear materials for cheek plates. As mentioned, the HRC technology takes a different approach through the use of a flanged roll, which in turn also reduces edge wear.
HPGRs typically operate with improved comminution efficiency relative to rotating mills—this effect is typically more pronounced with harder ore types. Also. HPGRs improve observed downstream comminution efficiency. This is attributable to both increased fines generation (which can be corrected for mathematically, as this portion of comminution w ork is actually done by the HPGR. and not downstream unit operation), but also due to what appears to be weakening of the ore. which many researchers attribute to micro-cracking. This effect has been observed by the author in both well-controlled (and fincs-corrected) laboratory tests, and also in plant trials, as well as by other operators and researchers. A typical HPGR-circuit product approaches the lines generation of an SAG-circuit product, both with markedly more fines than a crushing circuit.
Of note is that while the HPGR improves comminution efficiency, the savings in overall circuit power requirements can be reduced or even negated by an increase in conveying and pumping costs relative to large single-line SAG circuits. Put simply, some of the power savings of more efficient comminution is used to transport material through the various unit operations of crushing, HPGR milling, and screening.
Media wear is much less than an SAG circuit in terms of total volume (balls and liners) or as unit consumption in terms of kg/kWh or kg/t. However, although the volume is less, the wear materials are much more highly finished—in economic terms, a high-volume. lower value media is replaced by a low-volume. higher value media. The cost is materials is therefore canceling to a greater or lesser extent. On the other hand, the savings in transport and logistics costs for the reduced volume can be substantial.
A number of trade-off study papers have been published. Very generally, such trade-offs often pit the higher capital cost of an HPGR circuit (with additional unit operations, bells, etc.) to lower comminution energy costs (based on higher comminution efficiency) relative to an SAG circuit. During studies of the Boddington project, comminution power efficiency gain was somewhat offset by increased pow’er for additional conveying and screening units, for an overall net 5% decrease in unit power required for the circuit (Seidel et al., 2006). While the magnitude of the observed pow’er efficiency benefit varies. HPGR circuits demonstrate a consistent benefit, which tends to be more marked for harder ores. Considerations in these trade-off studies also consider the differences in media consumption and overall circuit (not solely comminution) pow’er requirements.
In summary’, and relative to an SAG mill primary circuit, HPGRs appear to be most attractive with hard and abrasive ores, and in environments with high power costs. Availabilities are now’ such that aside from rolls change-outs, which are akin to a mill liner change, the unit rarely controls circuit availability. Overall single-line availabilities comparable to SAG milling can be attained.
When is HPGR better than Ball Mill
HPGR is typically used in a third-stage or fourth-stage crushing application ahead of grinding. You could always try to build a circuit doing 45 µm classification, but I suspect your circulating load would be overwhelming. Most HPGR applications in hard rock mining achieve 3000 µm to 7000 µm product
Options for Plant Design/ Upgrading of Comminution Circuits
The largest HPGR Polycom in operation (Figure 5) using a maximum roll diameter of 2.2 meters is processing diamond-bearing rocks in Australia at a maximum feed rate of 600 to 800 mt/h with a top feed size of 150 millimeter (6″). This rock material is reduced in one pass to 57% -1 millimeter with a power input of less than 3 kWh/mt.
For gold ore operations, Polycom HPGR offers several attractive options all of which will help to improve the metallurgy of the gold and significantly improve operating costs:
By shifting more of the particle liberation to the high-pressure grinding roll, substantial savings in power consumption can be achieved.
HPGR test results published by Grier (1992) on gold ores from the Mt. Todd project showed significant energy savings for a HPGR/Ball Mill circuit as compared to a SAG/Ball Mill plant.
- By adding a Polycom high-pressure grinding roll, the throughput of existing plants can be increased by as much as 150% while simultaneously reducing the power consumption by up to 20%. Large Polycom units provide a high throughput potential (600 to 1200 mt/h).
- Ball mill capacity can be increased due to the fact that the discharge of the HPGR contains considerable amounts of finished product, and the Bond work index is lowered due to the presence of microfractures in the rock which reduces the particle strength.
- Increased production rates are possible if HPGR is used as a substitute in an SAG – Ball Mill circuit. In many cases, the increased throughput of the SAG mill cannot be matched by the existing ball mill if a conventional pebble crusher is used. For this purpose, the HPGR offers the advantage that the HPGR’s discharge contains considerable amounts of finer product at a reduced material strength/reduced Bond work index which, in turn, increases the capacity of the ball mill.
Polycom HPGR offers particular improvements in the early physical recovery of coarse gold and gold-bearing sulfides through the addition of a “PGF” Circuit (i.e., Polycom – Gravity Separation – Flash Flotation).
The Polycom HPGR provides an easy and fast adaptation for throughput and product size through pushbutton changes of the hydraulic pressure. Constant product fineness can be maintained even when variations in ore grindability occur. This is of particular importance to gold operations where variations in particle size of gold and gold-bearing sulfides, silicification, changing rock types or other alteration features present challenges to conventional grinding circuits.
- The use of HPGR as a replacement of, or addition to, SAG/ball mills saves space and simplifies the grinding circuit.
- Robust construction and low capital expenditure. The compact design of Polycom units allows installation into existing mill facilities.
- Fifty to seventy times less wear.
- The operating availability is well over 90%.
- Low maintenance requirements. Polycom provides on-line redressing of the wear profile.
A case study illustrating the optimization of a conventional gold ore grinding circuit is shown in the attached Table 3.
Operating Modes of the Polycom HPGR in a Gold Plant
The grinding circuit applications of Polycom HPGR units for mining applications have been described previously by Patzelt (1987), Otte (1988), and Otte & Patzelt (1991).
Following are several options for the use of the Polycom high-pressure grinding roll for optimization of gold ore comminution circuits. Specifically the increasing significance of whole ore oxidation treatments of refractory ores will require cost-efficient and optimal liberation of ultrafine precious metals mineralizations.
- Pregrinding for Wet Ball Milling
Use of HPGR eliminates tertiary crushing in a conventional grinding plant. In some cases, it may even eliminate the need for a secondary crushing stage. As an energy-saving alternative to the SAG mill, HPGR is particularly suited for the pregrinding of hard, highly siliceous gold ores. This will help to downsize the ball mill while maintaining the throughput. In the pregrinding mode, HPGR use may result in energy savings of 15 to 30% and throughput increases of 20 to 40% (Schonert, 1991). - Multiple-Pass HPGR Grinding
Dry or moist gold ore feeds can be subjected to several passes through the Polycom by using two grinding rolls or recirculating part of the Polycom discharge. This minimizes grinding work of ball mills or may completely eliminate ball milling. - Dry Finish Grinding
The greatest power savings can be achieved if the high-pressure grinding roll is used in closed circuit mode for finish grinding. Savings of up to 50% are possible in comparison with conventional tube mill systems. The material needs to be dried and a classifier is required. - Dry Primary and Hybrid Grinding
Primary grinding in the high-pressure grinding roll increases the capacity of an existing dry ball mill operation. Even greater increases in capacity can be achieved if the Polycom is operated in hybrid mode. Hybrid grinding means that a part of the separator tailings (which are recirculated to the ball mill) is diverted and fed to the Polycom together with the fresh feed. Thus, some of the finish grinding work is handled by the high-pressure grinding roll. The throughput of the existing grinding system can be increased by 50 to 70%, while power consumption can be cut by 20 to 30%.
Additional options for high-pressure grinding roll use in gold ore comminution circuits are illustrated in Figure 11. As indicated by Kapur et al. (1992), high-pressure roll grinding is likely to replace ball mills in increasing numbers in the near future.
Polycom Amenability Tests for Gold Ores
Krupp Polysius has developed a rapid and effective test for evaluating a gold ore’s amenability to high-pressure grinding. All test products are subjected to cyanide leach tests and mineralogical analysis to provide optimal performance data and recommendations for pilot plant work, scale-up and/or plant operation.
Preliminary exploratory tests require only 100 kg of ore per sample.
Basic bench-scale tests can be performed with 200 to 300 kg of feed material.
- Tests can be completed at minimal cost within 4 to 6 weeks.
- Reliable scale-up procedures are provided.
Polycom high-pressure grinding roll pilot plant facilities are available for gold mining companies at the Krupp Polysius Test Center.