The following paper deals with the problems that have arisen in the application of the flotation process to the beneficiation of non-metallic ores by flotation. The most important of these ores are listed and the commercial specifications of the desired products are given. The problems caused by the complexity of many of the raw ore deposits are discussed and illustrations are given, including a number of flow-sheets of typical milling plants, to show how these various problems were overcome.
Many technical papers have been written covering the theory and application of froth flotation to the non-metallic minerals. However, most of these data have been concerned with the uses of various flotation reagents and pulp conditions which, through experimentation, have been found to be best for obtaining the desired separations, and these data are, in many instances, more theoretical than practical. It is the purpose of this paper to present data from the practical standpoint of actual milling of some typical ores and, by these means, to indicate the problems involved.
INDUSTRIAL MINERALS EXTRACTION
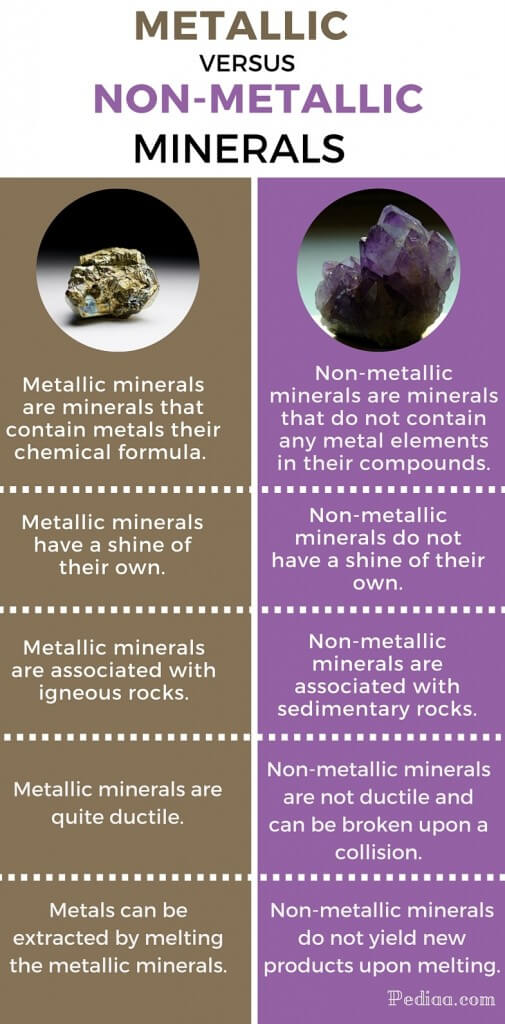
For the purpose of clarification of the meaning of the title of this paper, non-metallic minerals may be defined as those industrial minerals that are not primarily a source of metal production. Also, it is to be noted that the particular or special branch of the art of flotation that is applicable to concentration of these minerals may also be applied to beneficiation of certain metallic ores by concentrating or removing some non-metallic minerals as a by-product or as an impurity.The problems in the beneficiation of non-metallic mineral ores may be due to a number of conditions, which may require a combination of concentrating methods with flotation. Many of these minerals are in the low price brackets but, while the cost of fine grinding and flotation may be prohibitive, it may be economically possible to make a partial recovery of the values by the cheaper gravity concentration methods and to recover by flotation the slimed values which are lost by gravity in the case of some barite ores and low-grade fluorspar ores. Pre-concentration, using heavy media or coarse jigging, is often advantageous on low-grade ores to reject a large amount of the waste at a coarse size and produce an enriched and smaller tonnage for flotation. Another problem of much concern is presented by the occurrence in the ore of two or more basic minerals such as barite, fluorite, apatite, calcite, and dolomite, with acidic minerals such as feldspar, quartz, and mica. The presence of clay or other slime-forming minerals—which are classed as “interference” substances—reduces the effectiveness of most combinations of reagents and in many cases inhibits flotation.
The most effective separations of non-metallic minerals are accomplished where a single basic-type mineral is floated from one or more acidic-type minerals, as for instance the flotation of crystalline fluorite from quartz. This separation depends upon the fact that the two minerals may be readily freed from each other by grinding to flotation particle size. However, when the association of the minerals is close or the texture of one or both is such that the minerals cannot be entirely freed by grinding, a problem is presented. Middling particles may be produced under these conditions that cause a lowering in the grade of the finished concentrate or which may pass into tailing, with resulting low recovery of the valuable mineral. Under such conditions, the mill flow-sheet must be arranged to overcome as far as possible the effects of such close association.
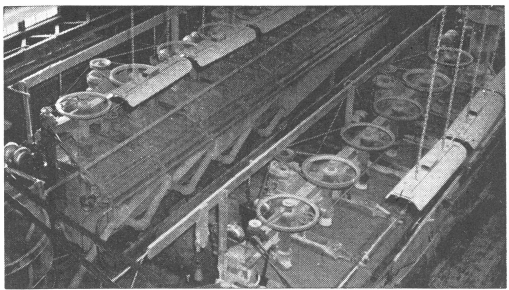
From our experience in testing and developing flow-sheets for many ores from all parts of the world, we have found that, in order to develop the most efficient concentration flow-sheet, a complete investigation of each individual ore is necessary.
The flowsheet must produce a product that will meet the market specifications for its sale, i.e., the concentrate must contain the minimum of impurity content and the required amount of the desired mineral content at the desired particle size. The problem presented may be further complicated by the conditions which exist in the locality where the deposit to be exploited is found. For this reason, the fullest information concerning climatic conditions, amount and purity of water available, and distance from cheap transportation and market, are desirable.
In the following pages, flotation of the most common industrial non-metallic minerals is discussed, with notes on market specifications, the problems of production most commonly encountered and the reagent combinations most commonly used to effect the separation of the valuable mineral.
Some non-metallic minerals that actually are sources of metals are included because of the important application of flotation as a means of freeing them from associated minerals that are of no value so that the resulting concentrate may meet market specifications.
Source:
This article is a reproduction of an excerpt of “In the Public Domain” documents held in 911Metallurgy Corp’s private library.