Table of Contents
The gold cyanide leaching mill site is centrally located with respect to the mine, water supply and improved highway. This selection reduced both the length of the haulage road from mine to mill and main water supply line to a minimum. The location provided a sloping mill site, adequate tailings disposal area, housing space for both mine and mill supervisory employees and operating labor, plus a suitable area for assay office, machine and maintenance shops, lime kiln, power plant, in addition, strip for small planes for emergency usage. A tramway was installed to deliver ore from the mine portal to a point accessible for truck haulage for six miles to the mill. The water supply was developed by wells in the gravel of a river-bed and pumped four miles through a 4-inch line to the mill site.
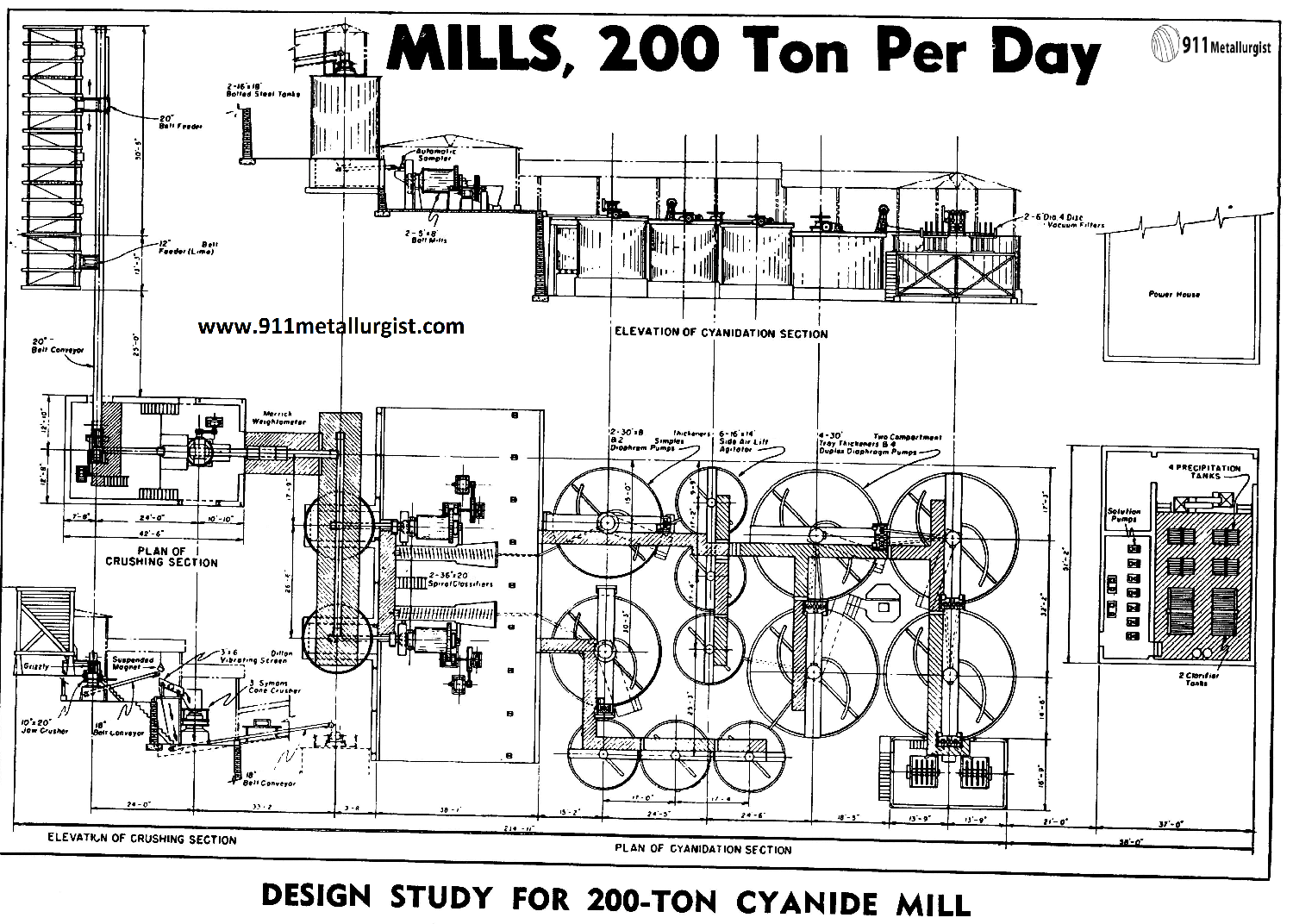
Cyanide Leaching Flowsheet
The flowsheet was developed from laboratory tests conducted by the 911Metallurgist, and is briefly as follows: Ore from the coarse bins is fed by a continuous feeder and conveyed to crushing section. Lime is fed on coarse ore conveyor due to large amount required and for ease of addition. A wedge bar grizzly removes the minus 1½ ” material ahead of the 10″x 20″ Jaw Crusher which is in open circuit with a double deck 3’x6′ Vibrating Screen and a 3′ cone crusher. The upper deck of the 3′ x 6′ screen has a heavy gauge space cloth to reduce wear on lower ½”opening screen. The crushed material is conveyed to mill storage bins by one fixed and one travelling belt conveyor so arranged to allow ore storage in either of the two fine ore bins, with provisions to permit storage in other additional bins in case of mill expansion.
Ore from mill bins is fed to each of the 5′ x 8′ Steel Head Ball Mills by variable speed belt ore feeders. The ball mills are in closed circuit with 36″ flared tank spiral classifiers. The overflow from each classifier at 95% minus 100 mesh at 25% solids flows by gravity to a 30′ diameter by 8′ deep primary thickener. The thickener overflow, pregnant solution flows to the precipitation plant below the mill. The underflow from each primary thickener is pumped to a bank of three 16′ diameter x 14′ deep, cyanide side airlift rake agitators in series. The pulp from the third agitator in each circuit flows to the first counter-current washing thickener of a series of four single sealed tray, two compartment thickeners. Each compartment is connected to an individual Adjustable Stroke Diaphragm Pump for the proper control and metering of the pulp between the tray thickeners. The underflows from the two compartments of the fourth and final thickener are pumped to two 6′ x 4-disc Disc Filters.
The filter cake is repulped and pumped at high density to tailing pond. Fresh wash water is added to the fourth thickener to make up loss of solution due to evaporation and for solution contained in filter cake. Water from tailings pond contains a small amount of cyanide and is reclaimed for use as wash water to the washing thickeners or for mill supply usage.
Gold Processing Plant Design
The design considerations were to provide ease of ore delivery by truck, minimum capital investment for equipment and construction items, contingent with highest economic recovery, and for low operation and maintenance expense. General construction incorporated best usage of locally available materials and labor, due to the remote location.
The coarse ore bins were located to allow access for trucks without extreme road-way grades and with ample space at unloading points for trucks to turn and dump without lost time. These bins were designed for construction from 8″ and 10″ square sawed timber framing and 3″ wood linings, which were available at reasonable cost. Four bin sections were provided for receiving and ore storage, plus one section for locally burned lime.
The crushing section was located to reduce conveyor length from and to storage points and permit minimum excavation and retaining walls in the sloping portion of the mill site. However, excavation and retaining walls did not affect costs to the usual extent due to low cost of local labor. All retaining walls were made from limestone masonry, using portland cement.
The equipment for crushing plant was selected to allow mill to be expanded to 400 tons per day without alterations or additions, except for the two additional fine ore bins. Space was provided for the expected increase in capacity.
The mill was designed for two identical parallel circuits of 100 tons per day each, and increased capacity planned to be handled in a similar manner.
The fine ore bins are round tanks, 16′ diameter by 18′ deep. These are of bolted design for ease of erection and for possible salvage value later. All mill solution and water storage tanks are also of bolted steel type. These tanks all being mounted on masonry piers with space provided for access to the ore feeders installed below. Automatic Samplers are used at belt feeder discharge to cut interval samples.
The grinding section allows ample working space around both ball mills and classifiers. Ball mill foundations being reinforced concrete to amply support the mills. The mills were equipped with combination drum scoop feeders and with welded steel scoop boxes, which have removable covers for access and inspection. The arrangement of the primary thickeners, rake agitators and washing tray thickeners was made to provide gravity counter flow of solution as desired with diaphragm pumps for the control of the pulp. The compact arrangement with walkways allowed operators easy access to the operating control points and unobstructed view of the operating area.
All thickeners and agitator tanks were of bolted design and mounted sand fills retained by circular masonry retaining walls, plus masonry retaining walls for the thickener underflow piping tunnels. A concrete floor, slightly above the ground line in the tank area was provided with drains to sump located between the four washing tray thickeners. This sump being connected to a SRL Pump to handle any solution spillage or for use as a transfer pump in case of the necessity to empty any thickener or agitator tank.
Detailed consideration was given to all pipe lines to allow adequate size and gradients for solution and pulp flows, together with compact, neat arrangement. All piping being bent in long radius, where bends were necessary and with pipe tees, where sharp turns were required. Clamp type joints were selected, both for ease in installation and possible removal for clearing in case of pipe stoppage. Due to arid and warm climate in the area no buildings were provided for the main plant. Corrugated sheet metal roofs supported by light weight steel, were installed over crushing section, fine ore bins, grinding section and over walkways and filter section to protect operators from the sun.
The precipitation plant equipment was installed in a masonry building with corrugated roof supported by steel roof trusses. This plant provided vacuum leaf clarification, zinc dust precipitation, and filtration, plus necessary solution and vacuum pumps.
Precipitate drying, and smelting furnaces were installed in a room separate from the precipitation section.
Power plant for the mill included three diesel electric generator units, one being for standby service. Three phase, 60 cycle, 440 volt, and single phase, 60 cycle, 220 volt current was generated for power and lighting.
The design and construction period for this complete plant required approximately four months, including initial start-up period, for a final check on metallurgy, and minor alterations and adjustments.
Recognition of the various factors and problems, and their proper evaluation in the planning stages resulted in a substantial saving in construction costs, and in the subsequent operation of this plant.
Source:
This article is a reproduction of an excerpt of “In the Public Domain” documents held in 911Metallurgy Corp’s private library.