Table of Contents
- ORE SAMPLES FOR TESTING OXIDE, TRANSITION AND SULFIDE ORES
- Mineralogical Study
- PRELIMINARY LEACHING TEST PROGRAM
- PRELIMINARY PRECIPITATION (CEMENTATION) TEST PROGRAM
- PRELIMINARY LPF TEST PROGRAM
- ANCILLARY TESTS TO IMPROVE EFFECTIVENESS OF THE LPF PROCESS
- Jig Test on Sulfide Ore Composite -10 Mesh Crushed Ore and Jig Test on 50/50 Transition/Oxide Ore Composite -10 Mesh Crushed Ore
- CONCEPTUAL FLOWSHEET DEVELOPMENT
- CONCLUSIONS AND RECOMMENDATIONS
- RECOMMENDATIONS FOR FUTURE WORK
- Photomicrographs & mineralogy
- RESULTS OF LEACHING TESTS WITH H2SO4
- Test Tr-1.5: Acid Consumption Metallurgical Balance
- Test Su-1.5: Acid Consumption Metallurgical Balance
- Sulfide Composite Sample Metallurgical Balance Oxide Ore
- Test Ox-2.0: Acid Consumption Metallurgical Balance
- Test Tr-2.0: Acid Consumption Metallurgical Balance
- Test Su-2.0: Acid Consumption Metallurgical Balance
- Test Ox-3.0: Acid Consumption Metallurgical Balance
- Test Tr-3.0: Acid Consumption Metallurgical Balance
- Test Su-3.0: Acid Consumption Metallurgical Balance
- RESULTS OF LEACHING TESTS WITH H2SO4
EXECUTIVE SUMMARY
- A Metallurgical Laboratory had completed preliminary economic studies on various processing options applicable to the Minerals Project in South America, containing oxide, transition and sulfide ore reserves. These included heap leaching with SX-EW; use of Roast-Leach-EW of sulfide concentrates to produce CuSO4 crystals; and potential application of the Leach-Precipitation-Flotation (LPF) option to treat all the three ores from Deposit. The results of the above studies indicated that the potential use of LPF provided the best preliminary economics.
- Based on the above premise, Minerals authorized Metallurgical Testing Laboratory to undertake an in depth study to confirm the practical and economic viability of the proposed LPF process for treating the ores under a two-phased project.
- The results of the initial H2SO4 consumption tests under Phase I of the project indicated that while the amount of acid required for oxide and transition ores were reasonable (94.6 lbs/ton and 155.2 lbs/ton respectively) the acid consumption for sulfide ore was very high (588.6 lbs/ton). Based on this fact, it was jointly (Metallurgical Testing Laboratory) decided to exclude the sulfide ores from the proposed LPF process. Thus, the sulfide ores will be treated by the conventional sulfide flotation process as planned.
- The first step in the proposed LPF process consisted of leaching the mixture (50:50) of oxide and transition ores with H2SO4 at varying pH (1.5, 2.0 and 2.5). It was found that leaching at a pH of 1.5 provided leaching of all the oxide copper content within 2 hours of leaching. The acid consumption in this case was 150 lbs/ton.
- The second step in the proposed LPF included the precipitation (cement) of solubilized copper with iron powder. The best ratio of Fe:Cu was established at 1.25:1.00.
- The final step in the proposed LPF process development included the flotation of cement copper along with the residual sulfide copper in the ore mixture using conventional collectors (Z-200 and AP407/242) and frother (MIBC).
- The results of the initial open-cycle LPF tests indicated an over all copper recovery of +80% with a grade of +60% Cu.
- Additional tests conducted under Phase I included potential recoveries of Au, Ag, Pb and Zn.
- Based on the results of the test program conducted under Phase I, Metallurgical Testing Laboratory developed a conceptual flowsheet of the proposed LPF plant as well as a conceptual flowsheet for the plant including conventional sulfide flotation and the proposed LPF plant as shown under Section 8.0 of the report.
- Since the results of the Phase I test on the proposed LPF process are attractive, Metallurgical Testing Laboratory strongly recommends that Minerals allow Metallurgical Testing Laboratory to continue the work under Phase II to finalize the LPF flowsheet (through closed-cycle testing) and preliminary process engineering.
- Upon successful completion of Phase II work, Metallurgical Testing Laboratory recommends that Metallurgical Testing Laboratory be allowed to cooperate with the E/C contractor at the mine site to coordinate the implementation of the proposed LPF plant along with the sulfide flotation plant already under construction under Phase II of the project.
INTRODUCTION to LPF
Over the past three months, we have conducted metallurgical studies under Phase I to develop he proposed Leach-Precipitation-Flotation (LPF) process for treating the ores (oxide, transition and sulfide). The primary objective of this Phase I work was to develop a conceptual flowsheet of the proposed LPF process. This conceptual flowsheet will then be used to finalize the flowsheet and undertake appropriate process engineering studies to project capital and operating costs to determine the economic viability of the proposed LPF process under Phase II of the project. For the current metallurgical studies, Minerals had provided composite samples of oxide, transition and sulfide ore types.
The metallurgical studies under Phase I work included:
1. Sample preparation, head assays, and sequential copper analysis and ore characterization studies.
2. Mineralogical studies on all the three samples, especially determination of acid consuming gangue (calcite, dolomite, etc.) and problematic gangue minerals interfering with the flotation phase of the LPF process.
3. Preliminary grind-time scoping tests to obtain the specific grind of 60% minus 200-mesh as specified by and other Lab for the sulfide ore processing.
4. Acid consumption tests on three individual ore types (oxide, transition and sulfide) to determine if the acid consumption is economically applicable to all ore types.
Note: It should be noted that the capital and operating costs for the required H2SO4 plant would be a major cost affecting the overall economic viability of the proposed LPF process.
5. Preliminary leaching tests on the mixture of oxide and transition ores to confirm the leaching effectiveness and optimum time for leaching.
6. Preliminary precipitation tests on the PLS generated from the above leaching test under item (4) with metallic iron to determine the optimum ratio of Fe:Cu expected grades of cement copper.
7. Preliminary open-cycle LPF tests under the best operating parameters obtained from the previous test to develop a conceptual flowsheet for the process.
8. Ancillary open-cycle flotation tests to determine the applicability of pre-flotation of calcite/dolomite from the oxide/transition ore as well as the sulfide ore to reduce the overall acid consumption in the leaching step.
9. Additional open-cycle flotation tests to determine the technical feasibility of pre-flotation of talc and troublesome gangue prior to leaching to improve the final grade of the cement copper concentrates.
10. Confirmatory LPF test using the best operating conditions from item (7).
11. Development of the conceptual flowsheet for the proposed LPF process for treating oxide and transition ores.
12. Auxiliary gravity concentration tests to remove leach from the grinding circuit.
13. Determination of the movement o zinc values contained in the ores during the leach, precipitation and flotation steps of the process with potential recovery of zinc by sulfidization.
14. Review of the results of the flotation test work conducted on the sulfide ore as well as the design criteria and equipment selected so that this information could be incorporated in the overall plant design to include both the LPF process for oxide/transition ores as well as the sulfide ore.
ORE SAMPLES FOR TESTING OXIDE, TRANSITION AND SULFIDE ORES
Sample Preparation and Head Assays
On receipt of the oxide, transition and sulfide ore composite samples from the Project in South America, Metallurgical Testing Laboratory undertook an appropriate sampling program to obtain maples for the head assays as well as test charges for the subsequent metallurgical test program.
Head Assays
The detailed results of the head assays for the three composite samples are shown under Table 1. These analytical results, ore or less, match the results provided by (refer to Table 2).
The above analytical results especially the acid soluble copper; clearly indicate that the oxide and transition ores contain acid soluble copper while the sulfide ore is predominantly a primary ore type without acid soluble copper.
Based on the above premise, it is anticipated that the sulfide ore reserves from the deposit would not be subjected to the proposed LPF process, especially if the acid consumption for this sulfide ore is very high.
It is also quite evident that the assay results for zinc indicate the presence of acid soluble zinc in the oxide/transition ore and it would be necessary to include a zinc recovery system in the flowsheet to recover this valuable by-product from the leach solution (PLS).
Moreover, the head assays show the presence of appreciable Au/Ag by-product value sin all the ore types and these should be recoverable either in the proposed LPF process or in the sulfide flotation procedure.
Certificate of Analysis
Mineralogical Study
Although had provided generalized mineralogical data along with the assays on the three ore types form the Project, Metallurgical Testing Laboratory felt that a more detailed mineralogical study was warranted since the acid consumption step and the quality of the final flotation concentrates (from both the LPF and sulfide flotation steps) would be critical to the overall result and economics.
The results of the mineralogical study on the three ore types are provided under Appendix I.
These results clearly indicate that the calcite/dolomite content of all the three ore types, especially the sulfide ore is unusually high and would result in the excessive acid consumption, which would make the proposed LPF process uneconomical. Moreover, the study also indicates the presence of troublesome gangue minerals such as talc, asbestos, etc., which would float along with cement copper and sulfides, respectively.
It should be noted that the carbonate content (CaCO3) of the oxide ore is 1.39% and transition ore is 2.46. However, the carbonate content of the sulfide ore is 17.6%. Accordingly, the acid consumption for the oxide and transition ores would be reasonable while the sulfide ore would be very high without any significant contribution of the soluble copper in the proposed LPF process.
Effect of Grind vs Time Tests
The size-assay analysis of the oxide/transition blend at the grind size of minus 10-mesh is provided in the attached table.
In order to determine the best grinding time for obtaining the desired grind of 60% minus 200- mesh (Evaluation for Sulfide Ore) for the LPF as well as sulfide flotation flowsheets, Metallurgical Testing Laboratory ran a series of three grinding tests with the following results:
Ore Types……………………………………..Oxide and Transition
Feed Size………………………………………10-Mesh
Orebody Plant Design Study
Scrubbed −10 mesh Oxide/Transitional Ore Sieve Analysis Metallurgical Balance
PRELIMINARY LEACHING TEST PROGRAM
Preliminary Acid Consumption Tests
The results of the preliminary leaching tests on all the three ore types from the Project are attached under Appendix II. Leaching tests were conducted at pH 1.5, 2.0 as well as 3.0 to determine the best pH parameters. Leaching test at pH 3.0 was investigated to determine the economic potential of leaching the contained malachite and azurite mineralization at lower acid concentration.
The results of this leaching test program are summarized as follows:
- Acid consumption test at pH 3.0 indicated that the available acid was not sufficient to leach all the soluble copper content of all the three ores.
- Even the pH 2.0 was not enough to dissolve all the available soluble copper.
- PH of 1.5 provided the best acid concentrates for dissolving most of the contained soluble copper from all the ore types as shown in the following table.
As can be seen, the acid consumption at pH 1.5 is reasonable for oxide and transition ores but not for sulfide ore type.
Accordingly, it is strongly recommended that the sulfide ore should not be used in the proposed LPF process and that it be processed with sulfide flotation circuit. This recommendation is in conformity with sentiment to exclude the sulfide ore from the proposed LPF process.
Leaching Test (Recovery vs Time)
A series of preliminary leaching tests were conducted at pH 1.5 in order to determine the best leaching time. Tests were conducted at leaching time of 1, 2, 4 and 6 hours at the specified pH.
The results of the above tests clearly indicated that 1 hour of leaching time at pH 1.5 is sufficient to dissolve all the soluble copper. However, in practice it would be judicious to allow 2 hours as the leach time for operating and design purposes.
PRELIMINARY PRECIPITATION (CEMENTATION) TEST PROGRAM
Copper Precipitation (Cementation) Tests
The PLS from the previous acid consumption tests were used to determine the best ratio of Fe: Cu for the required precipitation (cementation) tests.
Based on the stiochemetry a ratio of about 1:1 Fe: Cu is sufficient to precipitate all the dissolved copper, however, in practice in presence of other dissolved metals it may be necessary to utilize higher than 1:1 ratio.
In order to determine the best amount of iron a series of precipitation (cementation) tests were run at the ratio of 1:1 and 1.5:1 (Fe:Cu). The results of these tests are reported in the attached tables.
The results of these tests clearly indicate that 1:1 ratio was not quite sufficient to precipitate all the dissolved copper and that 88.9% of the total dissolved copper. On the other hand, at the ratio of 1.5:1 nearly 100% of the dissolved copper was precipitated.
Accordingly, it is recommended that in order to simulate a commercial operation at a ratio of Fe:Cu of 1.5:1 be used in the subsequent leach-precipitation-flotation testing.
PRELIMINARY LPF TEST PROGRAM
Initial LPF Test
Based on the results of the above acid leaching and precipitation tests, Metallurgical Testing Laboratory projected the following LPF:
Leach/Precipitation/Flotation Procedure For 50/50 Oxide/Transition Ore
GRIND
Minus 10 mesh (2.00mm) ore is ground to 60% minus 200 mesh (0.074mm) at 65% solids.
LEACH
Ground ore is diluted to 35% solids and agitation conditioned for 15 minutes with 144 lbs/t concentrated H2SO4 at pH 1.5 in a flotation cell at 1100 rpm with no aeration.
PRECIPITATION
18.0 lbs/t hydrogen reduced minus 100 mesh powdered iron is added and conditioned for 2 minutes at pH 1.7.
NEUTRALIZATION
70.0 lbs/t Ca(OH)2 is added and conditioned for 2 minutes at pH 6.8.
ROUGHER FLOTATION
Pulp is diluted to 25% solids with 1st cleaner tails and floated for 8 minutes with stage addition of 0.02 lbs/t Z-200, 0.1 lbs/t AERO Promoter 407 and 0.1 lbs/t AEROFLOAT 242 Promoter.
1st CLEANER FLOTATION
Rougher concentrate is diluted with 2nd Cleaner Tails and floated for 4 minutes with 0.04 lbs/t MIBC.
LPF Test DZ-1 (Initial LPF Test)
Test DZ-1 is a LPF Test on 500 grams of 50/50 Oxide/Transition Ore. Ore was rod mill ground to 60% minus 200 mesh, leached by bottle roll with H2SO4 for 120 minutes, conditioned for 15 minutes with 25.6 lbs/t minus 100 mesh powdered iron, conditioned for 2 minutes with 0.02 lbs/t Z-200 and 0.08 lbs/t MIBC, floated for 4 minutes, conditioned for 0.5 minutes with 0. 08 lbs/t MIBC, floated for 4 minutes, conditioned for 0.5 minutes with 0.08 lbs/t MIBC and floated for 4 minutes. Rougher concentrate was cleaned once with 0.08 lbs/t MIBC.
Summary of Results
Test DZ-1 produced a 1st Cleaner Concentrate assaying 63.3% Cu, 0.5% Pb, 19.5% Fe, 0.6% Zn, 7.2% Insol, 33.0 g/t Au, 476 g/t Ag.
Conclusions
The above results of the initial LPF test clearly indicate that this process is a potentially attractive practical and economical process for treating the oxide/transition ores and that effort should be made to prove the effectiveness of this process with additional testing and process engineering studies.
LPF Test DZ-2 (LPF with Pre-Flotation of Talc)
Test DZ-2 is a LPF Test on 1000 grams of 50/50 Oxide/Transition ore. Ore was rod mill ground to 60% minus 200 mesh, conditioned with 0.08 lbs/t Pine Oil, floated for 2 minutes, conditioned with 0.04 lbs/t Xanthate, floated for 2 minutes, leached by impeller agitation at pH 1. 5 for 120 minutes with 153 lbs/t H2SO4, conditioned for 15 minutes with 25.6 lbs/t powdered iron, conditioned for 5 minutes with 66 lbs/t Ca(OH)2, floated with 0.02 lbs/t Z-200 and 0.08 lbs/t MIBC for 8 minutes, conditioned with 0.02 lbs/t Z-200 and 0.08 lbs/t MIBC for 1 minute and floated for 8 minutes. Rougher concentrate was cleaned once with 0.08 lbs/t MIBC.
Summary of Results
Test DZ-2 produced a 1st Cleaner Concentrate assaying 68.4% Cu, 0.4% Pb, 14.7% Fe, 0.6% Zn, 16.0 g/t Au and g/t Ag.
Recommendations
In the pre-flotation of talc and leach test, too much copper is lost in the Pine Oil/Xanthate pre-floats (6.7%). Also, too much gold is lost in the Pine Oil/Xanthate pre-floats (46.2%).
Perhaps a better way to improve concentrate grade will be to add a 2nd cleaner and eliminate the pre-floats. This could be the next test before starting locked cycle tests with cleaner tails recycle, tailings thickener overflow recycle and concentrate filtrate recycle.
ANCILLARY TESTS TO IMPROVE EFFECTIVENESS OF THE LPF PROCESS
Calcite Flotation Tests
Flotation Test 1
The purpose of this test is to float calcite from the sulfide ore composite in order to reduce the H2SO4 consumption. With 1.0 lbs/t Fatty Acid only 3.8% of the weight floated assaying 23.6% Ca and 4.4% Cu. Only 5.8% of the Ca floated, while 17.3% of the Cu floated.
Flotation Test 2
The purpose of this test is to increase the Fatty Acid dosage from 1.0 lbs/t to 2.0 lbs/t. Weight percent floated increases to 23.0% and assays 21.2% Ca and 2.6% Cu. Now 33.0% of the Ca floated while 60.2% of the Cu floated.
Results
Only a small amount of Ca can be floated with Tall Oil Fatty Acid while a large amount of Cu floats. More selective Calcite flotation conditions are required.
Flotation Test 3
The purpose of this test is to investigate the effectiveness of Amine flotation on sulfide ore composite for selective flotation of calcite. With 0.5 lbs/t CUSTAMINE 552, total Cu recovery is 90.5% at 9.3% Cu assay and 9.3% Weight floating.
Previous straight conventional flotation tests (Non-LPF) on sulfide ore achieved only 85.0%, 82.0% and 86.9% total Cu recovery, respectively.
Flotation Test 4
Increasing CUSTAMINE dosage to 1.0 lbs/t increased total Cu recovery to 95.4% however excessive weight (56.2%) floated.
Calcite Flotation Test 5
Flotation test 5 is a Tall Oil Fatty Acid test attempting to float acid consuming carbonate gangue from Transition/Oxide ore ahead of sulfuric acid leaching. The ore was ground to 60% minus 200 mesh with 1.0 lbs/t Tall Oil Fatty Acid, floated for 2 minutes, conditioned with 1.0 lbs/t Tall Oil Fatty Acid, floated for 4 minutes.
Results
This test removed 4.6% of the weight in a white colored froth. Nine percent of the carbonate copper floated along with the carbonate gangue. This is thought to be excessive so a more selective collector is required.
Calcite Flotation Test 6
Flotation test 6 is a Petroleum Sulfonate test attempting to float acid consuming carbonate gangue from Transition/Oxide ore ahead of sulfuric acid leaching. The ore was ground to 60% minus 200 mesh, conditioned with 1.0 lbs/t Petroleum Sulfonate, floated for 2 minutes, conditioned with 1.0 lbs/t Petroleum Sulfonate, floated for 4 minutes.
Results
This test removed 7.3% of the weight. Fifteen percent of the carbonate copper floated along with the carbonate gangue. This is thought to be excessive so a more selective collector is required.
Conclusion
Selective flotation of calcite from the sulfide ore is technically not feasible. Accordingly, the sulfide ore should not be subjected to LPF process due to excessive acid consumption.
In order to improve the effectiveness of the proposed LPF process, ancillary tests were conducted on the oxide, transition and sulfide ore sample to reduce the H2SO4 consumption by pre-flotation of calcitic gangue.
The results of these tests, as reported in the attached data sheets, are as follows.
Jig Test on Sulfide Ore Composite -10 Mesh Crushed Ore and Jig Test on 50/50 Transition/Oxide Ore Composite -10 Mesh Crushed Ore
Jig Test 1
Summary
Two hundred (200) grams of -10 mesh sulfide ore was fed to a Denver Jig with low pulsating water flow. Fifty-one (51%) percent reported to the Jig Underflow. The underflow contained 70% of the Pb, 66% of the Cu, 56% of the Zn, 49% of the Ca and 54% of the Au.
Recommendations
Further tests could be run with high pulsating water flow to possibly only recover the coarse Galena in the Jig underflow.
Jig Test 2
Summary
Four hundred (400) grams of -10 mesh Transition/Oxide Ore (50/50) was fed to a Denver Jig with low pulsating water flow. Forty Four (44%) percent reported to the Jig underflow. The underflow contained 57% of the Pb, 42% of the Cu, 50% of the Zn, 50% of the Ca, 43% of the Mg and 49% of the Au.
Recommendations
Further tests could be run to possibly only recover the coarse Galena in the Jig underflow.
CONCEPTUAL FLOWSHEET DEVELOPMENT
The results of the above LPF tests clearly indicate that it is technically feasible to achieve a final grade of +60% Cu with a recovery of about 80%. Under best operating conditions, recovery should be about 85%.
Preliminary Operating and Design Parameters
Based on the above premise, Metallurgical Testing Laboratory will develop a conceptual flowsheet for the proposed LPF process for treating the oxide and transition ore types from the deposit. The basic operating and design parameters for the LPF process are as follows:
- Crushing and Grinding
Use existing SAG Mill in conjunction with a new ball mill to obtain the desired grind of 60% minus 200-mesh (P80 74μ) - Leaching with H2SO4
H2SO4 150 lbs/ton
pH 1.5
Solids 35%
Time 2 hours - Precipitation (Cementation)
Metallic iron – ratio of Fe:Cu – 1:1.25
(Sponge iron)
Conditioning Time = 10 minutes - Flotation of cement copper and residual sulfide
pH = 6.6
Collectors = Ca(OH)2 (70.0 lbs/t); Z-200 (0.02 lbs/t); AERO Promoter 407 (0.1 lbs/t)
Frothers = MIBC (0.04 lbs/t)
Ro Flotation Time = 15 minutes
Cl. Flotation Time = 10 minutes - Flotation recovery of zinc possible recovery of solubilized zinc by sulfidization of the LPF tailings followed by flotation of ZnS.
This technique to be evaluated in Phase II of the project. - Neutralization and thickening of the flotation tails.
- Recycling of thickener overflow.
- Final tailings disposal.
The conceptual flowsheet for the proposed LPF process is as follows
Metallurgical Testing Laboratory Conceptual Flowsheet LPF on 50/50 Transition/Oxide Ore
Combined Sulfide Flotation and LPF Flowsheets
In order to visualize the overall flowsheet for processing oxide, transition, and sulfide ores, Metallurgical Testing Laboratory has shown the combined flowsheet for coordinating sulfide float and the proposed LPF plant for treating the oxide/transition ores separately. Please note that some of the unit operations for the two plants include use of common facilities such as crushing, grinding and flotation.
This combined flowsheet is shown in the attached figure.
This conceptual flowsheet will be used to develop the future testing and process engineering for the Project.
CONCLUSIONS AND RECOMMENDATIONS
Based on the results of the Phase I test program conducted on the Samples (Oxide/Transition/Sulfide ores) by Metallurgical Testing Laboratory to confirm the application of the proposed LPF process following conclusions may be drawn:
- The proposed LPF process is technically applicable to the oxide and transition ore samples and not to the sulfide reserves of the deposit.
- The above conclusion is drawn on the basis of acid consumptions indicated by the three ore types. The oxide ore consumes 94.6 lbs/ton or 5.1 lbs H2SO4/lbs Cu while the intermediate ore type consumes 155.2 lbs/ton or 9.0 lbs H2SO4/lbs Cu. Thus the average consumption of H2SO4 on the mixture of oxide and transition ores is about 150 lbs/ton to hold the leach pH at 1.5. On the other hand, the acid consumption for the sulfide ore type is about 586 lbs/ton with hardly any contribution to the total soluble copper available for the subsequent cement copper precipitation step.
- The requirement for metallic iron to precipitate (cement) the soluble copper in the proposed LPF process is about 1.25:1 (Fe:Cu) ratio.
- The flotation step in the final phase of the LPF process is readily accomplished by floating the cement copper at a pH of 6.5 with conventional collectors (Z-200 and AP407/242) and froth (MIBC).
- Thus, by using the proposed LPF process it is technically feasible to obtain an overall recovery of +80% in a final concentrate averaging +60% Cu.
- It should be noted that the Au and Ag values contained in the oxide/transition ore blend are also recoverable to at least 50% in the final copper concentrate.
- On the other hand, most of the zinc solubilized in the leaching step may be recovered by sulfidization-flotation or from the plant tailings overflow by RO or other suitable precipitant.
- Ancillary flotation tests conducted to remove the calcitic gangue from all three samples by pre-flotation prior to LPF were not successful. The objective of this test program was to determine the effectiveness of pre-floating calcitie gangue to reduce the overall acid consumption of all the three ore types.
- Moreover, additional flotation tests were conducted to pre-float the contained talc-type mineralization as well as Pb to improve the quality of the final LPF concentrates. These tests were unsuccessful since some of the Cu, Au and Ag values floated along with the gangue minerals.
- Results of preliminary process recycling tests have indicated a problem area and this issue needs to be resolved prior to initiating the proposed locked-cycle tests under Phase II.
- Based on the above premise, Phase I of the proposed LPF process evaluation for all three ore types contained in the Mine deposit is now complete with the indication that the LPF process is technically feasible and that the project should be continued under Phase II to finalize the LPF flowsheet and develop preliminary process engineering data for the operating and design parameters for LPF plant implementation.
RECOMMENDATIONS FOR FUTURE WORK
In order to expedite the project concerned with the proposed LPF plant to be operated in conjunction with the sulfide flotation plant already under engineering and construction at Metallurgical Testing Laboratory recommends the following:
- To continue work on engineering design and construction of the sulfide flotation plant as planned and initiate the sulfide flotation operation as soon as possible.
- Plan on addition of the proposed LPF process equipment as soon as possible to the existing sulfide flotation plant.
- In order to achieve this objective, allow Metallurgical Testing Laboratory to continue the project (after completing the Phase II at end of March 2010) under Phase III to include:
Site visit by Metallurgical Testing Laboratory Sr. Process Consultant to collect pertinent information on the project in progress and plan for additional equipment for the LPF process.
Final engineering design, sizing and selection of the required LPF plant equipment to complement the sulfide plant under construction.
To develop the LPF plant capital and operating cost estimates at the level of +20% in cooperation with staff as well as on site E/C contractor. - Provide LPF process engineering back up to the E/C contractor on the site during the construction and implementation of the plant as well as LPF plant start up.
- It is also strongly recommended that you and your Project Manager visit us at the end of March 2010 to plan for the above activities.
- If the above plan of action (recommendations) is acceptable, please advise so that Metallurgical Testing Laboratory can provide a detailed proposal.
Photomicrographs & mineralogy
The purpose of this project is to determine the bulk mineralogy of three ore samples (client samples South America Ore Sulfide -10m, South America Ore Transition -10m and South America Ore Oxide -10m) with emphasis on gangue mineralogy. A standard polished thin section was prepared for each sample for study by transmitted/reflected light microscopy. Photomicrographs of relevant phases are included for documentation.
Client Sample No.: South America Ore Sulfide -10m
In thin section the South America Ore Sulfide -10m sample is primarily composed of clear to pale green fragments of amphibole identified as tremolite. The tremolite generally occurs as aggregates of long, prismatic crystals showing a well-defined cleavage. Some single crystals penetrate or float in bodies of light green serpentine. The majority of the amphibole is non-librous but some asbestiform tremolite occurs as a trace. Light green clinopyroxene characterized as diopside is present in significant amounts and occurs as stubby, subhedral prisms. Some crystals are fractured and stained with iron oxide. Carbonate is well represented and consists of both dolomite and calcite. The carbonates are present as individual crystals and as aggregates where it is intermixed with iron silicates. A few large dolomite aggregates carry pockets of serpentine. Chalcopyrite is the dominant sulfide and occurs as inclusions in both carbonate and amphibole with the same frequency. In carbonate the sulfide is somewhat coarser with a grain size up to 400µm. Some grains are fractured and show alteration to covellite and chalcocite. A few larger grains are also associated with brown colored sphalerite up to 100µm that generally carries minute grains of chalcopyrite in the 1-3 µm size range. When associated with amphibole, chalcopyrite tends to show little in the way of alteration and occurs as thin rods that follow the amphibole cleavage. Grain size varies from 2µm to 100µm in this mode. Bornite is present as individual grains up to 250µm but is more common as attachments to chalcopyrite. Fractures commonly show minor replacement by covellite. Galena is present in trace amounts and occurs as individual grains and as inclusions in other sulfides. Grain size rarely exceeds 100µm. Traces of magnetite and ilmenite are present and are only seen associated with iron silicates.
Client Sample No.: South America Ore Transition -10m
Amphibole characterized as tremolite is the primary phase. The tremolite occurs as subhedral to euhedral prisms up to 250µm. In this sample, the amphibole is commonly mixed with fine-grained chlorite, some granular to prismatic diopside and patchy serpentine. Many of the aggregates and crystals are fractured and stained with iron oxide. A trace of asbestiform tremolite is also present. Dolomite and sparry calcite are present in minor amounts and generally occur as aggregates with the iron silicates. A few large dolomite fragments carry small pockets and attachments of green serpentine. Copper carbonate in the form of malachite and blue azurite is present in trace amounts. These carbonates occur as single fragments, mixed with chrysocolla and some rare, interstitial filling between tremolite prisms. The sample contains a low amount of sulfide mineralogy. Chalcopyrite is the most prevalent and, depending on its association with other phases, varies greatly in grain size. When associated with carbonate chalcopyrite reaches dimensions up to 250µm. These larger grains commonly have attachments of sphalerite, galena and some bornite up to 100µm in size. Sphalerite is always seen with minute chalcopyrite inclusions from 1-2µm in size. The amphibole also carries some chalcopyrite inclusions that tend to be aligned along cleavage planes. In this mode, the sulfide rarely exceeds 10µm in size. Chalcopyrite in this sample shows mild to strong alteration. Most grains have thin alteration rinds of chalcocite and most fracturing carries fine-grained, secondary covellite. Although some of the iron oxide seen in the sample is the result of iron silicate decay, a portion appears to be from the oxidation of chalcopyrite. Many of the larger goethite/hematite bodies carry angular remnants of chalcopyrite. A trace of magnetite/ilmenite is present and also shows some secondary iron oxide alteration.
Client Sample No.: South America Ore Oxide -10m
This sample is primarily composed of iron silicates. Light green tremolite is the dominant type and occurs as fragments and prismatic crystals up to 1mm. Some crystals have fracturing filled with brown iron oxide and corroded boundaries from mild to moderate weathering. The majority of the amphibole is non-fibrous but a trace of asbestiform tremolite is present. Diopside occurs as stubby prisms and fragments that tend to be finer grained with dimensions that do not exceed 700µm. Like the amphibole, the clinopyroxene shows some fracturing stained with secondary iron oxide. A few fragments of iron stained serpentine up to 300µm are also present in trace amounts. A few euhedral grains of dolomite up to 75µm are present, but rare. Copper carbonate in the form of malachite and azunite are more common and arc frequently seen intermixed with chrysocolla and iron oxide with a grain size up to 750µm. Chalcocite is the most abundant copper sulfide and is generally seen replacing chalcopyrite and bornite. It is common to see chalcocite with cores of residual bornite/chalcopyrite. A few grains are also host to fine grained covellite. Magnetite occurs as small inclusions in amphibole with a grain size up to 25µm. Most grains show some hematite alteration. Larger masses of goethite/hematite occur attached to some iron silicates and a few patches carry small (2-3 µm) angular shards of chalcopyrite.
RESULTS OF LEACHING TESTS WITH H2SO4
Metallurgical Testing Laboratory
Oxide Ore
Test Ox-1.5: Acid Consumption Metallurgical Balance
Oxide Composite Sample Metallurgical Balance
Transitional Ore
Test Tr-1.5: Acid Consumption Metallurgical Balance
Transitional Composite Sample Metallurgical Balance
Sulfide Ore
Test Su-1.5: Acid Consumption Metallurgical Balance
Sulfide Composite Sample Metallurgical Balance
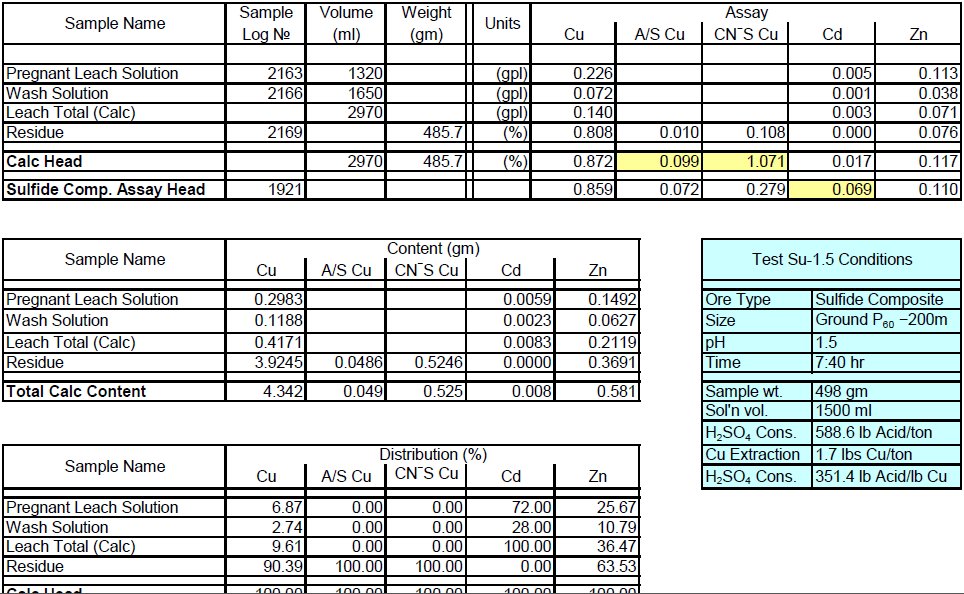
Oxide Ore
Test Ox-2.0: Acid Consumption Metallurgical Balance
Oxide Composite Sample Metallurgical Balance
Transitional Ore
Test Tr-2.0: Acid Consumption Metallurgical Balance
Transitional Composite Sample Metallurgical Balance
Sulfide Ore
Test Su-2.0: Acid Consumption Metallurgical Balance
Sulfide Composite Sample Metallurgical Balance
Oxide Ore
Test Ox-3.0: Acid Consumption Metallurgical Balance
Oxide Composite Sample Metallurgical Balance
Transitional Ore
Test Tr-3.0: Acid Consumption Metallurgical Balance
Transitional Composite Sample Metallurgical Balance
Sulfide Ore
Test Su-3.0: Acid Consumption Metallurgical Balance
Sulfide Composite Sample Metallurgical Balance