Sampling is the most important procedure in arriving at the value of an ore. Improper sampling makes other procedures, including assaying, valueless, as the sample must truly represent the ore from which it is taken. Before sampling, clean fresh faces must be exposed in order to prevent the possibility of salting.
Having taken a large representative sample by chiseling 3″ to 6″ wide and 1″ to 3″ deep completely across the vein, the larger pieces are broken up and the entire sample thoroughly mixed on a sampling cloth. The whole shoveled into a uniform cone, flattened into the shape of a pie, and divided into quarters. Two opposite quarters are taken out and the remaining ore piled into a cone. This procedure is repeated with a further breaking up of the larger lumps between quarterings until a suitable sized sample remains usually five to ten pounds. This is then taken to the assay office.
As one piece of ore may be rich and another worthless, or the same piece rich on one end and worth less on the other, the sample must be the average of all the ore and contain hundreds of small pieces, thus the necessity for a complete breaking up of all the rock in a sample. The smaller the size (preferably not greater than one-quarter inch), the more accurately will the sample represent the true value of the ore.
In sampling placers the variations are so great, and the values as a rule are so low, that weighed samples should be taken and the whole panned to as small a weight as possible and the entire amount of concentrates taken to the assay office for calculation of results. Samples should reach bedrock. There are many splendid sampling devices in general use.
Fire Assaying for Gold and Silver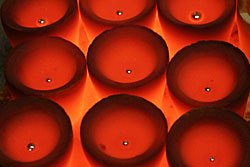
The following description of what is done with samples submitted for assay is given in the hope of supplying acceptable information to those who are not familiar with the details of assaying.
- A record must be made for each sample, giving the name and address, the date, the owner’s mark, the things to be assayed for, the amount of the charges and any other special instructions.
- The sample must be dried, if not already dry.
- The entire sample must be put through a fine crusher, which is first thoroughly cleaned.
- The crushed sample is mixed and quartered until only 8 or 10 ounces remain, which portion is a true representative of the whole sample.
- The unused portion known as “rejects” is now filled with duplicate markings of the original tag. This is done for two reasons: to provide a source for a duplicate sample should an accident happen to the original, and to have the sample for delivery to the owner if requested, or if required for other purposes.
- The sample of 8 to 10 ounces is ground to a very fine powder in a pulverizer, also thoroughly cleaned, being passed through the pulverizer repeatedly to insure complete pulverization and thorough mixing. Not only is the machine cleaned by brushing, but to guard against any possibility of one sample being mixed with even a small bit of another, a blank sample (known to contain no precious metals) is put through the pulverizer between samples.
- The pulverized sample, with its identifying tag, is now taken to the weighing and fluxing room where charges are weighed carefully and put into fire clay crucibles along with the proper fluxes. The fluxes and the ore are thoroughly mixed and covered.
- The prepared samples are now removed to the melting room where they are fused in the assay furnace. After fusion, which requires about 30 minutes, the molten charges are poured into molds This is smelting on a small scale with (of course) much more refined fluxes.
- Upon cooling, the worthless slag is freed from the base bullion which has settled to the bottom of the mold. This bullion, consisting mainly of lead, which was added with the fluxes in the oxide form. Contains the gold and silver in the ore.
- The bullion is carefully freed from all adhering particles of clay by pounding and shaping into a
cubelike form. - The bullion is now ready for refining and is subjected to a treatment in the muffle furnace known
as cupelling. Here the lead in the base bullion is changed to lead oxide and is absorbed into the cupel leaving the gold and silver in a refined state as a bead. This is refining on small scale. - The Assaying beads are now removed from the cupels and are carefully cleaned to detach any small particles that might be adhering to them.
- The beads are now weighed on the assay balances and the weight recorded. This is the combined weight of both gold and sliver.
- The beads are now treated with acid to remove the silver. This is called parting. The acid dissolves the silver, leaving the gold untouched In the form of a sponge. The gold sponge is carefully washed and dried, and is weighed on even more delicate scales than the one used for the combined beads. When the weight of the gold is determined. It is deducted from the weight of the combined button. Thus is obtained the total gold and silver in the ores.
- After the weighings are completed, the calculations are made and a certificate made out, showing the gold and silver in ounces and the value in dollars per ton of ore. This certificate is checked with the original record, signed, sealed and mailed out if requested.
- This however, does not conclude the attention given the work. The unused portion of the ground sample known as “pulp” must be filed for reference so that any time within 60 days the pulp may be called for and delivered to the owner. At the expiration of sixty days, if not called for, the pulp is carted to the dump.
- The dally record is indexed so that in case the customer wishes a copy of the certificate, the original record is made available without delay.
This describes the ordinary fire assay for gold. Different ores require somewhat different manipulations. But the fire assay remains the preeminent method for all classes of gold and silver ores and their products. This applies equally to platinum, palladium, iridium, rhodium, ruthenium, whether oxidized ores, sulphides, tellurides, or base ores of all kinds or colloids from photographic work, or gold or silver or platinum in any form.
Every conceivable interference has deliberately been added to weighed amounts of gold and silver and the proper assay then performed, and without a single exception a satisfactory check has been obtained between the amount of gold weighed In and the amount of gold recovered. Likewise, but with somewhat more variation, the silver has also been recovered. The losses are known.
The U. S. Bureau of Mines has made extensive tests of claims conflicting with the above and has invariably proven them either mistaken or fraudulent. All other competent investigators have reached the same conclusion.
A chemical method has been devised for field use. An iodine solution for dissolving the gold is used and the gold precipitated by re-distilled mercury which is later parted with nitric acid. The method, when properly performed. In every detail checks the fire assay closely. It is a slow and tedious method, however, and requires skilful operation.
In case of tellurides, a heavy enough button is required to prevent a high percentage of Tellurium in the lead which would cause the lead to wet the cupel and cause the whole alloy to sink into the cupel without oxidizing properly.
Volatilization is only a minor factor contrary to absurd stories.
Arsenides are rather hard to decompose, reports of as much as five per cent loss in the slag or 1/20 of the value having been reported by Chas. Butters. Roasting is an insurance of good results.
Antimony will cause the cupel to swell and break if in too large an amount. Adding a large amount of lead, or scarifying the button with lead, will overcome the difficulty.
Cobalt and nickel will cause the cupel to coat over with a film of their oxides. If there is not enough lead present, more lead or scorification will remedy this.
Much copper will give a copper button. More lead will remedy this, or what is called the combination method can be used or more lead and scorification.
To test losses, all possible interferences have been added and the highest loss recorded was about 14% under very much more severe conditions than ever existed in any properly conducted assay. On a $100 gold assay, the loss should not exceed sixty cents per ton.
The occurrence of commercial quantities of platinum in ore is rare.
The presence of platinum, and its allied metals, can be detected in the ordinary process of parting gold and silver. Depending on the amount of platinum present, the parting solution will be discolored, the color ranging from faint yellow to deep orange. An assay should be made for platinum whenever the parting solution is even slightly discolored after a slight dilution with water to remove colors produced by the action of nitric acid on silver.
Analysis of ail ores, metals, minerals and metallurgical products is familiar to thousands of chemists whose results on any identical samples check within narrow limits.
There is no ore, metal, mineral or metallurgical product which cannot be analyzed or recovered by standard methods or processes, all claims to the contrary notwithstanding.
Warning is given against anyone having special methods or secret processes for chemical analysis, assay or recovery. None of such methods have ever, at any time, made any success.
High sounding technical terms should always be a warning! Beware of mysteries! “Colloidal, Sub-atomic, Allotropic, Amorphous” and many other terms are used by frauds who have been exposed by the U.S. Bureau of Mines, notably in their Bulletin 2496, of 1922.