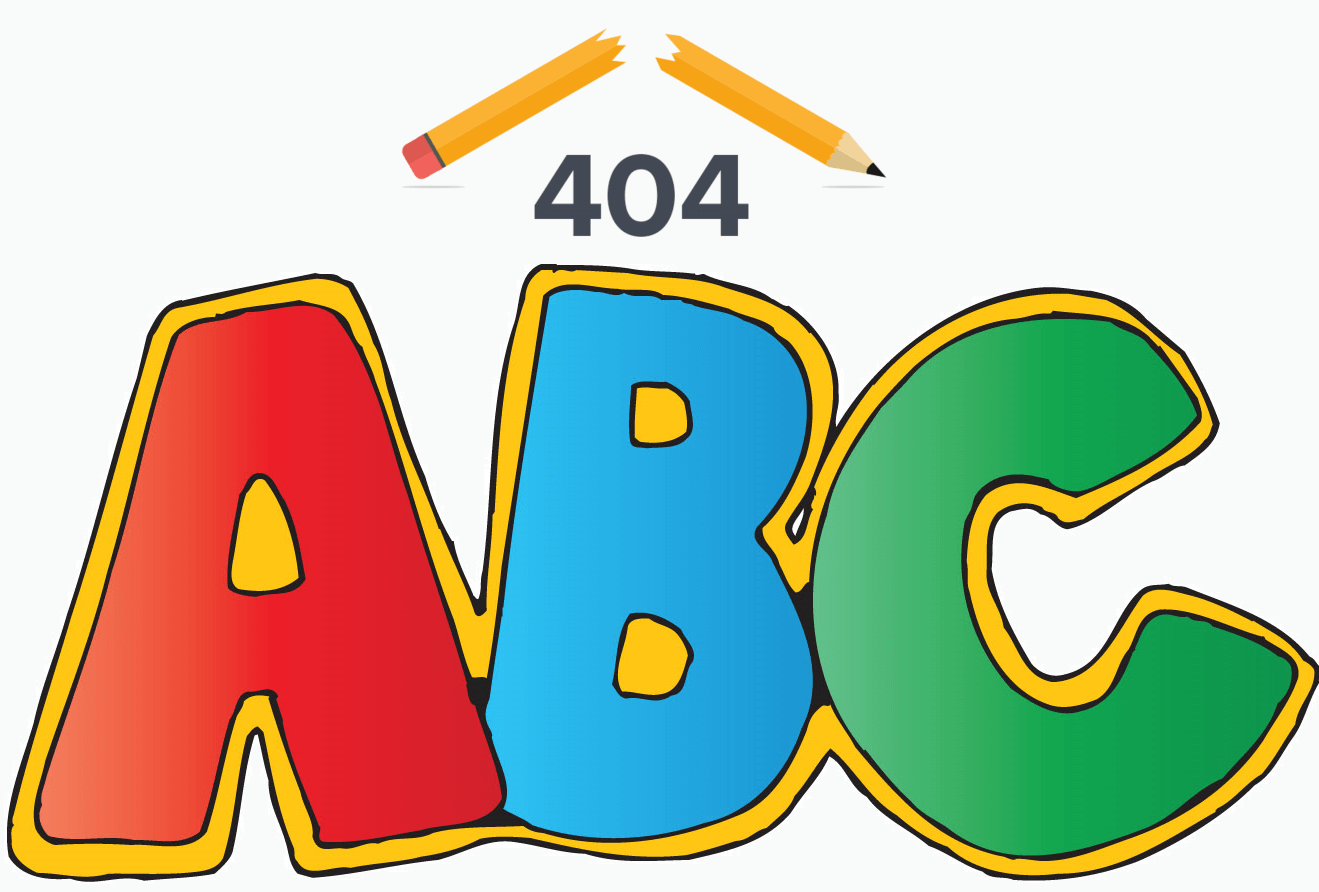
- ABC: Assay Based Controls are changes made to regulatory setpoints that are biased on the level or changes in the level of the valuable metal being recovered.
- ABC Circuit: A two-stage grinding circuit composed of an autogenous mill, a ball mill and a crusher.
- Abrasion: Wearing away by rubbing or friction.
- Acicular: Having the shape of a needle
- Activators: Cause a particular mineral to float with a collector when it otherwise would not.
- Adsorption: The gathering of a gas, liquid, or dissolved substance on a surface in a condensed layer.
- Aggregate: A group of unit or parts associated with one another. For example, a particle connected to a bubble.
- Agitator: A device for shaking or stirring.
- AG Mill: See autogenous mill.
- AG/SAG: Types of grinding mill which use the feedstock wholly or partly as the grinding media. In Autogenous Grinding (AG) large pieces of rock in the feed break other rock. In Semi-Autogenous Grinding (SAG) steel media such as balls are added to enhance the grinding action. Both types accept much coarser feed than do conventional (rod, ball) mills.
- Air Lock: The blockage of a conduit by an air pocket which prevents flow – the flow resumes when the inlet pressure is high enough to dislodge the air bubble.
- Alternating current: An electric current that reverses direction in a circuit at regular intervals.
- Analog Output: See manipulated variable.
- Angular: Having, a shape consisting of an angle or angles.
- Annulus: A ring.
- Apex: The bottom opening of a cyclone through which the underflow leaves.
- Apron feeder: A type of feeder that uses a series of overlapping steel plates to convey the load.
- Assay: The analysis of the ore to determine its chemical content.
- Attrition: A rubbing away or wearing down by friction.
- Attrition Grinding: Grinding by wearing away through rubbing and chipping.
- Autogenous Mill: A tumbling mill in which comminution is achieved by tumbling ore particles onto themselves.
- Automatic Mode: Controller operating mode in which the controller changes the manipulated variable to effect control.
- Baffles: Are used to help the mixing action by breaking up circular flow patterns.
- Balance cylinder: A cylinder in the crusher lubrication oil line that uses air pressure to force oil under the hydroset piston, raising it with the mainshaft, whenever the mainshaft jumps as a result of nipping some hard particle.
- Ball Mill: A tumbling mill in which steel balls tumble onto ore particles to break them.
- Belt feeder: A type of feeder that uses a rubber belt to convey the load.
- Blinding: Blocking or plugging of openings in a filter cloth.
- Blocking: Blocking is the condition where a single rock is too big to enter the crushing chamber.
- Bogey ( stacker conveyor): A wheel truck consisting of two wheels. The radial stacker has a total of six bogeys.
- Boom (stacker conveyor): A steel structure that supports the belt conveyor.
- Bornite: (Cu5FeS4) A brownish-bronze mineral which contains copper, iron and sulphur. Bornite is a source of copper.
- Bottom shell: The lower casting of the gyratory crusher body comprising the power transmission, eccentric, and hydroset system. The top and bottom shell castings meet at the crusher choke point.
- Boulder: A large mass of rock. Generally considered too big to be lifted by a man.
- Bowl Liner: Part that protects the bowl, the outer part that forms the crusher cavity.
- Breakage: Size reduction by causing rock to fracture.
- Breakage action: Refers to the method of breakage, eigher by impact or by attrition.
- Breakage event: In comminution modeling the action of size reduction is considered to consist of two components, selection and breakage. Taken together, the action is referred to as an event.
- Breakage pattern: The distribution of sizes of all particles produced from the breakage of a parent particle.
- Breakage rate: The frequency (number per unit time) of breakage events.
- Bridging: When two or more rocks are individually small enough to enter the crusher but straddle the opening in such a way so as to prevent each other from falling in.
- Bull Gear: Also called ring gear, the gear that encircles the tumbling mill and transmits the motion of the pinion gear to the mill. The mill rotates as the pinion gear meshes with the bull gear.
- Bushing: A fixed or removable cylindrical metal lining used to constrain, guide, or reduce friction.
- Bypass: The fraction of fine particles entrained by water in the classifier underflow.
- Cake Loading: Weight of filter cake per unit area of filter cloth.
- Cake Washing: Removal of solution from a cake by displacing it with water.
- Calcite: (CaCO3) A colourless or white mineral which is composed of calcium carbonate.
- Calibrate: To determine, check, or adjust the scale of a thermometer, guage, or other measuring instrument. This is usually done by comparison with a standard instrument.
- Carbonate: A compound which contains a carbonate group (CO3) composed of carbon and oxygen. In a carbonate mineral the carbonate is attached to a metal.
- Cascade Control: A control methodology where a series of controllers in which the output of one controller is the set point of the next.
- Cascading: The motion of the charge in a tumbling mill which occurs when the grinding media roll down from the top of the load to the toe of the load.
- Cataracting: The motion of the charge in a tumbling mill which occurs when the grinding media are ejected from the top of the load onto the toe of the load.
- Cavitation: The formation and subsequent collapse of bubbles in a liquid.
- Center of gravity: The point where the mass of a body is balanced in all directions A bar that is balanced on a fulcrum is acting on the fulcrum through its center of gravity.
- Center of Gravity: Point where the mass of an object is perfectly balanced in all directions.
- Centrifugal Force: The force that pushes a rotating object outward.
- Chalcocite: (Cu2S) A black mineral which contains copper and sulphur. Chalcocite is a source of copper.
- Chalcopyrite: (CuFeS2) A brass-yellow mineral which contains copper, iron and sulphur. Chalcopyrite is an important source of copper.
- Choke feed: When the crusher chamber is full and there is material above to keep it full.
- Choke Feed: Crusher operation where the crusher cavity is kept full.
- Choke point: See choke zone.
- Choke zone: That region between the mantle and concaves where the unit area, and therefore the unit volume, is at a minimum.
- Choking: When the downward flow of rock in the crusher is stopped for some reason.
- Circuit: A link of all flotation stages.
- Circulating Load: The quantity of material recycled in a closed circuit. The circulating load is calculated by dividing the flow of material in the recycle by the flow of material in the feed.
- Clarification: Removal of suspended solid particles from water usually by allowing the particles to settle.
- Classification: The separation of a mixture containing particles of different sizes into a stream containing coarse particles and a stream containing fine particles.
- Class of lever: A first class lever has the fulcrum between the load and the applied force (e.g. Crowbar, scissors). A second class lever has the load between the ful-crum and the applied force (e.g. Nutcracker, bottle opener). A third class lever has the applied force between the fulcrum and the load (e.g. Tweezers).
- Cleaners: A stage in a flotation circuit that treats concentrates from previous stages.
- Closed Circuit: A grinding circuit in which the underflow from the classifier at the mill discharge returns to the mill while the overflow leaves the circuit. In a normal closed circuit, the feed enters the circuit through the mill. In a reversed closed circuit, the feed enters the circuit through the classifier.
- Closed side setting: The minimum distance between mantle and concaves at the choke zone.
- Closed Side Setting: The minimum gap between crusher surfaces.
- CMC: Carboxy Methyl Cellulose is a depressant that adsorbs in preference to collectors and gives hydrophillic products.
- Coagulant: Chemical additive that causes particles to attract each other to form aggregates.
- Coagulate: The change from a liquid form into a thickened mass.
- Coalescence: What happens when two or more bubbles join together to form a single large bubble.
- Comminution: The breaking of large particles into small particles. The most common comminution processes are crushing and grinding.
- Comminution machine: Any machine designed to reduce the size of particles. In mineral processing the two broad categories are crushers and grinding mills.
- Competency: A term used to describe the structural integrity of a particular ore.
- Competent: A rock that is structurally intact, that is, it is without significant fractures or flaws that would make it crumble easily. Competent ores are important in Autogenous Grinding where it acts as grinding media.
- Compressibility: The ability of the filter cake to deform under pressure.
- Compression: The squeezing of a physical entity into a smaller volume.
- Concaves: Abrasion resistant steel plates that are mounted all around the inside of the crusher top shell bowl. They are intended to wear and require periodic replacement.
- Concentrate: The valuable product from a mineral processing plant.
- Concentrator: A plant where mineral processing takes place – also called a mill.
- Conditioner: A tank, usually agitated by an impeller, used to allow mineral particles to react with reagents.
- Contaminant: Undesirable solid or liquid material present in the product.
- Controlled Variable: Variable that the controller tries to maintain at set point
- Conventional mills: Fine grinding has traditionally been done for many years in cylindrical tumbling mills with a length to diameter ratio ranging from 2:1 to 3:2. These types have predominantly used rods or balls as grinding media. More recently large scale AG/SAG milling has become established. AG/SAG mills grind a coarser feed than do rod/ball mills and typically require downstream ball mills to finish the grinding. The term conventional mill refers to the traditional rod/ball type of tumbling mill as opposed to the newer AG/SAG mill.
- Conveyor: The conveyor moves bulk solids from one location to another on a belt.
- Coriolis Meter: A device that uses the bending force generated when a fluid changes direction, through a bend for example, to calculate mass flow.
- Correlation: A relationship between two things.
- Covalent Bond: A bond formed by sharing electrons.
- Critical Size: Size of the particles that build-up in the mill or in the circulating load due to a low rate of breakage.
- Critical Speed: The minimum speed at which the grinding media are pinned to the mill liners because of the centrifugal force.
- Crusher: A comminution device that breaks particles by exerting mechanical force.
- Crusher Cavity: Space inside the crusher where the ore is located.
- Crushing: Size reduction primarily by impact. Particles are broken down by forces applied perpendicular to their surface, compressing them.
- Crushing work index: Measures the quantity of electrical energy required to crush a given quantity of rock.
- CSS: See Closed Side Setting
- Cumulative size distribution: The standard method for representing size distribution analyses. Sizing can be by a number of methods, sieving is the most common. The cumulative percent passing is plotted on the vertical axis, the size is plotted on the horizontal axis. First, the percent of total sample passing the coarsest sieve is plotted against that size. Next, the percent of total sample passing the next coarsest sieve is plotted, and so on. The plot is cumulative because each plotted point includes the weight of material on all screens smaller than the one being plotted.
- Current: The amount of electric charge flowing past a specified circuit point per unit time.
- Cut Size: The particle size at which the classifier feed particles have an equal chance of going to the undersize or the oversize.
- Cyclone: A classifier which uses centrifugal force to separate a mixture containing particles of different sizes into a coarse stream and a fine stream.
- DCS: A Distributed Control System distributes the monitor and control duties among several devices.
- Dead Load: In a stockpile the rock particles not directly within the repose angle above a draw point will not flow unaided into the draw point. This region of the stockpile is called the dead load.
- Deadman switch: A safety mechanism that ensures stoppage of equipment if the operator is not proactively ordering its movement.
- Density: The mass of a material divided by its volume.
- Depressants: Prevents flotation of a particular mineral which otherwise would not float.
- De-water: Remove water from solids.
- Dewatering Rate: Speed at which water is forced from solid material or a filter cake.
- Digging Shoes: Pick up the grinding media and ore particles that settle at the bottom of the tower mill.
- Direct current: An electric current flowing in one direction only.
- Discharge Diaphragm: See Discharge Grate
- Discharge Grate: Grate inside the mill that retain coarse rocks.
- Discharge Lifters: See Pulp Lifters.
- Dispersants: Reagents that dispose the slimes which often agglomerate and cover the surfaces of larger particles, therefore preventing them from being recovered.
- Drag: Retarding force on a body resulting from the resistance to flow put up by the viscosity of the surrounding fluid.
- Drawhole: The opening underneath a stockpile that allows the ore to reach the feeders.
- Drawpoint: See Drawhole.
- Drive pulley: On a belt driven crusher, the grooved pulley attached to the pinion shaft. The grooves accept drive belts that convey power to the pinion from the motor. Direct drive crusher do not use drive pulleys.
- Dry cyclone: An air cyclone. It uses gravitational force to remove coarse dry particles from a contaminated air stream moving in a vortex.
- Dust enclosure: Any means for confining air contaminated with particulates so that it can be withdrawn from the surrounding environment.
- Dust suppression system: A system for capturing and removing particulates from contaminated air.
- Eccentric: A circular journal in which rests the bottom of the mainshaft assembly. The centerline of the journal is offset with respect to the crusher centerline so that when it is rotated the bottom of the mainshaft is caused to move in a circle around the crusher centerline. Viewed from the side, the motion of the mainshaft appears eccentric.
- Eccentric bushing: A bushing that fits inside the eccentric journal. The mainshaft assembly fits inside the bushing.
- Eccentric gear: Attached to the eccentric, the eccentric gear meshes with the pinion. Motor power is transferred to the main shaft assembly through this gear and the eccentric.
- Eccentric Motion: A rotating motion which is not centered on the center of the apparatus.
- Effort: A force applied against inertia.
- Eh: Pulp Potential.
- Electrochemical: Electon transfer from one substance to another.
- Electrometallurgy: The process of using electricity to extract the valuable metal from the concentrate – aluminum is extracted by electrometallurgy.
- Electrons: Revolve around the nucleus of an atom and have a negative charge.
- Electrostatic precipitator: A device for cleaning fine dust from contaminated air. It uses an electric field to polarize suspended particulates. The air stream is then passed by electrodes which attract oppositely charge particl-es.
- Electrowinning: A refining process which uses electricity – gold is refined by electrowinning.
- Entrainment: A way in which particles enter the froth by being carried in the water that accompanies each bubble in the film and the wake.
- Extraction: The removal of the valuable metal from the concentrate – the main extraction methods use heat, chemicals, or electricity.
- Feeder: A device for introducing dry bulk materials to a conveyor at a controlled rate.
- Filter Cake: The build-up of solid material against the filter cloth.
- Filter Cloth: Woven material that is permeable to water and upon which solid material is deposited.
- Filtrate: Water recovered through a filter cloth.
- Filtration Rate: Speed at which a cake builds or forms on a cloth.
- Flaky: Forming or tending to form flakes or thin, crisp fragments.
- Flocculent: Chemical additive that attaches to several particles forming a larger loosely attached group called a floc.
- Flotation: A process which uses the fact that different minerals have different affinities for certain chemicals in order to separate the valuable minerals from the gangue. The chemicals loaded with minerals are removed from the slurry by air bubbles.
- Fracture toughness: The resistance of a rock to the catastrophic extension of cracks within the rock mass.
- Froth: Bubbles formed on or in a liquid.
- Froth Freezing: A froth too dry to move.
- Fulcrum: The point or support on which a lever pivots.
- Fuzzy Logic Control: Fuzzy Logic Control determines control action using rules that are based on loose description of the process, for example, if the level is high then reduce the water flow somewhat.
- Galena: (PbS) a bluish gray mineral with which contains lead and sulphur. Galena is a source of lead.
- Gamma Gauge: A device which uses a weak radioactive source to produce gamma rays to measure density (% solids).
- Gangue: Worthless rock or other material in which valuable minerals are found.
- Gape: The opening dimension of a gyratory crusher as measured from the top of the mantle to the top of the concaves.
- Gilson screen: A machine designed to aid in the screening of intermediate sized particles. It consists of a frame that sits within a motorized shaking structure. Rectangular woven wire screen decks are placed within the frame, the motor is turned on, and coarse particle sample is shoveled onto the top screen.
- Gland Seal: A device which consists of packing compressed in a stuffing box for preventing slurry leakage around the rotating shaft joint.
- Grade: The percentage of a metal in a product.
- Grain: A discrete chunk of pure mineral. It may consist of one or many crystals.
- Graphite: A soft, black form of carbon with a metallic lustre, used for lead in pencils, for lubricating machinery, etc.
- Grate Discharge Mill: A type of mill in which the slurry flows through a grate to exit the mill. The other common type of mill discharge is the trunnion overflow discharge.
- Gravity methods: In mineral processing, refers to a separation process whereby gravity is utilized to effect separation between particles of greatly different densities.
- Grinding: Size reduction primarily by attrition. Particles are broken down by forces applied tangential to their surface, abrading and chipping them.
- Grinding balls: Media to aid the comminution of rock consisting of forged or cast spherical iron balls.
- Grinding charge: Refers to the media only (not the ore) in a grinding mill.
- Grinding Media: Solid bodies which tumble onto ore particles to break them into smaller particles. The most common grinding media are steel balls, steel rods, and large ore particles.
- Grinding work index: Measures the quantity of electrical energy required to grind a given quantity of rock.
- Grind Out: Procedure in which the mill is run without any solids feed for a short period to time to get rid of slurry in the mill.
- Hardness: Usually thought of as a rock’s ability to withstand deformation under load. In comminution it is commonly used to indicate the relative power requirements of different ores.
- Head Pressure: The energy supplied by the pump to the slurry. The head pressure is the difference between the pump discharge pressure and the pump suction pressure.
- Head pulley: The head pulley is located at the discharge end of a conveyor and is the usual location for connection of the conveyor drive.
- Head Tank: A tank situated higher than the equipment is feeds. Flow to the equipment is under the force of gravity.
- Heterogeneous: Consisting of dissimilar elements or parts.
- High alarm: In a control system, an alarm that occurs whenever some measured quantity (ie: level, speed, weight, flow, etc) reaches a level considered to be well above normal.
- High-high alarm: In a control system, an alarm that occurs whenever a measured quantity has passed sufficiently beyond a high point (see High alarm) that some count-er action must be taken.
- High Intensity Conditioner: A conditioner where a vigorous stirring action is used.
- Homogeneous: Uniform in structure or composition throughout.
- Hydraulic Gradient: Slope or change of height required for flow.
- Hydrocarbon: Any of a class of compounds containing only hydrogen and carbon.
- Hydrocyclone: A cyclone whose feed is a slurry of water and particles. It is also called a wet cyclone.
- Hydrogen Bonds: Bonds that result from the polar nature of water.
- Hydrometallurgy: The process of using chemical solutions to extract the valuable metal from the concentrate – gold and silver are extracted by hydrometallurgy.
- Hydrophilic: Water loving. Hydrophilic surfaces prefer to be in contact with water.
- Hydrophobic: Water fearing. Hydrophobic surfaces prefer to be in contact with something other than water, air for example.
- Hydroset: In a gyratory crusher, the hydroset system uses the hydraulic pressure of oil in a piston underneath the mainshaft to raise and lower the mainshaft and mantle. This is done to change the set of the crusher.,
- Hydrostatic Lift: Trunnion bearing lube oil pressure. Used in AG and SAG mills to monitor mill load.
- Idler: A roller used to support or guide the conveyor belt.
- Impact: In comminution, refers to breakage through the application of force perpendicular to the rock surface in a short period of time.
- Impact Grinding: Grinding by the violent shattering which results from striking the particles.
- Impact idler: Impact idlers cushion the shock at the loading point. They are grooved so that they can flex to absorb this shock, and are mounted very close together directly under a loading point.
- Impede: To obstruct.
- Impeller: The rotating blade of a centrifugal pump or blower.
- Inching: Slowly turning the mill to a new position. This is normally performed when relining the mill.
- Induction Time: The time it takes a particle to penetrate the water film and reach the air in the bubble.
- Inertia: The tendency of a body at rest to remain at rest or of a body in motion to stay in motion in a straight line unless acted on by an outside force.
- In-situ: When something is in-situ, it is in its natural position or place.
- Interface: The boundary between any two phases (solid, liquid or gas).
- Interlocks: A control methodology where equipment can be permitted to start, started or shutdown based on certain conditions.
- Ion: A neutral atom that has electrons added or removed from it.
- Ionic Bond: A bond formed by donating atoms.
- Journal: The part of a machine shaft or axel supported by a bearing.
- Keying the Charge: To hold the charge. Lifters key the charge, preventing slippage and allowing the charge to rise. In practice only the bottom layer (height of the lifter) of the charge is actually keyed.
- Kinetics: The description of the rate of change in a physical or chemical system.
- Launder: A trough conveying a slurry.
- Leaching: An extraction method which uses the fact that different minerals have different solubilities in chemical solutions to extract the valuable metal from the concentrate – gold and silver are normally extracted by cyanide leaching.
- Lever: A simple machine consisting of a rigid bar pivoted on a fixed point and used to transmit force, as in raising or moving a weight at one end by pushing down on the other.
- Liberated Particle: A particle composed mostly of a single mineral.
- Liberation: The fundamental step of mineral processing by which the valuable minerals are freed from the gangue mineral. Liberation takes place through size reduction.
- Lifters: Pieces that key the charge to promote the tumbling action.
- Liners: Pieces that protect the mill shell from wear.
- Live load: In a stockpile the rock particles directly within the repose angle above a draw point will flow unaided into the draw point. This region of the stockpile is called the live load.
- Locked Particle: A particle composed of several minerals.
- Logarithm: In mathematics, an exponent of the power to which a fixed number (usually 10) must be raised in order to produce a given number.
- Low alarm: In a control system, an alarm that occurs whenever some measured quantity (ie: level, speed, weight, flow, etc) reaches a level considered to be well below normal.
- Low-low alarm: In a control system, an alarm that occurs whenever a measured quantity has passed a low point (see Low alarm) and is at a point where some counter action must be taken.
- Magnetic separation: In mineral processing, refers to a separation process whereby magnetic force is utilized to effect separation between particles of different magnetic susceptibility.
- Mainshaft: The mainshaft is the moving part in a gyratory crusher. The mantle covers the mainshaft.
- Manipulated Variable: The variable that the controller changes.
- Mantle: Part that protects the cone, the inner part that forms the crusher cavity.
- Manual Mode: Controller operating mode in which the manipulated variable is kept constant. The controller suspends control action.
- Marcy Scale: An apparatus used to measure the density of a slurry.
- Massive Sulphide: Rock or ore composed mainly of sulphide minerals, both valuable minerals and gangue.
- Measured Variable: See Controlled Variable.
- Mesh Size: The number of openings per linear inch in a screen.
- Metal: A class of substances that are fusible, opaque, are good conductors of electricity, show a metallic luster, are malleable, comparatively heavy, and except for mercury are solid at ordinary temperatures.
- Meter: A unit of length equivalent to 39.37 inches exactly.
- MIBC: Methylisobutylcarbinol. A widely used frother.
- Micron: A measurement unit for length. There are 10,000 microns per centimeter, and 25,400 microns per inch.
- Middlings: A mixture of partly liberated particles.
- Mill Charge: See Mill Load.
- Mill Load: The contents of the mill composed of grinding media and slurry. The total mill load also includes mill shell, liners, etc. that increase the weight at the trunnions.
- Mineral: Minerals are groupings of chemical elements or compounds, with a consistent composition, found in the Earth’s crust.
- Mineral deposit: Any valuable mass of ore.
- Mineral Processing: The process of concentrating the valuable minerals in the ore in preparation for the extraction of the valuable metal.
- Moisture: Weight of water in a product divided by the weight of product expressed as a percentage.
- MSDS: The material safety data sheet outlines the hazards and first aid measures for each chemical.
- MV: See measured variable.
- Net Smelter Return: The economic value of the concentrate after transportation, smelting, refining and penalty charges are applied.
- Neutrons: Found in the nucleus of an atom and have a neutral charge.
- Niobium: A rare, steel gray, metallic chemical element that resembles tantalum in chemical properties.
- Open Circuit: A grinding circuit in which the particles go through the mill once. An open circuit has no classifier at the mill discharge to control particle size.
- Open side setting: The maximum distance between mantle and concaves at the choke zone.
- Ore: A mineral deposit that can be mined at a profit.
- Over current trip: A motor protection feature. When a motor draws excess power in response to a load it rapidly heats up, risking damage. The over current trip circuit detects an excess current and disconnects the motor.
- Overflow: The undersize material that leaves a cyclone.
- Overload: Unstable condition where the amount of material in the mill or in the circulating load increases and is compounded by a reduction in grinding capacity.
- Oversize: The coarse particle stream that leaves a classifier.
- Oxide: A compound which contains oxygen (O). In an oxide mineral, the oxygen is attached to a metal.
- Packing: Refers to a condition of compaction within the crusher where the material stops flowing.
- Pancake Mill: A tumbling mill with a length over diameter ratio (L/D) much less than one, for example a ratio of 1/3. Typical of AG and SAG mills in North-America.
- Particle: A single physical entity.
- Particle disappearance rate: The time rate at which particles leave a comminution process. In a primary crusher, particles may exit the crusher when they are small enough to pass the gap at the bottom.
- Partition Curve: A plot which describes how the particles fed to a classifier are divided between the undersize and the oversize. A partition curve gives the percentage of feed particles that report to the oversize for each particle size.
- Pebble Port: Large grate openings used to remove critical size material.
- Peening: Impact causing metal flow. In grates it reduces the opening size.
- Pendulum: A body suspended from a fixed support so that it swings freely back and forth under the influence of gravity.
- Percent (%) Solids: The percentage by weight of solids in a slurry (often called pulp or slurry density).
- Permeability: The ease with which an porous mass permits the passage of water.
- pH: A symbol used to express acid or alkaline content.
- PID Controller: A common controller which compensates proportionally to the error (P – proportional), compensates for sustained errors (I – integral) and compensates for changes in error (D – derivative).
- Pinion: The gear connected to the mill motor which causes the mill to rotate as its teeth mesh with the teeth of the bull gear.
- Plugging: When feed will no longer pass through the crusher. Due either to packing in the crushing chamber or an obstruction underneath the crusher.
- Polar Bond: A special type of covalent bond produced where there is an uneven sharing of electrons.
- Polarity: The uneven sharing of electrons.
- Polymetallic: Containing several valuable metals.
- Pore: An opening or hole in a filter cake or cloth.
- Porphyry Deposit: A deposit where the sulphides are distributed through out a non-sulphide gangue. Usually a low grade deposit.
- Powder: A collection of very fine particles.
- Powder factor: The ratio of average power to the maximum average power obtained when the voltage and current are synchronized.
- Power: Energy per unit of time.
- Power Factor: Ratio of average power to that when voltage and current are in synch.
- Precipitate: To separate (a substance) out from a solution as a solid.
- Pressure: Force applied to a unit area.
- Primary: First. A primary stage is the first stage in a series of stages.
- Primary crushing: The first stage of crushing in a comminution circuit. The primary crusher is the receiving point for blasted ore.
- Primary Grinding Circuit: First grinding circuit in a series of grinding stages.
- Primary gyratory crushing: The first stage of crushing where a gyratory type crusher is used. This stage is always described as primary crushing even if there is no additional crushing following.
- Process Variable: See Controlled Variable.
- Product: The valuable stream that leaves the circuit.
- Promoter: A collector normally used in conjunction with another collector.
- Protons: Found in the nucleus in an atom and have a positive charge.
- Pull Cord: See Safety cord.
- Pulp: See Slurry.
- Pulp Lifters: Lifters that carry the slurry from the discharge grate to the exit of the mill.
- Pump Box: A vessel which provides the pump with surge capacity.
- PV: See Process Variable.
- Pyrite: (FeS2) a pale brass-yellow mineral which contains sulphur and iron. It is also known as fool’s gold.
- Pyrometallurgy: The process of using heat to extract the valuable metal from the concentrate – iron is extracted by pyrometallurgy (smelting).
- Pyrrhotite: (FeS) A bronze-colored mineral which contains sulphur and iron.
- Quiescent Zone: The region between the mixing zone and the froth zone.
- Radial stacker: A type of conveyor that can pivot from one end and move in a horizontal arc. This gives it the ability to build a crescent shaped pile, or multiple individual piles.
- Radius of gyration: Viewed from above, the base of the mantle in a gyratory crusher moves in a circle around the crusher centerline. The radius of the circle can be adjusted by changing the eccentric and bushing.
- Ratio: The relationship in quantity, amount or size between two things. Usually calculated by dividing one value by the other.
- Ratio Control: A control methodology where the controller output is calculated so that a ratio with a measured variable is maintained.
- Reagent: A substance used for its chemical activity.
- Reagents: Substances used to produce a desired chemical reaction.
- Reclaim conveyor: A conveyor that recovers material from storage. The conveyors underneath the stockpile are this type.
- Recovery: The percentage of the valuable metal present in the feed that reports to the concentrate.
- Recycle: The stream that returns to pass again in the equipment. For example, the cyclone underflow in a closed ball mill circuit or the screen oversize in a closed SAG mill circuit.
- Reduction ratio: The ratio of the largest size that can enter the crusher to the largest size that can leave it. Equivalent to: Gape/Set.
- Refining: The process of removing impurities from the metal after it has been extracted from the concentrate.
- Regulated feed: Where the flow of material to the crusher is throttled in some manner so that it is never completely filled.
- Regulatory Control: Refers to the low-level control used to stabilize the process. An example of regulatory control is the simple control loop used to maintain tonnage at a fixed value.
- Repose angle: The slope at which a given material will come to rest under a given set of conditions.
- Representative sampling: When inferring some characteristic of a population from a small sample, the problem always exists that the sample is biased, that is, it does not represent the population with respect to that characteristic.
- Residence Time: The length of time a slurry spends in a vessel.
- Retention Time: The length of time a slurry spends in a vessel.
- Return idler: These support the conveyor belt on its return run.
- Reversed Closed Circuit: A grinding circuit in which the feed enters through the classifier. The undersize from the classifier located at the mill discharge leaves the circuit, and the oversize returns to the mill.
- Rock box: See Surge pocket.
- Rock breaker: An air powered impact hammer supported by a hydraulic boom.
- Rock hook: A hook shaped especially for prying up rocks wedged in the crushing chamber. The hook is slung from the overhead service crane.
- Rod Mill: A tumbling mill in which steel rods tumble onto ore particles to break them.
- Roping: The condition which occurs when the air core inside a cyclone collapses and the spiraling motion is almost lost. When roping occurs, the discharge has the appearance of a thick rope.
- Rougher: The first stage in a flotation circuit that treats the fresh circuit feed.
- Rounded: Shaped into the form of a circle or sphere.
- RTD: A resistance thermal device is a way of measuring temperature. It varies resistance proportional to the temperature.
- Run-of-mine: The average of all mined ores with respect to com-position and physical characteristics.
- SABC: A two-stage circuit composed of a semi-autogenous mill, a ball mill and a crusher.
- Safety cord: A cord that runs alongside a conveyor. It immediately disconnects power to the conveyor drive if it is pulled.
- SAG Mill: See Semi-autogenous Mill.
- Scavenger: A stage in a flotation circuit that treats the tailings from previous stages.
- Screen: An equipment consisting of a perforated or meshed sheet that is used to separate coarse particles from fine particles.
- Secondary: Second. A stage in a process that is second in a series.
- Secondary Grinding Circuit: Second grinding circuit in a series of grinding stages.
- Sedimentation: The settling of solid particles as a result of either gravity or centrifugal action.
- Semi-Autogenous Mill: A tumbling mill which uses a combination of ore and balls as grinding media. It is often referred to as a SAG mill.
- Separation: The fundamental step of mineral processing by which the product from the size reduction step (liberation) is separated into a valuable mineral stream (concentrate) and a gangue stream (tailings).
- Set: Equivalent to the open side setting. The distance of furthest approach between the mantle and concaves at the choke point.
- Set Point: Desired value that a controller attempts to maintain.
- Settling: The motion of a solid within a liquid created by a force such as gravity.
- SG: See Specific Gravity.
- Sharpness of Separation: A measure of classification efficiency. The sharpness of separation is related to the slope of the partition curve.
- Sheave: A wheel or disk with a grooved rim, especially one used as a pulley.
- Shorthead Crusher: A cone crusher designed to handle relatively fine material.
- Side travel switch: An electric switch that senses whether the conveyor belt is traveling off center (ie. misaligned).
- Sieve: A laboratory screen used to separate particles according to their size.
- Silicate: A compound which contains silica (Si).
- Single Stage Grinding: Operation where a single grinding circuit is used to obtain a final product size.
- Sinusoidal: A phenomenon that undulates in magnitude in a repetitive manner.
- Size classification: The process of separating particles from each other based on their sizes.
- Slabby: Having a broad, flat, thick shape.
- Slewing: Sideways motion.
- Slimes: Very fine particles, usually undesirable.
- Slurry: A mixture of ore particles and water.
- Slurry Density: The percentage of solids by mass.
- Smelting: An extraction method which uses heat to recover the valuable metal – iron and copper are usually extracted by smelting.
- Snub pulley: A secondary pulley near the head pulley, it increases the wrap of the belt around the head pulley for increased efficiency of power transmission.
- Sparger: Is used to inject gases, usually air into the pulp.
- Specific gravity: The ratio of the mass of a solid or liquid to the mass of an equal volume of distilled water.
- Specific Gravity: The mass of a substance compared to the mass of an equal volume of water. It is calculated by dividing the density of the substance by the density of water.
- Speed switch: An electric switch on the conveyor tail pulley that detects when the belt is moving.
- Sphalerite: (ZnS) a mineral which contains zinc and sulphur. Sphalerite is a source of zinc.
- Spider: The massive arm that spans the top of the gyratory crusher.
- Square Mill: A tumbling mill with a length over diameter ratio (L/D) of one.
- Stall: An overload induced stoppage.
- Standard Crusher: A cone crusher designed to handle relatively coarse material.
- Step bearing: A circular disk that sits directly beneath the mainshaft and supports it.
- Stockpile: A storage pile of dry bulk solids.
- Stone box: The receiving area for rock as it is dumped out of the haulage trucks. The stone box confines the rock so that it flows into the crusher.
- Sulphate: Any salt of sulphuric acid.
- Sulphide: A compound which contains sulphur (S). In a sulphide mineral, the sulphur is attached to a metal.
- Sump: Can refer to a floor sump (a pit used to collect spilled water or slurry), or can refer to the pump box.
- Supervisory Control: Refers to the high-level control that does not directly manipulate the valves and motors in the plant.
- Surface Tension: The tension in the interface between two phases. For example, a high surface tension at the air/water interface of a bubble means that it will rupture easily, like a stretched piece of cloth.
- Surge pocket: A storage compartment directly beneath the crusher that enables smooth feeding of crushed product onto a takeaway conveyor.
- Surging: Large fluctuations such as in flow or current.
- System Dynamics: The behavior of a system during a period of change.
- Tailings: The waste stream of a mineral processing operation. The valuable minerals are separated from the gangue, leaving the gangue to be disposed of.
- Tail pulley: The tail pulley is located at the feed end of a conveyor and is used to adjust the belt tension.
- Talc: A soft, smooth silicate of magnesium.
- Tangential: Which follows along a straight line that touches a curve at one point only.
- Tension: The elongation, or pulling apart, of a physical entity.
- Tertiary: Third. A stage in a process that is third in a series.
- Tertiary Grinding Circuit: Third grinding circuit in a series of grinding stages.
- Thickening: The process of removing water to increase the concentration or density.
- Ton: A measurement unit for mass. There are 2,000 pounds in one ton.
- Tonne: A measurement unit for mass. There are 1,000 kilograms in one tonne.
- Top shell: The upper casting of the gyratory crusher body to which are attached the concaves. The top shell provides the mainshaft with a fulcrum point through the spider and comprises the feed opening of the crusher.
- Torque: Force times the distance to the point of rotation. It is the energy of rotation.
- Toughness: The natural resistance of a material to fail in tension.
- Tower Mill: A vertical cylinder with a special screw or stirrer designed to move the grinding media. Grinding is achieved by the rubbing action of the media as it moves.
- Training idler: Training idlers track a conveyor belt to prevent misalignment (ie: side travel). When the belt moves sideways the idlers pivot in the middle to bring it back into alignment.
- Tramp metal: Any spurious metal object that does not belong.
- Tramp Metal: Unwanted piece of metal which can upset normal equipment operation.
- Trommel: The rotating cylindrical screen at the mill discharge which rejects coarse objects.
- Troughing idler: Troughing idlers support the belt load. Their profile causes the belt to trough thereby increasing its carrying capacity.
- Trunnion: The point of entry and discharge for the tumbling mill. The trunnion bearings support the mill at either end and ease rotation.
- Tube Mill: A tumbling mill with a length over diameter ratio (L/D) much larger than one, for example a ratio of 3/1.
- Tumbling Mill: A rotating horizontal cylinder partially filled with grinding media that tumble onto the ore to grind it.
- Tungsten: A heavy, steel-grey metallic chemical element having the highest melting point of any of the metals.
- Tyler Sieve Series: A brand of testing sieves that follow American Society for Testing Materials standard E-11-70. Tyler sieves are available from 38 microns (400 mesh) to 1.05 (26.5mm). 4~U.S.A Standard Sieve Series~A brand of testing sieves that follow American Society for Testing Materials standard E-11-70. U.S.A sieves are equivalent to Tyler sieves in the finer sizes, but go past the Tyler series in the coarse sizes, up to 5 (125mm).
- Ultrasonic Probes: A level of measurement in flotation cells.
- Underflow: The oversize material that leaves a cyclone.
- Undersize: The fine particle stream that leaves a classifier.
- Uniaxial compressive strength: The UCS is the maximum compressive force recorded at the point of ductile-brittle transition, divided by the cross sectional area of the sample.
- Vacuum: Suction force applied to a unit area.
- Valuable mineral: A mineral that can be treated at a profit. See ore.
- Velocity: Speed.
- Viscosity: The resistance of a fluid to flow.
- Voltage: Electromotive force or potential difference.
- Vortex Finder: The top opening of a cyclone through which the overflow leaves.
- Wet scrubber: A device for cleaning fine dust from contaminated air. It cleans by passing contaminated air through finely dispersed water sprays. The dust particles adhere to the water droplets and are scrubbed from the air.
- Work index: The amount of electrical energy required to carry out a size reduction process on a given quantity of rock. The crushing work index measures the energy required in crushing The grinding work index measures the energy required in grinding. They are not equivalent.
- Work Index: A measure of ore hardness which gives the energy required to grind one tonne of ore to a specific size.
- X-Ray Fluorescence: A phenomenon where material bombarded by X-Rays emits X-Rays of its own at specific frequencies.
For this list of terms used in mineral processing –> Thanks to METSO
https://www.911metallurgist.com/crushing-industry-vocabulary