Let me explain as to how a Sieve Analysis is done. If you take a sample of ground ore, heat it until it is completely dry. Take 500 grams of that sample, and place it on top of a set of screens designed for size analysis. These screens have a graduated mesh size. The screen with the largest opening between the wires will be on top of the pile and the screen with the smallest openings will be on the bottom.
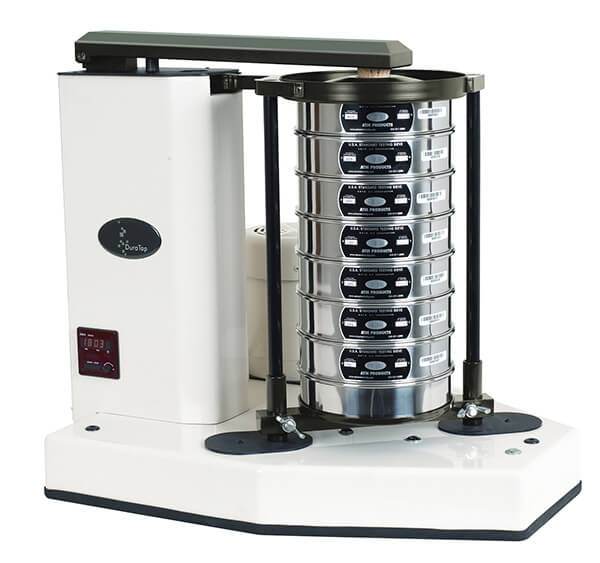
Vibrate this stack of -screens until all of the mineral has had a chance to filter down to the size of mesh that is small enough to support it. Then very carefully weigh the amount of ground rock that is on each of the screens. You will be able to determine the size of mesh that held the greatest amount of rock. By either assaying the contents of each screen or by visually evaluating the contents through a microscope it is possible to determine to what size the ore has to be ground to, to be able to collect the required amount of mineral.
This is called a SCREEN ANALYSIS. When a screen analysis report is made the size of each individual screen mesh is measured in two ways first by the number of holes per square inch of the screens surface or the size of the hole. If the screen size is reported as a 200 MESH SCREEN you will know that there are Two hundred holes for every square inch of screen.
On the other hand if the size is reported as 74 MICRONS the space between the wires is 74 microns in width. It is the space that is between the wires that is being measured. Most assay labs report the results of a screen analysis in mesh size instead of microns. The range of sizing usually is between 65 mesh and 325 mesh. As a point of interest, 400 mesh is so fine that cold water won’t go through it. Gasoline will, this means that if you have gas that has water in it gently pour it through a 400 mesh screen. The water will be retained while the gasoline will go through.
Now we have the amount of mineral that is in the ore, how hard it is to grind and the size that it has to be ground to. I suppose the next thing that I should explain is how the ore is ground.
Sieve Analysis
A sieve analysis of the ore will often supply information of considerable value. This may start at about 20 mesh and include the range of sizes to and including 325 mesh. A portion of each sieve size should be examined under the microscope and assayed for gold and silver.
A sample also should be separated into a sand portion and a slime portion. A series of such separations may be made, each starting with the ore crushed to a different degree of fineness. For example, a sample of ore might be crushed so that it all passes a 20-mesh sieve. The material is then separated by panning or by decanting under definite and controlled conditions into sand and slime fractions. Each fraction is weighed and assayed. Another sample of the ore might be ground to pass 65 mesh, and a similar separation made of sand and slime. Yet another separation might be made on the ore ground to pass 150 mesh. In this way the distribution of the precious metals can be determined under different degrees of grinding, and the possibilities for separate treatment of sand and slime thus indicated.
As a rule, preliminary cyanide tests are best made by agitation methods alone, and later the possibility of leaching a portion of the ore can be investigated.
No laboratory, whether used solely for research or for operation monitoring, will be complete without minimum sets of testing sieves and a sieve shaker. Throughout the research programs, the metallurgist will want to analyse the products with screens to determine how much work has been done or how much more work there is to do to permit the separation objective. In early research, a correlation between the chemical and screen analyses will be essential to determine where the values, contaminants and waste portions are concentrated but as the work progresses, the chemical analyses may not be required as frequently.
Knowing in which size fractions the metals of interest are concentrated, the metallurgist can formulate ideas of subsequent treatment such as regrinding or sand-slime separation, etc. Frequently, graphical plots of size analyses vs. other variables of interest will show sharp or adequate breaks in the curves to indicate the point at which a certain technique should be discontinued and a new attack planned.
However, screen analyses also can be misinterpreted or applied incorrectly. High chemical assays of the coarse fractions of a tailing may be the result of improper flotation conditions as frequently as they may be due to true middlings while mineralogical analyses may not be suitable since many middlings will float. Similarly, high metal values in the slime portion of a tailing may be a result of poor flotation practice. Thus, re-examinations of the grinding conditions periodically during flotation research are recommended.