Silver Sulphide Leaching & Filtration Circuit Startup & Shutdown Procedures
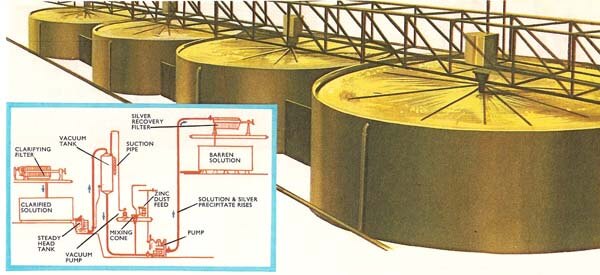
Details of good silver sulphide leaching and filtration circuit operation and instructions for sequencing and preparing for startup. The following items must be checked before the equipment in this EXAMPLE Argentite Leaching Circuit is started. The leach tank agitators should be running. Check that the Argentite filter feed pump, drum filter, repulper and tailings sampling pump […]
Silver Flotation Concentrate Leaching and Filtration Circuits

Producing a Silver Flotation concentrate from this EXAMPLE Argentite (cubic silver sulfide (Ag2S)) Flotation Circuit enters the first of four successive Argentite leach tanks. The purpose of this leach circuit is to dissolve the silver and gold recovered in the Flotation Circuit. A high strength solution of sodium cyanide, air, and lime are added to the […]
Crushing Plant Startup Sequence & Procedure
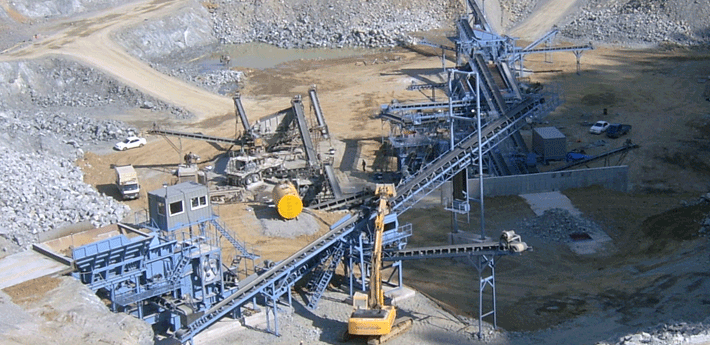
The following items make up an EXAMPLE Crushing Plant Startup Sequence & Procedure that all must be checked in preparation and before the equipment in the Crushing Plant is started. If maintenance has occurred since the last operating shift, ensure that the MCC is energized and that all safety locks have been removed from equipment starters. Walk along […]
Small Crushing Plant Operating Guide
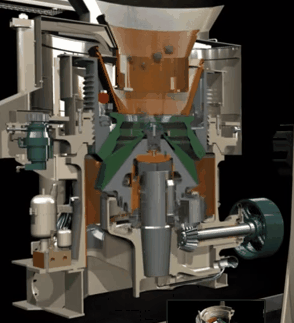
This EXAMPLE Small Crushing Plant is designed to crush 500 tonnes per day, operating 12 hours per day with an availability of 70%. The Plant will crush run-of-mine material (-16″) to 100%, passing 5/8″ at a rate of 60 tonnes per hour. Start-stop stations are provided for all equipment in this Plant at the crusher control […]
Hydrochloric Acid & Sodium Cyanide

Even a small concentration of hydrochloric acid in the air irritates the membranes of the respiratory tract making it easily detectable in amounts below the Threshold Limit Value of five parts per million. One to five parts per million can be detected by smell, while five to ten parts become disagreeable. In addition hydrochloric acid […]
Lead Nitrate Safety

Lead nitrate is used in small quantities in the gold recovery circuit. Lead is extremely toxic. It is a cumulative poison and so a dangerous exposure level would not necessarily show an immediate result, but continuous exposure at this level would maybe show as serious problems after a month. View a lead nitrate MSDS. Ingestion of […]
Sodium Cyanide Safety – Poisoning – HCN Vapor
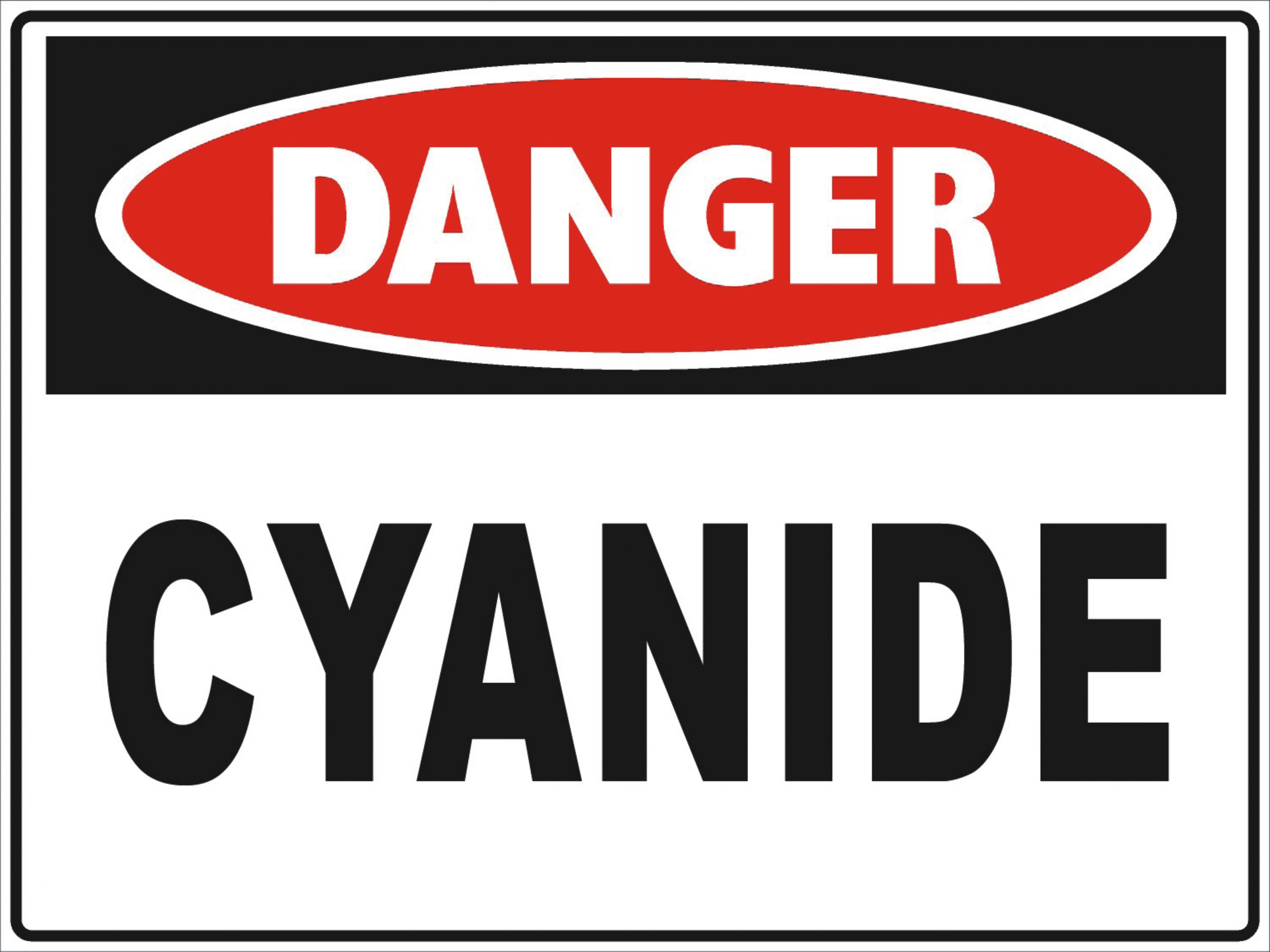
Almost all solutions in the plant contain cyanide, and in the absence of any other information it should be assumed that all solutions contain cyanide. Because of the toxicity of sodium cyanide, it is important that all persons coming in contact with it be completely familiar with and observe the established safety practices. Sodium cyanide […]
Good Concentrator Safety Guidelines & Practices

The following guidelines are considered good industrial practice: When any equipment or structure is dismantled in whole or in part, and subsequently re-assembled, it must be completely checked and found to be safe before it is started up. Whenever a person observes what appears to be an unsafe or harmful condition or act he should report it as soon as […]
Gold Process Description

In our Gold Process Description EXAMPLE, the ore will be received by the crushing plant initially by rail haulage from the ABC Zone and later by truck from the DEF Zones. The 350 tonne live capacity coarse ore bin is sufficient for train or truck load surges and provides approximately five hours storage of ore, […]