Table of Contents
- Merrill Crowe Plant Design Parameters
- Effect of CYANIDE STRENGTH and ALKALINITY in Merrill Crowe
- FEEDING ZINC DUST in a Merrill Crowe Plant
- USE OF LEAD SALTS in Merrill Crowe Processing
- EFFECT OF COPPER ON PRECIPITATION on Merrill Crowe
- EFFECT OF LEAD ON PRECIPITATION in Merrill Crowe
- TREATMENT OF Merrill Crowe PRECIPITATE
- TYPES OF BULLION MELTING FURNACES
- TESTING Cyanide SOLUTIONS IN Merrill Crowe
Efficient Merrill Crowe precipitation of gold and silver is dependent upon the proper control of certain physical and chemical properties of the solution. The most important of these properties are listed below:
- SUSPENDED SOLIDS, such as ore slime and precipitates of calcium carbonate, with hydrates of aluminum, magnesium and iron, present in the pregnant solution before clarification. These combined solids should be completely removed by efficient clarification.
- SUSPENDED PRECIPITATES, as above defined, which may continue to form in the solution AFTER clarification. This formation occurs slowly and is almost completely prevented by clarifying and precipitating simultaneously.
- SCALE FORMING COMPOUNDS, chiefly the carbonates and sulphates of lime.
- OXYGEN AND CARBON DIOXIDE GASES DISSOLVED IN THE SOLUTION.
- CYANIDE STRENGTH
- ALKALINITY
CLARIFICATION
In Merrill Crowe, perfect clarification is probably the most important factor in obtaining efficient precipitation. It should move all suspended solids from the pregnant solution, when those colloidal suspensions invisible to the naked eye. Long experience has shown that such clarification is most effected in low pressure vacuum leaf filters of special design to facilitate handling and changing covers. Details of this leaf are shown with a drawing and description of the complete unit. This includes the equipment used in the recently developed Pre-Coat conditioning of the clarifier leaves, without which the present perfection of clarification would not be possible.
Since filtration is effected under a negative pressure, partial removal of dissolved oxygen has already been effected when the solution enters the Crowe receiver, where the de-oxygenation is completed. By thus clarifying and de-aerating simultaneously, the capacity of the vacuum receiver is considerably increased, and the substantially complete removal of oxygen is greatly facilitated.
Pre-coat Clarification plays another important role in preparing solution for precipitation. Carbonates and sulphates of lime are present in varying amounts in all cyanide solutions and tend to deposit scale on all exposed surfaces. Conditions within the precipitate filter cake are particularly favorable for such deposition and the deposit thus formed not only covers the zinc surfaces and increases the consumption but also impedes the flow of solution through the filter fabric, causing high pressure and necessitating frequent removal of the filter cloth.
With the advent of Pre-coat Clarifcation this difficulty is minimized because a large proportion of the scale forming compounds, which might cause later trouble in the precipitate filter, are deposited on the enormous surface areas of the diatomaceous silica used as a Pre-Coat layer on the clarifying leaves. Since these filters are frequently washed and the layer of Pre-coat renewed, the deposition and elimination of the scale at this point is highly desirable.
Merrill Crowe Plant Design Parameters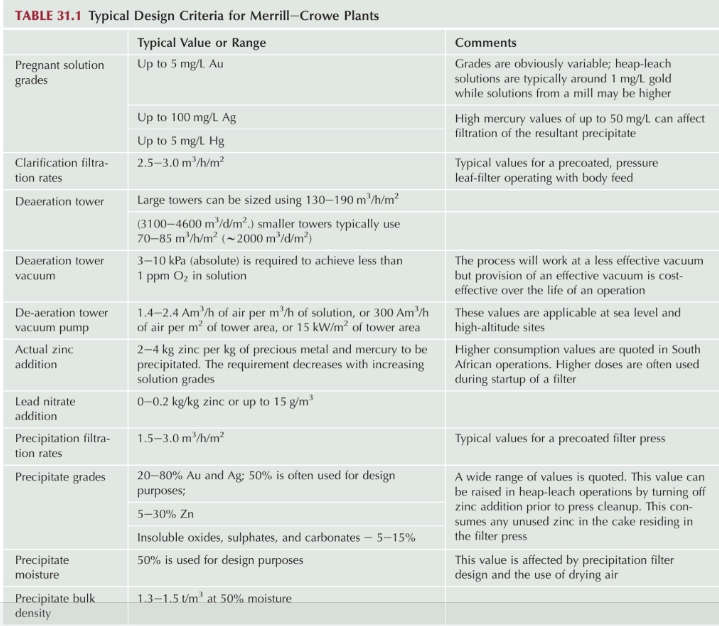
In plant operation one or more of the clarifying leaves should be removed daily and the adhering layer of Pre-Coat and slime washed off with a jet of water or solution. The Pre-coat layer greatly facilitates this washing besides prolonging the life of the filter fabric and maintaining its permeability, i.e.: the filtering capacity of the leaf.
In starting new plants, all solution tanks and pipe lines should be thoroughly washed out with lime water to remove oil and grease which otherwise will cause serious pressure trouble in the clarifying and precipitating filters.
THE OPERATOR SHOULD KEEP IN MIND THAT IMPERFECT CLARIFICATION IS THE MOST FREQUENT CAUSE OF PRECIPITATION TROUBLE AND THAT CAREFUL ATTENTION TO CLARIFICATION DETAILS WILL BE WELL REPAID IN IMPROVED PRECIPITATION RESULTS. THE CLARIFIED SOLUTION MUST BE NOT MERELY “CLEAR” BUT BRILLIANT LIKE THE BARREN SOLUTION ISSUING FROM THE PRECIPITATE FILTERS, AND NO WASHED AND PRE-COATED LEAF SHOULD BE RECONNECTED TO THE MAIN VACUUM MANIFOLD UNTIL THE CIRCULATING EFFLUENT SHOWS SUCH CLARITY.
DE-AERATION or REMOVAL OF DISSOLVED GASES
Efficient and complete precipitation of metals from cyanide solutions requires that the solution, after clarifying, be further conditioned by the substantially complete removal of dissolved oxygen. Complete Merrill Crowe precipitation cannot take place in the presence of even traces of free oxygen. Hydrogen, formed when metallic zinc precipitant dissolves in alkaline cyanide solution, will combine with and nullify the effect of free oxygen, but at the expense of a wasteful consumption of zinc and cyanide and the formation of troublesome by-products. In the Merrill-Crowe Process the oxygen is mechanically removed in a preliminary conditioning step, by subjecting the solution to the action of a high vacuum. Carbon dioxide is simultaneously removed, thus minimizing the formation of calcium carbonate in the precipitate filter.
SIMULTANEOUS CLARIFICATION DE-AERATION and PRECIPITATION
The remarkable efficiency of the Merrill-Crowe Precipitation Process is largely due to simultaneous clarification De-aeration of the solution followed by the immediate addition of suitably activated zinc dust and precipitation of the metals without rest and without exposing the solution to re-absorption of atmospheric oxygen. Most cyanide solutions after clarification will, upon standing even for a short time throw out suspended colloids, consisting largely of the hydrates of alumina magnesia and iron. Although hardly visible to the naked eye, these precipitates frequently form in sufficient quantity to coat and insulate the zinc, increasing the pressure in the precipitate filters and seriously interfering with precipitation. Under certain conditions a colloidal precipitate of copper cyanide (Cu2CN2) is similarly formed. These difficulties are minimized and in most cases entirely prevented by Simultaneous clarification De-aeration and Precipitation.
Effect of CYANIDE STRENGTH and ALKALINITY in Merrill Crowe
Alkaline cyanide solutions resulting from the treatment of most ores will usually contain appreciable amounts of free cyanide and lime. Generally speaking, the cyanide content required for maximum dissolution of gold and silver, is greater than that required for effective precipitation, which on a previously de-aerated solution need be no more than sufficient to dissolve the requisite amount of zinc to cause precipitation and to hold in solution the by- product compounds, such as zinc hydrate, which are formed when metallic zinc is dissolved in cyanide solution. . “Banket” ore of the Rand is a notable exception to the above statement. when the ore is finely ground, the gold dissolves rapidly in very weak cyanide, so weak in fact, that it is customary to add a small amount of fresh cyanide to the solutions before precipitation. If otherwise properly conditioned, it may be stated that solutions titrating 0.1 lb. or more NaCN per ton are readily precipitated, and that even as little as 0.05 lb. NaCN may frequently be sufficient. However, where these minimum strengths are used, it will be found that a continuous drip of strong cyanide solution added to the zinc emulsifier will sometimes be helpful in activating the zinc and ensuring trace barrens. The lower cyanide strengths are more favorable, to the precipitation of copper and where substantial amounts of this metal are dissolved from the ore, the pregnant solution should contain sufficient free cyanide to hold the, copper in solution.
The chief functions of lime used in cyanidation are to neutralize acid cyanicides in the ore and to promote coagulation and settlement of the ore pulp to facilitate filtration and to assist clarification of the decanted solution. Less frequently high lime content may be required to decompose the sulphides, of silver or the sulphotellurides of gold. So far as precipitation is concerned, very little lime is needed; merely enough to ensure the solubility of the added lead salt as alkali plumbite and to coagulate the zinc precipitate to ensure rapid and perfect filtration. Unnecessarily high lime during precipitation is apt to cause a wasteful consumption and hydration of the zinc, according to the following equation;
The calcium zincate thus formed is soluble if sufficient cyanide is present, but otherwise remains in suspension as a coating on the zinc surfaces, thus seriously interfering with precipitation. This and imperfect clarification are the principal causes of excess pressure, in prectpitate filters. In treating silver ores, the solutions must of course contain sufficient alkali to decompose the double cyanide formed when silver is precipitated on zinc, and to re-form alkali cyanide after, precipitation. As pointed out elsewhere it may be desirable to raise or lower the alkalinity, for the purpose of controlling deleterious colloids, or precipitates occurring in some solutions. Any such change should be made GRADUALLY by altering the lime feed to the grinding circuit or to the agitators; do not add lime, to pregnant solution storage tank or to clarifier. Proper alkalinity for any given ore or solution can only be determined by actual trial and experience.
FEEDING ZINC DUST in a Merrill Crowe Plant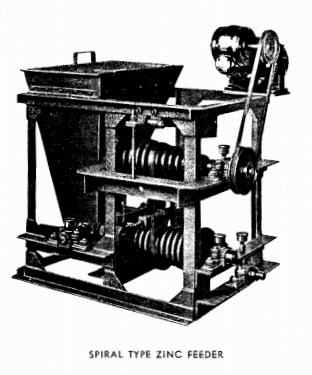
Equipment for feeding zinc dust is now well standardized and is shown in the photographs 1, 2 and 3 . The spiral feeder is sometimes used but the belt type is usually preferred. Either clarified and de-aerated pregnant or barren solution may be used to form the zinc emulsion, the amount approximating one to two g.p.m. for small plants and 3 to 5 g.p.m. for larger tonnages. The amount of zinc dust required varies with the character of the solution, with the nature and amount of impurities present and the metals to be precipitated. On clean gold ores the zinc dust consumption varies from .02 lb. to .06 lb. per ton of solution. These figures will be increased by the presence of appreciable amounts of silver or copper. In the cyanidation of silver ores, where the solutions may contain several ounces of silver per ton, the zinc consumption will approximate 0.6 oz. per ounce of silver precipitated.
USE OF LEAD SALTS in Merrill Crowe Processing
The precipitation of nearly all gold solutions and of some silver solutions is improved by the addition of a soluble lead salt, which immediately precipitates metallic load on the zinc, forming a very active zinc-lead couple stimulating precipitation of the precious metals. Either lead nitrate or lead acetate may be used although the former is preferable since it is more readily soluble. With some cyanide solutions, the addition of a soluble lead salt, either nitrate or acetate, has a tendency to form insoluble lead compounds. The character of this precipitate varies in different solutions and may contain lead cyanide, sulphate, chloride, or basic lead carbonate. These precipitates tend to choke the precipitate filters and may seriously interfere with precipitation. Therefore, where such conditions exist, the lead salt should be added to the solution before clarification, either to the pregnant solution storage tank or to the inlet of the clarifier, where the precipitated lead compounds are filtered out. Where no appreciable amount of insoluble lead precipitate is formed, the lead salt may be added in the form of a continuous drip to the zinc emulsifier, where it is immediately precipitated as a black film upon the zinc particles. As pointed out elsewhere, a simple form of liquid reagent feeder is used to add the load solution either to the zinc emulsifier, to the clarifier, or to the pregnant storage tank as desired.
The amount of lead salt used varies widely depending upon the nature of the solution being precipitated. On gold solutions the quantity may vary from as little as 5% to as much as 25% of the weight of zinc used. In treating ores containing lead which is soluble in alkaline cyanide solution, as for example silver ores containing lead carbonate, no additional lead salt is required. Similarly where the solutions contain appreciable amounts of silver or copper the added lead salt may not be needed, since these metals themselves form efficient precipitating couples with the zinc, and a porous, spongy precipitate which filters readily.

The successful use of lead salts requires careful supervision at all times, since if added at the wrong place, or not uniformly coated upon the zinc more harm than good may result. We have already stated that imperfect clarification is the most frequent cause of precipitation trouble; improper use of lead salts is probably the next. Careful study of both will well repay the operator.
EFFECT OF COPPER ON PRECIPITATION on Merrill Crowe
The presence of appreciable amounts of copper in cyanide solutions is usually accompanied by high cyanide consumption and may also decrease extraction if allowed to accumulate beyond certain limits, it seriously interferes with zinc shavings precipitation, causing plating or coating of the zinc and stopping precipitation of the precious metals. However, in the Merrill-Crowe Process, using zinc dust precipitant, the presence of copper has no detrimental effect other than to increase the zinc consumption and lower the grade of precipitate produced. Because new, fresh surfaces are exposed by the constant addition of finely divided zinc, precipitation of the gold and silver is complete, irrespective of the copper present.
EFFECT OF LEAD ON PRECIPITATION in Merrill Crowe
As already stated, the presence of small amounts of lead in solution is beneficial to precipitation. However, in cyaniding ores containing appreciable amounts of soluble lead such as lead carbonate, the amount of lead dissolved and precipitated may cause excessive consumption of zinc and a low grade or base precipitate which is difficult to refine. Lead does not readily combine with alkaline cyanide; the amount dissolved is determined by the lime present to form calcium plumbite. By keeping the lime at the minimum required for settlement, dissolution of lead can usually be kept down to a reasonable amount.
TREATMENT OF Merrill Crowe PRECIPITATE
The character and grade of precipitate produced in the Merrill-Crowe process will depend upon several factors. The most important is the nature of the ore being treated the amount of gold and silver and of base metals, copper and lead dissolved by the solutions. Clarification, of course, determines the amount of impurity such as ore slime: with the advent of Pre-Coat Simultaneous Clarification Precipitation this is now almost negligible. De-aeration and chemical control of the solution will largely determine the amount of zinc and zinc by products in the precipitate. With clean gold ores the product may contain from 6o% to 9o% gold and not to exceed 5% to 10% total zinc. On mixed gold and silver ores and particularly where the silver is relatively high, the precipitate may run as high as 95% combined gold and silver with only 3% to 5% total zinc.
Owing to the high grade precipitates now generally obtained, most plants in the western Hemisphere melt direct without preliminary treatment other than partial drying. In Africa, and particularly on the Rand, the “gold slimes” are acid treated and calcined, while in Australia melting is generally preceded by calcining. The purpose xxxxd treatment with sulphuric acid to remove excess zinc, while calcining, with or without an oxidizing agent such as nitre, is to oxidize the base metals so that they may be slagged off in molting. The above statements apply primarily to gold ores; high grade silver precipitate is invariably melted direct.
TYPES OF BULLION MELTING FURNACES
Three types of melting furnaces are in general use, all oil fired. For smaller plants, treating gold ores, the tilting furnace with removable graphite crucible is usually preferred. Clay liners are quite generally used to prolong the life of the pot.
In larger plants particularly those treating silver ores, ting furnaces of the reverberatory type are most satisfactory, Such furnaces are provided with a molded hearth of suitable refractory and may be either single or double depending on the amount of precipitate to be handled.
In the largest mills, treating either gold or silver ores stationary reverberatory furnaces are used. These may be built to operate as a conventional reverberatory furnace, with the usual fusion hearth of firebrick, or other suitable refractory, or may be used as reverbaratory pot fusion furnaces, with lined graphite pots. This is the furnace generally used in the large mills on the Rand.
Precipitate containing up to 30% to 4o% moisture may be fluxed and melted without drying, or dryers, either steam or electric may be used to reduce the moisture, to from 15% to 2o% before adding flux and charging to the furnace. Where filter presses are used, blowing with compressed air yields a suitable product for melting without further drying.
MELTING FLUXES
Fluxes used in melting cyanide precipitate vary somewhat in different parts of the world: the following mixtures are typical but in starting a new plant trial fusions should be made in each case, to determine the most suitable mixture. For melting raw precipitate from clean gold solutions the following charge will usually give rapid fusions and clean fluid slags.
- 75 lb. precipitate (15% to 20% moisture)
- 45 lb. manganese dioxide
- 50 lb. borax
- 25 lb. silica sand
Note: Soda bi-carbonate or fluorspar may be substituted for part of the borax and the manganese may be replaced by nitre.
Silver precipitate, containing 80% or better of silver, is readily melted with the following charge:
- 100 lb. precipitate (15% to 20% moisture)
- 3 to 5 lb. soda bi-carbonate
- 5 to 10 lb. borax
- 3 to 5 lb. silica said
For melting calcined gold precipitates the following charge is used in many plants:
- 100 lb. dry calcine
- 10 lb. soda ash
- 25 to 40 lb. silica sand
- 5 lb. fluorspar
- 40 to 60 lb. borax
Note: 5 to 15 lb. manganese dioxide may be added in some cases.
TESTING Cyanide SOLUTIONS IN Merrill Crowe
The following methods will be found useful for the rapid estimation of gold or silver in barren or precipitated solution. With practice, both estimations can be made with considerable accuracy but are, of course, intended to be entirely supplementary to the regular shift and daily assays.
DOWSETT’S ESTIMATION OF GOLD IN CYANIDE SOLUTION
Take approximately 1000 cc. solution in a tight stopper jar. (A quart Mason jar is convenient.)
- Add saturated solution of NaCN to bring the solution to be tested up to about .10% NaCN.
- Add two drops of lead acetate. (Clear saturated solution.)
- Add a pinch of zinc dust (approx. 2 grams).
- Shake well for about two minutes.
- Pour into large evaporating dish. Settle and decant clear solution.
- Add 10 cc. aqua regia and evaporate nearly to dryness.
- Take up in 2 cc. conc. hydrochloric acid.
- Pour into small test tube and cool thoroughly.
- The tube should be about 3 to 4 inches long and not over 3/8 inch diameter, and the cooling is important.
- Incline the tube and add a few drops of fresh saturated stannous chloride solution.
The presence of gold will be indicated by a purplish ring at point of contact or by a purplish tinge throughout if the tube is shaken.
The evaporation may be performed over a spirit lamp or similar flame and does not take over five minutes. The presence of as little as .02 dwt. Gold per ton of solution is very plainly shown.
ESTIMATION OF SILVER IN CYANIDE SOLUTION
A few drops of a 10% solution of sodium sulphide added,to 25 or 50 cc. of the. solution to be tested, gives a pure white precipitate of zinc sulphide in the absence of silver. The precipitate becomes brownish in the presence of silver, and the depth of color is a very close indication of the amount present.
The presence of the usual small amounts of lead in the solution does not affect the result appreciably.
THE ESTIMATION OF OXYGEN IN CYANIDE SOLUTION
During dissolution of the metals, cyanide solutions should of course contain oxygen; before subsequent precipitation of the metals, all of the free oxygen should be removed. Oxygenation s accomplished by contacting the solution or pulp with air in various types of agitators: removal of the free oxygen is affected by the Merrill Crowe Process, in which thin films of solution are exposed to a high vacuum in a suitable receiver.
Ordinary water and most cyanide solutions, except those containing unusual amounts of reducing agents, such as sulphocyanide or sulphides, saturate rapidly with oxygen and all cyanide solutions of which we have any knowledge give off all but traces of free oxygen in passing through the Crowe apparatus. Also solutions which have, been completely precipitated, either by zinc dust or by zinc shavings. usually contain no free oxygen.
A systematic study of the oxygen content of solutions at various stages of mill operation has, in several cases within our knowledge. led to material improvement and savings. A deficiency in oxygen may be found in agitators or thickeners and the effluent from the Crowe receiver should be checked to make certain that substantially all of the free oxygen is removed before precipitation. The most suitable methods for determining oxygen in cyanide solutions are given below.
Fill one of the 250 cc. bottles with the solution to be tested. Use a rubber tube reaching to the bottom of the bottle and avoid all agitation. A drop or two of kerosene oil in the bottle will film the solution and still further prevent absorption of oxygen. Fill the bottle nearly full, then add 1/10 gm. pyro and I cc. of 2N.NaOH, and stopper instantly, taking care that no air bubble is left under the stopper. Shake well and compare with standard colors.
Some solutions, particularly those resulting from the cyanidation of silver ores, show fading colors and become cloudy on the addition of pyro and soda. In such cases a better comparison is made after standing a definite time, say three to six minutes. Also on such solutions a better standard color is obtained by making up with regular plant solution to which is added the usual amount of soda and pyro. Then after standing from three, to six minutes, this color is matched with the dye or caramel and the fractional standards prepared as usual. A small amount of sold pigment, such as yellow ochre, added to the dye or caramel solution will match precipitate which sometimes forms. With such solutions it is better to make up a fresh set of standards whenever oxygen tests are to be made.
This method depends upon the reducing action of a standard sodium hydrosulphite solution on indigo blue. After all the oxygen has been titrated, any excess of hydrosulphite changes the indigo blue test to indigo white. The method is said to be accurate to tenths of a milligram per liter of solution, although such accuracy is not required for the purposes under discussion. We refer to the author’s paper for a full discussion of the method.
Chart A, Fig. l, is used to determine barometric pressure at various altitudes; Chart B is used to determine standard saturation values for various temperatures and pressures. In Chart A, altitudes, in feet, are plotted on the horizontal axis and pressures, in millimeters, on the vertical axis. To find the pressure corresponding to a certain altitude, follow the elevation line downward to its intersection with the curve X, then horizontally to the right and read the pressure. For example, if the elevation is 6000 ft., the 6000-ft. line is followed to its intersection O with the curve X, then the corresponding pressure, 607 mm., is obtained from the right-hand side of the chart.
In chart B, temperatures are plotted on the horizontal axis and the amount of oxygen, in milligrams per liter of distilled water, is plotted on the vertical axis; various pressure curves also are plotted as shown. To find the saturation value for a certain temperature and pressure follow the temperature line upwards until the point corresponding to a given pressure is reached, then follow horizontally across to the left-hand side of the chart and read off the amount, in milligrams, of oxygen per liter of solution. For example, to determine the amount of oxygen in a solution having a temperature of 590 F. at an elevation of 6000 ft. it has already been found that at an elevation of 6000 ft. the pressure is 607 mm.: therefore the 607-mm. pressure curve must be used: that is, it is necessary to interpolate between the 600-mm. and the 650-mm. curves. The 590 F. line is followed to its intersection R with the 607-mm. curve, then from the left hand side of the chart is read off 8 mg. of oxygen per liter. The same procedure is used for the various pressure, using the curve corresponding to the particular pressure. For any particular plant, a solubility curve for that elevation should be plotted.
WHITE’S METHOD
This method was developed by Mr. H. A. White, Consulting Metallurgist for the Union Corporation at Johannesburg, South Africa, and is based upon the color imparted to an alkaline solution on the addition of pyrogallic acid, the “pyro” used in photographic work.
APPARATUS REQUIRED:
- 1 doz. 250 cc. glass-stoppered bottles
- 1 burette
CHEMICALS REQUIRED
- Sodium Hydrate (NaOH) Solution, 2N (80 gm. Per liter.)
- Pyrogallic acid or “pyro” (the crystalline salt is preferable to the powder.)
- Brown dye (Diamond Brown or Caramel).
PREPARATION OF STANDARD COLORS
Saturate a quantity of ordinary hydrant water with oxygen by passing air through it for an hour. Then let stand for another hour to remove bubbles of occluded air. Fill one of the 250 cc. bottles with this water add about 1/10 gm. Of pyro and 1 cc. of 2N. NaOH. The pyro crystals must immediately sink below the surface. Then insert glass stopper with a twisting motion to exclude any small air bubbles. After adding the soda solution, the bottle should be full to within a quarter-inch of the top, so that the stopper may be inserted at a slight angle. Shake bottle until all the “pyro” is dissolved.
The water will take on a reddish brown color corresponding to the oxygen content of oxygen saturated water at the existing temperature and pressure. The percentage oxygen content of water. saturated under any given set of conditions, may be calculated from the tab1e of Roscoe and Lunt, Volumetric Analysis, Sutton, or from the chart of weinig and Bowon shown below.
This color is then matched with a water solution of diamond dye or caramel A small amount of chromate of potash will sometimes assist in obtaining the exact shade.
Let us assume that under the existing conditions the saturation point of water corresponds to 8 mg. oxygen per liter. Then if standard bottles are made up containing I part of the color corresponding to saturation and 7 parts water this lighter color will correspond to I mg. oxygen per liter and equal parts of standard color and water will correspond to 4 mg. of oxygen. In the same way make up a series of eight bottles the colors of which represent oxygen contents of from I to 8 mg. oxygen per liter.
CROWE’S LABORATORY PRECIPITATION METHOD
The following method of precipitating cyanide solutions will frequently be found useful in testing laboratory. It depends upon the elimination of dissolved oxygen from the solution by the addition of a chemical reducing agent which may be either sodium or calcium hydrosulphite. While the reactions involved are not strictly comparable with actual plant practice, the results will be found to check closely with those obtained by mechanical de-aeration of the solution as practiced in the Merrill-Crowe Process.
Complete precipitation of gold and silver from cyanide solutions with zinc dust requires that all free oxygen be first removed or neutralized. The precipitant itself can accomplish this but with a wasteful consumption of zinc. Exposure to a high vacuum removes from 90% to 95% the oxygen and the remainder is consumed by reaction with the zinc or by the addition of a small amount of hydrosulphite. As a laboratory procedure it is simpler to add sufficient of the reducing agent to combine with all of the dissolved oxygen initially present or which may be introduced during the tests.
METHOD A
To 1000 cc. of the solution to be precipitated add 150 mg. of sodium hydrosulphite. Then emulsify 100 mg. of zinc dust in 10 cc. of distilled water to which has been added 10 mg. of lead nitrate. Add the emulsion to the solution and stir intermittently for 30 minutes. Filter rapidly on a 2-inch Buchner filter with double filter paper which has been suitably pre-coated with paper pulp or diatomaceous silica.
N.B. The solution should be stirred gently to minimize introduction, of air, and the filtration stopped before all the solution is through, this, also top prevent aeration. If the solution contains appreciable amounts of silver or copper, the zinc dust should be increased accordingly.
METHOD B
Dissolve 100 mg. of zinc dust in 20 cc. of distilled water, saturated with sulphur dioxide. Neutralize with a slight excess of calcium hydrate and filter on a small filter. Add the clear filtrate of calcium hydrosulphite to 1000 cc. of the solution to be precipitated. Then add the lead-zinc emulsion and proceed as in Method A.
https://www.911metallurgist.com/merrill-crowe-process-equipment
References:
The Merrill-Crowe Process, Simulataneous: Pre-Coat Clarification, De-Aeration, Precipitation by Merco. THE MERRILL COMPANY ENGINEERS
Zinc-dust cementation of silver from alkaline cyanide solutions analysis of Merrill-Crowe plant data